Les 3 types les plus courants de blessures dues à la manutention manuelle
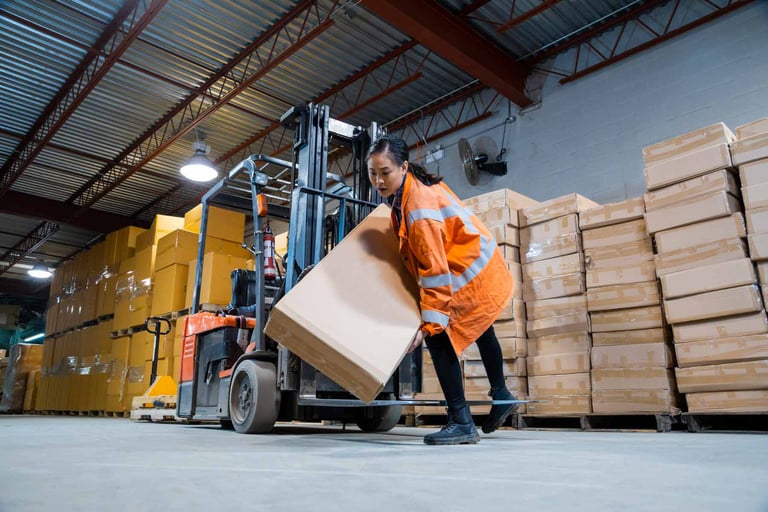
Les entrepôts sont des environnements animés, regorgeant d’un ensemble complexe d’équipements, d’imposantes montagnes de produits et d’une main-d’œuvre travaillant jour et nuit. Ce contexte dynamique accroît considérablement le risque d’accidents du travail et de blessures dus à la manutention manuelle.
Rien qu’en 2020, le secteur du transport et de l’entreposage privé a déclaré 206 900 cas d’accidents et de maladies non mortels. Parmi ceux-ci, 99 800 ont donné lieu à des jours d’absence du travail, 57 000 à un transfert ou à une restriction d’emploi et 50 100 étaient d’autres cas enregistrables. Le taux d’incidence total des cas enregistrables était de 4,0 pour 100 employés en équivalent temps plein (ETP).
Où se produisent la plupart des accidents dans un entrepôt ?
Les cinq premiers endroits sont les quais, les chariots élévateurs, les convoyeurs, le stockage des matériaux ainsi que le levage et la manutention manuels.
Les statistiques américaines de référence détaillent ci-dessous les spécificités des accidents du travail et des maladies professionnelles non mortels qui ont entraîné des jours d’absence du travail dans le secteur du transport et de l’entreposage :
Caractéristiques du cas Nombre de cas
Nature de la blessure ou de la maladie
Entorses, foulures, déchirures 42,280
Courbatures, douleurs 15,630
Ecchymoses, contusions 10,370
Fractures 7,790
Coupures, lacérations 3,900
Partie du corps affectée
Dos 16,910
Épaule 9,840
Genou 9,370
Plusieurs parties du corps 8,540
Main 8,030
Événement ou exposition à l’origine d’une blessure ou d’une maladie
Heurt par un objet ou un équipement 12,100
Effort excessif lors du levage ou de l’abaissement 11,950
Chute au même niveau 10,940
Chute à un niveau inférieur 6,750
Incidents de la route impliquant des véhicules terrestres à moteur 6,430
Bureau des statistiques du travail des États-Unis, transport et entreposage, 2016 – 2020.
Ces statistiques révèlent les risques tangibles auxquels sont confrontés les employés de ce secteur, avec un nombre alarmant de 206 900 cas d’accidents du travail et de maladies professionnelles non mortels. Les trois principaux événements à l’origine de blessures sont le heurt par un objet ou un équipement, l’effort excessif lors du levage ou de l’abaissement et la chute au même niveau. Les trois principales conséquences sur les employés sont les entorses, les foulures, les déchirures, les courbatures, les douleurs ainsi que les ecchymoses et les contusions, en particulier au niveau du dos, des épaules et des genoux.
Les blessures les plus courantes liées à la manutention manuelle
- Troubles musculo-squelettiques.
