Pharma manufacturing: main challenges and potential solutions
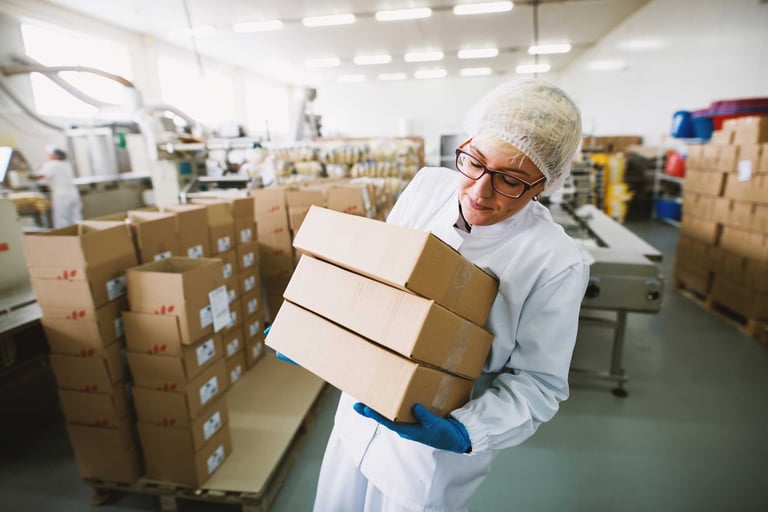
Pharma manufacturing is complex and sometimes hazardous industry. The manufacturing process demands precise, safe and hygienic lifting at the weighing, processing and packaging stages.
Our customised lifting solutions can address the main challenges in the industry like improving productivity plus large health and safety benefits.
The main challenges of pharma manufacturing
The pharma manufacturing process involves much more than simply combining ingredients to form tablets, capsules, solutions or ointments. The process is heavily dependent on the material flowrate. High performance depends on consistently feeding substances into successive processes along the line, demanding reliability, accuracy, hygiene, and minimal interruptions.
The process is also hazardous. There are moving machine parts, pressurised equipment, and the manual handling of heavy materials, often in confined spaces. The lifting, pushing, pulling, carrying and putting down objects are currently responsible for an extraordinary 66% of accidents and injuries in the pharmaceutical industry.
Production managers face a relentless focus on productivity
Pharma has a long way to go to match other industries' progress in rethinking how they operate to cut costs and contain staffing levels. Regardless of the subsector: big pharma, smaller companies, healthcare conglomerates and generics manufacturers may have different cost structures, but all have struggled to drive step-change productivity gains.
One aspect of the pharma manufacturing process where some of these challenges can be addressed is consistently overlooked. This article examines how the performance can be boosted with the use of smart lifting technologies designed for the pharma industry on:
- Weighing and dispensing
- Processing
- Packaging
Pharma manufacturing: Weighing and dispensing
The weighroom is an important entry point into pharmaceutical manufacturing, with strict requirements on cleanliness. It is the transition point for materials coming from the warehouse and entering the processing area. The handling of substances in the weighroom is crucial. Careful attention to layout, equipment and operations here are the starting point for an efficient manufacturing process.
Weighroom design and equipment differ depending on the type of processing that takes place, but some common principles should drive the design of any pharmaceutical weighroom: a unidirectional flow of materials and personnel, segregation between hazardous and non-hazardous materials, and separation of storage and manufacturing items and spaces.
“There is a lot of lifting at this stage in the pharmaceutical industry, often with sacks of 25kg to 50kg – any bigger and the materials become compressed,” says Søren Skriver Nielsen, Sales Director for TAWI in Denmark, who has long experience working with the industry. As they come off the dirty pallet, sacks or drums must be cleaned before entering production. “Everything here has to be easy to clean. For heavy lifting, however, equipment is often dirty and dusty, while chain hoists are slow,” Søren says.
“Vacuum lifters are much faster and easy to keep clean. Sometimes companies fear that lifting technology will slow them down. When they start using it, they find it is 10-15% faster than manual lifting, especially if moving sacks from one place to another. Made with high quality 316 steel, the machines can be hose-washed to prevent contamination.”
Mobile vacuum lifters are a semi-automatic solution that does not replace the employee but helps them perform lifting tasks with minimal effort and risk. These machines can move raw material into and within the weighroom and transport it from weighing to processing areas. ATEX certification can be important in some areas where the powder is mixed. This means each component of the lifting equipment must be designed and tested to meet requirements for reducing the risk of explosion, and installation must be carried out by ATEX trained personnel.
