Facing manual handling challenges in the automotive industry
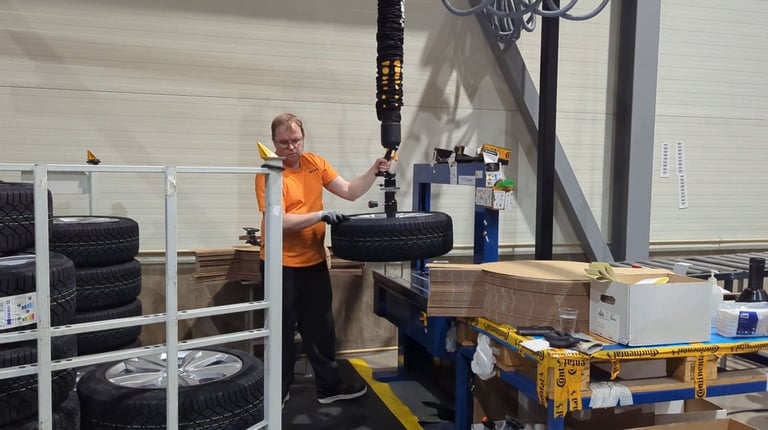
Automobile manufacture involves many diverse types of work across a wide range of sectors and industries. One challenge all sectors face, is that of manual handling.
Whether a matter of packaging and assembling parts or moving and installing components on a production line, manual handling in the automotive sector covers a broad spectrum of activities and encompasses many repetitive or strenuous tasks. The lifting, pushing, pulling, holding, and carrying that is required is a major contributing factor to workplace injuries, absences due to injury, and loss of production time. And at the end of the day – to lost revenue.
Manual handling is, of course, not the only challenge facing the automotive industry
But you might be surprised how dramatically this one issue can impact your business and how dealing with this challenge in an effective manner can reap other, seemingly unrelated - rewards. Let’s start by taking a look at some of the most overall challenges facing the automotive manufacturing industry.
Top concerns and challenges in automotive manufacturing:
- The need to maintain process speed while avoiding rework due to errors
- The need to maintain operational precision and comply with rigorous quality regulations
- The need to ensure occupational safety while carrying out processes with constant repetitive tasks
- The need to maintain operational precision in processes that cannot be automated
- The need to carry out manual activities in an ergonomic and productive way
- The need to improve the working conditions of employees
- The need to invest in Ecco-friendly new technology focused on sustainability
- The need to be flexible enough to deal with unexpected global events
Does every cloud have a silver lining?
Without question, the recent pandemic has changed the way we live, work, and buy things. It has also impacted the auto industry, exposing weaknesses in production and supply processes and giving rise to new challenges, from supply chain issues and managing social distancing in the workplace, to difficulty in finding and keeping skilled workers.
The inability to align production lines with social distancing demands alone led to a variety of factory and assembly line closures during 2020, with job losses as a result. While the worst of the pandemic is hopefully behind us, the challenges we have seen are likely to remain or recur.
How can we keep production on track while staying safe in close working environments?
And how can we continue to attract skilled workers in an increasingly competitive environment?
The pandemic is not the only recent upheaval affecting the auto industry. Increased governmental and public focus on environmental issues has caused the industry to seek greener alternatives to traditional gas or diesel combustion engines. This means that many car companies are beginning a partial – or in some cases total - switch to electric motors, entailing new production techniques and a range of new components and parts.
Like any dramatic shift in manufacturing, this places strain upon logistics, assembly, and associated processes. How can manufacturers build more flexible, adaptable workplaces, that are as future-proof as possible? How does on prepare for the unexpected?
The world is always changing. Both the pandemic and the rapid move to new technologies have been a wake-up call for all industries, requiring changes in how we carry out all stages of the manufacturing process. Some of these changes will prove to be temporary, others to be permanent or reoccurring.
So what can a company do now to safeguard the future?
Adaptability = Future-proof manufacturing
Perhaps the most important success factor for any future-safe industry is the ability to quickly and adequately adapt to change. In a rapidly growing sector like the automotive industry and its supply chain, constant changes are the norm, now more than ever. These changes, while driving a new era of automotive innovation, are also transforming entire engineering processes, production facilities, and manufacturing solutions.
More and more, the automobile industry relies on just in time manufacturing to meet these challenges and to fulfil its order book without holding excess stock and finished cars and vehicles. To achieve this delicate balance, a facility must have every stage of every process optimized to be as quick and safe as possible. Every component must be in the right place and at the right time, and in the right condition.
It takes thousands of components - in a huge variety of shapes and sizes - to build a vehicle. Lifting and handling solutions in an automobile manufacturer need to be not only flexible and adaptable enough to handle this wide array of components, but able to carry out the complex or strenuous tasks of moving and placing them repetitively, accurately, delicately, and reliably.
