The (Re)evolution of the food packaging process
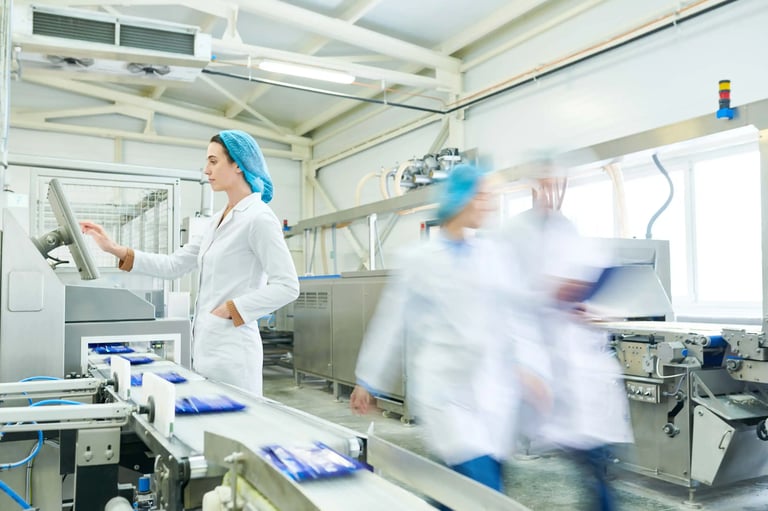
Goods and products must be protected and preserved if they are to get from where they are produced to where they are used without being damaged. And while modern packaging does a remarkable job at safeguarding contents, smart companies are now understanding that how you handle the food packaging process is just as important.
The Ever-Changing Food Packaging Industry Process
The process of packaging food products has undergone a vast transformation over the years, from the Stone Age to the Industrial Revolution and beyond. With each technological wave, packaging has evolved, transitioning from treated mulberry bark and ancient glass vessels to advanced metal and plastic containers. Despite these advancements, modern packaging is not without its challenges. Food packaging serves to protect its contents from the elements, increase life span, and reduce contamination. However, before it can do any of those things, it must make it safely from the production facility to the consumer.
Humans have been addressing packaging challenges for almost as long as civilisation has existed. Some of the most beautiful items in our museums, in fact – clay or earthen jars and vessels – represent our ancient efforts to create suitable packaging.
Did you know?
Two of the most common packaging materials were discovered completely by accident. The world’s first prefabricated carton came about when a printer’s machine malfunctioned and sliced through an entire stack of paper bags. Likewise, polyvinylidene chloride (PVDC), the main ingredient of saran wrap, was discovered accidentally when a lab worker at Dow Chemical came across a vial he couldn’t scrub clean. Once the colour was removed from this stubborn dark green film, it became the world’s most popular food packaging material.
Nothing starts on the shelf, it has to get there
In the food and beverage industry, regardless of whether the product is packaged in sacks, tubs, boxes, or drums, careful handling is crucial to prevent damage to the packaging and its contents. Operators enhance packaging integrity and safety by stretch-wrapping and palletising stock using film rolls. Neglecting this step can result in damage to primary packaging, leading to ingredient loss, contamination, or spoilage.
Napoleon’s Food Preservation Prize
In 1795, French Emperor Napoleon needed to find a way to feed his army. He offered a prize of 12,000 Francs to the person who could invent a better method of food preservation. The prize went unclaimed for another 15 years until it was claimed by Nicolas Appert, whose method of boiling then sealing food in airtight glass containers is still used today.
In the food and beverage industry, the wide range of weights and sizes necessitates diverse packaging solutions
Structural integrity is crucial to prevent packaging breakage to safely handle the products and ingredients, whether it involves cushioning delicate items like eggs or robust material sacks to carry potatoes. Food and ingredients are not the only things that need protecting - your workers' health and safety also need to be considered. Striking the right balance between efficient operations for maximum profitability whilst prioritising worker health and safety is a must.
This is where TAWI lifting solutions come in
TAWI lifting solutions are designed to enhance efficiency while reducing up to 80% of the strain on employees' bodies, achieving the ideal balance between employee well-being and profitability. With TAWI, lifting becomes effortless—our vacuum lifts and trolleys take the strain, enabling your employees to operate the machinery with ease.
What does this mean for your business? Employees can be redeployed to other tasks within the warehouse, boosting productivity, resource allocation and efficiency without the need for additional staff. Our solutions consistently improve work performance while enhancing the health and safety of your workforce.
