Actualités
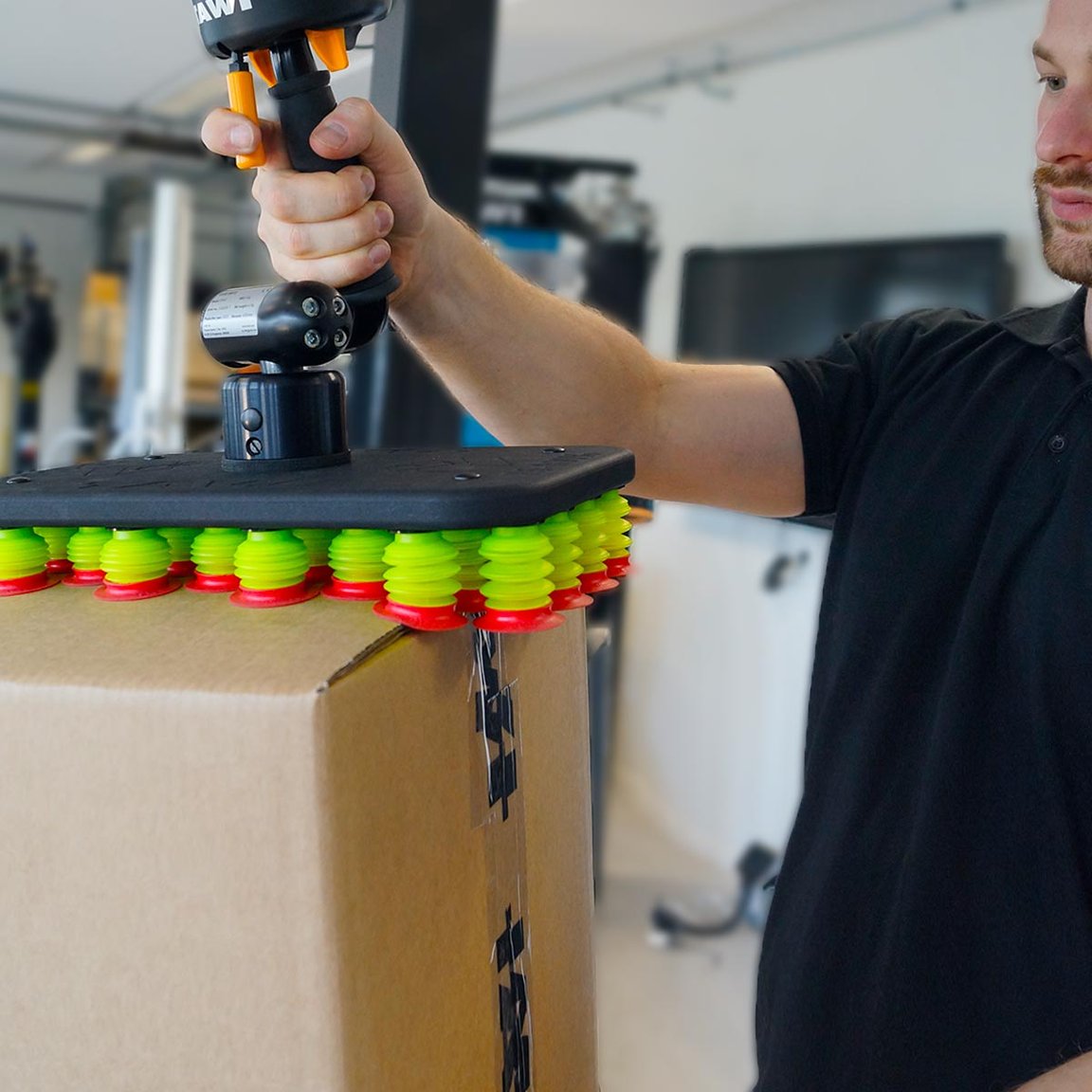
Manipulez plus, avec moins d’efforts – Découvrez le FlexiGrip
Dans les environnements logistiques où tout va très vite, chaque seconde compte — mais la sécurité et la fiabilité sont tout aussi essentielles. Les systèmes de levage doivent suivre le rythme, même lorsque les charges sont mal alignées ou emballées de manière irrégulière. C’est pour répondre à ces défis que nous avons conçu le FlexiGrip : une nouvelle ventouse intelligente, pensée pour une manutention rapide et fluide des cartons.
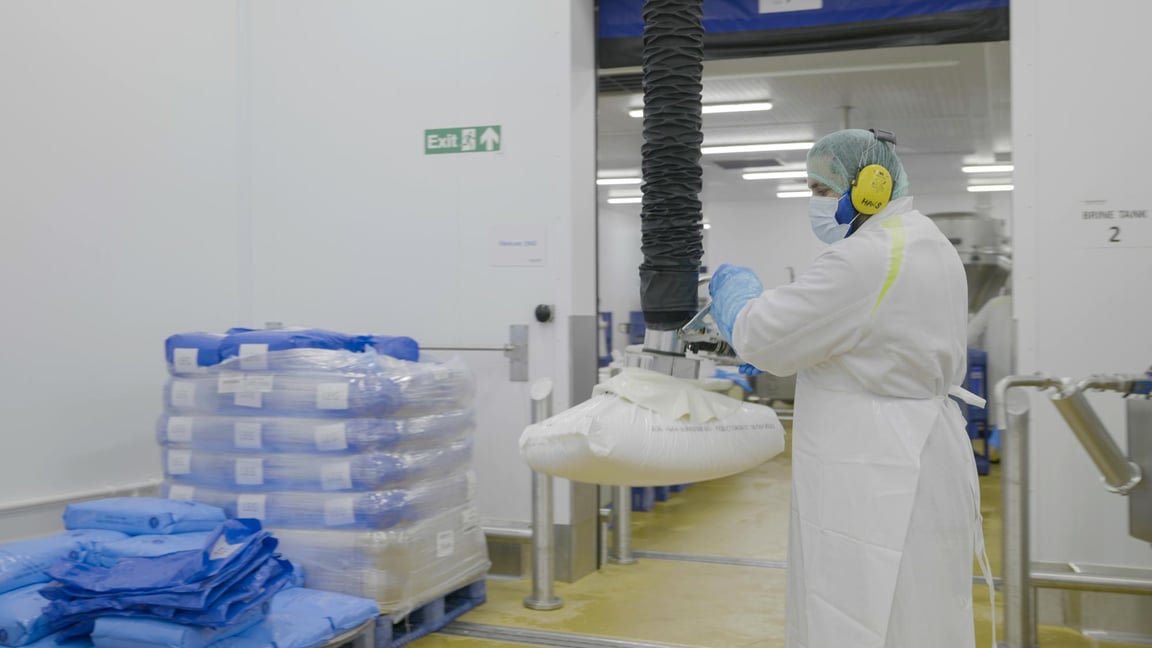
L'innovation dans l'industrie agroalimentaire : Tendances et défis en 2025
L'innovation dans l'industrie agroalimentaire est motivée par l'évolution de la demande des consommateurs, les bouleversements technologiques et les préoccupations en matière de développement durable. Pour rester compétitives en 2025 et au-delà, les entreprises doivent non seulement suivre l'évolution des tendances de l'industrie alimentaire, mais aussi relever de manière proactive les défis qui accompagnent ce changement.
