Flexibility and efficiency in the beverage industry
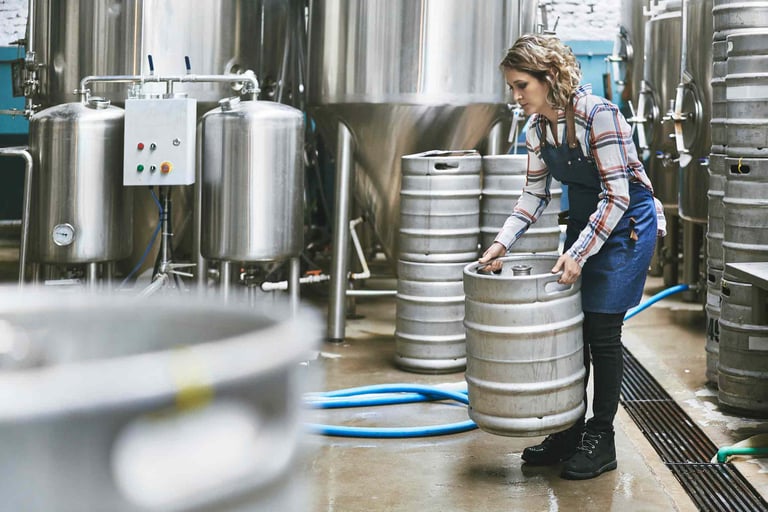
Never before has there been such a range of different types of beverages. While this evolution is great news for the beverage industry at large, it does pose certain efficiency challenges, particularly for production facilities, warehouses, and distribution centers.
“A customer can have a car painted any color he wants as long as it's black.” - Henry Ford, 1939
To put it mildly – things have changed since Henry Ford uttered those famous words. These days, consumers expect to get products in a wide range of versions, not just the ones the manufacturer chooses. This trend can even be seen in the food and beverage industry. Never before has there been such a range of different types of beverages.
Consumers are experimenting with new flavors and ingredients, even entirely new beverage categories. And when larger players are slow to act to meet these changing demands, smaller, more agile producers pop up to fill the gaps. While this evolution is great news for the beverage industry at large, it does pose certain challenges.
The efficiency challenge of handling more
Managing the growing number of new product launches, packaging designs and sizes requires a great deal of flexibility and agility on the part of the manufacturer. It means that production facilities and logistics centers must be able to quickly adapt to new demands and new products, to a wide range of ever-changing operational and practical hurdles – and so too must their staff. In addition, the manual handling involved with the production, storage, and shipping of all of these products brings with it a list of safety and health hazards that can endanger both employees and profitability.
Consumer and market demands, however, represent only a small portion of the challenges facing the beverage industry. There are also regulatory and legal standards and requirements that must be met, safety practices that must be adhered to, and a long list of human resource and staffing issues. Not meeting any of these requirements can prove disastrous to your business.
As if that wasn't enough...
The Covid pandemic that began in 2020 was a game-changer for many businesses, including food and beverage companies, with effects both beneficial and detrimental to operations. Covid brought a surge of consumer panic buying and demand for products with a long shelf-life, but also the shuttering of many firms in the foodservice industry, from restaurants and pubs to caterers and event properties.
Consumer preferences are always changing, but the pandemic created shifts in buying habits that most of the industry was not prepared for. Manufacturers were left looking for ways to increase production amidst a global crisis that affected the availability of labor and raw materials as well as the logistical chains that both supplied the factories and delivered products.
The end result was an inability to accurately predict consumer trends or to accurately manage the production needed to supply it. Food and beverage manufacturers have been forced to adapt quickly or risk going out of business.
And so, what have we learned from this experience so far? What key take-aways can we use to improve our businesses?
Key success factors in beverage production and logistics
- Creating a more flexible workplace
- Creating a more flexible workforce
- Maintaining staff health and safety
- Reducing absence due to injury
- Minimising damage and loss
Flexibility and efficiency challenges in beverage production
“The only constant in life is change.” - Heraclitus 535 – 475 BC
Being flexible and able to adapt to changing demands is not merely a matter of shifting production capabilities – the repercussions of every change echo throughout the entire chain.
