Four common challenges in warehouse order picking (and how to address them)
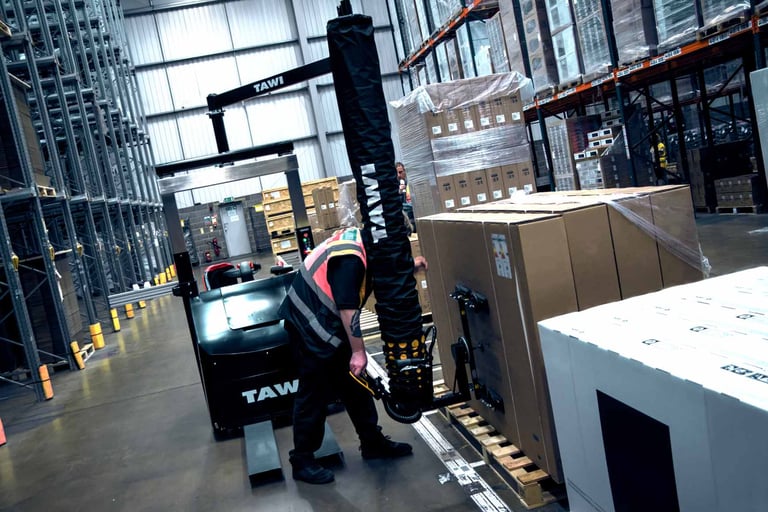
Within logistics, order picking often accounts for more than half of warehouse operating costs. The continued reliance on manual labour contributes significantly to the relatively high costs.
Then along comes a mobile lifting device that attaches to a palette jack and is equipped with a lifting arm that uses suction to grip heavy boxes securely. The lifting device addresses all four of the main headaches for production managers with regard to warehouse order picking; labour-intensity, time-efficiency, risk of employee injury and risk of product damage.
Toilets have a secret life. The next time you are seated on the throne of stone, think for a moment how it got there. Weighing around 40kg, it is no easy task to get this lump of porcelain from a store or delivery centre and into your smallest room. For one of North America’s largest hardware chains, this problem has economic implications. With thousands of stores, they sell a colossal volume of toilets, packed in boxes. It is a two-person lift to get the box onto a palette and out of the store.
From two-person lift to one person picking
Then along comes a lifting device that attaches to a palette jack and is equipped with a lifting arm that uses suction to grip heavy boxes securely. Using the device is slightly slower than two people working as a team, but it allows one person on their own to pick the toilets for delivery.
The hardware chain orders one such mobile picking device for each of its stores and sees a return on its investment within just four months, calculated only in terms of toilets and the labour needed to pick them. The staff relieved of picking duties are redeployed to other tasks. Job done – everyone is happy.
This story is one of the recent successes achieved by TAWI’s Mobile Order Picker. But the problem of order picking in modern logistics is much, much bigger than the humble latrine.
‘Order Picking 4.0’
Of all warehouse operations, order picking is one of the most expensive, and at the same time one of the hardest to automate. Order picking methods such as batching, zoning and wave picking have helped reduce the total picking time required to collect the requested items, and therefore raise efficiency. But although there have been concerted attempts to automate the picking process, manual order picking systems are still prevalent in practice.
Yet order picking is a key aspect of almost all supply chains and has a significant effect on operational efficiency of warehouses. Within logistics, order picking often accounts for more than half of warehouse operating costs. The continued reliance on manual labour contributes significantly to the relatively high costs.
The digital transformation means that industries around the world are facing novel challenges. In logistics, diverse, mass-customised and individualised goods are increasing the complexity of supply chains. This complicates the efficient management of logistics processes by, for example, decreasing the possibilities for bulk handling and shipping.
The rapid rise of e-commerce goes hand-in-hand with growing challenges for picking.
There are a number of reasons for this, including:
- An ever-rising number of orders
- High customer expectations in terms of fast and error-free delivery
- A growing variety of products in inventories
- Orders that increasingly comprise a smaller number of items
- High employee turnover and low availability of workers
The more complex the orders, the more important innovative order picking methods become
The digital transformation of industry is commonly referred to as “Industry 4.0”, while parallel developments in the logistics sector are known as Logistics 4.0. In order picking, we are also seeing the implementation of technologies to respond to the challenges of digitisation, including technical solutions that support the manual order picking process.