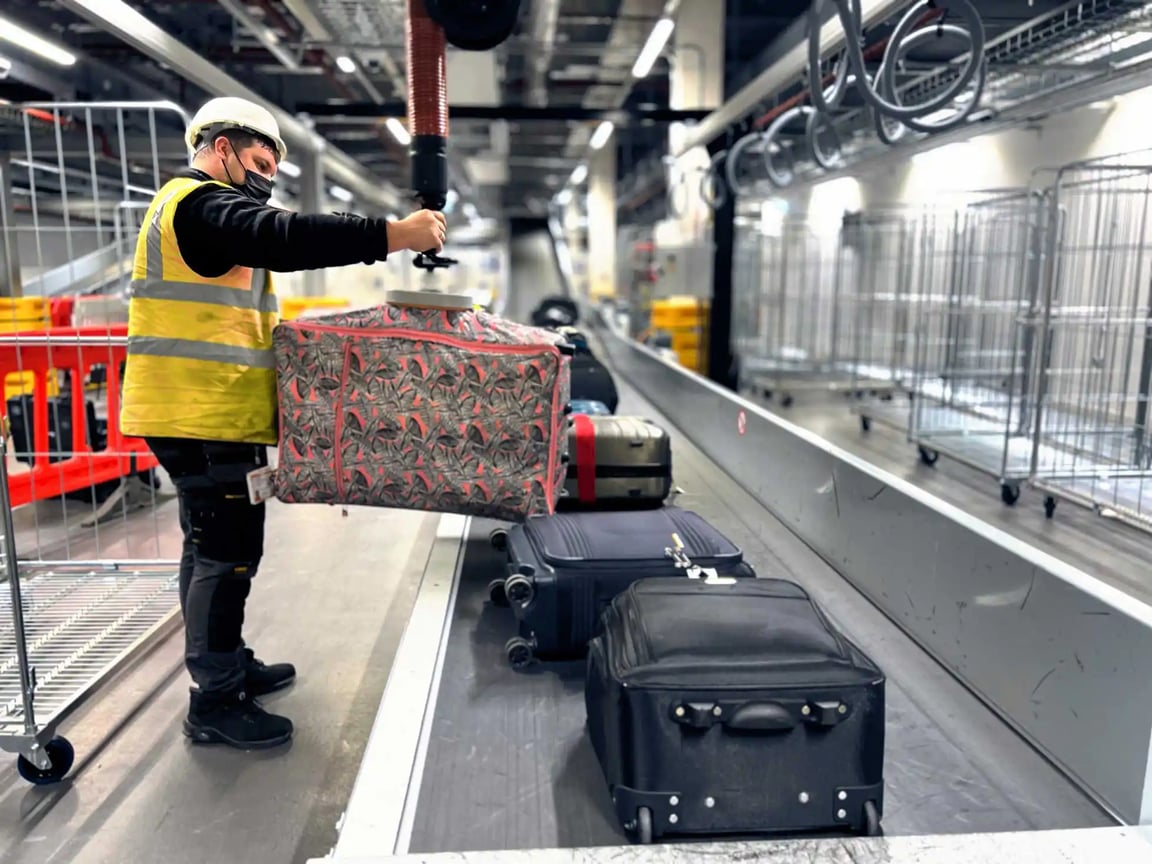
Le coût réel d'une mauvaise manutention des bagages
Les gens peuvent plaisanter sur le fait que les bagages ne sont pas manipulés avec soin ou qu'ils se perdent souvent aux points de transfert lorsqu'ils voyagent. Mais la vérité est que les passagers attendent beaucoup de leurs bagages, et qu'une mauvaise manipulation des bagages a un coût - un coût qui se répercute sur le personnel, la productivité et le budget.
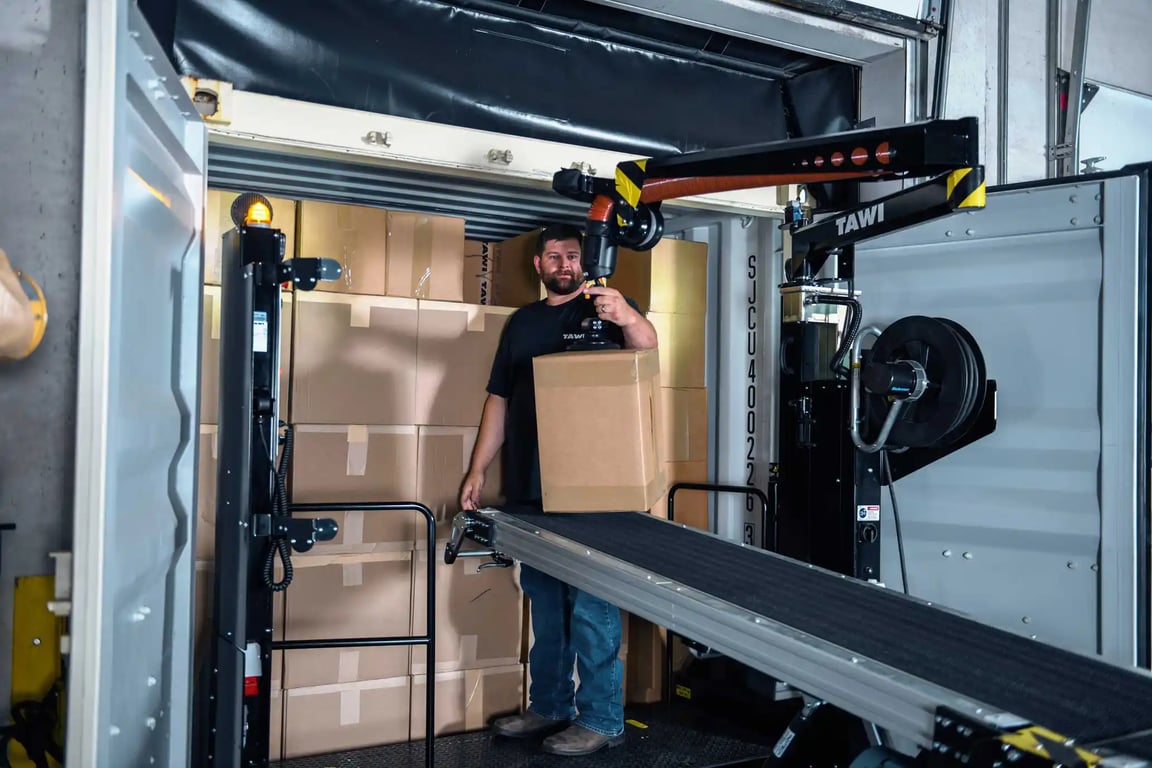
Simplifier votre logistique : améliorer votre efficacité avec la bonne solution de déchargement de conteneurs
Le déchargement de conteneurs est l’un des rares aspects de l’économie moderne à nécessiter encore de la main-d’œuvre. En raison de la diversité des articles et de l’exiguïté des espaces dans lesquels ils sont emballés, les seuls processus encore manuels dans la logistique sont le chargement et le déchargement de ces grandes caisses en acier.
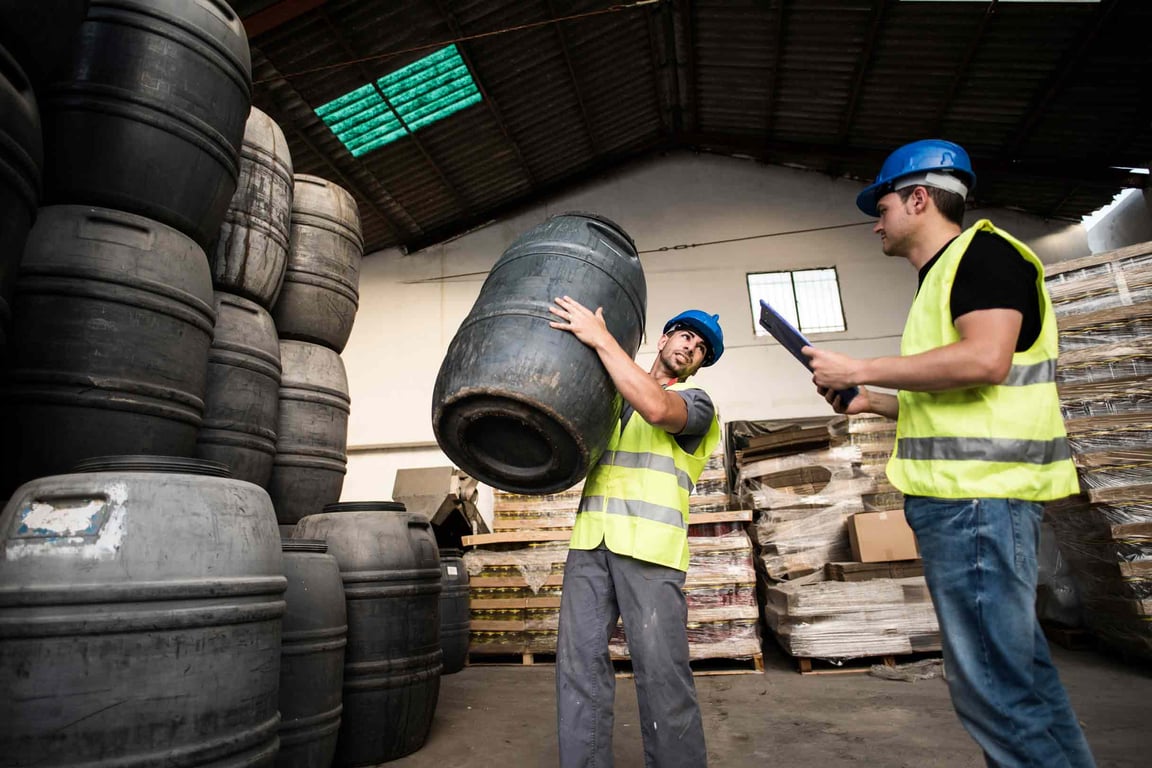
Manutention manuelle dangereuse : évaluation des risques et préventions
Les troubles musculo-squelettiques (TMS) liés au travail et résultant de la manutention manuelle sont l'une des principales causes de perte de temps de travail et de restrictions professionnelles. En procédant à une évaluation des risques sur votre lieu de travail, vous pouvez mettre en œuvre de manière proactive des mesures préventives pour atténuer les TMS.
