Lifting Insights
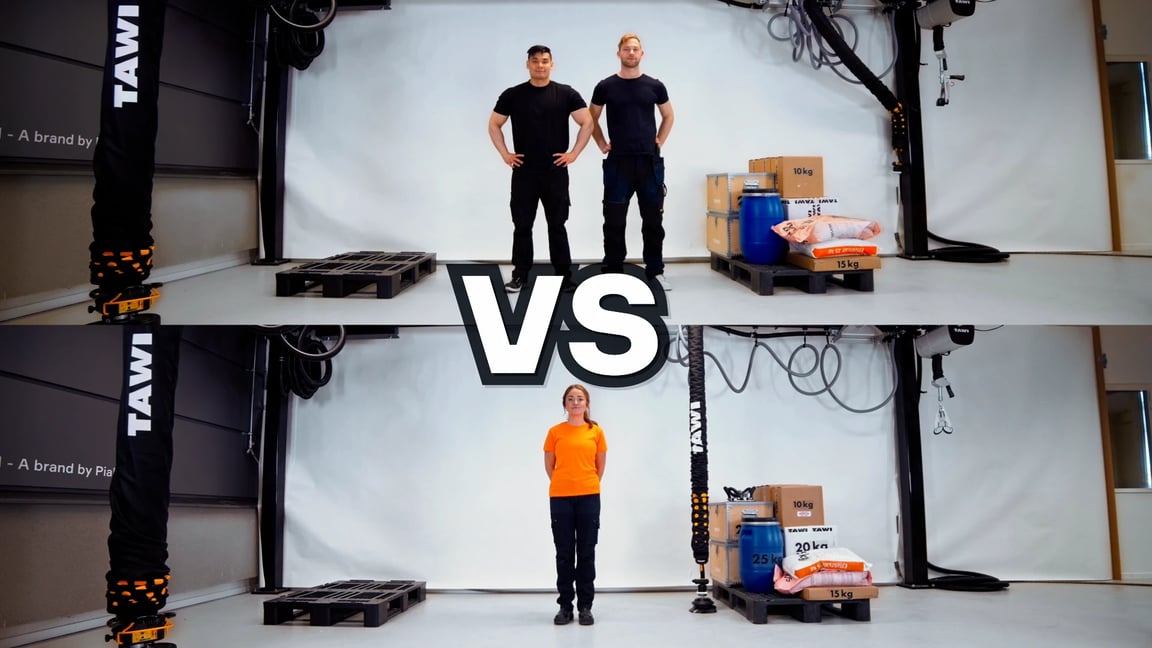
Manual Lifting vs Smart Lifting in the Modern Workplace
From warehouses to factories, manual lifting safety remains important as ever, given that manual lifting is a part of daily operations. But behind every box lifted or load heaved is a hidden cost: injury, absenteeism and long-term health consequences for workers.
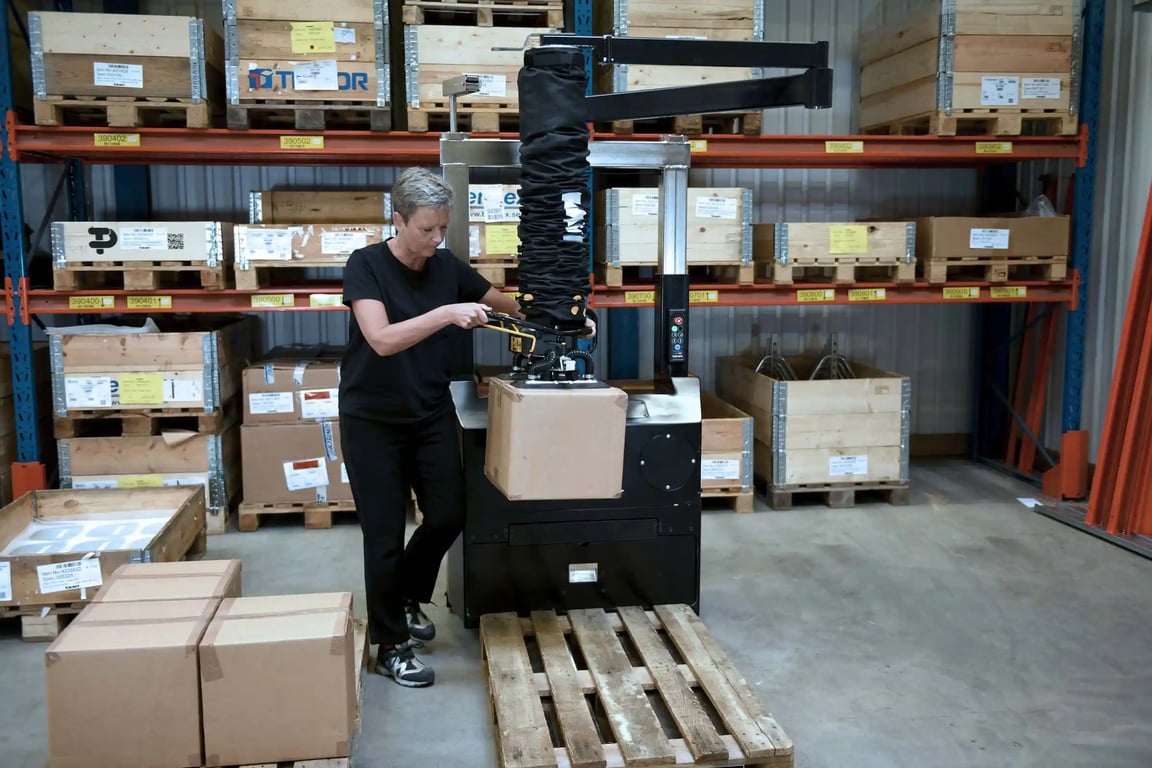
Smart Lifting vs Full Automation: Finding the Balance in Manufacturing Efficiency
Flexible material handling is crucial for unlocking greater manufacturing efficiency, but in a world racing toward automation, choosing the right solution isn’t always straightforward.
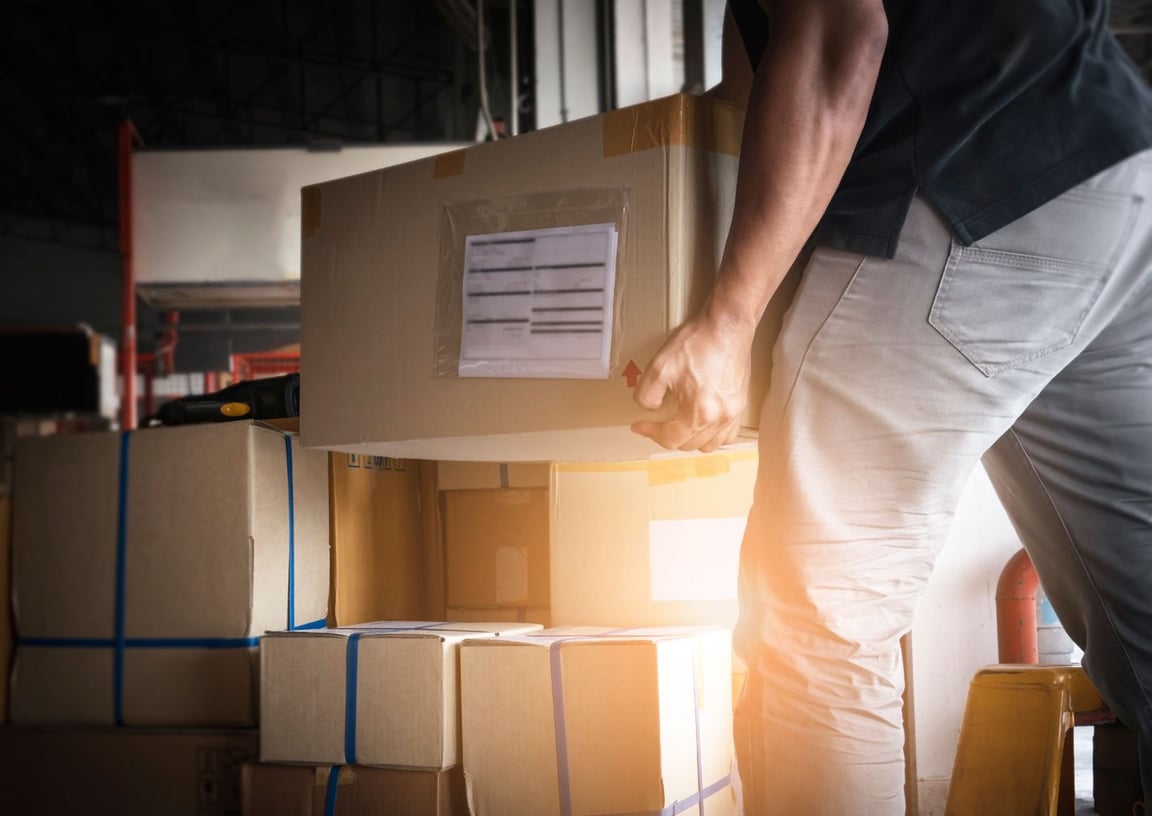
Lifting Weight Limits at Work: What's the Maximum You Can Lift?
