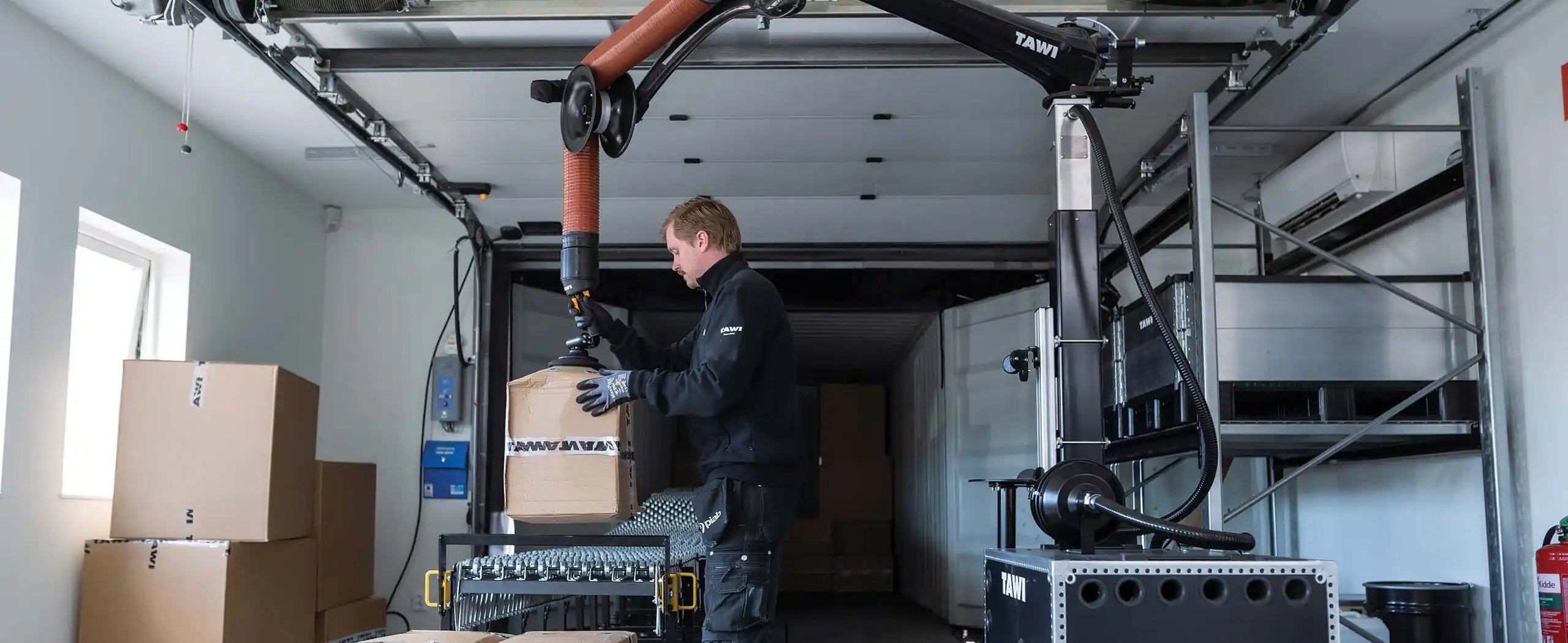
Ergonomic Lifting Solutions
Make your material handling safe & efficient
Find out what our customers sayWhat Do You Want To Lift?
Want to lift something else? View all applications here
Why TAWI?
Our Lifting Equipment
Vacuum Lifters
Use vacuum power to grip and lift all kinds of loads. User-friendly lifters for safe and efficient material handling.
View products - Vacuum LiftersMobile Vacuum Lifters
Easily moved around your facility with forklift or LLOP. Ideal for order picking or other logistic lifting processes.
View products - Mobile Vacuum LiftersContainer Unloading Systems
Mobile lifters for unloading and loading shipping containers and trucks. Improving efficiency and ergonomics.
View products - Container Unloading SystemsPortable Lifting Trolleys
Portable, electric stackers, easily adapted to meet your specific requirements.
View products - Portable Lifting TrolleysJoin us in person at our upcoming Trade Shows
Improved ROI at Yusen Logistics
TAWI's vacuum lifting equipment has removed 100% of the lift and has completely streamlined the process. In a timed experiment, the vacuum lifters are 20% more efficient, requiring 30% less labour.
Rob Hamborg, Yusen Logistics UK Site Manager
Â
Solutions for a Wide Range of Industries
Airports & Ports
Ergonomic lifting solutions reduce the high number of work-related injuries associated with manual handling
Read more - Airports & PortsLogistics & Warehousing
High speed handling, loading and unloading of all types of goods.
