Lifting Insights
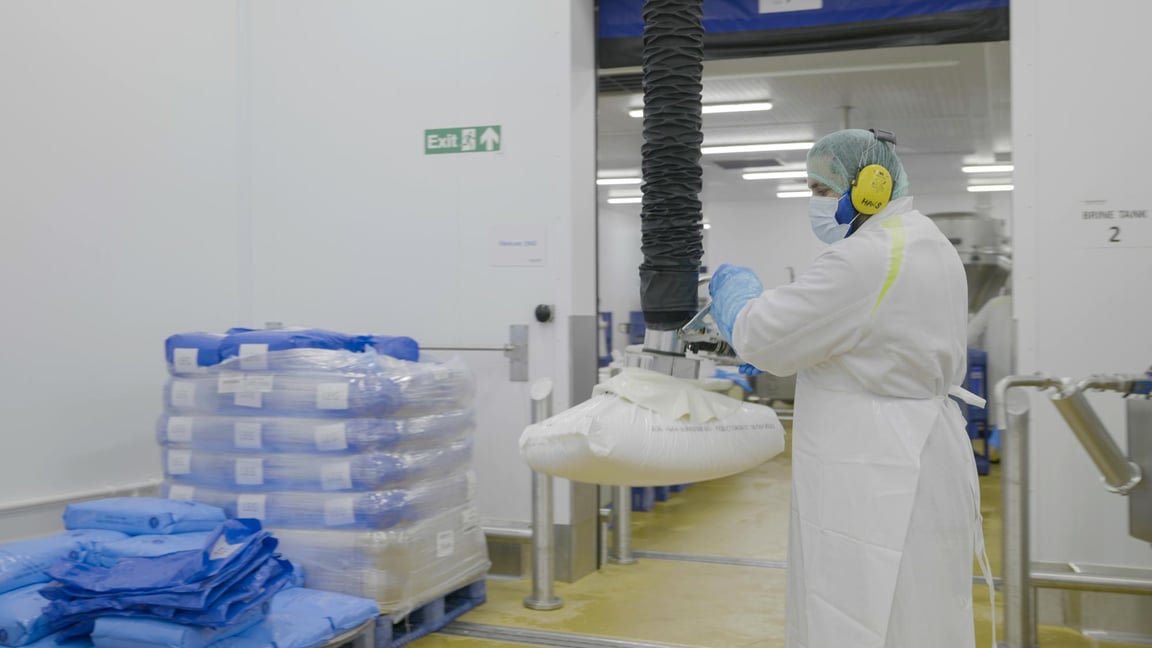
Innovation in Food and Beverage Industry: Trends & Challenges in 2025
Innovation in food and beverage industry is driven by shifting consumer demands, technological disruption, and sustainability concerns. To stay competitive in 2025 and beyond, businesses must not only keep up with evolving food industry trends but also proactively address the challenges that come with change.
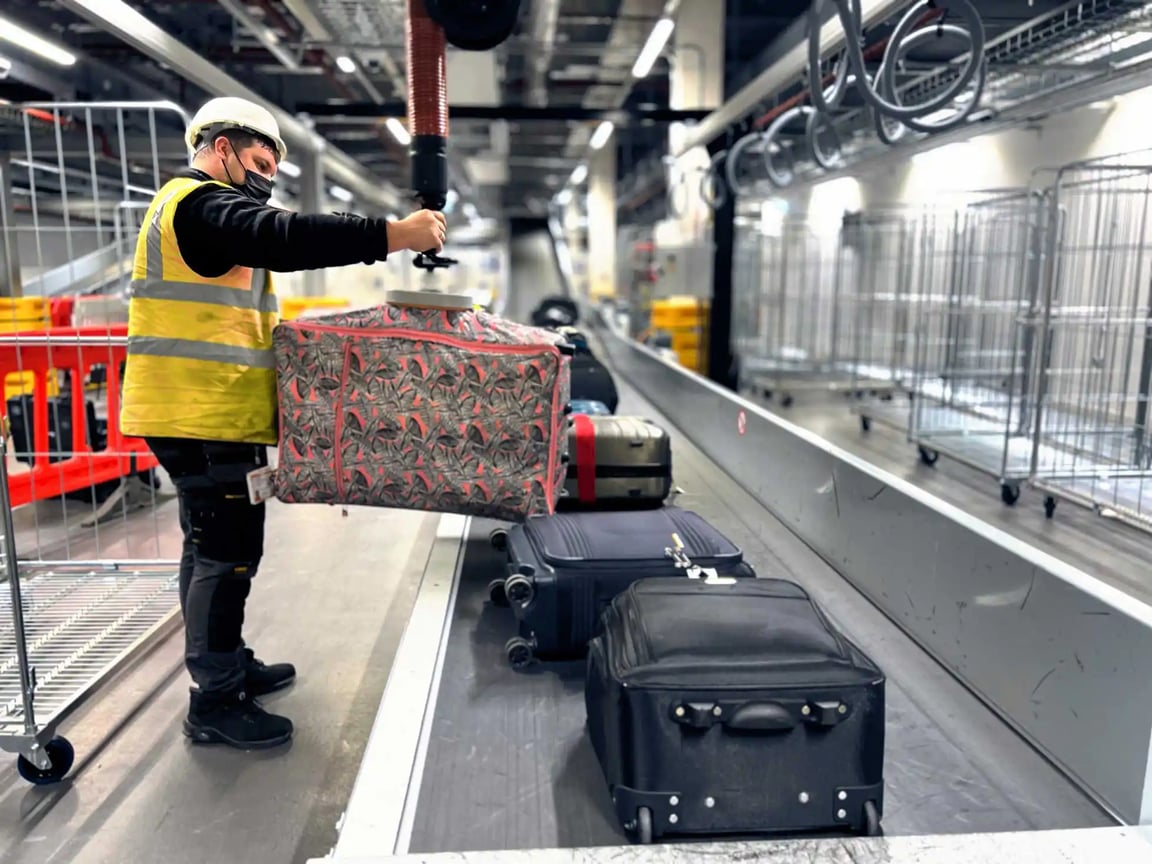
The True Cost of Getting Baggage Handling Wrong
People may joke about how baggage is not handled with care or often gets lost at transfer locations when they