Los tres tipos más habituales de lesiones por manipulación manual
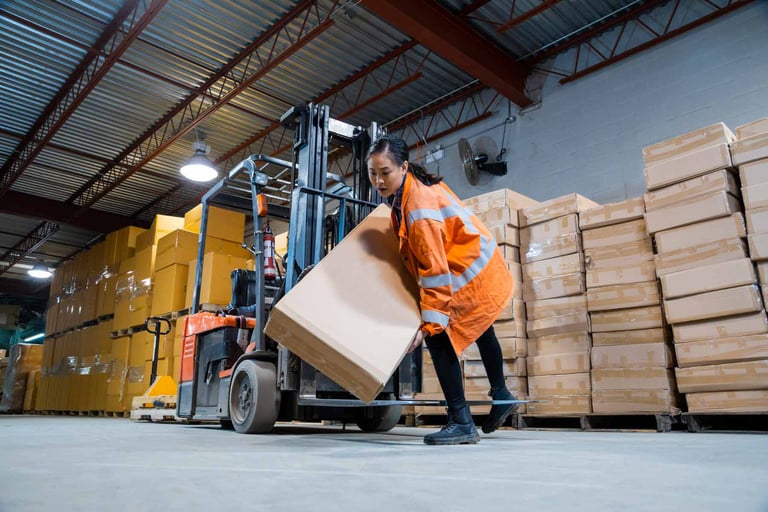
Los almacenes son entornos ajetreados, repletos de una compleja gama de equipos, enormes pilas de productos y una mano de obra que trabaja las veinticuatro horas del día. Este entorno dinámico aumenta significativamente el riesgo de daños en el lugar de trabajo y de lesiones por manipulación manual.
Solo en 2020 el sector del transporte privado y el almacenamiento registró 206.900 casos de lesiones y enfermedades no mortales. De estos, 99 800 dieron lugar a días de baja laboral (DAFW), 57 000 provocaron un traslado o restricción de puesto de trabajo (DJTR) y 50 100 fueron otros casos registrables (ORC). La tasa total de incidencia de casos registrados fue de 4,0 por 100 trabajadores en jornada completa equivalente (FTE).
¿Dónde se producen la mayoría de los accidentes en un almacén?
Los 5 grupos principales son muelles, carretillas elevadoras, cintas transportadoras, almacenamiento de materiales y elevación y manipulación manuales.
Las estadísticas de referencia de EE. UU. detallan las lesiones y enfermedades profesionales no mortales que implicaron días de baja laboral en el sector del transporte y el almacenamiento:
Característica del caso / Cantidad de casos
Naturaleza de la lesión o enfermedad
Esguinces, distensiones, desgarros: 42.280
Molestias, dolor: 15.630
Hematomas, contusiones: 10.370
Fracturas: 7.790
Cortes, laceraciones: 3.900
Parte del cuerpo afectada
Esplada: 16.910
Hombro: 9.840
Rodilla: 9.370
Varias partes del cuerpo: 8.540
Mano: 8.030
Incidente o situación causante de lesión o enfermedad
Golpeado por objeto o equipo: 12.100
Sobreesfuerzo al levantar o bajar: 11.950
Caída al mismo nivel: 10.940
Caída a un nivel inferior: 6.750
Incidentes de circulación con vehículos motorizados involucrados: 6.430
Oficina de Estadísticas Laborales, Transporte y Almacenamiento de EE. UU., 2016-2020..
Estas estadísticas revelan los riesgos tangibles a los que se enfrentan los trabajadores de este sector, con la alarmante cifra de 206 900 casos de lesiones y enfermedades profesionales no mortales. Las tres principales causas que provocan lesiones son el golpe contra un objeto o equipo, el sobreesfuerzo al levantar o bajar y la caída al mismo nivel. Los tres principales tipos de lesiones son los esguinces, las distensiones, los desgarros, molestias, dolores y hematomas y contusiones, que afectan especialmente a la espalda, los hombros y las rodillas.
Entre las lesiones comunes por manipulación manual se incluyen:
- Trastornos musculoesqueléticos.
- Distensiones y esguinces u otras lesiones de los tejidos blandos.
