Are lumper services still cost-effective for the logistics industry?
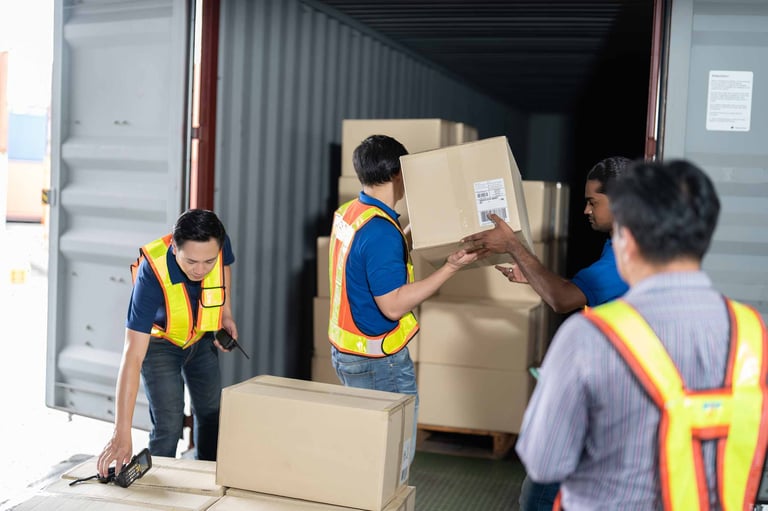
If you’re involved in the supply chain sector, you’re likely familiar with the term ‘lumper’. For those who aren’t, ‘lumping’ is a term used in the trucking industry to describe the process of loading and unloading freight by anyone other than the shipper, receiver or truck driver.
Lumper Services: A necessity or a costly convenience?
Lumpers, typically found in the food sector, have served as a useful backup when gaps in the supply chain arise, where truck drivers would otherwise be responsible for unloading and sorting their loads. In return for their services, lumping companies charge a fee.
According to a 2023 supply chain survey targeting decision-makers in nine European countries, 76% of logistics leaders reported labour shortages as either high or extreme, indicating a gap in the supply chain that needs addressing. Furthermore, 58% specified that workforce shortages have negatively impacted service levels. So a solution to this is certainly relevant in today's environment, but, does hiring lumpers remain the most economically viable solution to address this issue?
At TAWI, we argue that the benefits of a permanent solution to labour shortages within a company far outweigh temporary solutions, such as hiring lumpers.
In-house workers vs Lumpers Services
Are you contemplating the addition of more in-house workers as a more permanent solution? Even without a significant labour shortage, this might not be the most cost-effective solution. The key difference between the two lies in the payment structure: one is a flat fee, the other is an hourly rate. According to Indeed & ZipRecruiter, in 2024 the average hourly wage of a material handler in the US is between $15-20ph. On the other hand, the cost of a lumper service can range from $50 to unload a truck to $250 to unload a full trailer, depending on the amount of work and number of labour hours required.
Whilst it’s challenging to make a direct price comparison or provide exact figures, lumper services are generally less expensive than in-house dock workers because they don’t qualify for the same benefits. Lumpers charge a lump sum for their services, unlike in-house workers who require hourly compensation in addition to health insurance, safety gear, workers’ compensation and leave allowances, all of which add up.
Lumpers, as independent contractors, are responsible for their insurance, injuries and other costs incurred during their work. Employing lumpers helps facilities reduce liabilities, such as workers’ compensation and disability insurance premiums. Indeed, the insistence of docks on carriers paying lumpers is primarily because it transfers the liability to the third-party agency that hires them.
The Controversy Surrounding Lumper Services
As mentioned, the fee of lumper services is hard to pin down as it depends on the contractor and quantity that is being unloaded, but there are other costs to your business to consider when using a lumper service.
Lumper services often find themselves under scrutiny, with terms like "scam" frequently appearing in freight and trucker-focused blogs. Whilst such generalisations can't be applied to all lumper services, which play a crucial role in maintaining a smooth supply chain, there are indeed some areas of concern. One such area revolves around the fee structure. Tension arises when it comes to reimbursing the cost of the lumper. When a carrier or broker engages in a lumper service, the driver pays the lumper fee to get the truck unloaded. This fee is then reimbursed to the driver by the carrier or broker.
This process can become problematic due to the industry's reliance on outdated, paper-based payment methods like cash, industry-specific checks and lumper receipts, which can take a significant amount of time to process and reconcile. The driver may face a lengthy wait to get reimbursed, and in the worst-case scenario, the driver isn't reimbursed at all due to poor reconciliation. Fortunately, the payment process is undergoing rapid modernisation; with digital transactions, payments are not only instant but also secure the lumper receipt and audit trail.
However, lumper services can have indirect costs on your business, making the process inefficient compared to other avenues. Money can be lost as drivers can be forced to wait for the arrival of a lumper leading to costly delays also.
Is there another way?
TAWI has engineered a solution that allows you to optimise the productivity and efficiency of your existing trained workforce without compromising on safety. How is this achieved? The manual unloading of goods can be physically demanding. By utilising our efficient vacuum lifting solutions for unloading containers, your business can save both time and money, whilst also prioritising the well-being of your employees and minimising downtime. We provide a variety of vacuum lifting solutions, each customised for different aspects of package handling.
Our Container Unloader enables all workers to lift up to 80kg, as the vacuum does the heavy lifting, and your employees simply guide the vacuum. This is a one-handed operation that allows the operator to grip items from any angle and rotate them. Additionally, it’s mounted on a mast that can be raised or lowered, and on an arm that allows it to move side-to-side and forwards/backwards, aiding operators in reaching items.
Explore this case study at S&S Activewear in North America to see how the Container Unloader can optimise warehouse operations.
Our lifters give your workforce complete flexibility and maintain health and well-being within your workplace whilst addressing the increasing pressures of packaging handling.
Want to dive deeper into how you can boost efficiency in your warehouse? Check out our guide "The Complete Guide to Improving Efficiency within Warehousing Logistics".