This guide explores maximum weight limits for lifting at work. It provides insights on recommended maximum weights for employees and offer practical tips for maintaining a safe working environment.
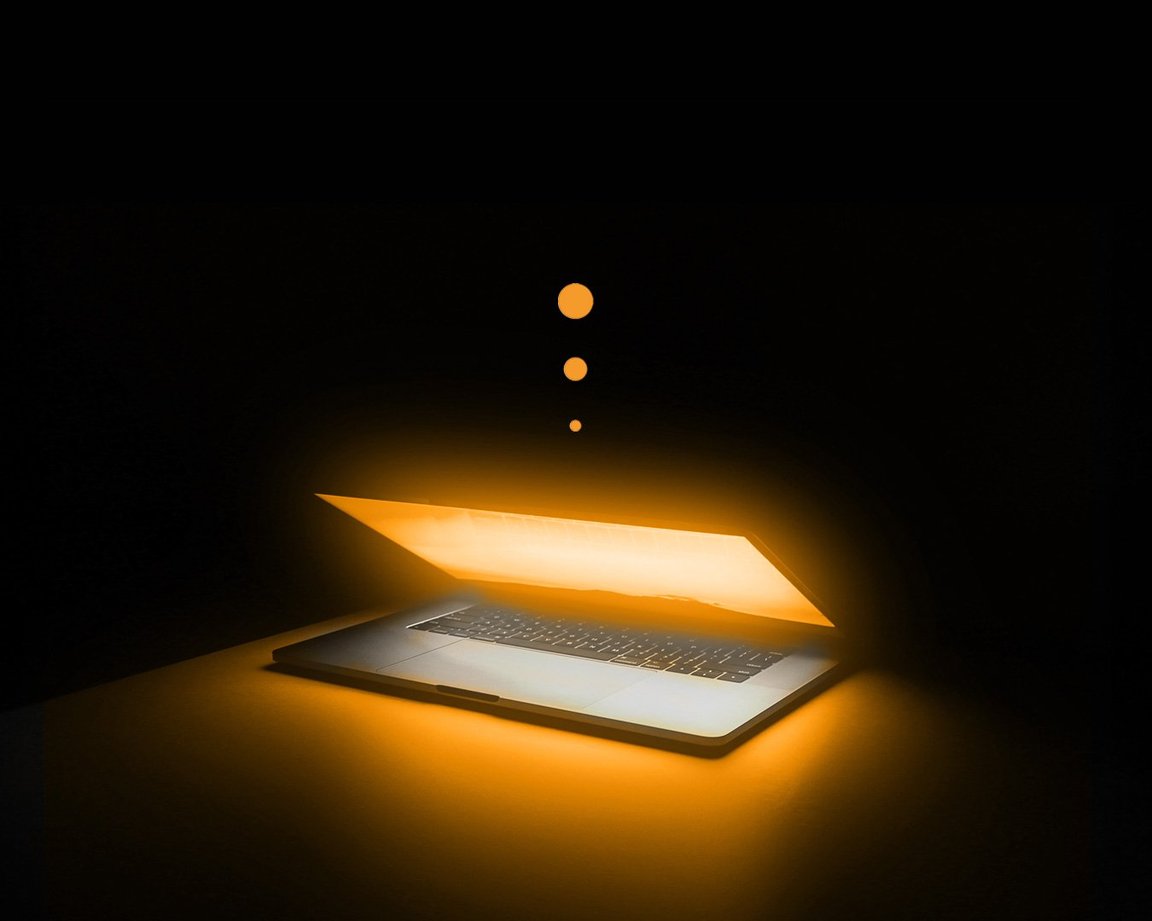
Smart Lifting Starts Here – Welcome to the New TAWI Website
We’ve launched our new scalable and adaptable website to enhance customer experience and digital presence.
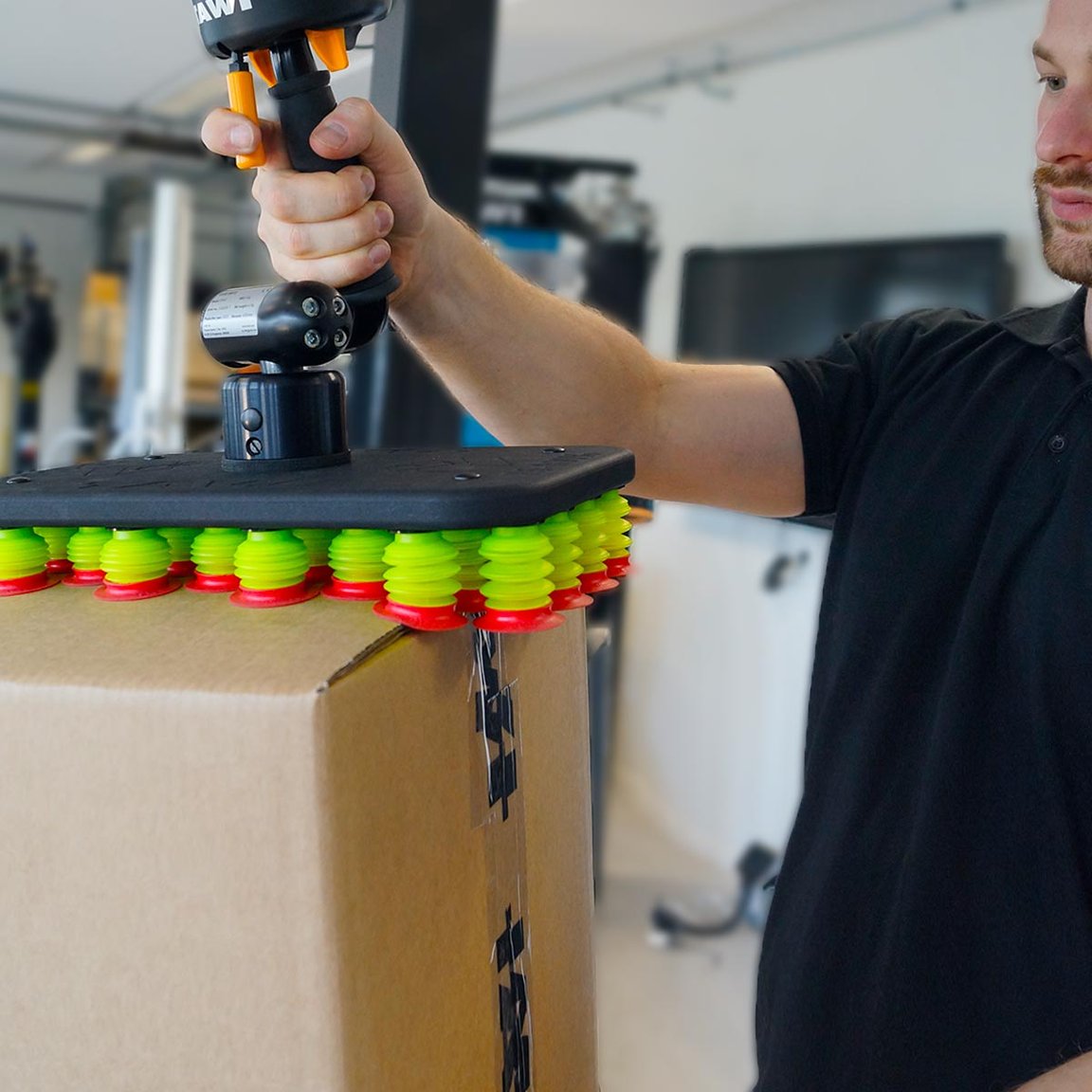
Handle More with Less Effort – Introducing TAWI FlexiGrip
In today’s fast-moving logistics and warehouse environments, time is critical — but so is safety and reliability. Lifting systems need to keep up with the demands of modern operations, especially when the loads aren’t always perfectly aligned or evenly packed. That’s why we developed TAWI FlexiGrip: a new smart suction foot designed for high-speed box handling.