Researchers refer to these systems as “Order Picking 4.0”. Machine-based picking systems, in which order picking is performed by robots, remain limited in practice because of less flexibility and adaptability to pick heterogenous goods. Thus, we can reasonably assume that humans will remain an essential part of Order Picking 4.0, particularly given the trend of rising e-commerce and individualisation with high-mix and low-volume warehouses.
Warehouse order picking: a solution emerges
What might Order Picking 4.0 look like in practice? TAWI has been developing semi-automated lifting technologies for more than 30 years. We don’t pretend to have all the answers, but sometimes we can offer the logistics industry something so simple yet ingenious that it is worth a quick look at how this came about. The backstory also tells us about the common challenges faced by business with regard to warehouse order picking.
From prototype to final solution
At TAWI we are specialists in vacuum lifting technologies, but often our solutions come attached to a big steel frame that is bolted to the floor. A few years ago, our division in the USA found that businesses were knocking on its door in search of something new for warehouse order picking.
One such company was a national chain of stores selling sporting goods. They needed to pick a variety of bulky boxes packed with jackets, balls, nets and whatever, scattered throughout their warehouses. Picking these boxes meant driving a pallet jack up to the shelves and pulling out the boxes onto a pallet. This had to be a team lift – at least two people on the job.
“In addition to the weight of the items, they had to reach into the shelf, where you can’t do a proper lift. So from an injury perspective it was risky,” says Mike Lee, president of TAWI North America. “We experimented with a powered pallet jack, a sort of mini-forklift, onto which we mounted one of our vacuum lifters, powering the vacuum pump from the forklift battery. And it worked! The client liked it a lot.”
Optimal mobility and flexibility
The basic idea was sound, but it demanded a lot of work to develop a mobile lifting device that could fit onto any make of forklift or pallet jack, and that didn’t need to be bolted on – you don’t want to carry around the picking equipment when it isn’t needed. Secondly, an independent power source was essential.
“The solution was a standalone product compatible with any forklift or pallet jack, battery powered, lifting up to 80kg, and with an ‘easy reach’ tool that extends into a rack or shelf to pick out the product,” Mike says. “This makes the machine both flexible and 100% mobile. Moreover, the risk of injury to the worker and damage to the product fall essentially to zero.”
The lifting device thereby addresses all four of the main headaches for production managers with regard to warehouse order picking:
- It is very labour-intensive
- It is very time-consuming
- The risk of injury to employees is significant
- Risk of product damage
In essence, this is a tried and tested technology with added mobility and reach. When TAWI took its Mobile Order Picker to the market, several clients said they had started to design something similar themselves. This included “big box” stores on the outskirts of towns, but also warehouse distribution centres that serve the e-commerce market.
“Our vacuum lifters are not new, we invented them 30 years ago,” Mike says. “So the basic guts of the Mobile Order Picker is a well-known technology. It is very user friendly – staff are up and running after just an hour or two of training. And the return on investment is much better than full automation. Semi-automation like this is far less costly and far more flexible.”
Labour shortages and the benefits of semi-automation
A feature of the world economy as it emerges from the Covid pandemic is a shortage of workers in many countries. Migrants have returned to their home countries, older people have retired early, and childcare or health problems have led others to exit the labour market altogether. Employers have discovered that staff availability is not a given, but a business risk to mitigate against. According to the Financial Times, “a new generation of workers, from shelf stackers to delivery drivers, have learned just how essential they really are”.
How does this affect order picking?
“The picking process in warehouses is very labour intensive, and there was a labour shortage in logistics even before Covid,” Mike Lee says. “For most of the companies we speak to, this is a key driver in their thinking about order picking methods: they have no people. Some products require three or even four people to safely do the lift – think about barbecue grills, mattresses or canoes. So the hard truth is that many sites just ignore the safety aspect.”
Retail stores are everywhere, but distribution centres are often in more rural areas, adding to the labour problem. In the USA they are often are located on big motorway routes and grouped together, adding to the demand for workers. In short, you cannot limit your workforce to physically stronger induviduals. With mobile vacuum lifting technology you not just halve the number of workers you need, but you open up this task to a much wider workforce.
A smart and mobile lifting solution
The TAWI equation is to reduce injury, increase productivity, and boost labour flexibility. We are proud that the Mobile Order Picker doesn’t just solve this equation, but does so elegantly and convincingly. The technology is still new on the market and has excited considerable interest. In the USA, for example, a major e-commerce retailer has recently purchased 10 mobile order picking systems from TAWI and is piloting them at their distribution centres. Please don’t hesitate to contact one of our representatives to find out how this solution can help your business, just fill out the form below.