Streamline logistics: enhance efficiency with the right container unloading solution
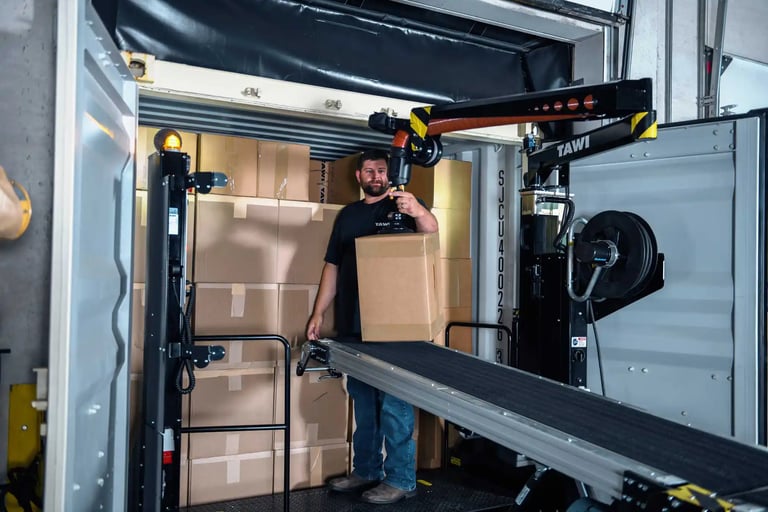
Container unloading is one of the few remaining labour-intensive aspects of the modern economy. Due to the diverse range of items and the limited spaces within which they are packed, loading and unloading these large steel crates are among the last processes in logistics that rely heavily upon manual labour.
With the surge in e-commerce, the supply chain is experiencing a massive increase of containers filled with consumer goods. This raises the crucial question: How can the industry streamline the loading and unloading of containers, without compromising on safety?
If steel and electricity could replace muscle and sinew in this crucial function, there would be obvious benefits for workers, employers, and the economy as it would streamline logistics. Luckily, we have worked hard to provide a solution to the container unloading problems. If you are a logistics professional seeking to safely and efficiently unload a container or trailer, keep reading and prepare to get some actionable information.
Container unloading challenges
Container unloading is challenging for various reasons:
A container typically has limited space and manoeuvrability, making it challenging to streamline logistics.
It is usually performed by relying on manual labour, which is in short supply and prone to injury.
Lifting heavy items puts a strain on people. According to NSC Injury Facts, musculoskeletal disorders (MSDs) create financial burdens for businesses, including medical costs, reduced productivity, and employee absence.
In 2020, the private sector reported 247,620 MSD injuries or illnesses, resulting in lost workdays. Implementing ergonomic measures and workplace safety initiatives is crucial to minimise the impact of MSDs on businesses.
“We have had so many customers coming to us and sharing the pain of manually unloading inside a container or trailer… Logistics companies have problems with ergonomics. It is hard to find people to do this job, and a swift return on investment (ROI) is both essential and difficult to achieve with existing mechanical solutions. This is the essential dilemma of container unloading.” Anders Knapasjö, President Nordic, Baltic & Germany for TAWI.
In theory, machines can streamline logistics as they can transform the unloading process as long as they are designed to consider the complex issues that arise when a container is backed up to the warehouse gate.
However, automated systems have limited flexibility. Even if a machine can handle a wide range of items stacked in various ways, there will always be something that demands human intervention.
Flexibility is expensive. Mimicking a human being’s ability to identify, reach, grasp, twist, and lift multiple items comes at a prohibitive cost.
Robots are not a solution – at least not for the foreseeable future
However, unloading containers is an excellent example of an industrial process in which semi-autonomous systems – machines combined with human operators – are more likely to offer an efficient way forward to streamline logistics.
The TAWI Container Unloader, our mobile container unloading solution, has been specifically engineered to address this need. It’s designed to enhance both efficiency and safety by tackling lifting challenges with its versatile capabilities, making it adaptable to a variety of operations.