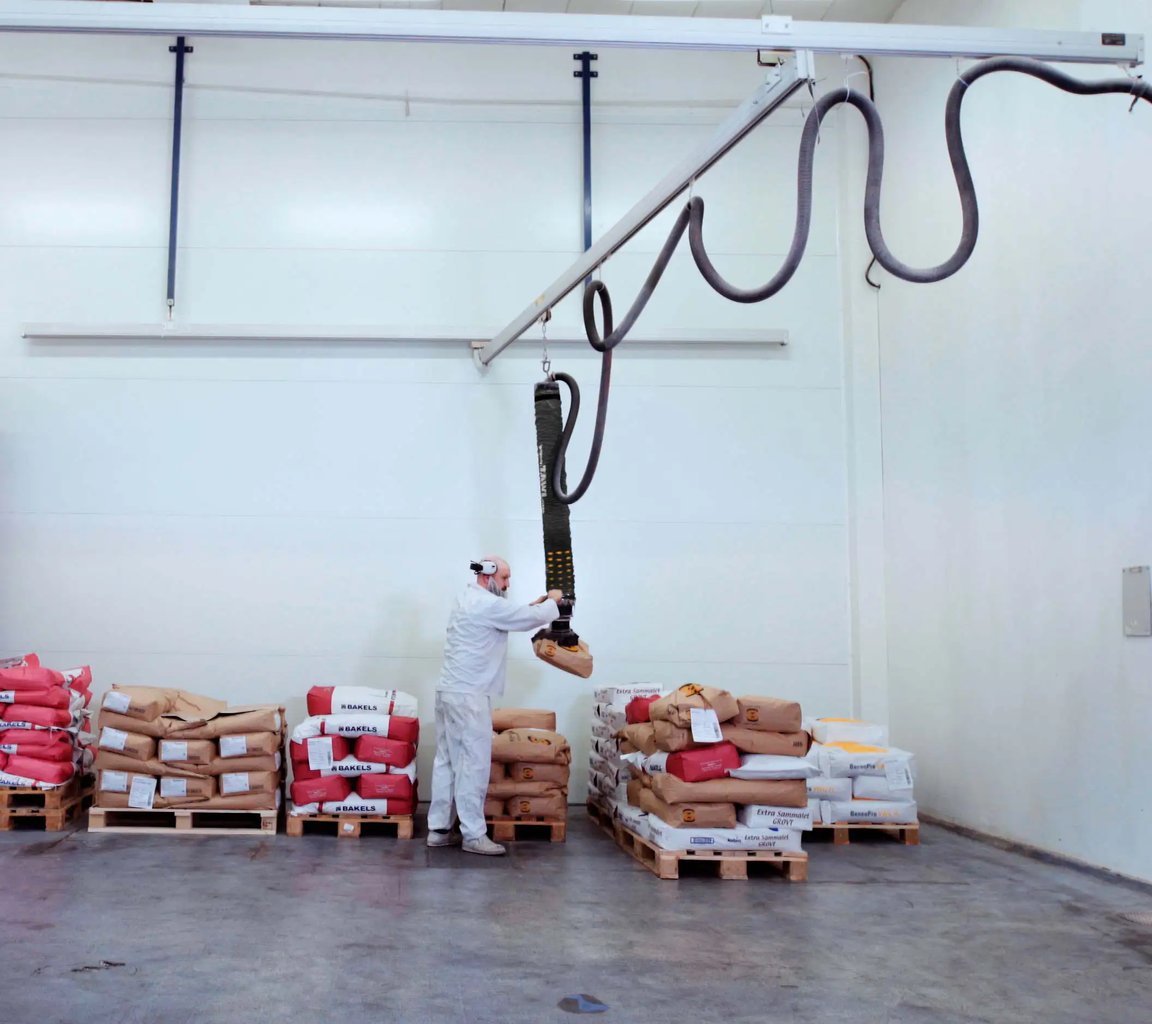
Enhancing Food Industry Safety: The Role of Sack Lifters in Efficient Handling
The demand for faster food and beverage processing has intensified due to evolving consumer habits. In recent years, a surge of “conscious consumers” has emerged—individuals who prioritise fresher, healthier foods without additives or preservatives. However, the absence of additives means that food spoils more rapidly.
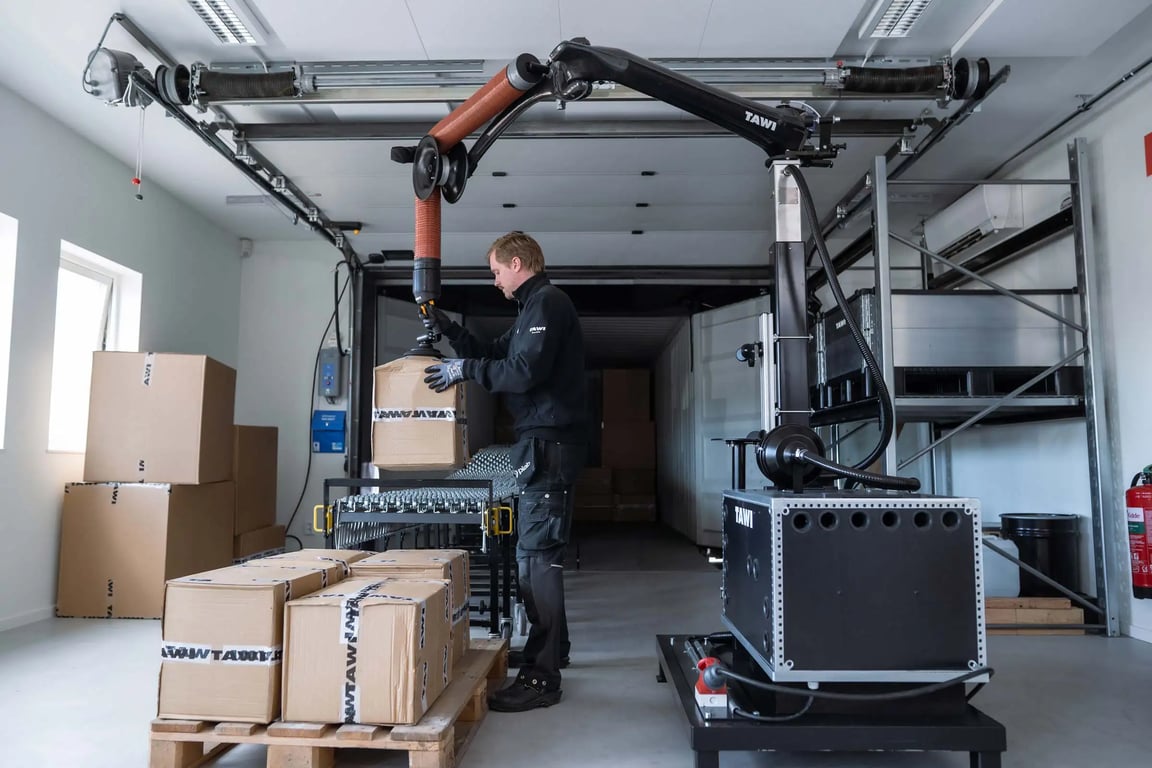
Visit TAWI at CeMAT 2025: Discover a Mobile Solution for Your Lifting Needs
Save the date! TAWI will be at CeMAT 2025, Australia’s leading trade show focused on intralogistics, robotics and automation, warehousing, supply chain management, and material handling. Come to Sydney to see TAWI’s mobile lifting solutions in action.
