The 3 most common types of manual handling injuries
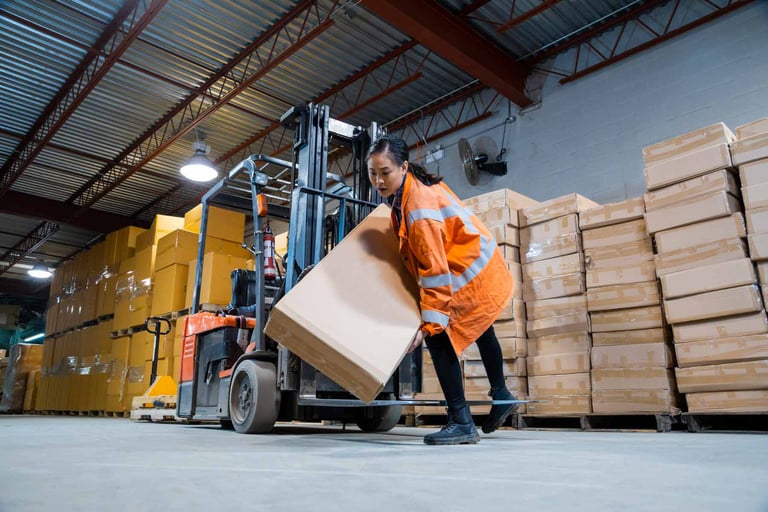
Warehouses are bustling environments, teeming with a complex array of equipment, towering stacks of products and a workforce labouring around the clock. This dynamic setting significantly heightens the risk of workplace harms and manual handling injuries.
In 2020 alone, the private transportation and warehousing industry reported 206,900 total recordable cases of nonfatal injuries and illnesses. Of these, 99,800 resulted in days away from work (DAFW), 57,000 led to job transfer or restriction (DJTR) and 50,100 were other recordable cases (ORC). The total recordable case incidence rate was 4.0 per 100 full-time equivalent (FTE) workers.
Where do most accidents occur in a warehouse?
The top five are docks, forklifts, conveyors, materials storage, and manual lifting and handling.
Benchmark US statistics detail out the specifics of non-fatal occupational injuries and illnesses which involved days away from work in the transportation and warehousing sector:
Case Characteristic Number of Cases
Nature of Injury or Illness
Sprains, strains, tears 42,280
Soreness, pain 15,630
Bruises, contusions 10,370
Fractures 7,790
Cuts, lacerations 3,900
Part of the Body Affected
Back 16,910
Shoulder 9,840
Knee 9,370
Multiple body parts 8,540
Hand 8,030
Event or Exposure Leading to Injury or Illness
Struck by object or equipment 12,100
Overexertion in lifting or lowering 11,950
Fall on the same level 10,940
Fall to a lower level 6,750
Roadway incidents involving motorised land vehicles 6,430
U.S Bureau of Labor Statistics, Transportation and Warehousing, 2016 - 2020.
These statistics reveal the tangible risks faced by workers in this sector, with an alarming 206,900 cases of nonfatal occupational injuries and illnesses. The top three events leading to injury are being struck by an object or equipment, overexertion in lifting or lowering and falling on the same level. The top three impacts on workers are sprains, strains, tears, soreness, pain, and bruises, contusions, particularly affecting the back, shoulder and knees.
Common manual handling injuries include:
- Musculoskeletal disorders.
- Strains and sprains, or other soft tissue injuries.
- Hand injuries, such as broken fingers or other broken bones in the hand.
- Back injuries, spinal damage or slipped discs.
- Shoulder injuries.
- Cuts and lacerations.
- Ankle and foot injuries.
However, they can be divided into three main categories:
- Being Struck by Object or Equipment: This cause accounts for almost a third of these types of injuries, with a significant portion of workers being hit by trucks. Research has found that every year, one in five workplace fatalities and over 12,000 injuries are caused by forklifts and other industrial vehicles. These statistics underscore the importance of regular forklift training for employees. However, accidents are not solely caused by forklifts. Incorrectly stacked items can lead to them tumbling, falling and hitting employees. Staff should be well-trained in safe loading and unloading of pallets, safe stacking heights and weights, and the importance of not climbing, leaning or walking on pallets.
- Overexertion in Lifting or Lowering: Manual handling accounts for over a third of all workplace injuries, including strains, sprains, back injuries, cuts, bruises and broken bones. Although there might be occasions when your staff must handle heavy materials, such tasks should be avoided as much as possible.