- Entorses et foulures, ou autres lésions des tissus mous.
- Blessures à la main, telles que les fractures des doigts ou d’autres os de la main.
- Blessures au dos, lésions de la colonne vertébrale ou hernies discales.
- Blessures à l’épaule.
- Coupures et lacérations.
- Blessures à la cheville et au pied.
On peut toutefois les classer en trois grandes catégories :
- Heurt par un objet ou un équipement : cette cause représente près d’un tiers de ces types de blessures, une grande partie des employés étant heurtés par des camions. Des recherches ont montré que chaque année, un décès sur cinq et plus de 12 000 blessures sur le lieu de travail sont causés par des chariots élévateurs et d’autres véhicules industriels. Ces statistiques soulignent l’importance d’une formation régulière des employés aux chariots élévateurs. Cependant, les accidents ne sont pas uniquement causés par ces derniers. Des objets mal empilés peuvent se renverser, tomber et heurter les employés. Le personnel doit être bien formé au chargement et au déchargement sûrs des palettes, aux hauteurs et aux poids d’empilage sécurisés et à l’importance de ne pas grimper, se pencher ou marcher sur les palettes.
- Effort excessif lors du levage ou de l’abaissement : la manutention manuelle est à l’origine de plus d’un tiers des accidents du travail, notamment les foulures, les entorses, les lésions dorsales, les coupures, les ecchymoses et les fractures. Bien qu’il puisse arriver que votre personnel doive manipuler des matériaux lourds, ces tâches devraient être évitées autant que possible.
- Chutes au même niveau : les chutes au même niveau sont une cause fréquente d’accidents du travail entraînant des blessures. Il s’agit généralement de glissades et de trébuchements sur le sol sur lequel vous travaillez. Pour éviter de tels accidents, une formation adéquate et des procédures solides sont nécessaires pour s’assurer que le personnel sait comment arrimer et déplacer en toute sécurité les objets stockés en hauteur. Des équipements de protection individuelle (EPI) tels que des casques de protection sont souvent nécessaires, de même que des panneaux d’avertissement dans les zones de danger potentiel.
Parmi les causes les plus courantes, citons le manque de formation. Il peut par exemple conduire un employé à se blesser au dos en soulevant une charge lourde du fait qu’il se sert de son dos plutôt que de ses jambes. En outre, l’absence d’indications claires sur le poids et la manutention des colis peut amplifier les problèmes. Par exemple, un employé tente de soulever une charge, mais se rend vite compte qu’elle est trop lourde et la laisse tomber sur son pied, ce qui provoque des fractures métatarsiennes.
Comprendre les blessures dues à la manutention manuelle sur le lieu de travail : qui est responsable ?
La sécurité sur le lieu de travail est une responsabilité partagée qui concerne tout le monde : employeurs, employés, clients et même visiteurs. Chaque personne qui entre sur un lieu de travail a un rôle à jouer pour assurer sa sécurité et celle des autres.
Cependant, d’un point de vue juridique, le niveau de responsabilité varie. La part la plus importante de la responsabilité incombe à l’employeur, mais les employés ont également une obligation légale en matière de santé et de sécurité. Aux États-Unis, une série de lois et règlements constitue la base d’un environnement de travail équitable et respectueux, protégeant les droits et le bien-être des employés d’entrepôts.
Législation et réglementation du travail : examen plus approfondi
La loi sur les normes de travail équitable Fair Labor Standards Act, (FLSA) est une loi fédérale qui fixe les critères de référence en matière de salaires et d’heures de travail. Elle définit un salaire minimum, le droit à la rémunération des heures supplémentaires, la tenue de registres et les normes relatives au travail des enfants. Cette loi garantit que les employés reçoivent une compensation équitable pour leur travail et leur engagement.
La loi sur la sécurité et la santé au travail Occupational Safety and Health Act (OSHA) joue un rôle crucial dans le maintien d’un environnement de travail sûr et sain. Elle fixe les lignes directrices auxquelles les entrepôts doivent se conformer afin de prévenir les accidents et de préserver la santé de leurs employés. Il s’agit notamment de dispenser une formation adéquate, d’organiser régulièrement des exercices de sécurité et de veiller à ce que tous les équipements soient sûrs et en bon état.