Read more - Logistics & WarehousingFood & Beverage
Reliable handling of everything from baking ingredients to blocks of cheese or kegs of beer.
Read more - Food & BeveragePharma
Safe handling of drums, boxes, reels and more in highly sensitive environments.
Read more - PharmaChemical
Ergonomic lifting systems for safe use in ATEX zones and clean rooms. For efficient handling of chemicals.
Read more - ChemicalAutomotive
Ergonomic handling of automotive components, everything from tires to windshields.
Read more - AutomotiveWood & Steel
Effortless lifting of wood, glass and steel products, including tilt and rotation of large sheets and panels.
Read more - Wood & SteelRenewable Energy
Versatility in handling solar panels across all stages of logistics.
Read more - Renewable Energy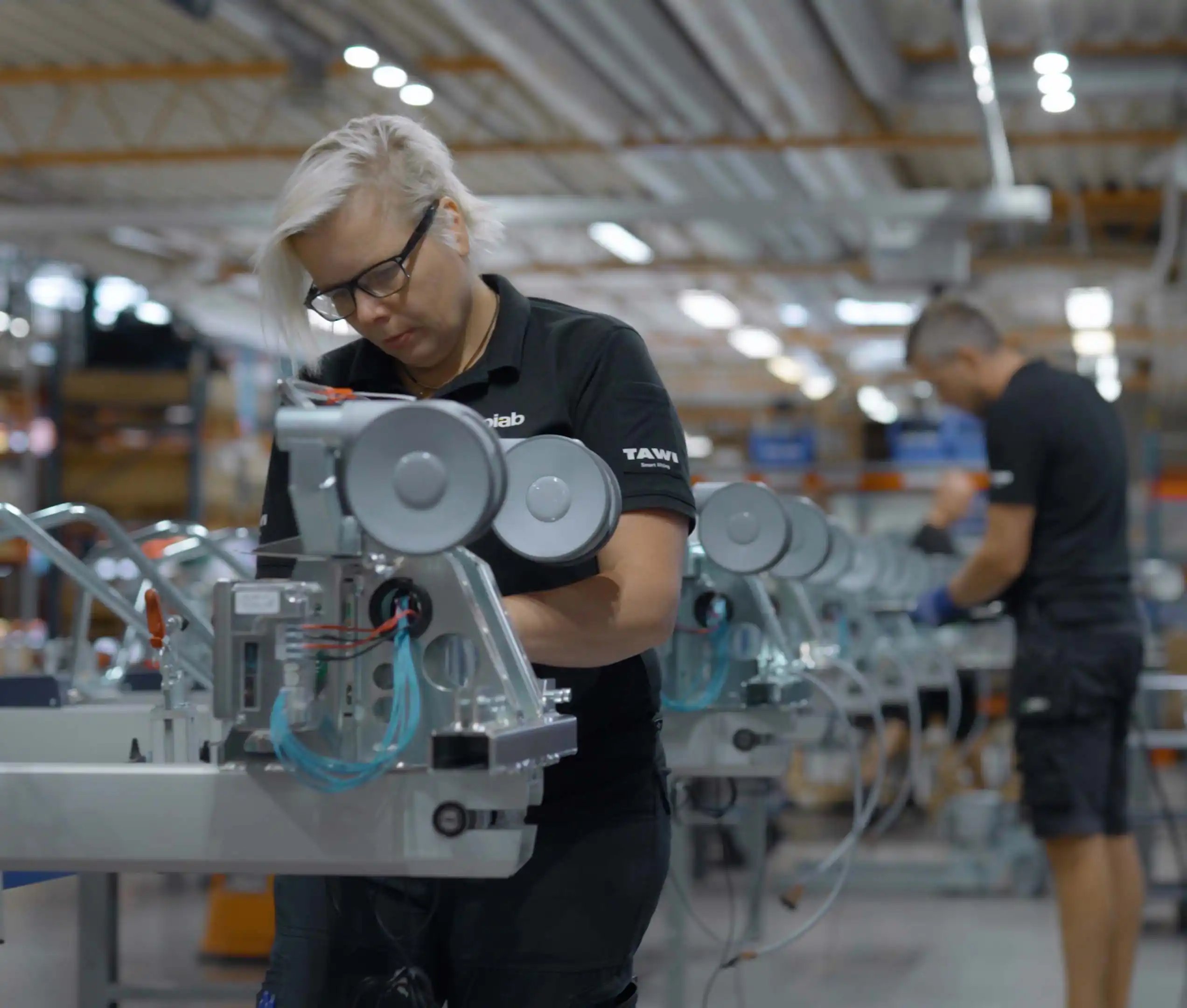
Swedish Inventors since 1923
We provide a complete range of ergonomic lifting solutions, standard and customized. TAWI lifting equipment enables businesses to move from manual handling to smart lifting solutions in production, logistics, and distribution. Our solutions are the first step from a fully manual handling position onto the journey of automation; a quick and cost efficient step.
