Hazardous manual handling: Risk assessment and preventions
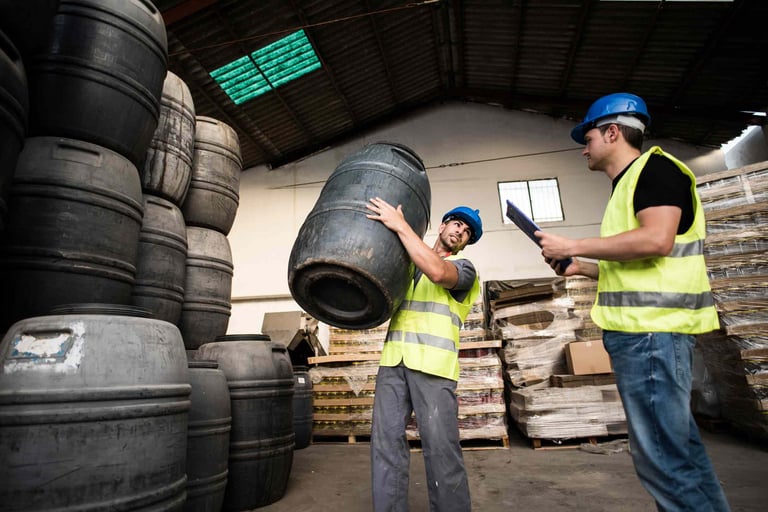
Work-related musculoskeletal disorders (MSDs) resulting from manual handling are a leading cause of lost work time and work restrictions. By conducting a risk assessment in your workplace, you can proactively implement preventive measures to mitigate MSDs.
Using ergonomic lifting equipment can play a significant role in preventing manual handling injuries and enhancing worker productivity. This type of equipment is often cost-effective and offers additional advantages beyond reducing the risks associated with manual handling.
Understanding the Categories of Manual Handling Risks
Manual handling of loads is a significant contributor to occupational health problems. Several risk factors make manual handling hazardous and increase the likelihood of workplace injuries. These factors can be classified into four categories: the load, the task, the environment, and the individual.
The Load
- Weight: Loads exceeding 20 to 25 kg are generally too heavy for safe lifting by most individuals.
- Size: Large and bulky loads that cannot be carried close to the body cause muscle fatigue, primarily if handled repeatedly within a short time.
- Grasping Difficulty: Objects that are challenging to grip increase the risk of accidents due to slipping.
- Reach Difficulty: Bending or twisting the body to reach a heavy object can result in spinal injuries.
- Imbalance: Unevenly balanced loads lead to uneven muscle loading, particularly when the load's centre of gravity is not aligned with the worker's.
The Task
- Strenuousness: Tasks that are excessively strenuous or performed for extended periods without sufficient recovery time pose risks.
- Awkward Movements or Postures: Bending or twisting the trunk, over-reaching, raising arms, or holding loads away from the body can cause strain.
- Repetitive Handling: Frequent repetition of load handling can contribute to musculoskeletal disorders.
The Work Environment
- Insufficient Space: Limited space for manual handling can result in strained body postures and imbalances in loads.
- Floor Conditions: Slippery, uneven, or unstable floors increase the risk of accidents.
- Temperature Extremes: Heat causes fatigue and sweating, making it harder to hold objects and necessitating more force. Cold environments can lead to numb hands, impairing grip strength.
- Poor Lighting: Inadequate lighting increases the risk of accidents during load handling and forces workers into awkward body positions to compensate for reduced visibility.
Individual and Lifestyle Factors
- Physical Capabilities: Factors such as weight, height, and strength influence the ability to handle loads safely.
- Age: The risk of low back disorders rises with age and the number of working years. The initial occurrence of low back pain typically happens by the age of 30.
- Experience and Training: Lack of experience and training can contribute to improper manual handling techniques.
- Prior Medical History: Pre-existing health conditions can increase the vulnerability to manual handling-related injuries.
- Lifestyle and Habits: Factors like smoking and a sedentary lifestyle affect overall health and can exacerbate the risks associated with manual handling.
Conducting a Manual Handling Risk Assessment
A manual handling risk assessment is a crucial step in ensuring the health and safety of workers. Employers are responsible for assessing the risks associated with manual handling tasks and taking appropriate measures to prevent harm.
The assessment involves a thorough examination of potential hazards within the workplace. Upon identifying the risks, control measures can be implemented to mitigate them effectively. The primary objective is to reduce or eliminate the risks of injuries, accidents, or occupational illnesses arising from hazardous manual handling.
Conducting a Workplace Risk Assessment
Performing a comprehensive risk assessment has many benefits for businesses. These include reduced costs due to improved productivity and less employee sick leave. The European Agency for Safety and Health at Work provides a helpful checklist to identify high-risk manual handling operations:
- Identify Hazards: Carefully examine the workplace to identify potential hazards related to manual handling. This includes analysing the load, task, environment, awkward postures that are required to perform different tasks, and individual factors discussed earlier.
- Assess Risks: Evaluate the likelihood and severity of the identified hazards. Determine the level of risk associated with each hazard and prioritise them based on the potential for harm.
- Implement Control Measures: Develop a plan to control and minimise the risks. Start with measures that eliminate or reduce manual handling as much as possible. Consider task redesign, automation, or mechanical lifting equipment to alleviate the strain on workers. Implement technical measures such as vacuum lifters, hoists, and trolleys to improve ergonomics and safety.
- Monitor and Review: Regularly monitor the effectiveness of the control measures and adjust them as needed. Conduct periodic reviews of the risk assessment to ensure it remains current and reflects any workplace changes.
Preventing the Risks of Hazardous Manual Handling
After completing the risk assessment, it's crucial to implement effective control measures to prevent manual handling risks in the workplace. Consider the following preventive measures:
- Elimination of Manual Handling: Explore ways to reorganise work processes to minimise or eliminate the need for manual handling. Redesign tasks or introduce powered or mechanical handling equipment such as lift trucks or conveyors.
- Technical Measures: When manual handling is unavoidable, prioritise automation and lifting and transporting equipment. Ergonomic lifting aids such as vacuum lifters, hoists, container unloaders, and trolleys can significantly reduce the risk of injuries. These cost-effective measures offer various benefits, including improved productivity, reduced employee turnover costs, and enhanced workforce flexibility.
- Organisational Measures: If elimination or technical measures are not feasible, focus on improving workplace conditions to reduce risks. Arrange materials in a way that minimises reaching or bending. Allocate heavy or frequent tasks to multiple workers to distribute the load. Encourage breaks and task rotation to prevent fatigue during manual handling activities.
- Information and Training: Properly inform and train workers about the potential risks associated with manual handling. Educate them on how to recognise and avoid these risks. Provide comprehensive training on the correct use of equipment and safe handling techniques.
Implement cost-effective preventive measures tailored to your industry. This will reduce the risks associated with hazardous manual handling. A thorough risk assessment should consider the load, task, environment, and individual factors. This will create a safer and healthier work environment.
Remember, the use of ergonomic lifting equipment not only protects employee health, but also enhances productivity and reduces costs. For more information on manual handling challenges and ergonomic lifting solutions specific to your industry, refer to the provided resources.
It is essential to prioritise preventing hazardous manual handling. Proper risk assessment and implementation of preventive measures are necessary for this. This will lead to a safe and productive workplace.
Employers can reduce the risk of work-related musculoskeletal disorders. They can do this by providing the necessary tools and training. This will create a healthier work environment for their employees.