This is where vacuum lifting solutions are an ideal addition to your manufacturing toolbox
TAWI vacuum lifters offer solutions for gripping, rotating, tilting, and lifting a broad range of components such as, batteries, tires, chassis parts, dashboards, windscreens, windows, doors, and more. TAWI’s solutions are helping numerous manufacturers dramatically improve efficiency and productivity by enabling manual tasks which normally require two or more operators to be done by a single employee. With TAWI vacuum lifting, all operators can carry out any process safely and efficiently. The result is a more flexible workforce, ready to adapt to any change needed – and just in time.
But far from simply enabling your company to better deal with a changing future roadmap, TAWI solutions provide immediate financial incentives as well. We do this by helping reduce the negative impact of faulty manual handling.
What are the most common manual handling risk factors?
- Loads that are too heavy
- Loads that are too large
- Loads that are difficult to grasp
- Loads that are unbalanced or unstable
- Strenuous or repetitive movements
- Awkward lifting or moving postures
Want to learn more about common manual handling injuries? Check out this article "the 3 most common manual handling injuries".
One size never fits all
In an effort to create less emphasis on human or manual control and reduce the risk of person-to-person contact, many manufacturers are looking to automate as many processes as possible. Not all processes can be automated, however, especially some of the more common manual ones. And the very processes that are difficult to automate are those that pose the leading challenges to achieving occupational health and safety in the industry.
Automation using robots is often an ideal solution
But auto production covers many processes beyond the final assembly of the car. These many sub-processes, such as the parts supply chain, chassis assembly, handling of spare parts, tire creation and handling, injection of plastics to create dashboards and control panels, and the like, are hard – or impossible – to automate. They can, however, can benefit dramatically from vacuum lifting and handling solutions.
In addition, the implementation of robots to automate tasks can require extensive investment – ROI on robot automation can exceed 36 months, while a vacuum assisted lifting unit can provide ROI in less than 12. Vacuum lifting solutions enable a single employee to do the work of two or more, safely and ergonomically, and with no damage to components or products. Allowing adequate distancing where required, improving employee health and morale, and increasing efficiency and productivity.
Negative health effects of incorrect manual handling:
- Back, neck, shoulder, arm, and other body injuries
- Damage to muscles, tendons, ligaments, bones, joints, blood vessels and nerves
- Severe cuts, bruises, fractures, etc., due to accidents
- Long term neck and upper limb disorders
- Long term lower limb disorders
- Long term back injuries and pain
Risky workplaces are risky business
Manual handling is the primary cause of musculoskeletal disorders (MSDs) in the automotive industry. MSDs encompass a wide variety of injuries, running the gamut from damage to joints, ligaments, , tendons and nerves, and other structures in the back to injuries to arms, shoulders, neck, abdomen and legs. Often referred to as 'sprain and strains’, MSDs account for more than half of all injury claims in the workplace.
In addition to the pain and suffering experienced by workers suffering these injuries, these claims cost employers as well; many millions of dollars are lost every year due to injuries, absences, and lost production time.
Manual handling occurs in almost all working environments, and workers in the automotive industry are especially at risk
Manual handling may cause cumulative disorders due to gradual deterioration of the musculoskeletal system through continuous lifting / handling activities, cause acute trauma such as cuts or fractures due to accidents, and may have serious consequences to workers, restricting their ability to undertake a wide range of work and leisure activities for the remainder of their lives. Prevention is vital. Reducing the risk of these types of injuries involves carrying out manual tasks in the safest and most efficient manner.
Discover more about how to prevent hazardous manual handling these in our guide.
Benefits of eliminating manual handling risks:
- Increased worker safety and ergonomics = decreased absence, less production loss
- Increased process speed, decreased rework due to errors
- Improved work conditions = easier recruitment and worker retention
- Increased workforce flexibility
- Increased process precision and efficiency
- Better control over your entire production chain.
- Cost-effective integration into lean manufacturing solutions
- Improved bottom line
Is it time for TAWI's ergonomic solutions?
TAWI has focused many years of research and product development on improving or eliminating the postures, movements and forces that are known to be associated with MSD be from the workplace. TAWI lifting solutions for the automotive industry have been designed to remove the strain of repetitive lifting and to meet the specific challenges faced when handling incoming goods, such as the need to stack goods between very low and very high levels or to handle large, yet delicate items like window glass.
All TAWI lifters features unparalleled ergonomics and can be configured for handling a wide range of different goods such as boxes, sacks, windshields, sheets of metal, etc., quickly and safely and without kneeling or bending to reach the objects.
From receiving raw material in logistics centers, production line processes, handling of tires throughout production, to final assembly and storage, TAWI can help you create a more ergonomic workflow that will not only ensure a healthier, more flexible workforce, but also improve concentration and motivation in workers, which dramatically reduces errors and rework.
Challenges will always exist for the automotive industry and its suppliers
The best strategy for future success is to keep production processes as flexible as possible and to provide as safe and attractive a workplace as possible. TAWI vacuum lifting solutions can help on both fronts. Our experts will be happy to visit your site and help you identify the links in your vehicle manufacturing chain which can be immediately and dramatically improved.