- Lesiones en las manos, como rotura de dedos u otros huesos de la mano.
- Lesiones de espalda, daños en la columna o hernias discales.
- Lesiones en el hombro.
- Cortes y laceraciones.
- Lesiones en los tobillos y pies.
Sin embargo, se pueden dividir en tres categorías principales:
- Ser golpeado por un objeto o equipo: Esta causa representa casi un tercio de este tipo de lesiones, siendo una parte importante de los trabajadores golpeados por camiones. Las investigaciones han puesto de manifiesto que cada año, una de cada cinco muertes en el lugar de trabajo y más de 12 000 lesiones están causadas por carretillas elevadoras y otros vehículos industriales. Estas estadísticas subrayan la importancia de que los empleados reciban formación periódica sobre carretillas elevadoras. Sin embargo, los accidentes no están ocasionados únicamente por las carretillas elevadoras. Cuando los artículos están mal apilados, pueden caerse y golpear a los empleados. El personal debe estar bien formado en la carga y descarga segura de palets, alturas y pesos de apilamiento seguro y la importancia de no subirse, apoyarse o caminar sobre palets.
- Sobreesfuerzos al levantar o bajar cargas: La manipulación manual representa más de un tercio de todas las lesiones laborales, incluidas torceduras, esguinces, lesiones de espalda, cortes, contusiones y fracturas óseas. Aunque puede haber ocasiones en las que su personal deba manipular materiales pesados, dichas tareas deben evitarse en la medida de lo posible.
- Caídas al mismo nivel: Las caídas al mismo nivel son una causa común de accidentes laborales que desembocan en lesiones y suelen incluir por lo general resbalones y tropezones en el suelo en el que está trabajando. Para prevenir accidentes como estos, se necesita una formación adecuada y procesos rigurosos para garantizar que el personal sepa cómo sujetar y mover objetos almacenados en altura de forma segura. A menudo es necesario equipo de protección individual (EPI), como cascos, así como señales de advertencia en áreas de peligro potencial.
Las causas comunes también pueden incluir la falta de formación, lo que puede provocar que un empleado sufra una lesión en la espalda al levantar incorrectamente una carga pesada, usando la espalda en lugar de las piernas. Además, la falta de información clara sobre el peso y la manipulación de los paquetes puede agravar los problemas. Un ejemplo in situ podría ser un empleado que intenta levantar una carga pero se da cuenta de que es demasiado pesada, lo deja caer sobre su pie y se provoca fracturas en el metatarsiano.
Comprensión de las lesiones por manipulación manual en el lugar de trabajo: ¿Quién es responsable?
La seguridad en el lugar de trabajo es una responsabilidad compartida que involucra a todos: empleadores, empleados, clientes e incluso visitantes. Cada persona que entra en un lugar de trabajo tiene un papel que desempeñar para garantizar su seguridad y la de los demás.
Sin embargo, desde una perspectiva legal, el nivel de responsabilidad varía. La mayor parte de la responsabilidad recae en el empresario, mientras que los empleados también tienen una obligación legal en materia de salud y seguridad. En Estados Unidos, una serie de leyes y regulaciones forman la base de un ambiente de trabajo justo y respetuoso, salvaguardando los derechos y el bienestar de los empleados de almacén.
Leyes y reglamentos laborales: un análisis más detenido
La Ley estadounidense de normas laborales justas (FLSA, por sus siglas en inglés) es una legislación federal que establece la referencia para los salarios y el horario laboral. Establece un salario mínimo, el derecho a recibir el pago de las horas extras, un mantenimiento de registros y normas para el trabajo infantil. Esta ley garantiza que los empleados reciban una compensación justa por su trabajo y compromiso.
La Ley estadounidense de Seguridad y Salud en el Trabajo (OSHA, por sus siglas en inglés) desempeña un papel crucial en el mantenimiento de un entorno de trabajo seguro y saludable. Establece las directrices que deben seguir los almacenes para prevenir accidentes y salvaguardar la salud de sus trabajadores. Esto incluye brindar formación adecuada, realizar simulacros de seguridad regulares y garantizar que todo el equipo sea seguro y esté en buen estado.