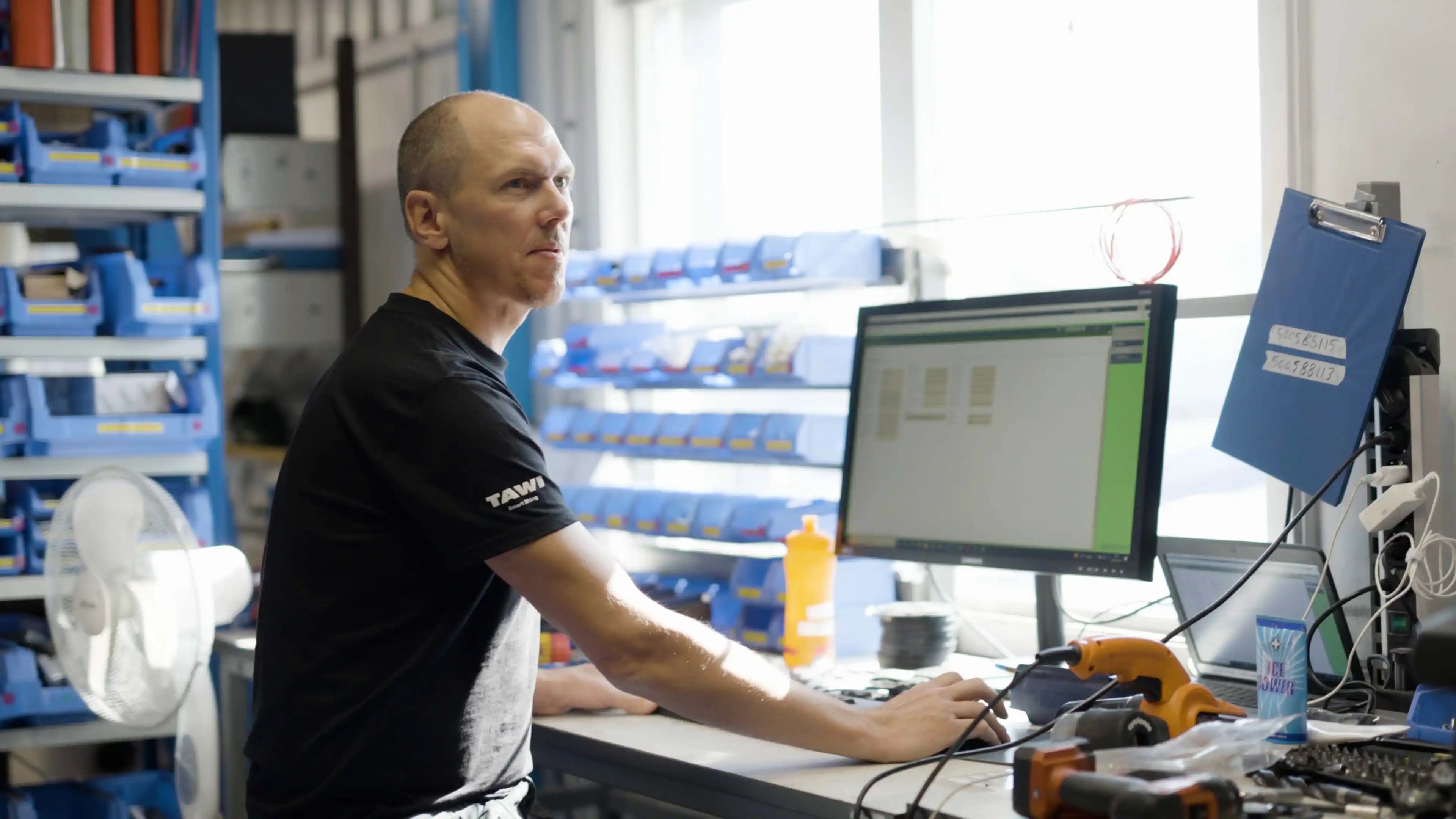
Service & Support
TAWI is there for businesses that want to improve their employees’ working conditions and increase productivity and workforce flexibility. When you invest in TAWI lifting solutions, our service and support team will ensure that the equipment never fails you. Choosing TAWI means getting Swedish quality and reliability in products, service, and support.