Pharmaceutical manufacturing: Processing
During the processing of pharmaceutical ingredients, the priority is to avoid contamination. Manufacturing pharmaceuticals is a sensitive process, including the delicate handling of active pharmaceutical ingredients (APIs). Production often takes place in protected cleanroom facilities designed to maintain extremely low levels of particulates, airborne organisms, or vaporised particles to maintain a safe environment. Every piece of equipment must be designed to generate minimal air contamination and be very easy to clean.
Take the experience of Ampliqon
Ampliqon is a Danish biotech company making PCR enzymes and laboratory reagents, whose products are widely used in hospitals, universities, research institutions and life-science industries internationally. At one point in the manufacturing process, Ampliqon uses TAWI lifting equipment to pour liquid from a barrel into small bottles without using a funnel, which carries a contamination risk.
This lifting technology permits flexible and precise actions to lift, turn and tilt all types of drums, barrels or pails, which can be tipped to exactly the right amount without needing to be emptied. In Ampliqon’s case, this is a customised solution for a very specific process.
“The ability to customise lifting equipment is essential to ensure the client is equipped with the best tool to optimise its processes and performance,” Søren Skriver Nielsen says. “Pharmaceutical companies are always striving to make the space they work in as small as possible to maintain high standards of cleanliness and avoid contamination, and often the cleanrooms have been built without consideration of lifting equipment. This means lifting machines often need to be adapted to work in confined spaces. Heavy and ungainly sacks or drums can be lifted without physical effort and emptied into a mixer safely and ergonomically without imposing repetitive strain on employees.”
Pharmaceutical manufacturing: Packaging
Mounting materials onto packaging machines are often heavy and cumbersome work. Reels of plastic film can weigh as much as 150kg. This heavyweight task poses a risk for the person handling the material, but can also cause a production halt if the materials are not swiftly installed in the machine. A fully mobile lifter, designed for use in pharmaceutical manufacturing areas, makes this process easier and more efficient, allowing ergonomic handling of heavy reels of packaging materials such as this:
Once the packing process is complete, the final stage of the pharma manufacturing process demands safe and reliable handling of packaged goods, often requiring boxes to be moved to and from pallets. Vacuum-assisted handling ensures that cartons filled with sensitive pharmaceuticals are not damaged. It also improves workplace ergonomics and safety, preventing workplace injury and muscle stress caused by repetitive lifting.
Do it like Denmark
For insight into future trends in pharmaceutical manufacturing, Denmark is a good place to start. First, pharma is a large part of the nation’s economy: measured by the number of employees relative to population, Denmark has the third-largest pharmaceutical industry in the world after Switzerland and Slovenia and is second in terms of the number of R&D personnel. So there is stiff competition for skilled labour in the sector, which cannot always rely on strong young people to do the extensive lifting required during the manufacturing process.
Moreover, the economy of this small Scandinavian nation is highly regulated, and pharmaceutical companies compete for labor by making their workplaces as safe and ergonomic as possible. As a result, the approach to manual lifting in the sector is often far ahead of regulations and recommendations elsewhere.
“Safety for workers goes hand in hand with production in Denmark’s pharmaceutical industry,” Søren says.” Pharma takes very good care of their employees, and there is also a shortage of workers, so they are fighting to get the right people. If the company doesn’t take care of its employees, they go somewhere else.”
The correct choice of lifting equipment opens the possibility of a much more flexible workforce. Age and gender are immaterial when a machine is doing the heavy, repetitive work that makes the manufacturing process onerous or dangerous for large parts of the potential workforce. Modern vacuum lifting equipment is largely intuitive and requires minimal training before workers feel comfortable using it.
“Most pharma companies are not aware of what lifting solutions exist and the benefits they can bring to the different steps of the manufacturing process,” Søren says. “And unlike fully automated robotic systems, they do not require a huge financial investment. Return on investment is usually measured in months.”
Conclusions
- Pharma manufacturing is complex and sometimes hazardous
- There is a relentless search for productivity and competition for skilled labour
- The manufacturing process demands precise, safe and hygienic lifting at the weighing, processing and packaging stages
- Customised, semi-automatic lifting equipment can offer productivity gains plus large health and safety benefits, with positive consequences for recruitment and retention.