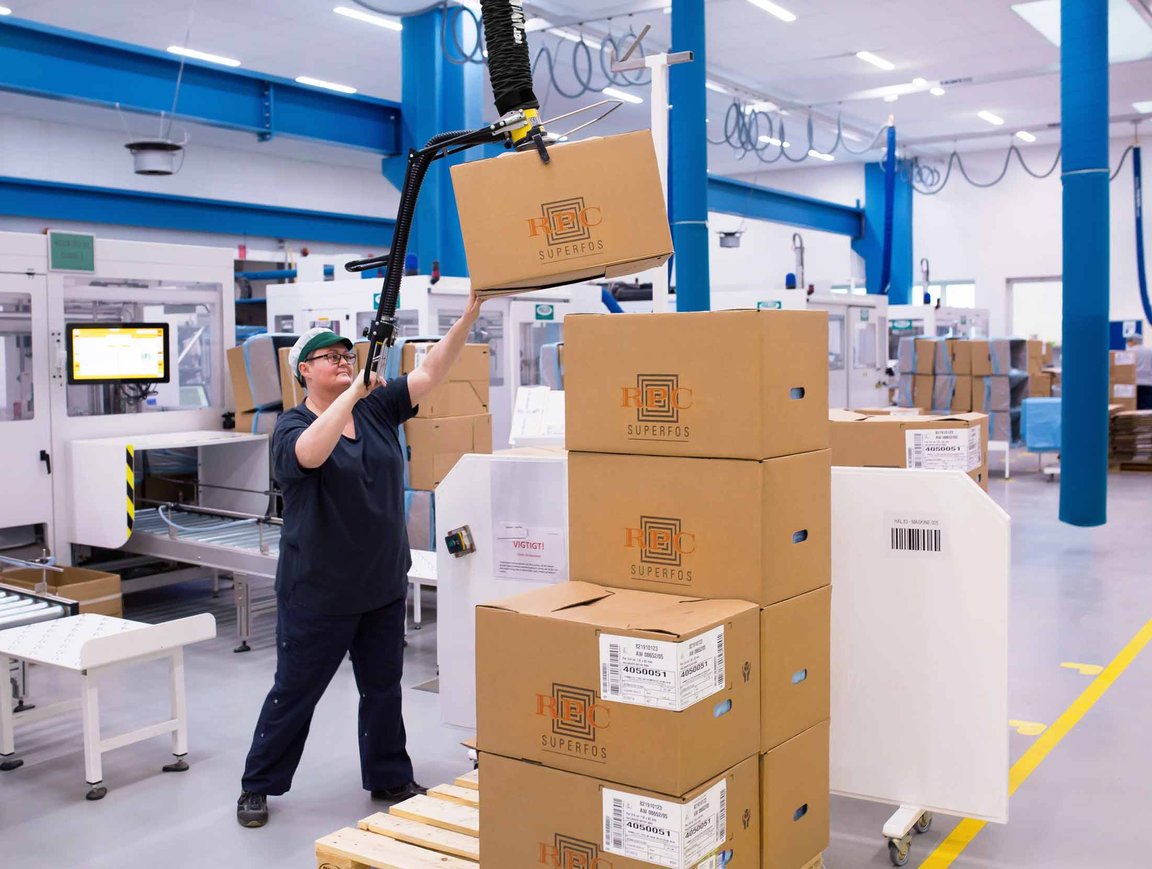
Les différentes solutions de levage qui simplifient la manutention de charges
Alors que vous étudiez les moyens de rationaliser et d’optimiser les opérations dans votre entrepôt ou votre usine de production, il est temps d’envisager l’utilisation d’équipements de levage. Au-delà des chariots élévateurs traditionnels, il existe une grande variété de systèmes de levage et d’accessoires.
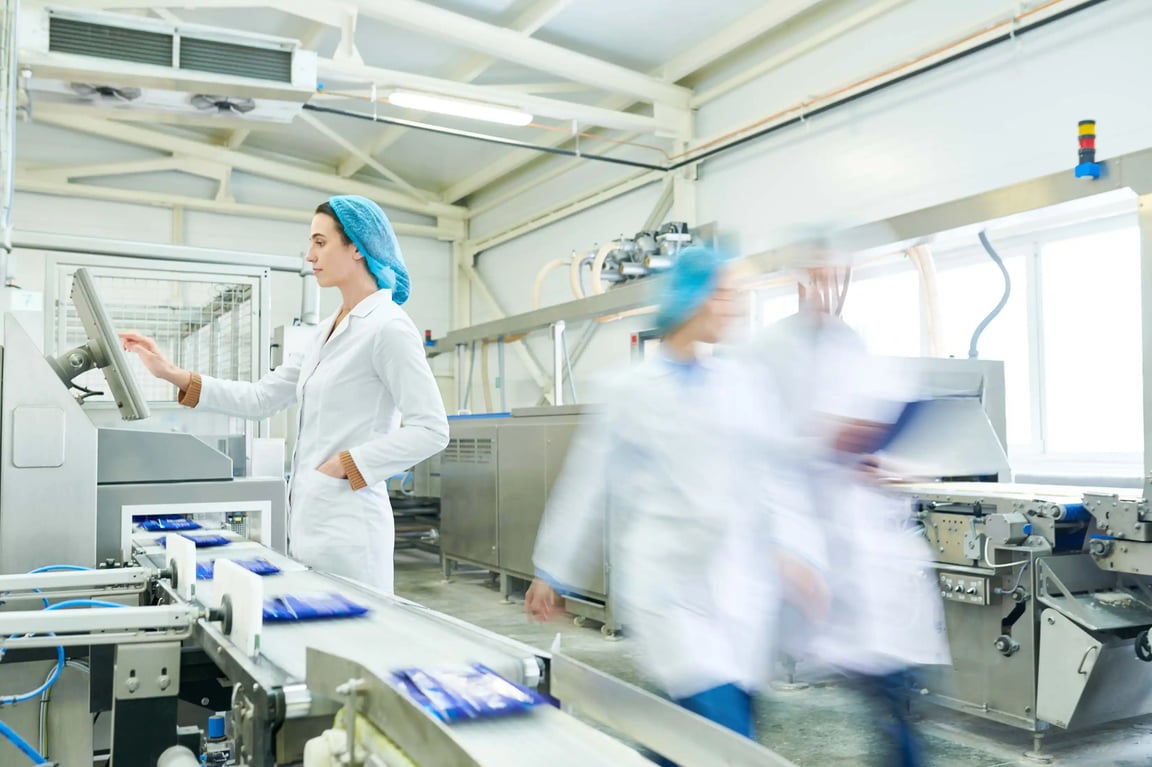
La (r)évolution du secteur de l’emballage alimentaire
Les biens et les produits doivent être protégés et préservés pour pouvoir passer du lieu de production à celui d’utilisation sans être endommagés. Et même si les emballages modernes font un travail remarquable pour protéger le contenu, les entreprises intelligentes comprennent désormais que la manière dont vous gérez le processus d’emballage des aliments est tout aussi importante.
