What is material handling: The ultimate guide
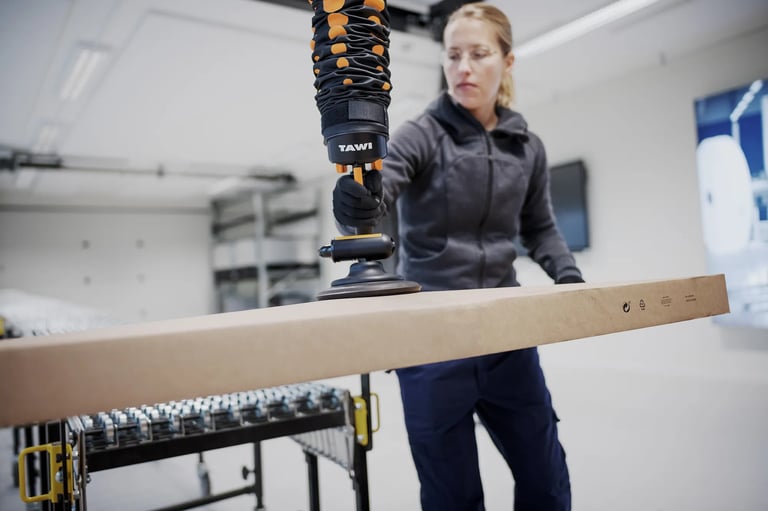
As you explore ways to streamline and optimise operations in your warehouse or production plant — it’s time to consider lifting equipment. There are a variety of lifters and accessories to choose from beyond traditional forklifts.
Strategic material handling is the foundation of successful supply chain logistics. Once implemented, your operational strategies must evolve as supply and demand grow and technology and tools advance. Let's dive in and explore the key principles behind handling your goods and raw materials. We'll also discuss some of the tools TAWI offers to optimise your operations.
What is material handling?
By dictionary definition, material handling refers to "the loading, unloading, and movement of goods, as within a factory or warehouse, especially by mechanical devices."
In other words, it's how you move, store, protect, control, and process products and materials of every kind. Processing is often a mixture of manual and semi-automated processing. The more automation, the better.
It includes, but is not limited to:
- The efficient processing and tracking of unit loads and individual goods from arrival to departure.
- Unloading the raw materials and parts required to create or assemble products.
- Safe and compliant storage of raw materials and goods on organised pallets and racks.
- Organising strategic unit loads to optimise manufacturing and order processing.
- Retrieving raw materials, supplies, and products to process, package, and ship.
- Loading to ship to a distribution centre or directly to a B2B or B2C client.
The benefits of strategic materials handling
Tailored strategies go beyond standard inventory management, as they deliver on numerous KPIs, including:
Reduced labour spending—manual handling consumes 25% or more of labour spending. This number can be drastically reduced with semi-automation.
Throughput—manual handling consumes up to 87% of production time. Semi-automated processes drastically improve loading, picking, unloading, and processing times.
Manufacturing costs—inefficient operations account for 70% of manufacturing costs.
Waste and damage—manual practices increase the odds of product damage and misplaced goods.
Internal risk—semi-automated and automated systems ensure safe social distancing, improved ergonomics, and reduced injury.
Improved job satisfaction—employees want a strategic approach to minimise burnout, boredom, injury, and turnover.
Compliance—modern technology and tools are designed to support industry and regional compliance, including ATEX zones and cleanroom compliance.
Customer service—the faster you produce goods and process your orders, the happier your end consumer will be.
Order accuracy—semi-automated strategies increase picking and shipping accuracy from 97% to 99%.
Universal Principles of Efficient Material Handling
There are ten universal principles for implementing materials handling in logistics. These principles are practical regardless of business type, product type, warehouse layout, or order volume. However, they must be built upon as your product mix and order/processing volume increase as software and technology advance.
#1 Strategic planning
The first step is defining your initial needs or current areas of opportunity. Then, you can begin to explore solutions, including improved layout, upgrading software, and determining the most effective semi-automated tools and technology.
#2 Agile and standardised
An exciting thing about semi-automating your material handling is that it lets you cross-train your employees. It also empowers you to employ more team members with entry-level skill sets.
#3 Functional
The system must work. It must provide a simplified method of moving items to and from designated areas in the warehouse. The route must be as streamlined and strategic as possible. Don't be shy about asking for employee input, as they often see areas of opportunity.
#4 Safe and ergonomic
Even if the load is light, repetitive bending, reaching, lifting, and transferring goods leads to physical burnout. Utilising industrial hoists and vacuum lifters improves ergonomics, minimising risk and enhancing job satisfaction. This includes systems that utilise gravity to your benefit.
#5 Move in loads
Moving one item at a time is inefficient. With the exception of large and bulky items, such as heavy canisters or large sheets, items should be moved in bulk for as much of the process as possible. This includes moving multi-item boxes, full pallets, containers, and totes.
