How you can improve occupational health & safety through smart lifting
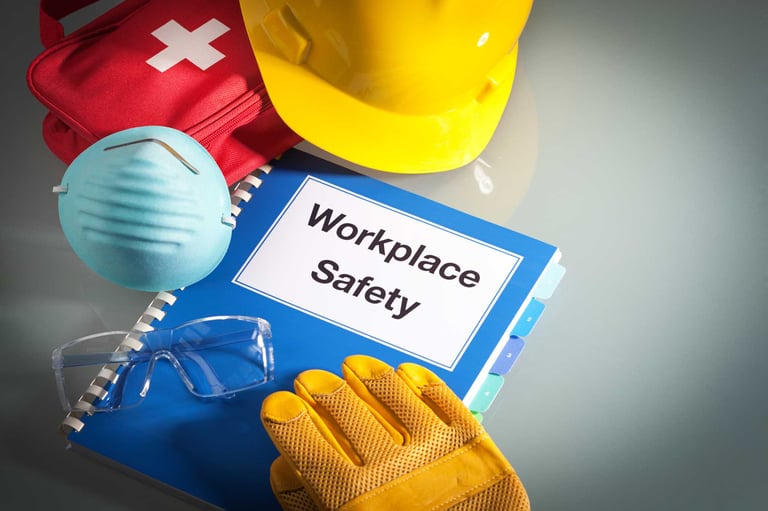
Set long-term objectives for improving occupational health and safety. By striving to minimise the causes of hazards in the work environment, you can contribute to reduce the costs of work-related injuries and illness, improve working conditions, and increase productivity.
Start with prevention
Many factors influence workplace health and safety. Ergonomics, stress, and chemical hazards are some important aspects to consider. In all these areas there are rules that employers must follow. This article focuses on ergonomics, including how to adapt tasks and workflows to people in order to minimise the risk of accidents and ill health. Planning and organising work in a sustainable way is key to successful prevention of workplace hazards.
Since occupational hazards occur at the workplace, it is the employer’s responsibility to ensure that the work environment is healthy and safe. This includes preventing and protecting workers from occupational risks. Education on risk prevention, and training on how to perform tasks in a safe way, are vital components for creating a healthy and safe workplace.
Identify and understand risks to occupational health & safety
Generally, small workplaces report a higher amount of work-related injuries than large ones. It seems that the rate of serious injuries in small workplaces (defined as those with fewer than 50 employees) is twice that in large workplaces (defined as those with more than 200 employees).
Regardless the size of business, there is a strong link between working conditions and musculoskeletal disorders (MSDs). MSDs occur in most industries and often arise in connection with manual handling such as heavy lifting, repetitive tasks, uncomfortable, strenuous and stressful work postures and movements.
Manual handling primarily refers to the manual labour of lifting, carrying, dragging, or pulling. This also covers tasks such as moving goods to and from shelves, sorting and palletising packages, topping up mixers and machines with raw materials by hand and many more. Heavy manual handling involves the risk of overloading the operators back, shoulders and arms. This is particularly risky when handling is combined with poor work postures.
Current knowledge emphasises three aspects as the most significant for preventing back injuries:
- Avoid heavy lifts if possible (or use technical aids such as vacuum lifters or lifting trolleys)
- Keep the load close to the body
- Avoid lifting and twisting at the same time
The human body is built for movement and carrying loads, and even thrives on it as long as there is variation in load and movements as well as the opportunity to recover. If the same movements or carrying is repeated often, or last for a long time, the chance of recovery is limited, and the risk of ill-health or accidents increases.
What is a high-risk load? (No, we’re not talking explosives)
High-risk loads, or health-endangering loads, include heavy loads, repeated loads, one-sided loads, and static muscle work. Load dose is a measure often used to estimate the risk of ill-health or injuries.