La loi sur l’indemnisation des travailleurs Worker’s Compensation Act (FECA) garantit qu’un employé blessé au travail reçoit une indemnisation appropriée. Elle couvre non seulement les frais médicaux, mais aussi les indemnités de remplacement du salaire de l’employé blessé, offrant ainsi un filet de sécurité à ceux qui en ont le plus besoin. Une amende de l’OHSA peut s’élever à 7 000 dollars pour une infraction « mineure » et à 70 000 dollars pour les récidivistes.
Le coût des accidents sur le lieu de travail varie, mais selon le National Safety Council, chaque coût direct pour une entreprise s’élève à 38 000 dollars et peut atteindre 150 000 dollars en coûts indirects.
Réglementations dans le domaine des transports et de la logistique
Il existe des réglementations supplémentaires en matière de transport et de logistique qui doivent être respectées afin de minimiser les risques d’accident et de garantir la sécurité des marchandises et des personnes impliquées dans le transport. Le respect de ces réglementations permet également de réduire les coûts, car en évitant les dommages et les accidents, on réduit les coûts liés aux pertes et aux assurances et on protège la réputation de l’entreprise d’entreposage sur le marché.
Ces réglementations comprennent des règles sur la conformité des véhicules aux normes de sécurité et d’environnement, telles que l’assurance des camions commerciaux et celle des entrepôts. Il existe également des réglementations relatives à la manutention et à la sécurité des marchandises, conçues pour éviter les dommages aux employés et garantir que les marchandises sont manipulées, stockées et transportées de manière à éviter les dommages et les pertes.
L’évaluation des risques : une étape clé
Les employeurs sont tenus de procéder à une évaluation des risques, c’est-à-dire d’évaluer tous les risques auxquels leurs employés sont exposés. Des mesures de prévention et de protection doivent être mises en place, notamment en veillant à ce que chaque employé ait reçu les informations et la formation nécessaires en matière de santé et de sécurité. Parfois, des mesures supplémentaires peuvent être prises, par exemple en empêchant les situations dangereuses de se produire par le biais d’une formation.
Bien qu’il n’existe pas de règles européennes décrivant exactement la manière dont vous devez procéder à l’évaluation des risques, dans certains pays, les règles nationales peuvent inclure des exigences plus détaillées concernant le contenu et la forme de l’évaluation des risques. Il en va de même pour les États-Unis.
Quelques mesures à prendre lors d’une évaluation des risques
- Recueillir les informations pertinentes.
- Identifier les dangers possibles.
- Évaluer les risques découlant des dangers ; par exemple, estimer la probabilité et la gravité des conséquences et décider si le risque peut être toléré.
- Planifier des actions pour éliminer ou réduire les risques.
- Documenter l’évaluation des risques.
Même si des évaluations des risques sont effectuées, elles ne font qu’identifier les risques au lieu de les atténuer. Chez TAWI, nous avons mis au point une solution qui réduit considérablement le risque de blessures liées à la manutention des marchandises, et qui permet même de réduire de 80 % les efforts physiques des employés.
Nos solutions de levage par le vide allègent au sens propre du terme la charge pour vous et vos employés. Cela signifie moins de risques associés à la manutention, une protection des employés contre les dommages et une protection de votre entreprise contre les pertes financières et les atteintes à la réputation. Nos produits améliorent la sécurité des entrepôts en réduisant les blessures, car ils se chargent de tout le travail de levage. Il en résulte moins d’efforts physiques, moins de fatigue et moins de risques de chutes de marchandises en raison d’un poids excessif.
Conclusion
Comprendre ces types courants de blessures liées à la manutention manuelle et mettre en œuvre des mesures préventives permet de réduire considérablement le risque de blessures sur le lieu de travail, garantissant ainsi un environnement plus sûr et plus productif pour votre personnel.
Vous voulez minimiser les blessures tout en améliorant les performances de votre entreprise ? Lisez notre guide : "Le guide complet pour améliorer l’efficacité de la logistique d’entreposage".