#6 Space utilisation
Both vertical and horizontal space should be considered when implementing efficient materials handling in logistics. Even the plant or warehouse areas are narrow or have low ceilings. This often calls for a mix of forklift-mounted, ceiling-mounted, and stationary lifting tools.
#7 A to Z systematic
Implementing a coordinated system that handles all materials from arrival to departure. This includes any combination of:
- Processing incoming deliveries
- Unloading and inspecting
- Moving, unitising, and storing
- Production of raw goods
- Assembling parts
- Picking and packaging
- Labelling and shipping
- External shipping
- Returns handling
#8 Environmental sustainability
Prioritising the environment saves energy and materials spending, can improve operational safety, and attracts aligned consumers from hazardous materials handling to recycling and reusing waste.
#9 Semi-automated
From push-button or joystick-operated lifts and pickers to hoists, cranes, trolleys, forklifts, conveyor belts, robotics, and technologies that minimise manual lifting or picking. We dive into some of your top options further below.
#10 Lifecycle sensitive
Upgrading tools and technology is an investment that pays itself back in decreased labour spending, improved risk management, and optimised throughput. Be sure to calculate your lifecycle costs, including your:
- Capital investment
- Setup and installation
- Programming
- Training
- System testing
- Operational costs
- Maintenance and repairs
- Recycle and reuse potential
- Downtime for the transition
The three primary types of materials handling
Few operations are 100% manual, and smaller production and fulfilment plants may not have much automation. For example, a startup product someone launches in their home or garage. It might grow to the point that external storage and processing are required, but the initial system may have little more than a conveyor belt and push carts. As supply and demand grow, the need for semi-automation grows too.
Below are the three primary types of material handling in logistics:
1. Manual material handling
Employees lift, carry, deliver, and unpack boxes and containers by hand during this process. Or with little more than a hand trolley and straight-line conveyor belt. Maybe larger loads are transported via a forklift, but unpacking the load is typically manual. This system of operation is labour-intensive and can create bottlenecks and processing delays.
Even if the load is light, the repetitive nature of bending, reaching, and lifting can lead to neck, back, and shoulder strain—the heavier or bulkier the load, the greater the risk of injury.
Either way, a manual system has a higher risk of accident, injury, and employee turnover. While a top option for startups, this method of handling is generic, and it isn't time, labour, or cost-efficient.
2. Semi-automated material handling
This refers to systems utilising forklifts, electric trollies, and stationary, ceiling, and forklift-mounted hoists, cranes, and lifting equipment. These systems eliminate drop risk, enable single-person lifting of bulky goods, and lift materials that weigh up to 240 kg.
Semi-automation minimises bending, lifting, and straining by 80% or more. It can increase picking speed by two times or more depending on the types of materials you handle.
Lifting and gripping technology requires manual operation to attach, lift, reposition, and mount or stack. They are manually operated via ergonomic handles, automated push buttons, or joystick technology.
Most are operated from behind, which further decreases the risk of injury. This enables lifting deep into pallet racks and truck beds. Many options can be programmed to reach and position your highest racks.
The vacuum-powered suction cups and material handling hooks can be customised to lift your unique product range effortlessly. Many cups and hooks are interchangeable for maximum versatility.
3. Fully automated material handling
Fully automated processes all but eliminate the need for manual labour. Machines and robots complete the majority of the work. For example, people may only be required to:
- Unload and load at the loading dock.
- Perform quality assurance inspections.
- Operate and monitor technology.
These advanced systems utilise automated assembly lines, multi-route automatic picking, and forklifts with built-in sensors. They process orders up to 100 times faster than humans, with a fraction of the labour costs of a semi-automated process. Operating some of the technology can even be completed remotely.
Full automation drastically reduces injury risk and product damage. The primary roadblock is that these systems are a significant financial investment not in the budget for small to mid-sized operations.
Automation Tools and Technology
There is no one-size-fits-all solution, as your tools and technology must be tailored to your:
- Business type
- Product type
- Warehouse layout
- Ceiling height
- Order mix
- Order volume
- Compliance requirements
- And more
Let's dive into some of the most common products you will likely need.
Softwares
You are likely to utilise software, but if you haven't upgraded it in the last few years, it's time to consider your new options. The most robust software goes beyond inventory management to:
- Identifying warehouse bottlenecks.
- Automating maintenance alerts.
- Automating emergency and risk alerts.
- Advanced analytics for product forecasting.
- Advance analytics for staffing.
- Real-time inventory and order tracking.
- And more.
Storage systems
Storage systems maximise space and organise your parts, supplies, and inventory. This might include any combination of:
- Pallet racks
- Drive-through racks
- Push-back racks
- Sliding racks
- Interlocking stacking frames
- Bins, drawers, and shelves
- Floor-to-ceiling mezzanines
Automated handling systems
Mapping out efficient material handling in logistics requires stationary units that work together to minimise manual movement. This might include any combination of:
- Conveyer systems made from belts, rollers, or flexible chains.