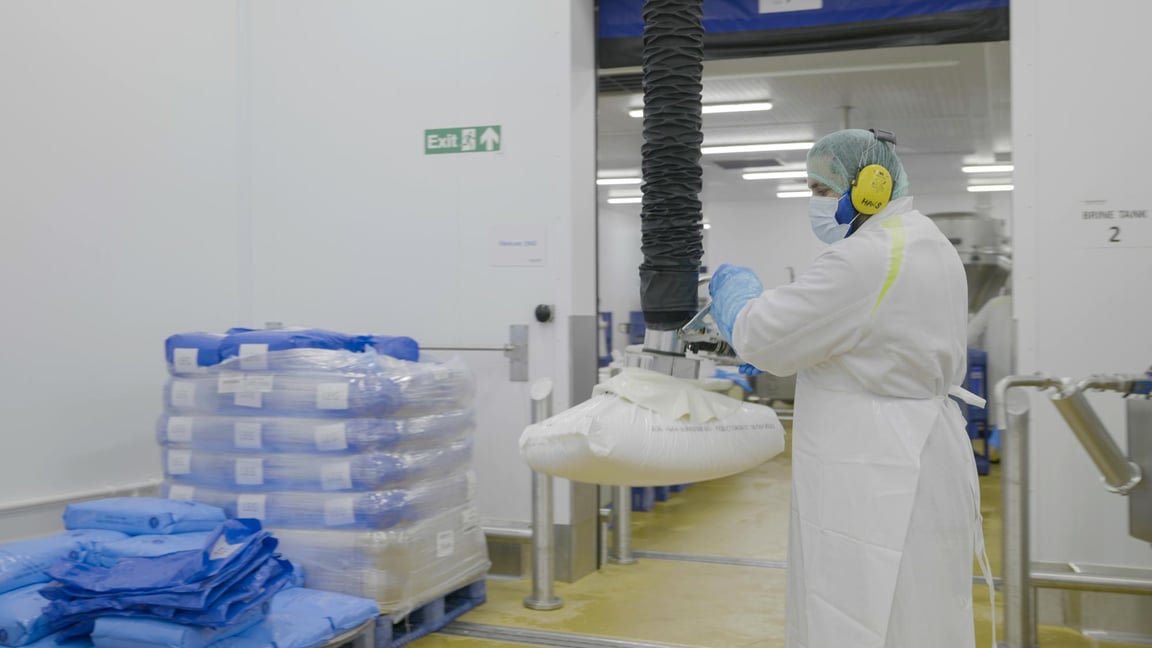
Innovation in Food and Beverage Industry: Trends & Challenges in 2025
Innovation in food and beverage industry is driven by shifting consumer demands, technological disruption, and sustainability concerns. To stay competitive in 2025 and beyond, businesses must not only keep up with evolving food industry trends but also proactively address the challenges that come with change.
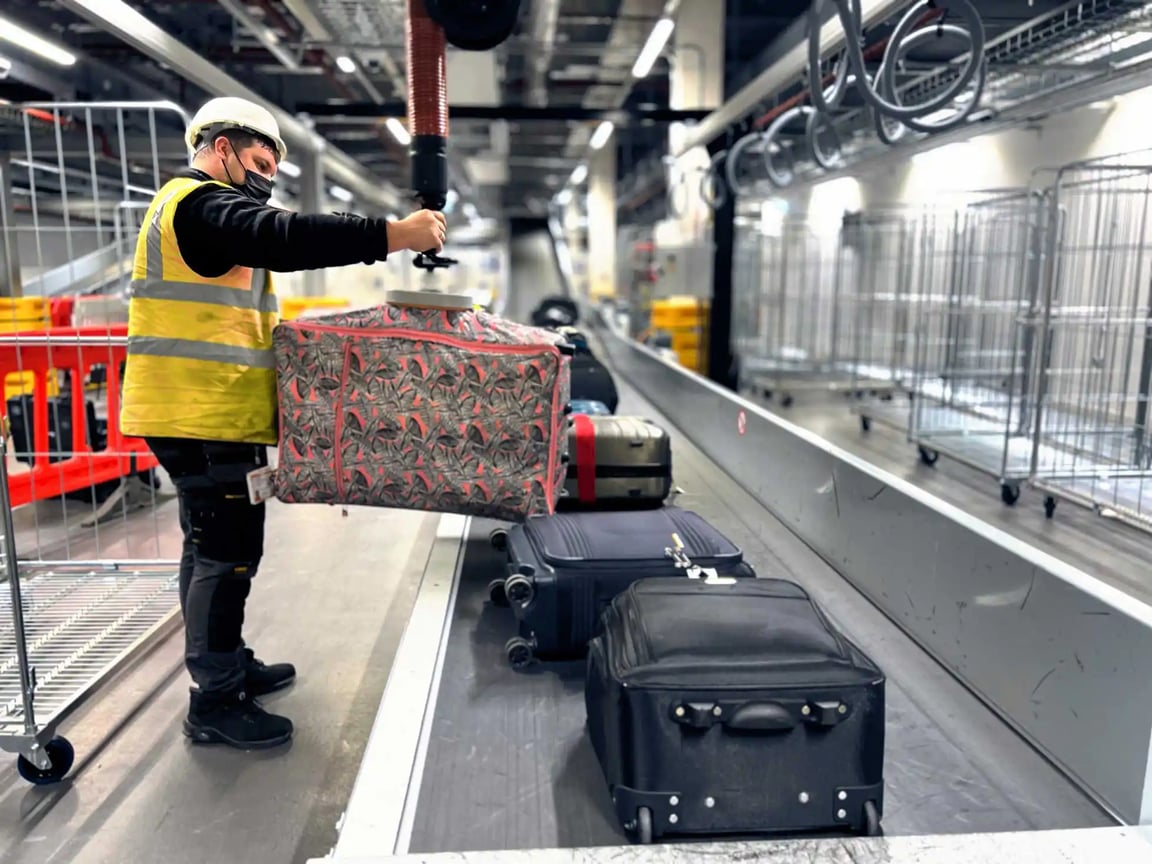
The True Cost of Getting Baggage Handling Wrong
People may joke about how baggage is not handled with care or often gets lost at transfer locations when they travel. But the truth is passengers have high expectations about their baggage, and there is a cost when baggage handling is done poorly – a cost that is being paid by staff, productivity, and budget.
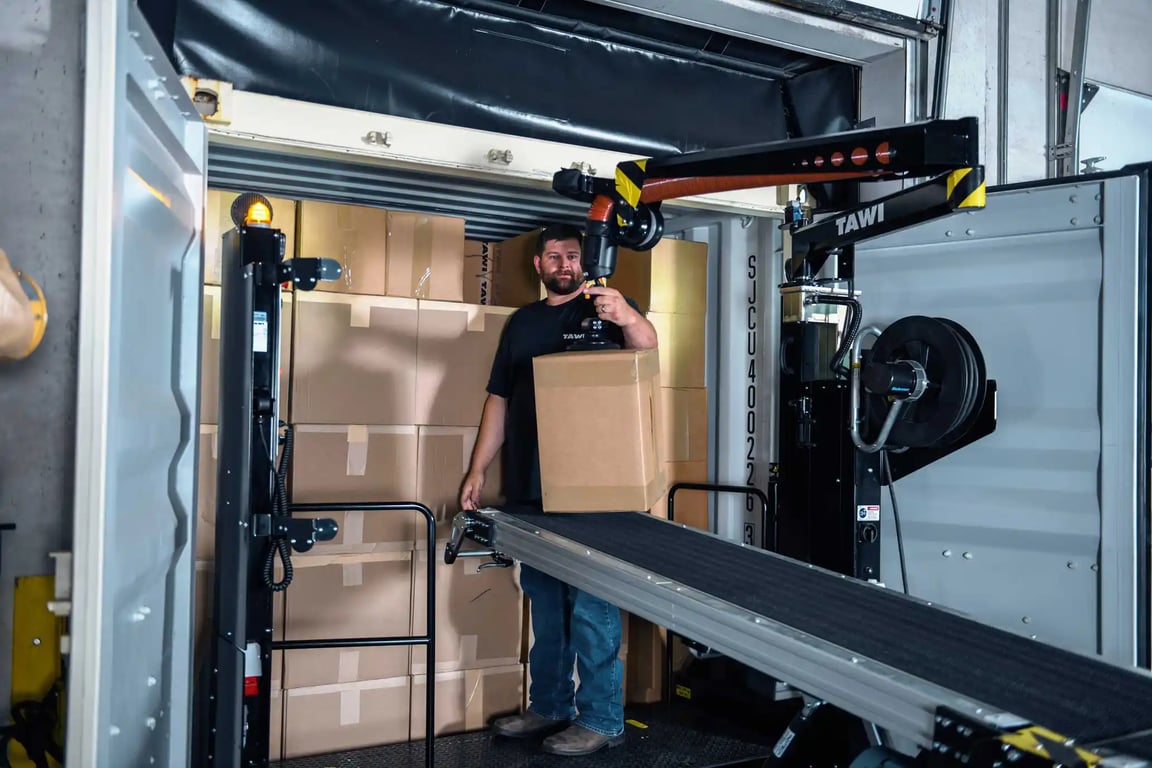
Streamline logistics: enhance efficiency with the right container unloading solution
Container unloading is one of the few remaining labour-intensive aspects of the modern economy. Due to the diverse range of items and the limited spaces within which they are packed, loading and unloading these large steel crates are among the last processes in logistics that rely heavily upon manual labour.
