How to get more from your operations with a warehouse trolley
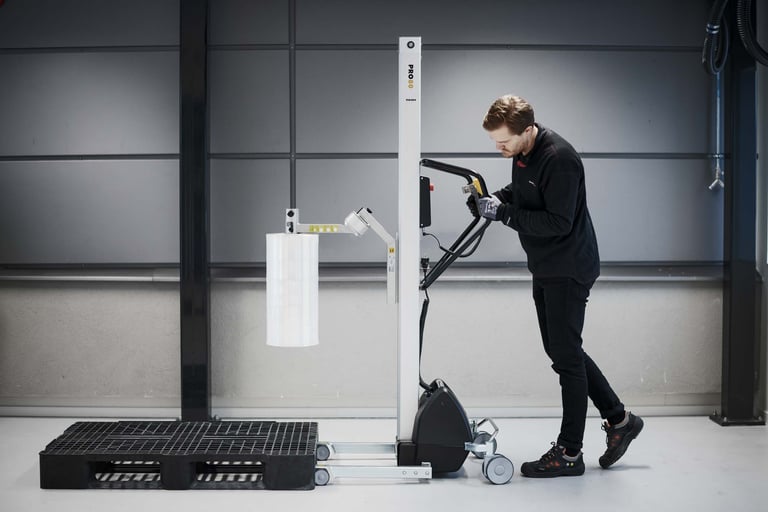
Warehouse management involves many diverse physical activities – from moving and handling raw materials and products to ensuring a continuous and timely flow of parts and components.
Successful warehouse management is more than just receiving and transferring goods
It is about finding new and better ways to lower costs and save time. With the proper approach, you can not only remove the hazards of manual lifting, but create a more flexible, more efficient operation in the process. TAWI’s line of ergonomic, electric warehouse trolleys, stackers, and platform trolleys can help you do just that.
Recent supply chain events have made their impact felt on almost all warehouse operations and brought increased focus on this important link in the chain. From retail to manufacturing, it has become clear that a more efficient warehouse operation increases not just longevity and sustainability but income and customer satisfaction.
The opposite is also true, however. Whatever the type of material handling involved, or in whatever type of warehouse operation, improper handling will cost you time and money. And potentially cause you to lose valuable customers.
Manual handling: any activity requiring the use of human force to lift, lower, push, pull, carry or otherwise move an object or thing. Manual handling takes place in every warehouse operation and can be a potential workplace hazard when it requires employees to move or handle objects of excessive weight or size or unwieldy or awkward shape. It is one of the most commonly ignored risks in warehouse operations, resulting in costly injuries and loss of productivity.
Maximizing Performance and Balancing Risk
Whether your warehouse operations are dealing with retail or wholesale logistics, manufacturing, or industrial material supply, certain demands are always in place. Chief among them is that your material or merchandise needs to get from where it is to where it needs to be. Another unavoidable truth is that any warehouse or loading bay operation requires a lot of heavy lifting. This often entails employees bending and twisting, lifting and moving heavy items, or lifting in awkward positions or postures.
Accepted wisdom is that items should be handled manually whenever possible in order to avoid the greater risk of injury – both to workers and products or materials - that can come with powered industrial trucks. This doesn’t mean, however, that handling materials manually is free of hazards.
Warehousing operation challenges
Manual handling is exhausting and a frequent cause of serious injuries. In fact, the overexertion and bodily stress that arise from manual handling and the injuries that result from these activities account for approximately one third of total lost work time in warehousing operations. The many challenges connected to warehouse stacking, stock distribution, and shop floor handling run the gamut from lifting and moving trays, crates, and packages to handling large rolls, barrels, and boxes (often heavy or oddly shaped and above shoulder height). At every stage of operations there are both risks to employees and to the goods being lifted and moved. All of these factors take a toll on both productivity and profitability.
Most warehousing operations, whether in the retail, wholesale, manufacturing, or industrial sectors, include the manual handling of heavy, bulky, and awkward items, and involve potentially hazardous repetitive or physically stressful tasks. Whether moving or shifting barrels, cartons, or rolls, stacking cartons on pallets, or moving individual components or products, stress injuries as a result of performing these manual tasks are the highest cause of injury in all of these industries. The loss of productivity and manhours is substantial.
What are the potential hazards of improper lifting for workers?
- Damage to back and joints
- Sprains and strains
- Fractures and bruises
- Cuts and scrapes
- Debilitating injuries (or even death)
The most common types of injuries are back injuries, other sprains and strains, and cuts and lacerations. Strain related injuries can also occur from constant repetitive tasks. Body pain and discomfort are most commonly experienced by employees in the back, shoulders and arms. Discomfort or pain can be caused or aggravated by manual handling activities at work, such as lifting, carrying, pushing, holding, and sustained or stressful body postures.
These manual handling injuries are most commonly the consequence of over-exertion while lifting, carrying, pushing or pulling an object, slip and falls during manual handling; or being struck by an object during manual handling.
