Your guide to efficient order picking
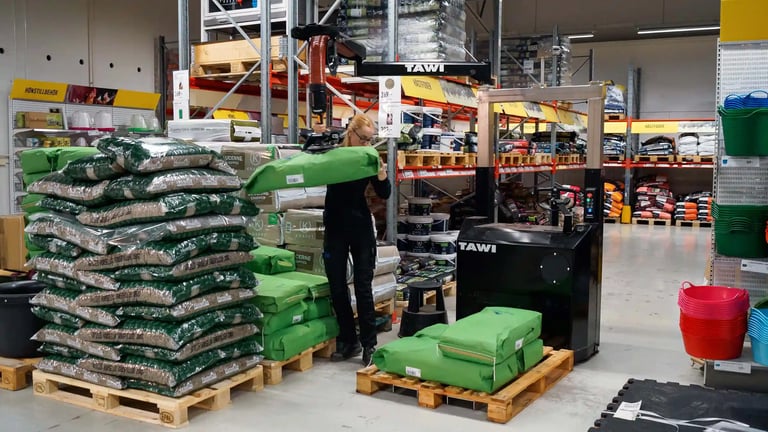
Is inefficient warehouse order picking slowing down order fulfilment? While many operations in your warehouse can be automated, order picking remains largely manual. Human logic is required in most settings.
That being said, order picking accounts for 55% of labour costs - creating great potential for labour savings. Technology and equipment designed for semi-automation can increase picking speed from up to 140 items per hour to up to 300 items per hour. It can also increase accuracy from 97% to 99%.
Let’s dive in and discuss a variety of logistic strategies.
What is order picking?
Order picking is the first and most important part of order fulfilment. After a customer’s order is placed, order pickers locate and “pick” it from the pallet rack to the forklift truck. This is often followed by loading up other orders, relocating orders to the packaging/shipping area, and unloading orders in the shipping line.
Manually picking from the pallet rack and loading on the shipping line requires reaching, bending, and straining. Even with proper ergonomics, the repetitive nature of this work leads to physical fatigue. Physical fatigue can slow down picking and increase the risk of injury.
With semi-automated tools, reaching and lifting are eliminated. The technology reduces bending, lifting, and strain by 80%. It also improves lifting and loading speed and the accuracy of placement.
Benefits of efficient order picking:
- Minimize staffing needs
- Ensure safe social distancing
- Pick more orders in less time
- Improve customer service
- Reduce damaged goods
- Support industry and regional compliance
- Improve warehouse ergonomics and safety
- Increase job satisfaction and employee retention
Traditional warehouse order-picking strategies
Which order picking methods best suit your business or logistics centre depends on several factors. This includes your:
- Business type
- Product type
- Warehouse layout
- Order mix
- Order volume
- Compliance requirements
Below are some of the most popular order-picking strategies. Many of these strategies can be combined.
Zone picking
If you have a large or high-volume warehouse, zone picking is a popular strategy. The warehouse is divided into designated zones, and each employee is responsible for picking SKUs from their zone.
This strategy streamlines and optimises logistics by minimising “traffic jams”. It also reduces the amount of walking required by each employee.
Batch picking
Batch picking is the concept of picking up multiple customer orders with the same SKU at the same time. This is popular in warehouses that only have a few SKUs, or a high volume of multiple SKUs.
For example, one batch may be filling up the forklift with eight of the same SKU. The next batch could be an entirely different SKU, but all from the same pallet rack.
Discrete picking
Discrete picking is ideal for small warehouses and warehouses with a limited range of SKUs. However, it’s time and labour-intensive, therefore not ideal for high-volume warehouses. This is because the picker picks all the items for a customer order, one SKU at a time.
Once the individual customer order is picked, pickers transfer and load it to the shipping area and begin on the next customer order.
Wave picking
Wave picking is similar to discrete picking, but pickers fulfil orders in “waves”, or designated times throughout the day. Employees are cross-trained, performing other job duties in between waves.
This strategy optimises labour and breaks the monotony of the day in small warehouses but is inefficient as fulfilment grows.
Combination of different strategies
The strategies above can be combined in a variety of ways.
- Batch picking could be used on slow order days, or slower order shifts.
- Discrete picking could be used for your highest volume SKUs.
- Zone picking may only be used during the holiday season or your busy season.
- Wave picking can be used in lower-volume areas of your warehouse.
How can you pick up speed in warehouse picking?
Warehouse order picking is further optimised by implementing a supportive fulfilment process. With the right tools, technology, and operational processes you can achieve high-speed fulfillment. From selecting inventory software to refining your layout, product placement, and more.
Below are tried-and-tested ways to improve speed and efficiency. They can be mixed and matched in different ways. Some may only be relevant during your high season.