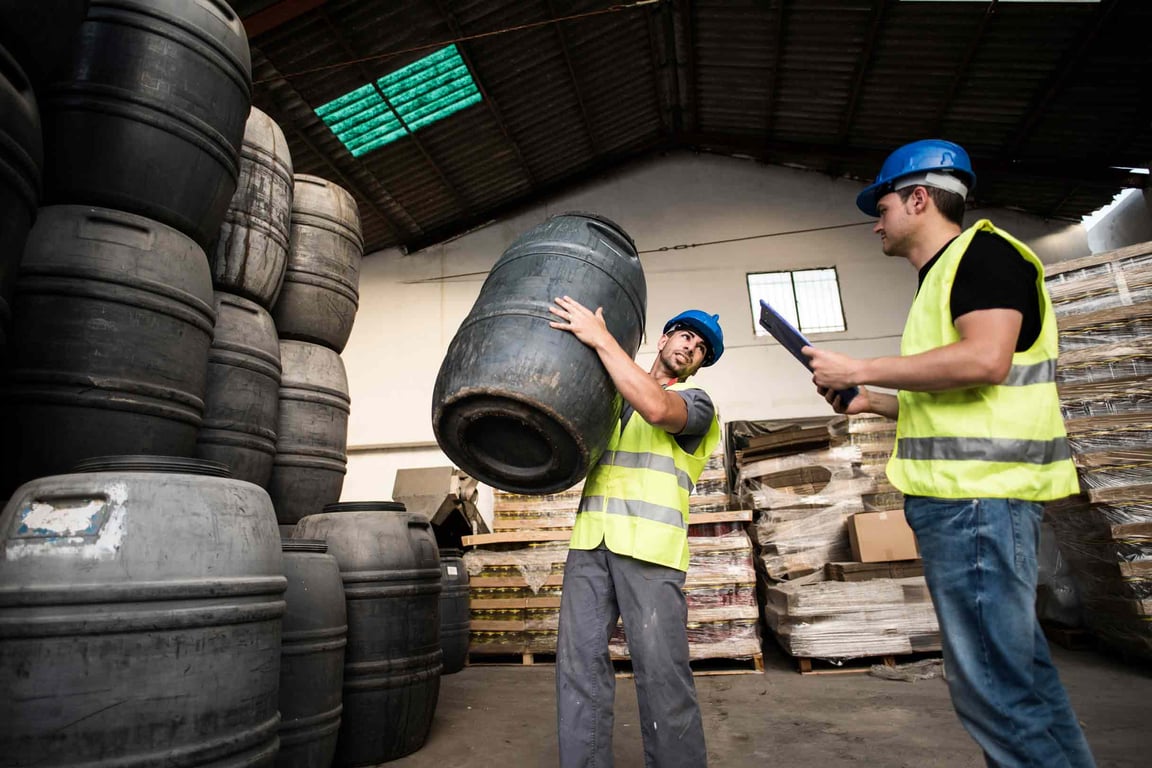
Hazardous manual handling: Risk assessment and preventions
Work-related musculoskeletal disorders (MSDs) resulting from manual handling are a leading cause of lost work time and work restrictions. By conducting a risk assessment in your workplace, you can proactively implement preventive measures to mitigate MSDs.
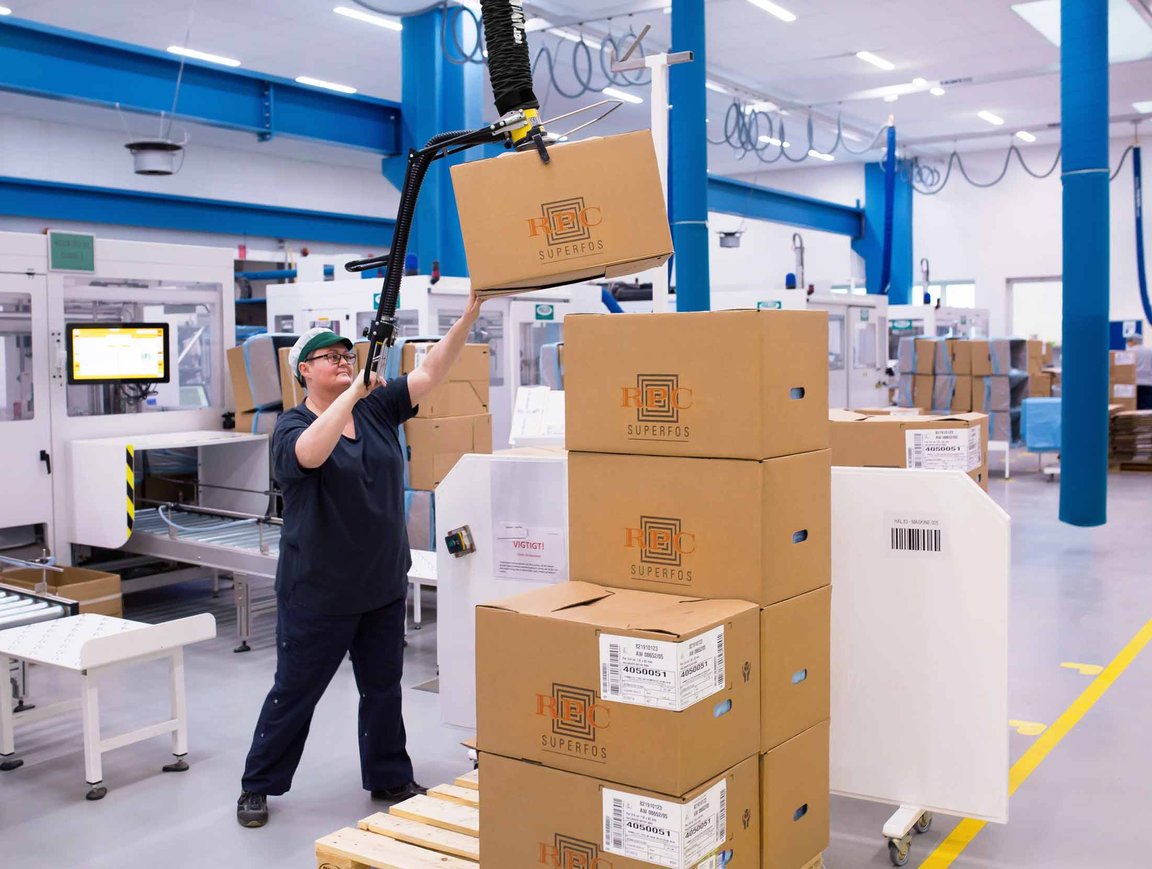
The types of lifting equipment that simplify material handling
As you explore ways to streamline and optimise operations in your warehouse or production plant — it’s time to consider lifting equipment. There are a variety of lifters and accessories to choose from beyond traditional forklifts.