Risk identification - the first step in reducing manual handling problems
Risk identification involves the identification of tasks that may cause injuries or accidents. If your warehouse operations involve any of the following, then you have areas that can be improved:
- Frequent or prolonged bending, reaching, or twisting
- Lifting above shoulder height
- Frequent awkward postures or repetitive or forceful movements
- Unnecessary double handling
- Loads being moved or carried over long distances
- Loads that are difficult to handle or grip due to size, shape, or other factors
- Items that are fragile or easily damaged
The task of assessing your specific manual handling risks is key to implementing the proper solutions.
The workers who carry out manual handling tasks are most often the first to notice problem areas, and can usually point out the tasks that cause discomfort or pain during their work. Listening to them will usually provide ideas about safer or more efficient ways to do the job.
Ergonomics & economics combined (with smart warehouse trolley)
Ergonomics is often interpreted to mean simply improving the work environment so that damage to employees’ health and wellbeing is minimized. All agree that this is an admirable goal. The word Ergonomics, however, (from the Greek words ergon, meaning work or labor, and nomos, or natural laws) means literally “the study of work”.
At TAWI, we have always taken this broader definition to heart. In our view, ergonomics means studying – and improving - people's efficiency in their working environment. Comfort and usability are important factors, to be sure, but the result is not just a safer environment, but a more effective and more efficient one. And a more effective and more efficient workplace is a more profitable one.
Safer lifting and handling
Smart companies are recognising that restructuring or changing warehouse workplace conditions to make the job safer and easier provides a range of benefits. Removing the types of lifting and handling that cause musculoskeletal disorders reduces workplace injuries and absences. Easier lifting enables a broader range of employees to do the jobs in question, which facilitates easier staffing, hiring, and employee retention. Safer lifting and handling means less damage to products or materials, which means fewer errors and returns. All of which translate to less time, money, and resources being wasted.
Which is why we are so fond of our simple equation. Ergonomics = Economics. Isn’t math wonderful?
What are the potential risks of improper lifting to your warehousing operations?
- Loss of productivity
- Less efficient operations
- Damage to products and materials
- Less flexible workforce
- Increased employee absence
Efficient warehouse trolley - every cloud has a silver lining
Every challenge is also an opportunity. The challenge presented by manual lifting is no different. With the proper approach, you can not only remove the hazards of manual lifting, but create a more flexible, more efficient operation in the process. And TAWI’s line of ergonomic, electric warehouse trolleys, stackers, and platform trolleys can help you do just that.
Our electric lifters are available in different models, all with our innovative, modular design and all able to be fitted with a wide selection of lifting tools, enabling the safe and efficient lifting of just about any material or object. This allows users to adapt the lifters to meet their specific needs, with purpose-designed tools and a range of features engineered to provide optimal precision and control.
Special features also help ensure safety for both user and load, with all models equipped with a safety mechanism that immediately stops the lifter if the tool hits an object during lowering, ensuring that the lifter will not tip over or damage anything that happens to come in the way. With a TAWI warehouse trolley, any user, no matter how tall or strong, can manage goods up to 250 kg safely and easily; lifting, lowering, turning, tilting, rotating and moving boxes, drums, reels, crates, and most any other common load, bringing unprecedented flexibility to your workforce.
TAWI warehouse trolley solutions:
- Reduce fatigue and repetitive stress
- Reduce risk of accidents and injury
- Improve employee health and productivity
- Increase employee flexibility and capacity
- Protect transported goods
In addition, our proprietary QuickLoad function helps you program the lifter to stop at exactly the desired level, making it easy to stack goods in shelves or mount reels on machine axis. Flexible legs allow you to adjust the width of the trolley so that you can drive into pallets and reach as far as you need, further enhancing both usefulness and flexibility.
Our mobile, battery-powered lifting trolleys are particularly useful in industrial or manufacturing environments and our stainless-steel trolleys are designed to be easy to clean and sterilize. TAWI lifting trolleys can even be configured for safe material handling in facilities with strict sanitary requirements, such as food- or pharmaceutical processing.
Flexible warehouse trolleys to fit your needs
Compared to full-size lift trucks, TAWI’s lifting trolleys are both compact and lightweight, making them ideal for material handling in areas where space is limited or where goods are hard to reach, and taking up much less space when not in use.
Whichever configuration you choose, A TAWI trolley and lifting solution will help eliminate the risks associated with manual handling and provide a more efficient and productive workplace. TAWI lifting trolleys are also an excellent investment. Alone or in combination with other handling equipment, our warehouse trolley solutions will reduce cycle times and enhance productivity in almost any retail, wholesale, industrial, or manufacturing setting.
TAWI is here to help
Simply put, the range of potential hazards associated with manual lifting not only damages your products and staff, but your bottom line. There are, however, ways to eliminate —or at least minimise — such hazards. TAWI can help you implement better lifting solutions which will reduce workplace accidents involving the moving, handling, and storing of materials and result in more efficient and more productive warehouse operations.
Contact TAWI today to find out more about how we can help future-proof your operations with smarter warehouse lifting solutions and help you remain viable – and profitable - whatever the future holds.