The load dose is a combination of the following work factors:
- how much (intensity)
- how often (frequency)
- how long (duration)
A high load dose is often a high-risk load, but even low load doses can have negative health effects, especially when the work is repetitive. Repetitive work means that the employee is performing one or a few tasks (with similar movements) over and over again for a large part of the working day. The task is commonly only one part of more extensive workflow and is often performed at a high pace.
Continuous repetition of the same movements give rise to a uniform, constant load. The object being handled need hardly weigh anything at all as the arms own weight is sufficient to strain muscles and joints in an unfavourable manner. The long-term consequence can be the gradual onset of injuries that take a long time to heal. Once injured, we often regain the same pain when subjected to similar loads.
What are the employer’s responsibilities?
Employers are responsible for ensuring that the workplace and the work to be done is ergonomically well designed. To implement preventive measures, the employer must examine working conditions and make a risk assessment. Here is a helpful guide on how to carry out a risk assessment at your workplace.
When an employee is injured due to acute overload, or suffers an occupational illness due to prolonged overload, the employer must take action. The sooner action is taken, the easier it will be for the employee to get back to work.
Employers should assess if loads, either individually or in combination, may risk causing MSDs. Risks must be assessed on the basis of the load’s duration, frequency and intensity (as mentioned above). Furthermore, the employer should design the workplace in a way that minimises the risk of MSDs when manually handling loads.
Taking preventive measures involves both organisational processes and implementation of lifting aids such as vacuum lifters and lifting trolleys to avoid workers needing to handle loads manually.
What are the employee’s responsibilities?
Employees also have responsibilities. Paying attention to risks in the work environment and reporting them to their employer is one obligation. To prevent risks of accidents and disorders the employee must also use aids and protective equipment in accordance with the employer´s instructions on how to carry out the work.
Improving occupational health & safety with lifting equipment from TAWI
As previously mentioned, manual handling and heavy lifts should be avoided to prevent workplace injuries and accidents. Sometimes, avoiding manual handling by re-organizing the specific task is not possible and the employer needs to look at alternative solutions. Lifting aids, including mobile and stationary vacuum lifters, lifting trolleys and hoists are a few examples of equipment that will not only help you minimise the risk of injuries but will often also contribute to increased productivity.
The combination of improved workplace health and safety AND increased productivity will ensure a sustainable future for your business. This is what we at TAWI want to help you achieve. Our smart lifting equipment is designed to improve occupational health & safety while supporting your workflow, whether it’s in production, distribution, or logistics.
Ergonomic lifting equipment boosts occupational health & safety
"The biggest benefit is fewer injuries, but also that we have become more efficient" says Niklas Blomberg, Project Leader Logistics at Jollyroom.
How lifting equipment prevents work-related injuries and improve workplace health and safety at RPC Superfos
At RPC Superfos in Denmark, large volumes of packaging products are produced and packed on pallets every day 24/7. At the end of the process flow, finished products are packed into big cardboard boxes and placed on pallets. Employees stack these boxes up to 2.6 meters on pallets, involving frequent lifting above shoulder height. This kind of repetitive and high load lifts affect the body in the long term and can often lead to work-related injuries.
About 20 years ago, RPC Superfos decided to invest in their first vacuum lifters from TAWI, with great outcomes. “With our vacuum lifters, we lower the risk of work-related injuries happening in the long run. Moreover, our employees are pleased that we have found a solution that considers their health and well-being”, Henning Frederiksen, Project Manager, RPC Superfos in Randers, Denmark.
The vacuum lifters are used day and night by the packaging workers and all new employees are taught how to operate the lifters as part of their initial training. “We would not be able to handle the manual lifting operations without them”, Susan Betzer, packaging employee at RPC Superfos in Randers, Denmark.
Curious to explore how you can improve health and safety at your workplace?
Do you have manual handling tasks that cannot be eliminated? With decades of experience helping our clients lift and move goods in a sustainable way, we can guide you to the best solution for your business. We can help ensure health and safety in your workplace, without interfering with productivity. Get in touch to schedule a free site visit or product demonstration.