In the beverage industry, this means that the physical challenges involved with the lifting and moving of heavy, cumbersome items like sacks of ingredients, large and cumbersome drums, and shrink-wrap rolls must be able to be performed by available staff. It means that the repeated, often awkward, handling of bottles, cans, and kegs must be done in a safe and sustainable manner, while still ensuring high product quality and productivity.
And, naturally, it means being able to change with the times, to have the tools in place that enable you to shift operations based on ingredient changes, quality concerns and staffing shortages. It means creating a production or logistics operation that can be quickly transformed to meet whatever challenges the future holds.
But first, a few words about safety
Did you know that that the leading cause of workplace absence and loss of production is caused by improper manual handling? This is especially true in the beverage industry, with its repetitive lifting and moving of heavy or unwieldly objects, often resulting in wear and tear injuries and physical overstrain that lead to down-time and sick leave. The sprains and strains that arise from unsafe lifting or handling, the back injuries, and soft-tissue injuries to wrists, arms, shoulders, neck or legs, lead to high rates of absence, high employee turnover, and sometimes devastating disturbances to operations.
Long seen as an HR matter, smart companies in the beverage segment are now viewing injuries due to unsafe handling as a key production issue, and acting accordingly. Vacuum lifting solutions from TAWI can help create a more ergonomic, more agile, and more profitable operation.
Negative health effects of incorrect manual handling:
- Back, neck, shoulder, arm, and other body injuries
- Damage to muscles, tendons, ligaments, bones, joints, blood vessels and nerves
- Severe cuts, bruises, fractures, etc., due to accidents
- Long term neck and upper limb disorders
- Long term lower limb disorders
- Long term back injuries and pain
The TAWI motto: ergonomics = economics
There are many ways that improper lifting procedures can impact your bottom line.
Increasing handling safety increases efficiency which raises customer retention. When efficiency falls, customer retention will as well. And when customers leave, your bottom line will reflect their departure.
Inefficient lifting operations leads to wasted labor. One study showed that wasted motion added up to almost seven lost weeks per year. Ask yourself - how much more productive would your operations be if you had an extra seven weeks of labor at your disposal?
Employees tasked with repetitive lifting and picking duties are at greater risk for musculoskeletal disorders (MSD’s). MSDs are often responsible for a third of all work-related injuries. Absences due to illness or injury represent a large chunk of operating expenses and decrease productivity.
At the end of the day, even the most physically fit employee will be tired – occasionally, a few will be injured.
Ergonomic lifting equipment never gets tired – or injured - it just keeps working
With TAWI lifting solutions for the beverage industry, you can better manage production, optimize operations and reduce waste. This also includes making employees’ jobs easier with less manual work, ensuring compliance and managing business growth. Simply put, better material handling is essential to ensuring a safe and efficient - and profitable - workplace.
At Dugges Brewery in Sweden, TAWI vacuum lifter has helped to eliminate heavy lifting of kegs and greatly improved the work environment. Explore the full customer case.
Creating a safer, efficient and more flexible workplace
In addition to creating a safer workplace, smart lifting solutions helps make operational shifts easier to manage and accommodate. Any worker can safely lift and manage any load, with often only a single employee required to handle materials that previously required several workers. The ability to use any employee for any job means it is easier to reallocate your resources when needed due to absences, production changes, or varying work orders. With a smart lifting solution, you can easily adapt to an alternative production plan and accommodate operational changes – while still maintaining quality and speed.
The ability of any worker to manage heavy or cumbersome loads means that you can create a more diverse workforce, reducing hiring restrictions. A more flexible workforce also means that you can create effective job scheduling based on supplier delivery dates and raw material availability.
We've got you covered
TAWI provides lifting solutions for every stage of the beverage industry, from the handling of incoming materials at the production facility, through processing, packaging & palletizing, to handling the final products in all their forms. Our solutions can lift and move cans and kegs of different weights and sizes or handle multiple bottles. Keeping products safe and reducing worker injury and absence in the process.
Whatever the type of beverage you need to lift or move, whatever type of packaging it comes in, we want to find a lifting solution that will make your business more efficient and more profitable. Our ergonomic lifters take the risky physical work out of material handling and can work all day, every day so that your employees can too.