La Ley estadounidense de compensación al trabajador (FECA, por sus siglas en inglés) garantiza que si un empleado sufre una lesión en el trabajo, reciba una compensación adecuada. Esto no solo cubre los gastos médicos sino que también proporciona prestaciones de sustitución salarial a los trabajadores lesionados, ofreciendo una red de seguridad a quienes más la necesitan. Una multa de la OHSA puede ascender hasta los 7,000 $ por una infracción «menor» y hasta los 70 000 $ si se reincide.
El coste de los accidentes en el lugar de trabajo varía, pero según el Consejo Nacional de Seguridad de Estados Unidos, cada coste directo para una empresa es de 38 000 $ y puede llegar a 150 000 $ en costes indirectos.
Reglamentos en el ámbito del transporte y la logística
Existen normas adicionales en el ámbito del transporte y la logística que se deben cumplir para minimizar los riesgos de accidentes, garantizando la seguridad de las mercancías y de las personas involucradas en el transporte. El cumplimiento de estas normas también redunda en la rentabilidad, ya que evitar daños y accidentes reduce los costes relacionados con pérdidas y seguros, y protege la reputación de la empresa en el mercado.
Estos reglamentos incluyen normas relativas a los vehículos que cumplen con los estándares medioambientales y de seguridad, como las coberturas del seguro de camiones comerciales y las coberturas de seguro de almacén. También existen normativas en torno a la Manipulación y la Seguridad de Mercancías, diseñadas para evitar daños a los trabajadores y garantizar que las mercancías se manipulen, almacenen y transporten de forma que se eviten daños y pérdidas.
Evaluación de riesgos: un paso clave
Los empleadores están obligados a realizar una evaluación de riesgos, analizando todos los riesgos a los que están expuestos sus empleados. Se deben implementar medidas preventivas y de protección, como garantizar que cada trabajador haya recibido la información y formación necesarias en materia de salud y seguridad. En ocasiones, se podrían tomar medidas adicionales, por ejemplo, evitar que se produzcan situaciones peligrosas y proporcionar formación.
Si bien no existen normas de la UE que describan exactamente cómo se deben realizar las evaluaciones de riesgos, en algunos países las normas nacionales pueden incluir requisitos más detallados sobre el contenido y la forma de las evaluaciones de riesgos. . Lo mismo puede decirse de Estados Unidos.
A continuación se detallan algunas medidas que deben tomarse al realizar una evaluación de riesgos:
- Recopilar la información relevante.
- Identificar los posibles peligros.
- Evaluar los riesgos derivados de los peligros; por ejemplo, estimar la probabilidad y la gravedad de las consecuencias y decidir si el riesgo puede asumirse.
- Planificar acciones para eliminar o reducir los riesgos.
- Documentar la evaluación de riesgos.
Aunque se realicen evaluaciones de riesgos, estas simplemente identifican el riesgo en lugar de paliarlo. En TAWI, hemos diseñado una solución que mitiga significativamente el riesgo de lesiones asociadas a la manipulación de cargas, reduciendo incluso el esfuerzo físico de los empleados en un notable 80%.
Metafóricamente hablando, nuestros elevadores por vacío reducen la carga para usted y para sus empleados. Esto significa mitigar los riesgos asociados a una buena manipulación, proteger a los trabajadores de posibles daños y proteger a su empresa de pérdidas económicas y daños a su buena reputación. Nuestros productos mejoran la seguridad del almacén al reducir las lesiones, ya que los elevadores por vacío se encargan de hacer todo el levantamiento. Esto da como resultado menos esfuerzo físico, menor fatiga y una menor probabilidad de que la mercancía se caiga debido a un peso excesivo.
Conclusión
La comprensión de estos tipos comunes de lesiones por manipulación manual y la implementación de medidas preventivas pueden reducir significativamente el riesgo de lesiones en el lugar de trabajo, garantizando un entorno más seguro y productivo para su plantilla.
¿Quiere minimizar las lesiones y al mismo tiempo mejorar el rendimiento de su empresa? ¿Por qué no lee nuestra guía? «Guía completa para mejorar la eficiencia en la Logística de Almacén»..