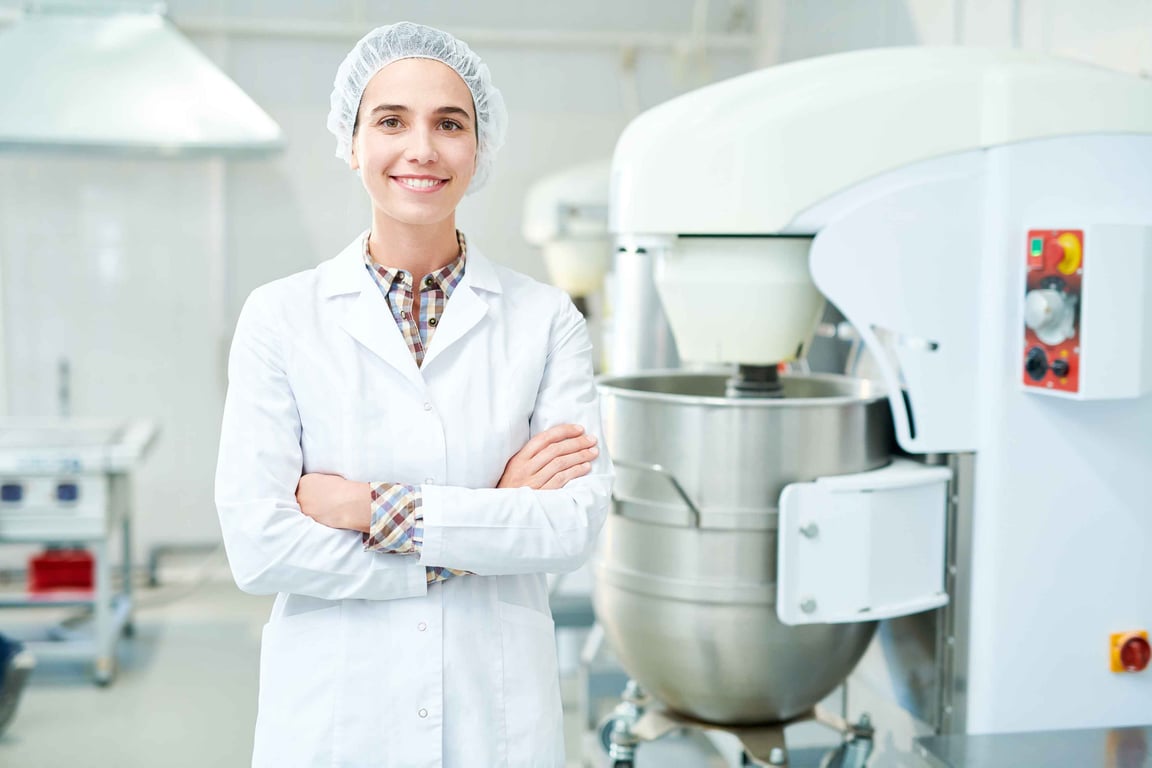
Créer un environnement préservant la santé et la sécurité dans l’industrie agroalimentaire
Les opérations de levage font partie intégrante de l’industrie agroalimentaire. Malheureusement, ils peuvent aussi être une source importante de blessures ou d’absences au travail. La mise en œuvre de la santé et de la sécurité au travail dans l’industrie de la Boisson et l’industrie Agroalimentaire, va bien au-delà des normes et des lois, elle a un impact majeur sur votre entreprise.
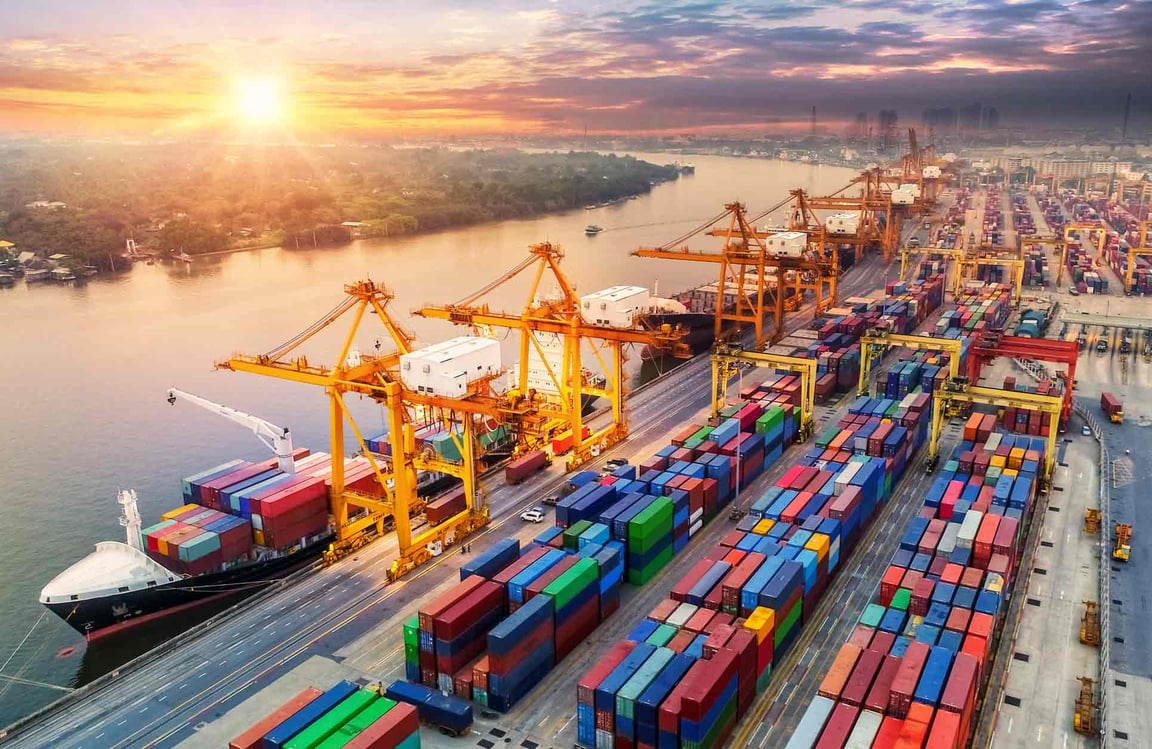
Les tendances de la logistique pour 2024
Le secteur de la logistique est en constante évolution et s’adapte à la croissance rapide de la technologie et à la nécessité de préserver l’environnement. Pour qu’une entreprise puisse garder une longueur d’avance et rester compétitive à l’heure actuelle, elle doit être suffisamment souple pour s’adapter aux dernières avancées technologiques, aux nouveaux processus et aux nouvelles stratégies pour réussir.
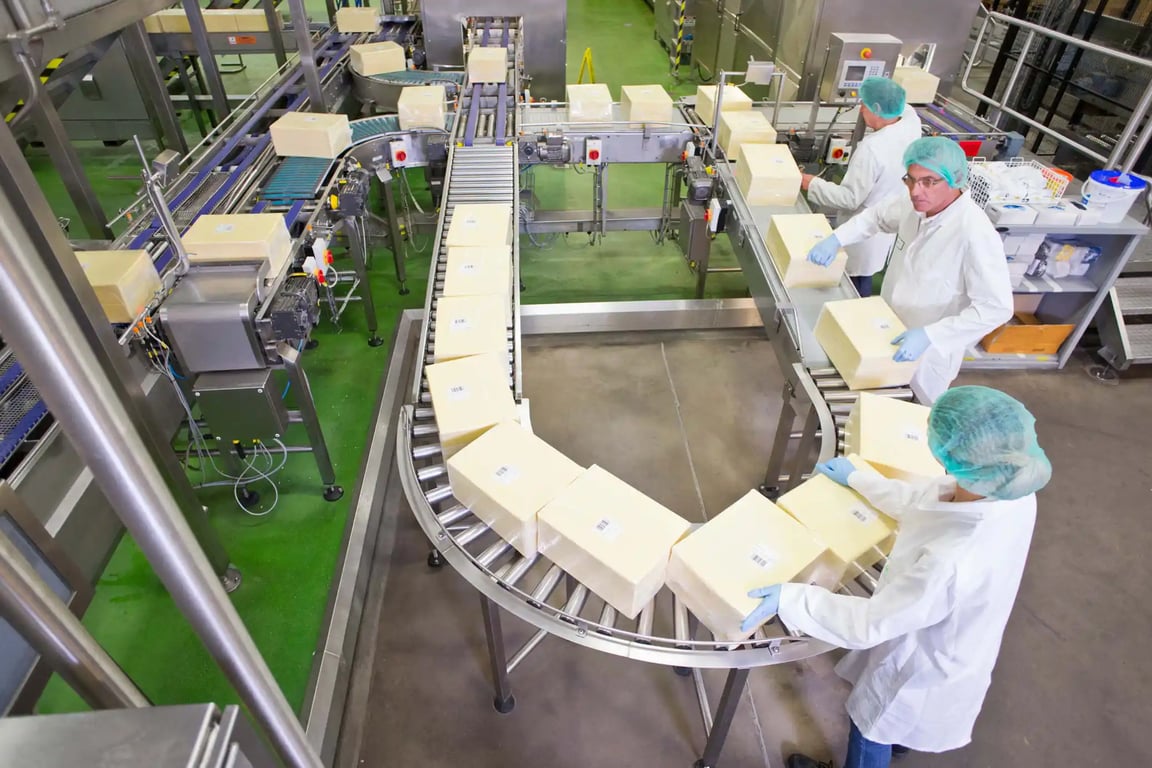
Développement durable et économies dans le secteur agroalimentaire
Lorsque l’on considère les systèmes de levage par le vide, les gerbeurs de manutention et les solutions de levage mobiles TAWI, l’attrait initial réside dans leurs avantages en termes d’efficacité et de sécurité. Ces outils rationalisent les tâches de levage, réduisent les contraintes physiques sur les travailleurs et transforment les travaux effectués par deux personnes en opérations fluides en solo.