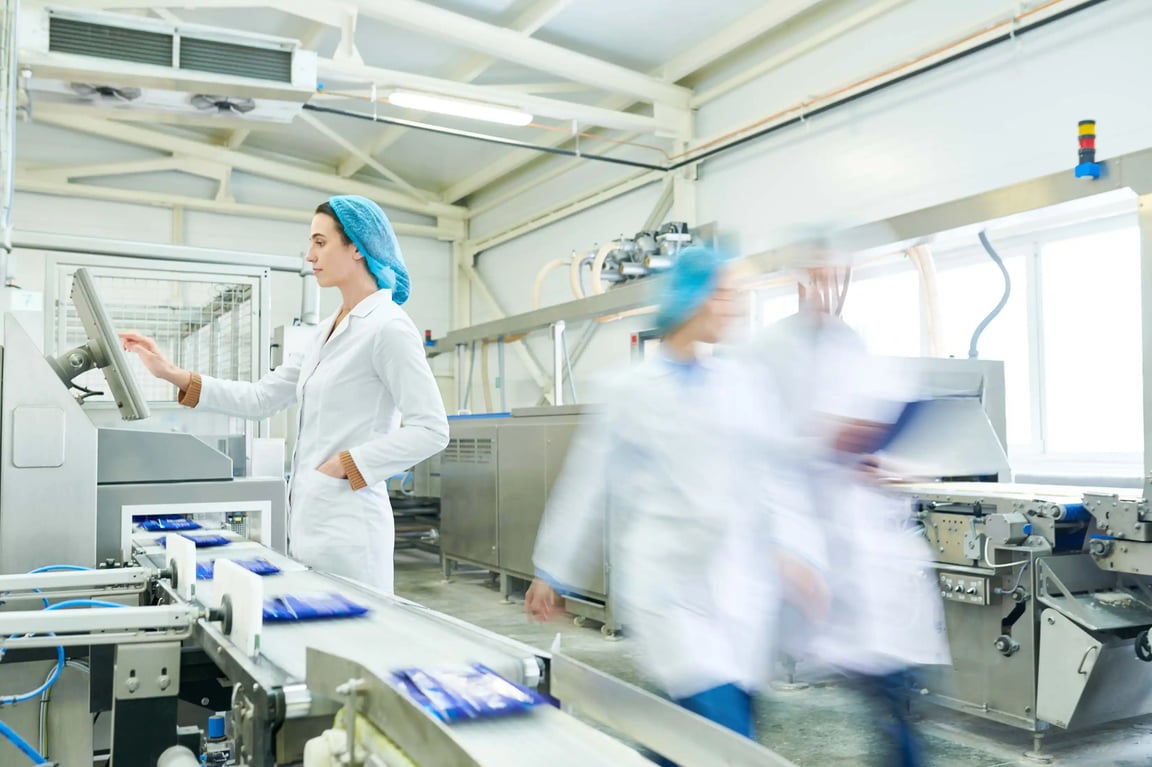
The (Re)evolution of the food packaging process
Goods and products must be protected and preserved if they are to get from where they are produced to where they are used without being damaged. And while modern packaging does a remarkable job at safeguarding contents, smart companies are now understanding that how you handle the food packaging process is just as important.
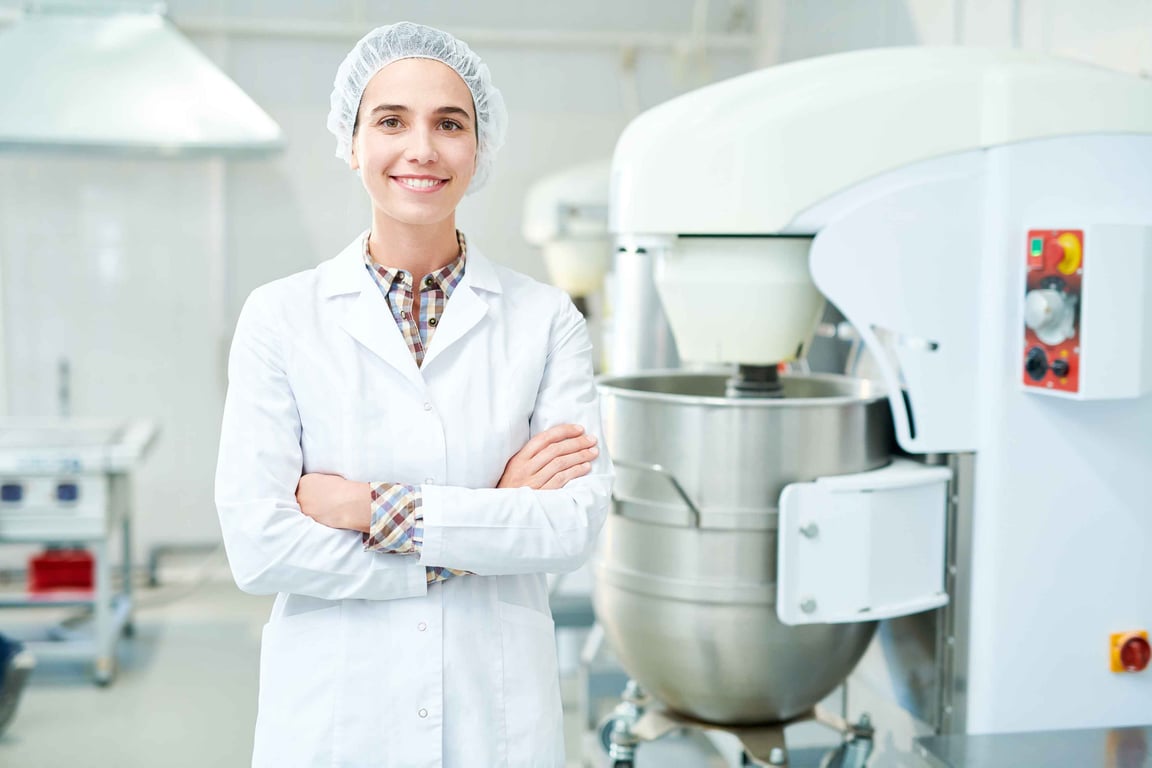
Creating optimal health & safety in the food and beverage industry
Lifting operations are an integral part of the food and beverage industry. Unfortunately, they can also be a key source of injuries or workplace absence. Implementing occupational health and safety in the food and beverage industry goes far past meeting government standards and laws, it has a major impact on your business.
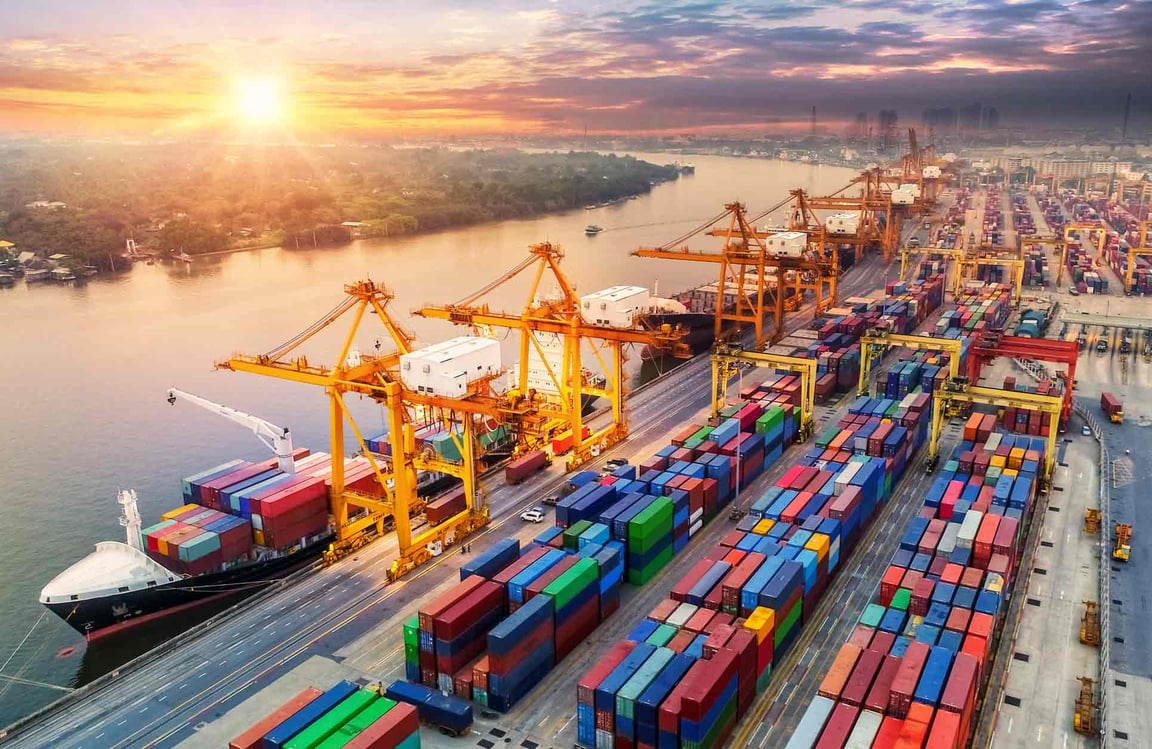
Top logistics trends in 2024
The logistics industry is constantly changing and adapting to the rapid growth of technology and the need to conserve the environment. For any business to stay ahead of the curve and remain competitive in these times, it must be flexible enough to accommodate the latest technological advancements, new processes, and strategies to succeed.