- Falls on the Same Level: Falls on the same level are a common cause of workplace accidents that result in injury, these typically include slips and trips on the floor you’re working on. To prevent accidents like these, adequate training and robust processes are needed to ensure that staff know how to secure and move objects stored at height safely. Personal Protective Equipment (PPE) like hard hats is often necessary, as well as warning signs in areas of potential hazard.
Common causes can also include lack of training which can lead to an employee suffering from a back injury from incorrectly lifting a heavy load, using their back rather than their legs. Further to this, a lack of clear weight and handling details on packages can exacerbate issues. An in situ example could be that an employee attempts to lift a load but soon realises it is too heavy, dropping it on their foot, causing metatarsal fractures.
Understanding Manual Handling Injuries in the Workplace: Who’s Accountable?
Workplace safety is a shared responsibility that involves everyone - employers, employees, clients and even visitors. Each individual who enters a workplace has a part to play in ensuring their safety and the safety of others.
However, from a legal perspective, the level of responsibility varies. The lion’s share of the responsibility falls on the employer, whilst employees also have a legal obligation towards health and safety. In the US, a series of laws and regulations form the foundation of a fair and respectful working environment, safeguarding the rights and welfare of warehouse employees.
Labor Laws and Regulations: A Closer Look
The Fair Labor Standards Act (FLSA) is a federal legislation that sets the benchmark for wages and working hours. It lays down a minimum wage, eligibility for overtime pay, recordkeeping and standards for child labor. This law ensures that employees receive fair compensation for their hard work and commitment.
The Occupational Safety and Health Act (OSHA) plays a crucial role in maintaining a safe and healthy work environment. It sets the guidelines that warehouses must adhere to in order to prevent accidents and safeguard the health of their workers. This includes providing adequate training, conducting regular safety drills and ensuring all equipment is safe and in good condition.
The Worker’s Compensation Act (FECA) ensure that if an employee is injured at work, they receive suitable compensation. This not only covers medical expenses but also provides wage replacement benefits to the injured workers, offering a safety net to those who need it most. An OHSA fine can cost up to $7,000 for a “minor” infraction, and up to $70k for repeat offenders.
The cost of accidents in a workplace varies but according to the National Safety Council, every direct cost to a company is $38,000 and can be as much as $150,000 in indirect costs.
Regulations in Transportation and Logistics
There are additional transportation and logistics regulations that must be adhered to in order to minimise the risks of accidents, ensuring the safety of the goods and the people involved in transportation. Adherence to these regulations also leads to cost efficiency, as avoidance of damages and accidents reduces costs related to losses and insurance, and protects the reputation of the warehousing business in the market.
These regulations include rules surrounding vehicles complying with safety and environmental standards, such as commercial trucking insurance and warehouse insurance coverages. There are also regulations surrounding Goods Handling and Safety, designed to prevent damage to workers and ensure goods are handled, stored and transported to prevent damages and losses.
Risk Assessment: A Key Step
Employers are required to conduct a risk assessment, evaluating all the risks their employees are exposed to. Preventative and protective measures must be put in place, such as ensuring that each worker has received the necessary health and safety information and training. Sometimes, additional measures might be taken, for example, preventing dangerous situations from occurring and providing training.
While there are no EU rules that describe exactly how you should conduct risk assessments, in some countries, national rules may include more detailed requirements concerning the content and form of risk assessments. The same can be said for America.
Here are certain actions to take while conducting a risk assessment:
- Collect the relevant information
- Identify the possible hazards
- Assess the risks arising from the hazards; for example, estimate the probability and severity of the consequences and decide whether the risk can be tolerated
- Plan actions to eliminate or reduce risks
- Document the risk assessment
Even though risk assessments are conducted, they merely identify the risk instead of alleviating it. At TAWI, we've engineered a solution that significantly mitigates the risk of injuries associated with goods handling, even reducing physical strain on employees by a remarkable 80%.
Our vacuum lifters figuratively lighten the load for you and your employees. This means less mitigating risks associated with good handling, protecting workers from harm and protecting your business from financial loss and damages to reputation. Our products enhance warehouse safety by reducing injuries, as the vacuums handle all the lifting. This results in less physical strain, reduced fatigue and a lower likelihood of goods being dropped due to excessive weight.
Conclusion
Understanding these common types of manual handling injuries and implementing preventive measures can significantly reduce the risk of workplace injuries, ensuring a safer and more productive environment for your workforce.
Want to minimise injuries whilst bolstering business performance? Why not read our guide: "The Complete guide to improving efficiency within warehousing logistics".