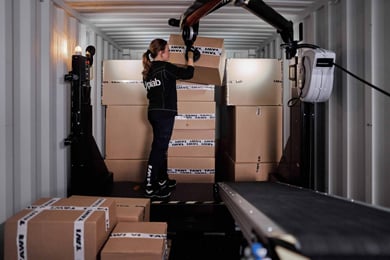
Chargement et déchargement efficaces
Un chargement et un déchargement bien organisés sont la clé d’un processus logistique efficace. Faire un pas vers l’automatisation de vos processus de manutention manuelle est une stratégie essentielle pour rendre votre personnel logistique plus efficace.
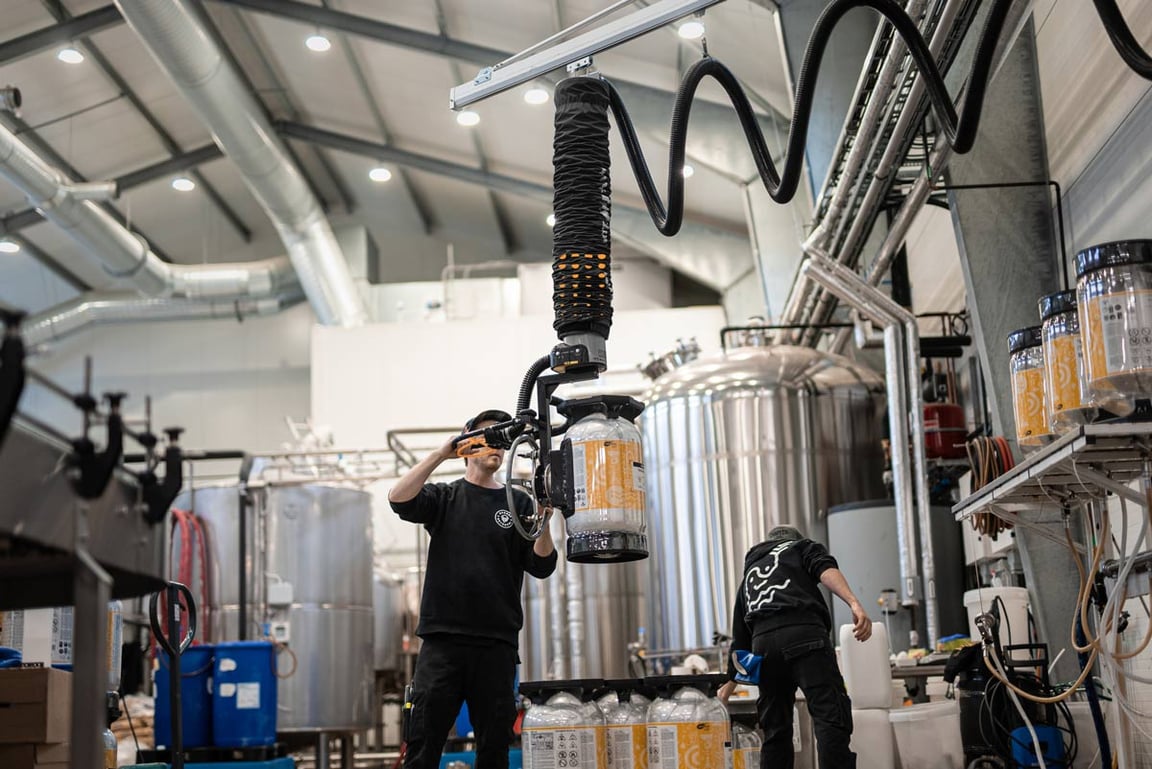
Pourquoi la manutention de charges dans l'agroalimentaire est-elle si importante ?
La manutention de charges est un aspect essentiel de l'industrie agroalimentaire. Elle englobe le déplacement, le stockage, la protection et le contrôle des produits tout au long du processus de fabrication. Une manutention efficace garantit que les produits alimentaires sont transportés de manière sûre et efficace de la production à l'emballage, au stockage et à la distribution.
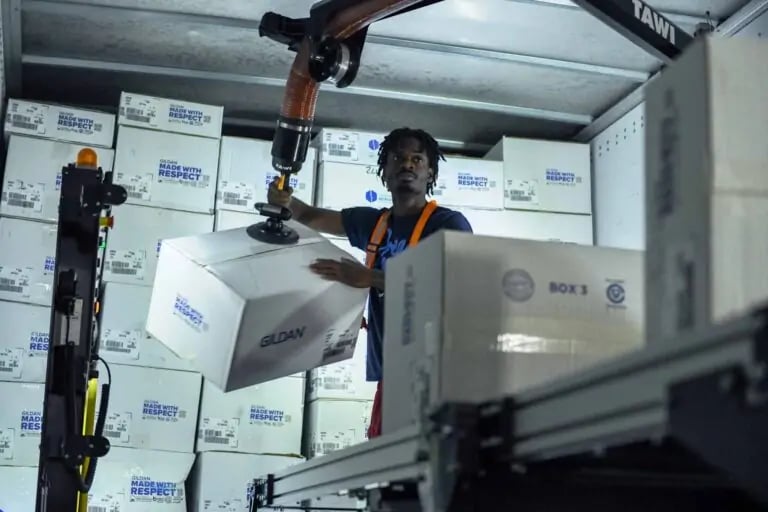
5 étapes pour améliorer votre efficacité opérationnelle en logistique
Confrontées à des défis tels que la pénurie de main-d’œuvre et les risques pour la sécurité, les méthodes logistiques traditionnelles peinent à maintenir leur efficacité opérationnelle. L’intégration de technologies telles que le suivi par GPS, l’automatisation et les systèmes de levage par le vide innovants permet non seulement d’accroître l’efficacité opérationnelle, mais aussi de réduire les coûts, d’améliorer la sécurité et de garantir la satisfaction des clients.