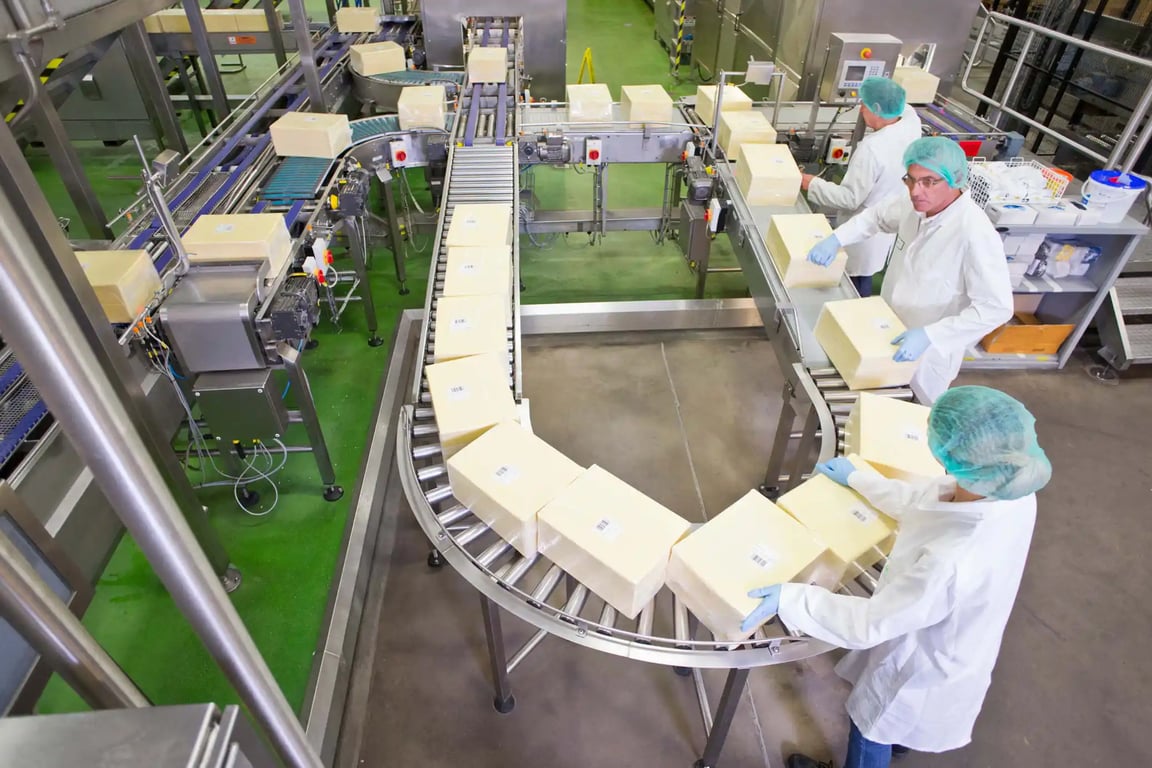
Sustainability and Savings in Food & Beverage
When considering TAWI vacuum lifters, lifting trolleys, and mobile lifting solutions, the initial draw lies in their efficiency and safety benefits. These tools streamline lifting tasks, reduce physical strain on workers, and transform two-person jobs into seamless solo operations.
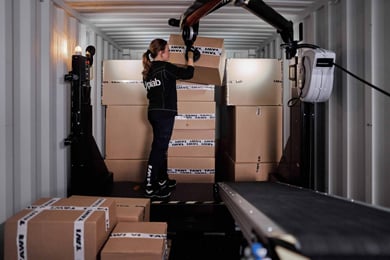
Efficient Loading and Unloading
Well-organised loading and unloading are key to an efficient logistic process. Taking a step towards automation in your manual handling processes is an essential strategy to make your logistic workforce more efficient.
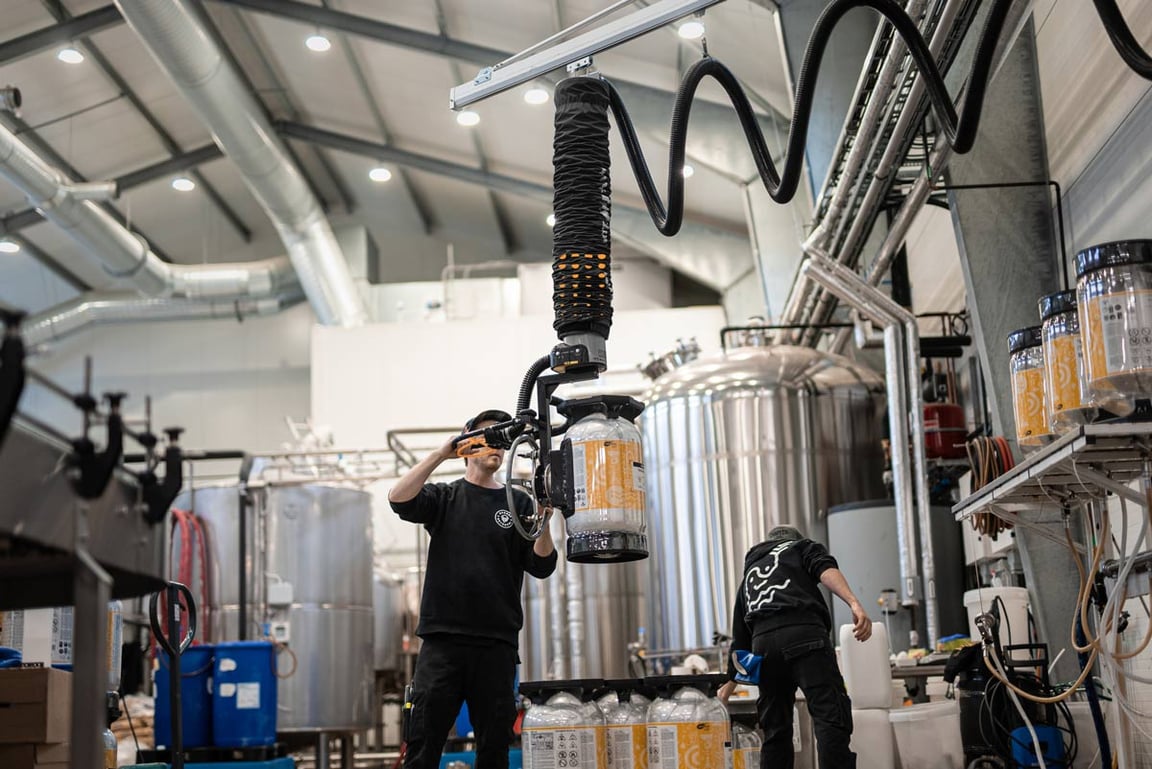
Why material handling in F&B is so important
Material handling is an essential aspect of the food and beverage (F&B) industry, encompassing the movement, storage, protection, and control of products throughout the manufacturing process. Effective material handling ensures that food products are safely and efficiently transported from production to packaging, storage, and distribution.