Traditional container unloading tips and best practices
As mentioned, container unloading is a challenging task, and it is important to think about safety as well as efficiency. To ensure secure and effective container unloading and to streamline logistics in general, here are some essential tips and best practices to follow:
- Take special precautions if the container is loaded with hazardous materials:
Adhere to all relevant safety regulations and guidelines specific to handling hazardous substances. Provide appropriate protective gear to workers and ensure they are trained in handling such materials safely. - Utilise appropriate equipment:
Depending on the nature of the cargo and its weight, choose suitable equipment for unloading containers. Forklifts, mobile lifting solutions, container unloading systems, cranes, and conveyor belts can streamline the unloading process, increasing efficiency and reducing manual effort. Select the equipment that best matches the requirements of your cargo and facility. - Assess all possible dangers and address them:
Before initiating the unloading process, carefully assess all possible dangers associated with the container and its contents. Look for signs of instability in the load, such as leaning or shifting items. If any hazards are identified, take immediate action to mitigate them. Secure the load properly to prevent it from falling or causing injury to workers. - Ensure worker safety:
Workers directly involved in container unloading should be trained in proper safety procedures and techniques. Emphasise the importance of maintaining a clear and safe workspace, ensuring that workers do not get trapped or injured inside the container. Implement effective communication channels and signals to coordinate movements and minimise risks. - Optimise workflow and organisation:
Efficient container unloading requires careful planning and organisation. Establish a systematic approach to unloading containers, ensuring a smooth flow of goods so as to streamline logistics. Clearly label and categorise items to facilitate their handling and subsequent storage. Consider implementing technology-driven solutions, such as barcode scanning or RFID tagging, to enhance accuracy and streamline inventory management.
By implementing these container unloading tips and best practices, you can enhance both the safety and streamlined logistics of your operations. Remember, prioritising worker safety and proactively addressing potential hazards are crucial for successful container unloading, and this doesn’t have to come at the expense of optimising efficiencies.
Here’s how to streamline logistics with TAWI's container unloading solutions
In response to the urgent need for machinery to help with container unloading, we at TAWI have developed mechanical aids that can tackle all the unloading challenges safely, intuitively, and flexibly. Our engineers developed solutions suitable for unloading the full spectrum of parcels.
TAWI offers two technical solutions to support efforts to streamline your unloading.
Solution #1
Firstly, the Mobile High-Frequency Lifter (MHL) can resolve all container unloading challenges.
How does it work?
- Push it on a pallet jack, take it inside your container, connect it to a source of electricity, and start unloading from the top of the stack with a gentle squeeze of an ergonomic trigger.
- The mobile high-frequency lifter uses TAWI’s tried and tested vacuum technology to grasp items and release them onto a pallet or conveyor.
Our Nordics Sales Manager, Anders Knapasjö, has been centrally involved in developing this solution. Below, he answers many interesting questions about the machine and its role in container and truck unloading.
What is the main problem that the Mobile High-frequency Lifter helps to face?
The purpose of the unit itself is quite simple: its function is to lift objects from a container or trailer onto a conveyor or pallet helping streamline logistics.
The Mobile High-frequency Lifter takes away 90% of the effort involved in unloading items weighing up to 50kg. It offers great versatility, allowing you to attach multiple suction tools, and enabling the lifting of various objects.
This is a plug-and-play machine, you just need an external power supply, and off you go. This lifting solution is nimble; you can move it on a pallet jack from place to place, so one machine can serve an entire warehouse – you don’t need to install one at each gate.
Solution #2
The TAWI Container Unloader (CU) helps improve efficiency and safety during the unloading of containers and sortation. How does it work?
Designed to enhance both efficiency and safety in container unloading operations, the TAWI Container Unloader is a mobile solution powered by a battery. It boasts a lifting capacity of up to 50 kg and is equipped with an integrated ergonomic vacuum lift, capable of lifting and rotating items from any angle.
The unloader also features a versatile mobile conveyor belt that can be adjusted in various directions for improved reach and ergonomics. For optimal reach, the operator platform can be adjusted in height and is equipped with safety rails for added protection. Thanks to its wheels and battery-powered system, the container unloader is fully mobile and can easily be moved to different doors or sites. Additionally, it has a flexible modular system that allows for unloading items onto a conveyor belt or a pallet.
What is the main problem that the Container Unloader helps to face?
The main problem that the container unloader solution addresses is the labour-intensive and potentially hazardous task of manually unloading containers. Manual unloading can lead to injuries from repetitive lifting and decreased productivity due to fatigue. It also often requires several people to meet unloading time frames, which can incur significant expenses. The Container Unloader helps to mitigate these issues by providing a semi-autonomous system that combines the capabilities of machines with human operators. This results in a more efficient and safer unloading process, reducing the risk of injuries and improving productivity.