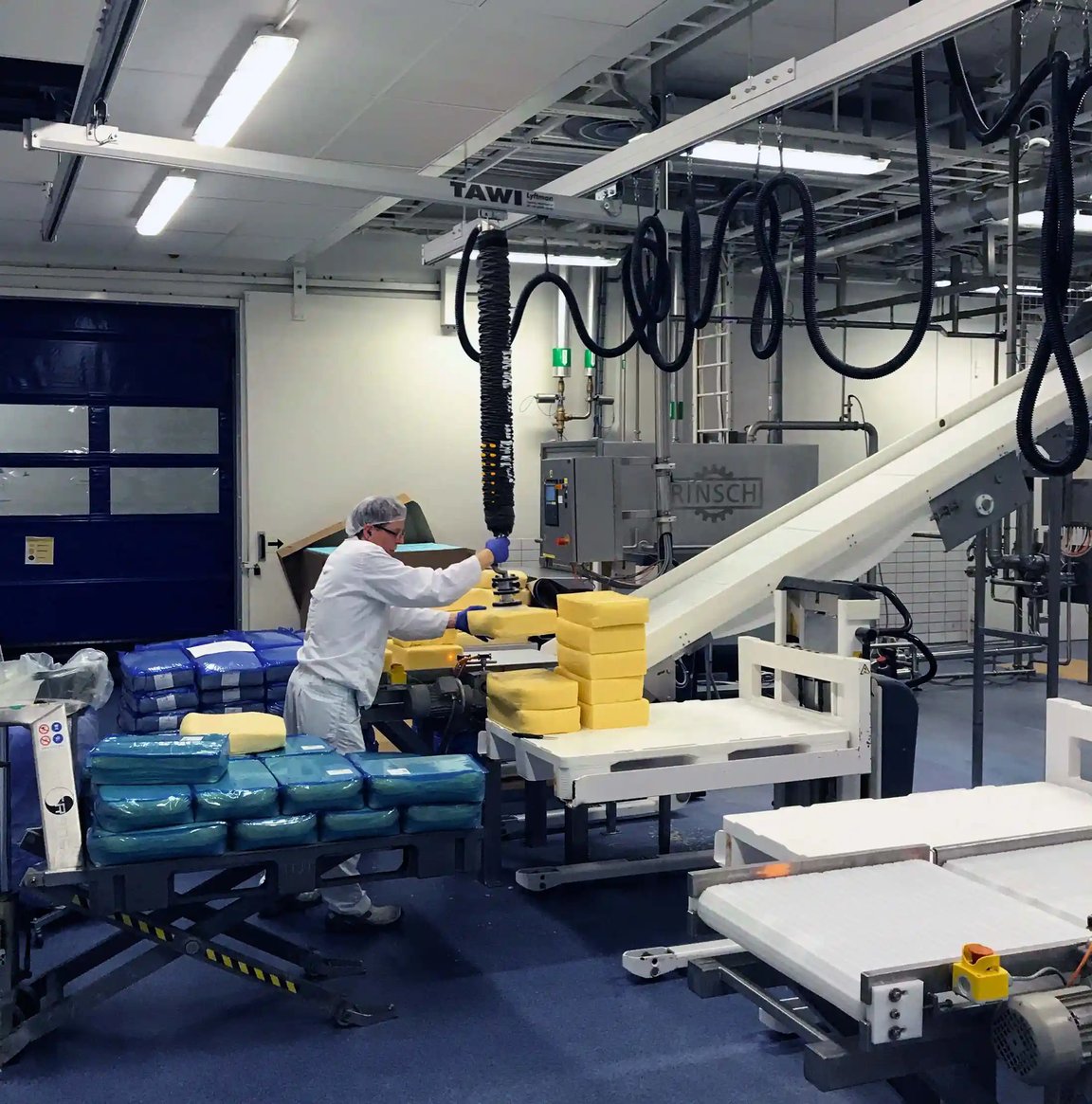
Aider les fabricants de produits alimentaires à répondre aux exigences de la demande
Les responsables d'usines agroalimentaires connaissent mieux que quiconque l'importance des gains marginaux et d'optimiser ses opérations. Alors que la plupart des entreprises ont réduit leurs effectifs pendant la crise COVID19, l'industrie agroalimentaire a continué à produire à plein régime.
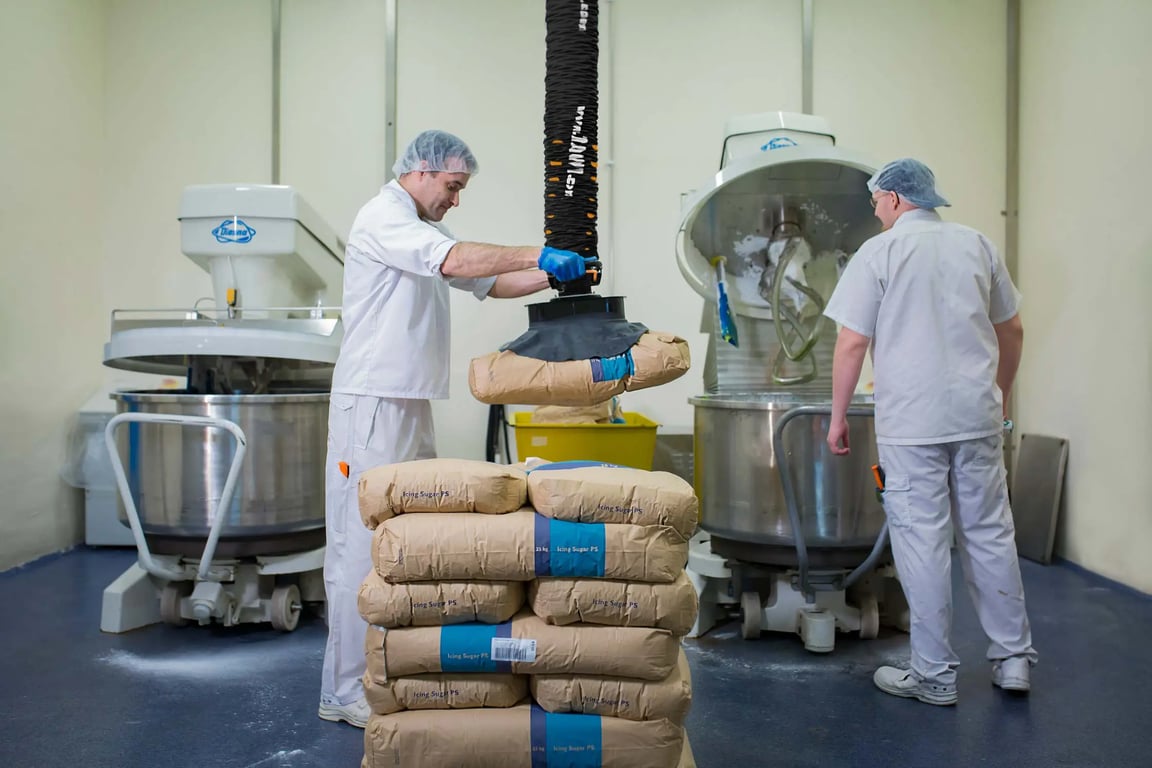
Le levage par le vide est-il adapté à mon entreprise de produits agroalimentaires
"Les entreprises industrielles ont profondément besoin de se moderniser, mais elles ont tendance à manquer cruellement d’investissements dans la technologie […] contrairement aux B2C, ces organisations B2B sont aux prises avec une architecture obsolète et un méli-mélo de processus qui entravent les tentatives de croissance rentable." – Howard Doberman, Responsable de la transformation des opérations mondiales, Deloitte.
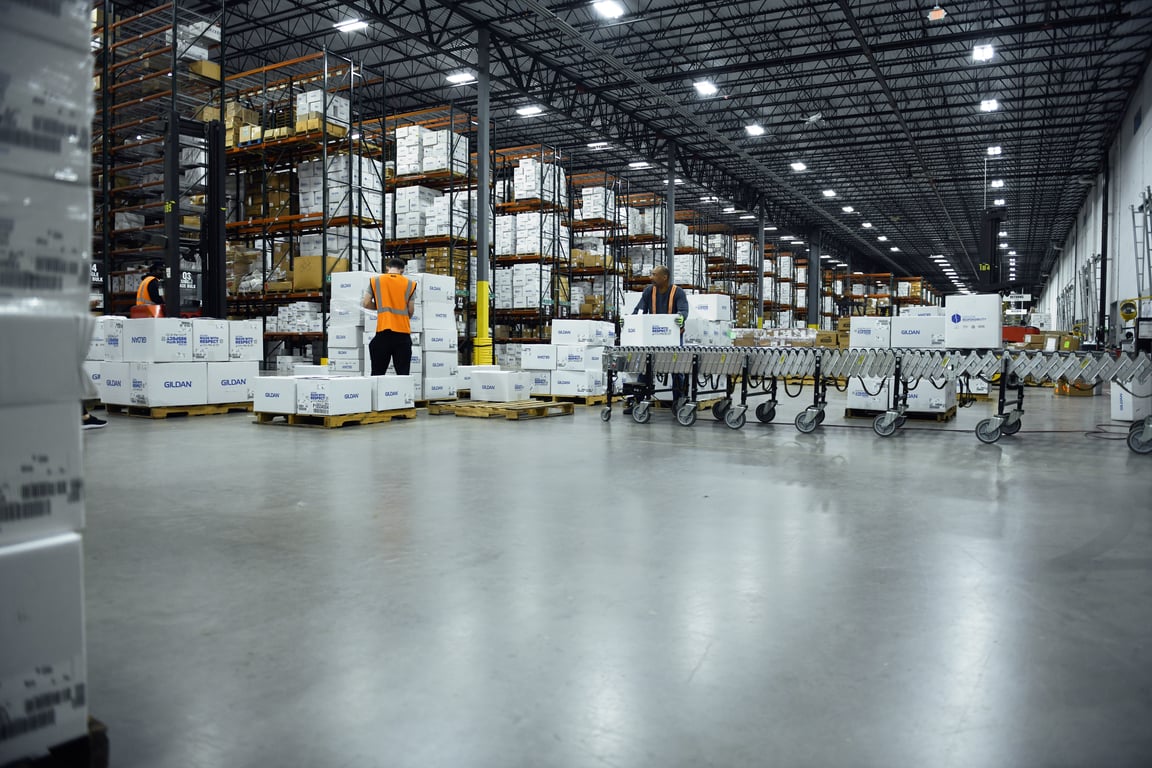
Les plus gros problèmes logistiques en 2025
Le secteur de la logistique est de plus en plus étroitement lié à l’économie, à la politique et à l’état de l’environnement dans le monde. Ces défis auxquels ce secteur est confronté ne sont pas simplement logistiques, ils reflètent des tendances et des changements sociétaux plus larges. Cependant, ces problèmes et défis logistiques ne doivent pas nécessairement se transformer en problèmes pour votre entreprise.