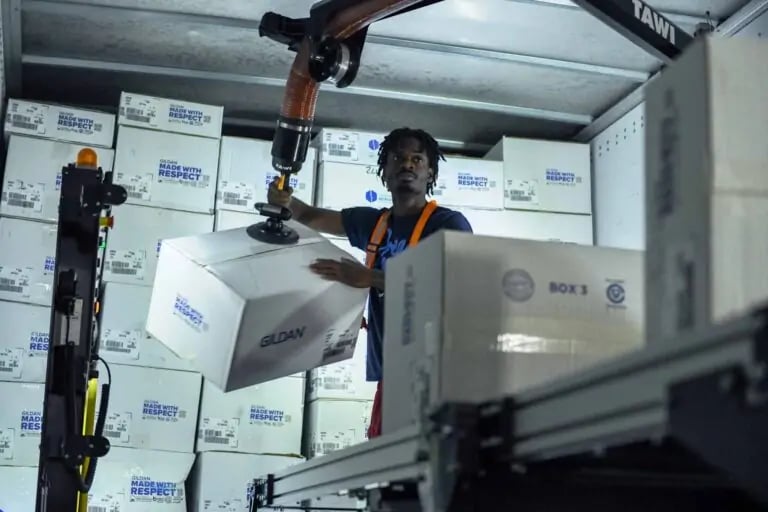
5 Steps to improve operational efficiency in logistics
Facing challenges such as labour shortages and safety risks, traditional logistics methods struggle to maintain operational efficiency. Incorporating technologies like GPS tracking, automation, and innovative vacuum lifters can not only boost operational efficiency but also reduce costs, improve safety, and ensure customer satisfaction.
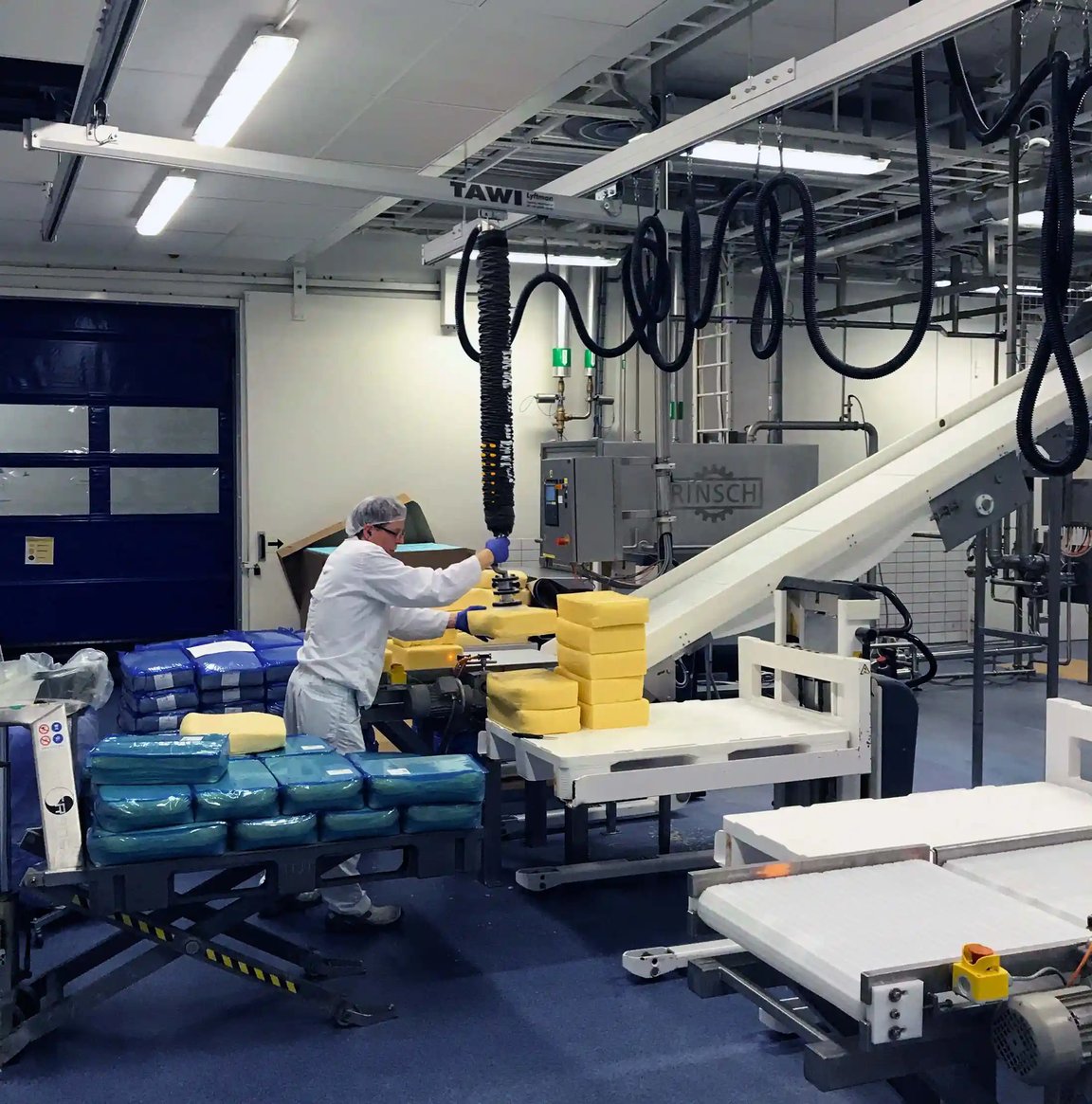
Helping food manufacturers keep up with demands
Food and Beverage plant operators know better than most the importance of marginal gains and precise optimisations. While most businesses downsized during the COVID19 crisis, the food and beverage industry continued to operate at full-scale production.
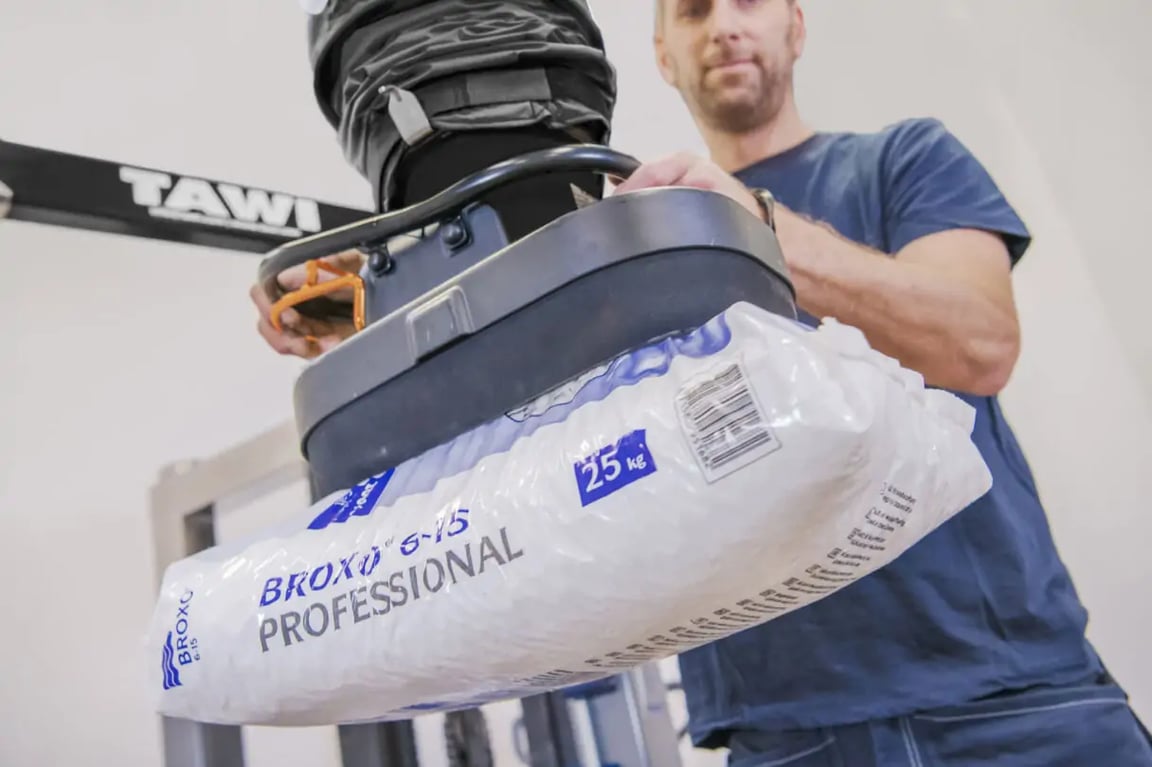
Food & Beverage Industry: Will It Lift?
In the food industry, understanding the subtleties between food processing and food manufacturing requires a certain level of expertise. However, it’s universally recognised that both sectors require strict hygiene and cleanliness standards.