Why has nobody done something like this before?
The problem has always been the cramped conditions inside containers. These are only 2.4m (7’10”) from floor to ceiling.
Most lifting machines require significant headroom above the object to be lifted, making it impossible to lift objects high up in the container. We have solved this with a patented “elbow” and wheel system that inverts most of the steel vacuum tube by 90° from vertical to horizontal to streamline logistics.
These container unloading solutions means the mobile lifters can reach up to the highest lifting points in a container, a capability unmatched by any other product on the market.
How easy is it to use?
User-friendliness is key, both in terms of getting to know the machine and then putting it to use. The Container Unloader and Mobile High-frequency Lifter are extremely user-friendly, they take just a few minutes to learn how to use it efficiently. Our training teams provide thorough training sessions on using our solutions when setting up machinery, so your workers feel confident using them.
Is its use confined to container unloading?
No. So far we have only talked about using the MHL inside a container. But after you have emptied it, maybe you want to move stuff from one pallet to another. Then you can simply move the product and pick and place your objects wherever you like.
Maybe you need to repack items somewhere inside the terminal – again, use our Mobile high-frequency lifter. In other words, this mobile machine has the potential to eliminate manual lifting inside the terminal also, making it easy to streamline logistics by adapting to a fast-changing environment with high production demands.
Are these container unloading solutions as fast as a person?
The difference is that these machines can keep up the same tempo throughout a working day, whilst a person slows down and needs to rest.
So over a full shift, these unloading solutions are actually faster than a person. In general:
- Manual handling will be faster than using mechanical help over the first hour or so.
- By the third hour, the speed of each method is the same.
- After three and four hours, the machine beats the person every time because it never gets tired.
This is crucial because the logistics business is all about speed.
What does all this mean for a company using these solutions?
Firstly, depending on what you are lifting, both the Mobile high-frequency lifter and the Container Unloader can turn a two-person lift into a one-person lift, instantly helping streamline logistics. In this case, the ROI is a no-brainer. In certain countries, you also have insurance issues, such as in the USA where you don’t have the same health service provision as in Western Europe.
But there are multiple efficiency gains with switching away from manual unloading. Staff turnover falls dramatically, while a large new recruitment pool opens up because anyone can lift anything with our product, whether they are old or young, male or female, big or small.
Both solutions allow your teams to work consistently, at the same tempo, for longer periods. Co you can calculate more rationally how long particular tasks will take and the resources you will need to do them. This in turn means you can plan much more accurately, making for a more efficient flow of goods into the terminal and into the warehouse. It is all about making the logistics flow as smooth and predictable as possible so that you can best manage your team, terminal and warehouse allowing you to discover other ways to streamline logistics.
This brings a lot of positive effects beyond simply lifting inside the container. It is suddenly easier to allocate resources such as people, forklifts, and so on – there is a domino effect throughout the business.
So, can TAWI’s solutions do everything except make the coffee?!
Any machine has its limitations. Logistics involves multiple challenges, and the MHL & CU won’t suit every task. Here are some things to be aware of:
- To expect this unit to lift everything is unrealistic. It will handle 80-90% of objects, but some will be outside range.
- Depending on the items and how they are packed, the top layer in the container can be a problem. For example, if the container is crammed to the ceiling, you may manually pull out the top layer before the MHL or CU can take over.
- When fully extended, the arm is 2m (6’7”) long and rotates 360 degrees so that you can reach a maximum of 4m. With a crane system attached to the warehouse ceiling, you can lift objects as far as 10m.
- Sometimes a fixed crane vacuum lifting system will be more efficient in the long run for a particular task. For example, if you have a fixed conveyor in the warehouse and are sorting from the belt to pallets, the MHL probably doesn’t have the necessary reach. The MHL is a flexible solution for companies looking to move around with multiple pickup points.
To summarise, TAWI provides a wide range of smart vacuum lifting solutions to optimise your logistics operations. Our goal as a company is to connect the dots within the complex matrix of logistics issues.
If you’re looking to streamline logistics infrastructure in your warehouse, and improve efficiency, consider incorporating TAWI’s innovative solutions.
Now you have read a detailed overview on enhancing container unloading efficiency, we’ve put together a comprehensive guide towards Logistics Efficiency. The Complete Guide to Improving Efficiency within Warehousing Logistics (How you don't need to choose between productivity and people) is available here.