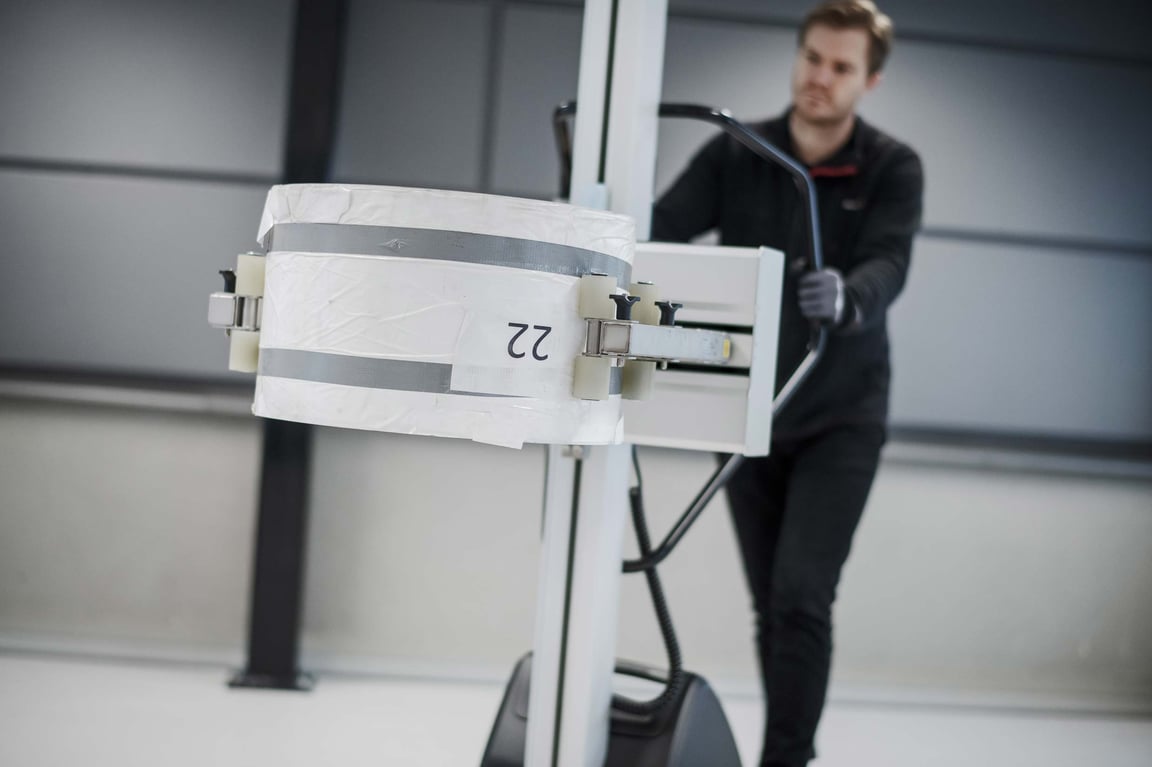
Manutention de bobines grâce à un système de levage intelligent
Selon la manière dont les bobines doivent être manipulées depuis des palettes puis déplacées pour une utilisation ultérieure, différentes solutions de levage peuvent être utilisées. Investir dans un équipement de manutention de bobines optimisé pour votre flux de travail réduit considérablement les blessures et augmente l'efficacité et la flexibilité de la main-d'œuvre.
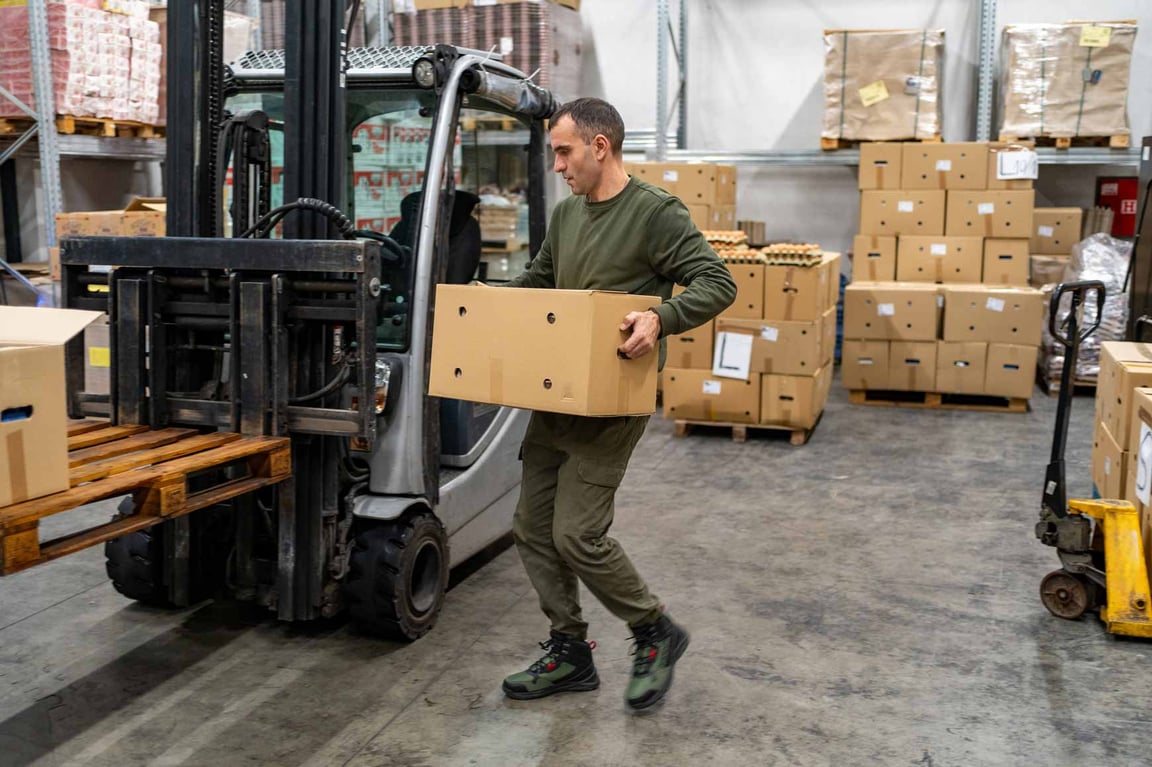
La sécurité dans les entrepôts est-elle en contradiction avec la productivité et l’efficacité ?
Contrairement aux idées reçues, la sécurité, la productivité et l’efficacité ne sont pas antagonistes dans les opérations d’entreposage. En fait, elles peuvent coexister et se renforcer mutuellement. Mais comment y parvenir ?
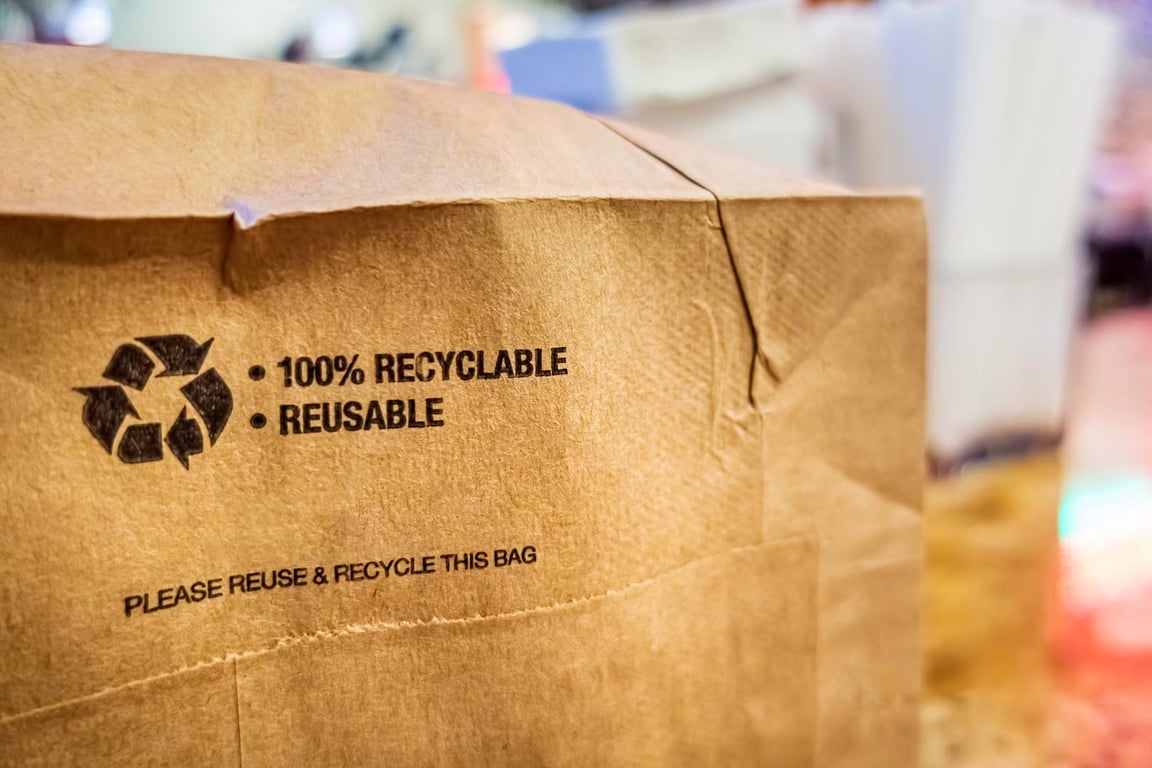
Les tendances dans les matériaux d’emballage : ces derniers sont-ils compatibles avec le levage par le vide ?
