Create a flexible workforce with TAWI
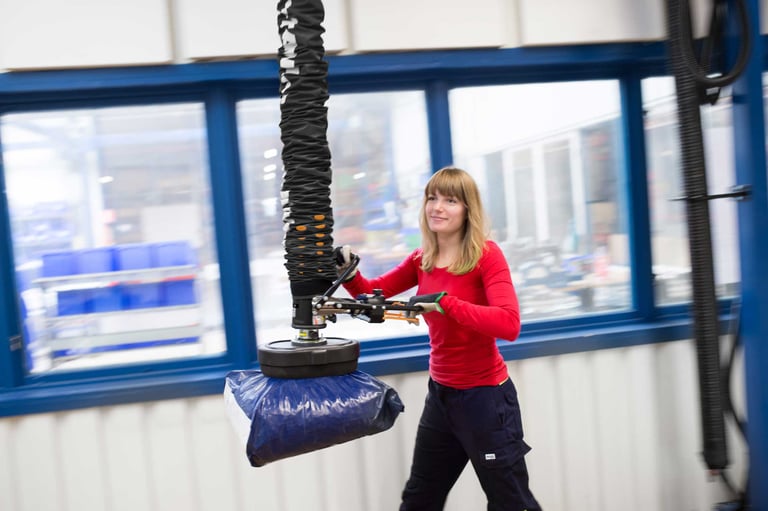
Warehouses and distribution centres face significant challenges with labour shortages and high employee turnover rates, leading to increased overtime and staffing issues. A flexible workforce, enhanced with vacuum lifting technology, can be a game-changer in addressing these challenges.
Defining a Flexible Workforce:
A flexible, agile, or dynamic workforce in warehousing implies cross-training employees to work in multiple positions. This approach moves away from relying on specialists trained in limited roles, thereby reducing the impact of staffing gaps and standard employee turnover. With modern technology, semi or fully-automating production, fulfilment, and distribution, the need for specialty roles is drastically minimised.
How TAWI Vacuum Lifters enhance workforce flexibility
Scalability and responsiveness:
By integrating equipment like vacuum lifters into your warehouse operations, every member of your workforce can perform the same job tasks regardless of physical strength or capabilities. This all but eliminates the need for specialised roles and allows for greater flexibility in workforce allocation.
With equipment-assisted operations, you can easily scale your workforce up or down based on demand fluctuations. During peak seasons or sudden workload increases, extra workers can quickly learn to use the equipment. This flexibility enables you to meet customer demands promptly while optimising resource allocation.
Improved cost efficiency:
Adopting equipment-based solutions, such as vacuum lifters, not only enhances working efficiency but also improves cost-effectiveness. Instead of hiring and training specialised workers for physically demanding tasks, you can employ a more diverse and agile workforce.
Your employees can be trained to operate the equipment, enabling them to adapt and perform a range of tasks with efficiency. This eliminates the need for separate teams or departments, reducing labour costs and optimising the utilisation of resources in your warehouse.
Improved retention rates:
A dynamic workforce reduces the monotony and physical fatigue of repetitive tasks, thereby improving job satisfaction, quality of life, and employee loyalty. UK average turnover rate across all industries is 15% annually. In warehousing and logistics, it’s even higher. When you combine workforce agility with semi-automation, you can drastically improve retention rates.
Increased productivity:
All of the factors above deliver increased throughput and organization-wide productivity. Combining a flexible workforce with semi-automated tools like a TAWI vacuum lifter can significantly enhance overall efficiency and throughput in your warehouse. Cost-savings include the ability to get more done with fewer employees, increased retention rates and decreased labour spendings. Not to mention fewer incident and injury claims.
High return on investment:
Vacuum lifters increase lifting speed, reduce picking errors, and lower the number of employees needed, leading to significant cost savings and scalability in your operations. While also an investment, vacuum lift equipment accelerates lifting speed by up to 100 times per unit. It also reduces picking errors from 3% to 1%.
3 ways to leverage TAWI Vacuum Lifters in your warehouse operations:
- Container unloading: say goodbye to heavy manual handling and hello to ergonomic, safe, and fast unloading with a mobile container unloader with integrated vacuum lift.
- Sorting & palletizing: streamline your processes with high-speed vacuum lifters, ensuring swift and ergonomic package handling.
- Order picking: improve your warehouse operations with a mobile order picker, designed for time-efficient and simple order picking.
Looking for ways to improve your logistic operations? Explore possibilities here.
TAWI has technology that can be customised to lift boxes, crates, bags, sheets, canisters, food items, fragile items, odd-shaped items, and more. By integrating these tools into your operations, you can transform your workforce into a more flexible, efficient, and satisfied team.
How to implement a flexible workforce empowered by TAWI vacuum equipment in your warehouse
Identify task requirements:
Evaluate the specific tasks in your warehouse operations that can be supported by the equipment. This may include tasks that require physical effort, like carrying heavy objects, handling materials, or repeating the same motions. These tasks can be made easier with equipment like vacuum lifters.
Select appropriate equipment:
Contact TAWI so we can guide you in selecting the right equipment that aligns with your warehouse needs. Factors to take into consideration includes load capacity, manoeuvrability, safety features, and ease of use. Vacuum lifters, for example, are versatile tools that can handle various loads and are user-friendly.
Provide comprehensive training:
It’s vital to ensure that all employees receive proper training on the safe and effective operation of the equipment. TAWI offer comprehensive training that cover equipment usage, safety protocols, maintenance, and troubleshooting. This will equip your workforce with the necessary skills to operate equipment efficiently while minimising the risk of accidents.
By following these suggestions, you can successfully implement a flexible workforce that is empowered by equipment such as vacuum lifters. This approach enhances operational efficiency, productivity, and adaptability, allowing your warehouse to thrive in a dynamic and competitive environment.
Ready to learn more about TAWI vacuum lift equipment?
If you would like to learn more about how vacuum lift equipment can help you create a more flexible workforce, TAWI is here to help.
Most warehouses require a mix of lifting tools and technology to create safe, efficient, and agile operations. We customise your lifts to your product and material specs and ensure you have the size and weight capacity for your inventory and supplies. Reach out now to learn more, simply fill out the form below.