The Painful Reality of Manual Lifting
Musculoskeletal disorders (MSDs) encompass a range of conditions, including upper limb disorders, back injuries, and chronic ailments like tenosynovitis and carpal tunnel syndrome. These issues often arise from repetitive tasks and awkward lifting, leading to chronic back pain.
But how does this relate to the food packaging process?
Well, MSDs are prevalent in packaging operations, affecting joints, vertebrae, and intervertebral discs. In the food and drink industry, workers encounter a variety of MSDs due to repetitive tasks and lifting heavy loads. Neck, shoulder, and lower back pain are common, along with nerve troubles. Shockingly, about one-third of reportable injuries in this sector result from handling and lifting.
In 2017 alone, overexertion and repetitive motion – leading causes of workplace injuries – cost U.S. companies over $13 billion. It is easy to calculate the direct costs of employee injuries, but the indirect costs can be more difficult to determine. These additional costs can cover things such as retraining or replacing an injured employee, scheduling and production delays, administrative expenses, legal costs, hiring difficulty, and even lower employee morale – all arising from a single employee workplace injury.
The good news? Most of these injuries are preventable
It all begins with creating a sustainable, ergonomic workplace—one that prioritises safety reduces worker absence, and keeps your operations running smoothly.
Increasing food packaging process efficiency
Smart companies are taking a closer look at worker safety and working conditions, and how they affect company costs and profits. Many are turning to ergonomic solutions to mitigate risks for their employees. Any responsible packaging manager is familiar with ergonomics – the process of gaining insight into human abilities and limitations and then designing or arranging workplaces, products and systems so that they fit the people who use them.
At TAWI, we take this as our starting point, developing products that increase the capabilities of each and every worker, and create a safer, more efficient, and more profitable workplace. At TAWI, we use our extensive knowledge and expertise to tailor products and solutions to match your specific situations and your unique needs – call it ergonomics in action.
Packaging (Re)evolution in Action: Enhancing Efficiency and Safety
A large percentage of workplace injuries are linked to worker fatigue. Working in the packaging industry can be physically taxing, and the longer a worker performs their tasks, the more tired they become. Tired workers are more likely to make mistakes which can put them and fellow employees at risk and increase the likelihood of injury. A TAWI smart lifting solution never gets tired – or injured – it just keeps working.
TAWI’s vacuum lifters and trolley solutions enable any worker to lift, safely and efficiently, without damage to the products or the people who handle them. Lifting and moving the heavy and ungainly film reels used in packaging machines, for instance, must be done as quickly as possible in order to avoid downtime in production. Carrying out this activity at speed, however, involves a high risk of injury. TAWI Lifting Trolleys allow any worker to easily lift and mount reels, without risk of injury and with minimal downtime.
Protect Your Products: How TAWI Minimises Damage and Prevents Contamination
Another challenging situation is the packing or palletising of the ingredients or raw materials used in food and beverage products. Any tears or holes in the bags or sacks could allow foreign substances to contaminate the materials, potentially rendering them useless or dangerous to consume. TAWI’s line of vacuum lifting equipment removes this danger, quickly and carefully moving, stacking, or handling even the most fragile of containers or packaging with no risk of damage to either products or employees.
The TAWI Motto: Improved Ergonomics = Economics
The way you manage your handling and lifting procedures can dramatically impact your bottom line. The math is rather simple:
- Increased handling safety = increased efficiency
- Increased efficiency = improved customer retention
- Inefficient lifting operations = wasted labour
- Wasted labour = unneeded cost
- Employee injury/Absence = decreased productivity
The TAWI advantage
Evolve towards a more profitable process with:
- A more flexible workforce
- A safe and healthy workplace
- Reduced absence due to injury
- Minimised damage and loss
Whether for reels, bags, boxes, cans, cartons, pallets, or barrels, or even the direct handling of food products, TAWI stainless steel lifts and trolleys ensure safe and ergonomic lifting at all stages of your packaging process. TAWI lifting equipment is low cost, low maintenance, easy to install, requires minimum effort to use, and is easy to clean and disinfect – a crucial requirement in many food packaging environments.
With TAWI solution lifting solutions for the food packaging industry, you can optimise operations, reduce damage and waste, make employees’ jobs easier and safer, and ensure both regulatory compliance and company growth.
Contact us to discuss how you can make your food packaging process more efficient with a TAWI solution.