Les matériaux d’emballage sont une composante essentielle de la logistique moderne. Ils protègent les produits pendant le transport et le stockage, mais reflètent également l’image de marque des entreprises. Cela a conduit à une évolution significative des matériaux d’emballage, sous l’effet des progrès technologiques, de l’évolution des préférences des consommateurs et des préoccupations en matière de développement durable.
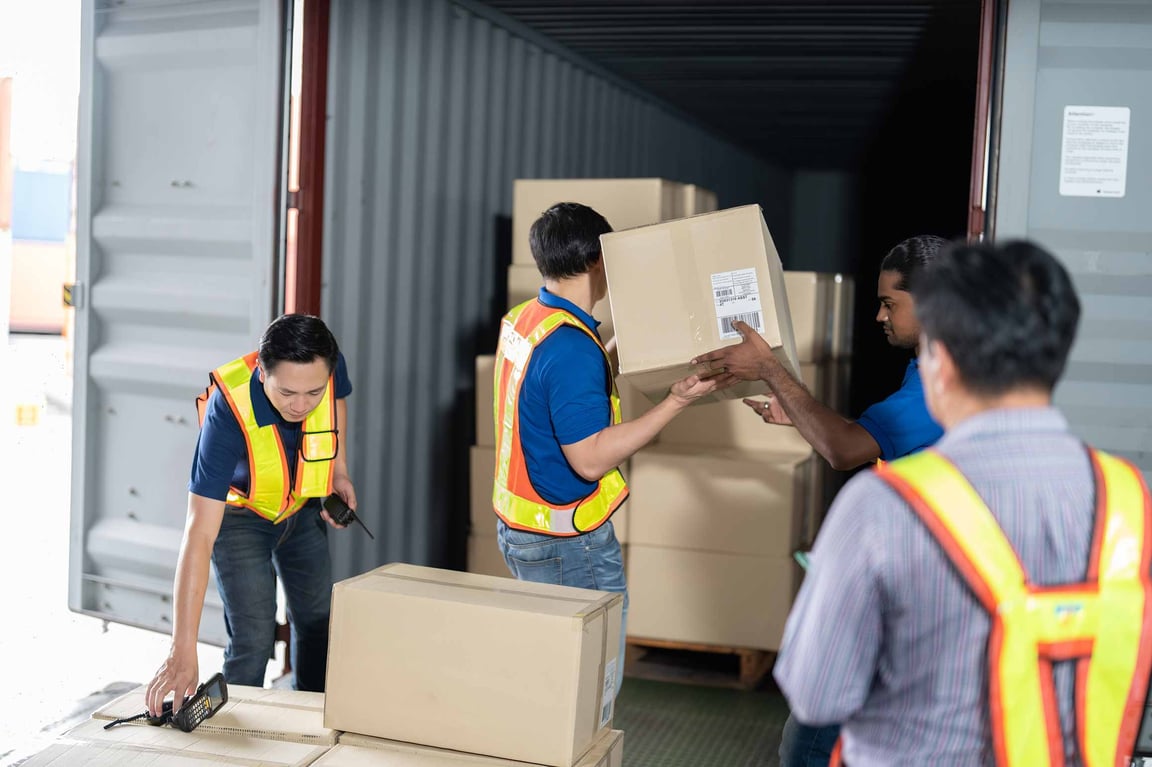
Les services de chargement-déchargement sont-ils encore rentables pour le secteur de la logistique ?
Si vous travaillez dans le secteur de la chaîne d’approvisionnement, vous connaissez probablement le terme de « chargeur-déchargeur ». Pour ceux qui ne le savent pas, il est utilisé dans le secteur du transport routier pour décrire le processus de chargement et de déchargement du fret par toute personne autre que l’expéditeur, le destinataire ou le chauffeur du camion.
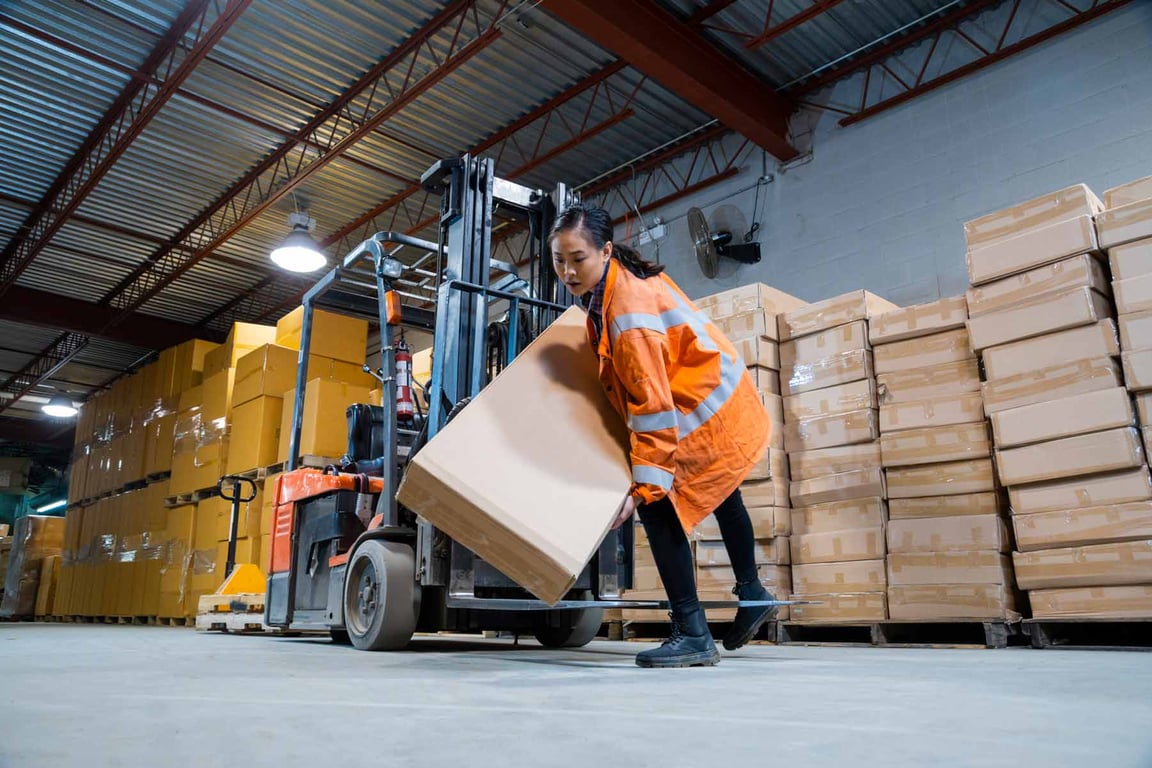
Les 3 types les plus courants de blessures dues à la manutention manuelle
Les entrepôts sont des environnements animés, regorgeant d’un ensemble complexe d’équipements, d’imposantes montagnes de produits et d’une main-d’œuvre travaillant jour et nuit. Ce contexte dynamique accroît considérablement le risque d’accidents du travail et de blessures dus à la manutention manuelle.