Ensure product availability and stock tracking:
There are multiple software solutions available to help you track the status of your inventory. They all have automated inventory alerts to manage expiration dates and determine when to replenish your inventory.
Data and analytics:
Your warehouse software generates a variety of generic and custom reports. These reports help refine your approach to the strategies below.
Prioritize product placement:
By placing your most popular SKUs closest to the packaging/shipping area, you optimise order picking. Periodically revisit your most popular SKUs, to ensure high-volume SKUs are closest and low-volume SKUs are farther away.
Implement seasonal product strategies:
Your highest volume products may vary greatly during the holiday season or select SKU busy seasons. For example, you will fulfil more toys in the months before Christmas and more outdoor gardening equipment in the spring and summer months. Adjust product placement accordingly.
Review warehouse layout:
The way products are arranged in your warehouse greatly impacts the speed and efficiency of the picking process. Grouping similar items together is beneficial. This includes items that are often ordered together in close proximity. For example, place all laptops and laptop accessories in the same area, regardless of brand, make, and model.
Implement routing:
Closely related to product placement and the picking strategies mentioned above, warehouse routing ensures the flow of “traffic”. Every second a picker is left waiting for another picker to move out of the way is labour dollars being wasted.
Improving order picking efficiency with technology and equipment
Make no mistake, warehouse picking and logistics technology and equipment are a significant investments. In addition to the benefits we’ve already covered, they open the door for an entry-level workforce.
Below are a few specific investments to consider. Many warehouses utilise a combination of the options below.
Start using inventory management software
Warehouses that start off small often begin with nothing more than their sales software. As your supply chain or business grows, upgrading to inventory management software is required. If you already have software, consider if it’s time for an upgrade.
The most advanced options provide a variety of benefits that optimise order fulfilment and warehouse logistics. It also integrates with your sales software to provide in-depth data and analytics.
It can:
- Identify operational bottlenecks
- Map out your picking strategy
- Eliminate out-of-stock orders
- Minimize expired/deadstock
- Automate inventory tracking
- Calculate operational costs
- Support interdepartmental transparency
- Deliver in-depth data and analytics
Automated storage and retrieval systems
Also referred to as AS/RS technology, these systems minimise or eliminate the need for human product picking. They are high-end and designed for high-volume warehouses and warehouses with heavy or bulky loads. They are often used in combination with one another.
Robots: automatic guided vehicles (AGVs) and autonomous mobile robots are most often used to automate order stacking and picking of large and bulky items. These intelligent systems use a variety of cameras and sensors to navigate, pick, and unload.
Unit-load AS/RS: these systems utilise a variety of automated lifts and multi-directional conveyors to pick and relocate orders.
Vertical lift modules (VLMs): these systems are designed to enable maximum vertical storage, and depending on your SKU, narrow aisles. They utilise a combination of static racks and computerised cranes to stack and pick with efficiency. They can pick from several stories high and reach deep into racks.
Use the right order picking equipment
Semi-automated picking equipment is an investment, but it’s the most budget-friendly option. An employee is required to guide the equipment, but they don’t have to manually lift SKUs. The options below are a top choice for both small and large warehouses.
Order picker forklift: a variety of picking tools can be attached to forklifts and pallet trucks to enable your employees to pick without lifting, bending, or straining. They are comprised of heavy-duty suction cups, that can lift from the top or sides of boxes and other SKUs. Many are vacuum powered for rapid lift and release. Lifting capacity is up to 80 KG.
Vacuum lifter: these industrial-powered lifters ergonomically and effortlessly lift complex, fragile, and cold items such as heavy boxes, bags, sheets of glass, wood panels, doors, windows, parts, food items, and more. Vacuum lifters are often combined with the technology below. Maximum lift capacity is 270 kg.
Multifunctional lifter: these are versatile because they come with interchangeable suction cups to lift a variety of SKUs. The suction cups can be custom-made. This includes boxes, plastic bags, glass, metal canisters, and ununiform items. These vacuum lifters vary in their lift capacity, hose length, and hose diameter—lifting up to 270 kg. They are also cleanroom, ATEX, and safety and hygiene-compliant.
High-frequency lifter: the top choice for items that need to be lifted and loaded with extreme precision. They are joystick-controlled to rapidly lift, rotate, position, and release from the top or side. Use to lift boxes, blocks of meat, blocks of cheese, luggage, and more. Maximum lifting capacity is 65 kg.
Conclusion
Investing in a versatile and evolving range of warehouse lifting equipment improves throughput, safety, compliance, customer satisfaction, and employee satisfaction. It can help you increase the volume of orders processed without expanding your staffing levels or warehouse size. In fact, it’s likely to drastically reduce your labour hours!
If you are struggling with how to create a more efficient order picking process, reach out today — and we will find the best solution for your lifting needs.