- Automated Storage and Retrieval Systems (AS/RS) that utilise cherry pickers or other shuttle systems for quick retrieval.
- Robotic delivery systems automate moving products from one assembly line to the next or from one area of operations to another.
- Automatic guided vehicles use any combination of magnets, floor wires, vision sensors, or lasers to move heavy or bulky unit loads.
Industrial trucks
If your current volume doesn't warrant plant-wide conveyor systems, we use industrial trucks to unload, move, and load products. Even with conveyor systems, you'll require industrial trucks.
- Standard hand trucks, push carts, dollies, and box carts.
- Pallet jacks to lift and move full pallets.
- Manual or electric forklifts or pallet trucks to lift larger loads.
- Electric push trollies that minimise the force required to move loads.
Bulk material handling
If you manage bulk raw materials, bulk handling systems optimise space and simplify handling.
- Hoppers are large funnels that direct loose materials into containers.
- Reclaimers are machines that pick up loose materials from the stockpile.
- Automated stackers move loose materials without hands-on intervention.
- Bucket elevators to transport and store bulk items such as grain sacks.
- Grain elevators store and move grain safely and efficiently.
- Silos securely store and quickly access grains, coal, sawdust, food products, etc.
- Stackers are advanced forklifts explicitly designed for lifting and stacking heavy loads.
TAWI's Semi-Automated Lifts, Hoists, and Crane Systems
TAWI offers a curated mix of semi-automated tools to reduce physical lifting, straining, and bending. Our products are proven to improve safety, support cross-training, and reduce labour hours—while increasing production throughput.
1. Order picker forklifts
Order picker forklifts attached to any forklift or truck. They utilise heavy-duty suction cups to lift from the top or sides of each box. Their features are below.
- Compatible with any forklift or pallet jack.
- Have an articulating arm for optimal reach.
- Their adjustable height facilitates reaching deep into pallet racks.
- Their support legs provide extra stability.
- They can grip boxes from the top or the side.
- They lift boxes of all sizes, up to 80 kg.
- Have an articulating arm that rotates at 360 degrees for easy loading.
- Can be ordered with interchangeable lifting tools to meet your needs.
2. Vacuum lifters
Vacuum lifters utilise industrial-powered technology to lift, tilt, rotate, and load various goods without damage. They lift 270 kg with the use of interchangeable suction cups. Suction cups can be customised to your unique needs.
Vacuum lifts can be ceiling or floor-mounted or mounted to your forklift or pallet jack to lift:
- Boxes
- Taped boxes
- Plastic bags
- Glass sheets
- Plastic panels
- Wood panels
- Windows
- Food products
- Metal canisters
- Odd-shaped parts
- Carton boxes
- Wine boxes
- Blocks of meat
- Blocks of cheese
- Luggage
- And more
3. Cranes
Crane systems are ideal for servicing the entire assembly line or logistics unit and areas that don't require plant-wide mobility. Cranes can be securely mounted to the ceiling, roof beam, floor, or floor pillar. Some can be mounted to a forklift or a trolley that can be repositioned manually or by remote control.
Jib cranes are typically floor or column-mounted with overhead arms to extend reach up to 6 meters. They can be used for material handling up to 125 kg.
Our customisable overhead cranes have a bridge that empowers long-distance lifting. This includes options with telescopic arms, cranes built for low ceilings, linear and non-linear production, and a single or double girder. Aluminium cranes are used for goods with a maximum weight of 125 kg. Steel cranes are used for loads up to 1500 kg.
4. Hoists/Air hoists
Chain or wire hoists may be your best option for ultimate precision, accuracy, and control. Hoists can be utilised for lifting various boxes and materials and are ideal for large, heavy, and semi-flexible items such as bags. Some can be designed to lift more than one item at a time.
Our chain hoists are IP65-rated, compliant for outdoor use and use in challenging conditions. They are managed from a safe distance by remote control. The hook can be rotated 360 degrees and lift to 2500 kg.
High-speed wire hoists are ideal when you require speed and precision for lighter loads up to 120 kg. The grip is managed with a single-hand joystick, can tilt and rotate, and can adapt to fit the size of your load. It can also securely hold loads while you unload them.
Our vacuum-powered panel lifters have suction cups that lift to 500 kg. They have a 90-degree vertical and horizontal tilt capacity. They grip, tilt, and rotate large and heavy sheets and panels.
5. Container unloaders
Container unloaders empower your team to quickly and efficiently unload loose cargo from trucks and containers. These powerful unloaders are designed to decrease the strain on the body by 80% or more while optimising unloading times. They turn many two-person jobs into one-person jobs.
This includes a battery operated container unloader that can easily be moved between different doors or sites and mobile high-frequency unloaders that can be moved throughout your production area.
Want to Learn More About Semi-Automating Material Handling in Logistics?
If you aren't sure what tools will optimise your process or want to discuss our customisable options.