travel. But the truth is passengers have high expectations about their baggage, and there is a cost when baggage handling is done poorly – a cost that is being paid by staff, productivity, and budget.
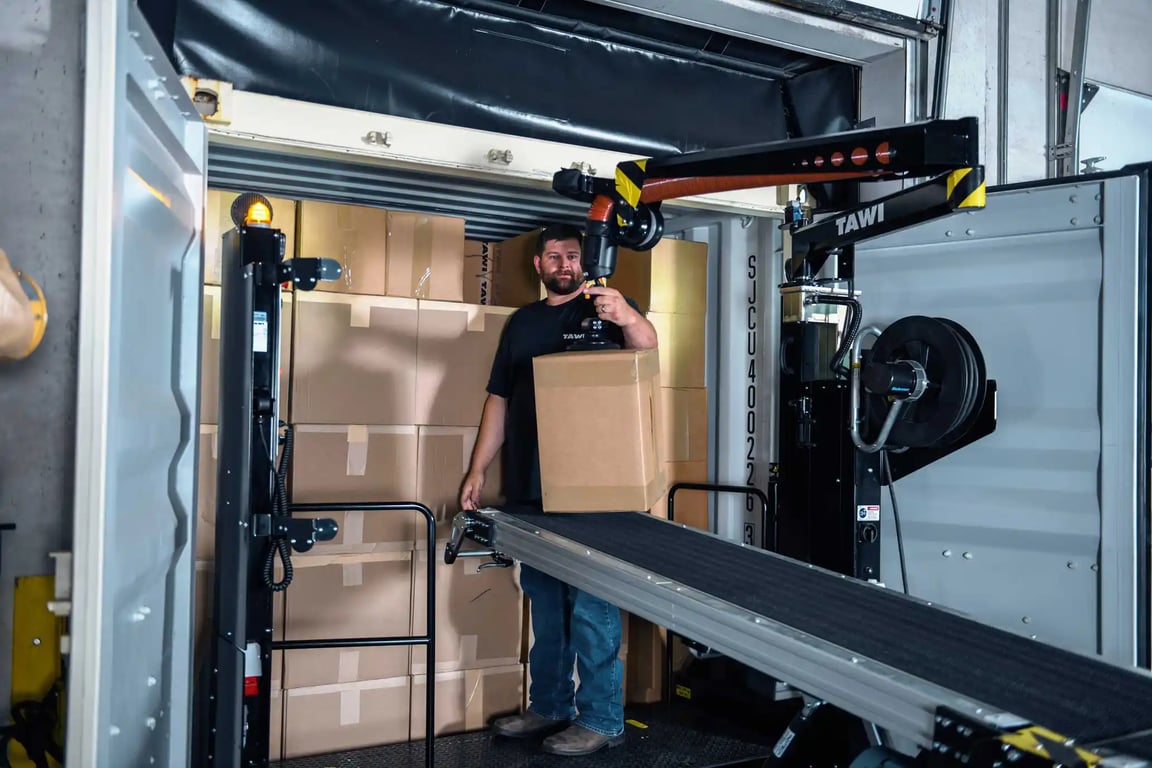
Streamline logistics: enhance efficiency with the right container unloading solution
Container unloading is one of the few remaining labor-intensive aspects of the modern economy. Due to the diverse range of items and the limited spaces within which they are packed, loading and unloading these large steel crates are among the last processes in logistics that rely heavily upon manual labor.
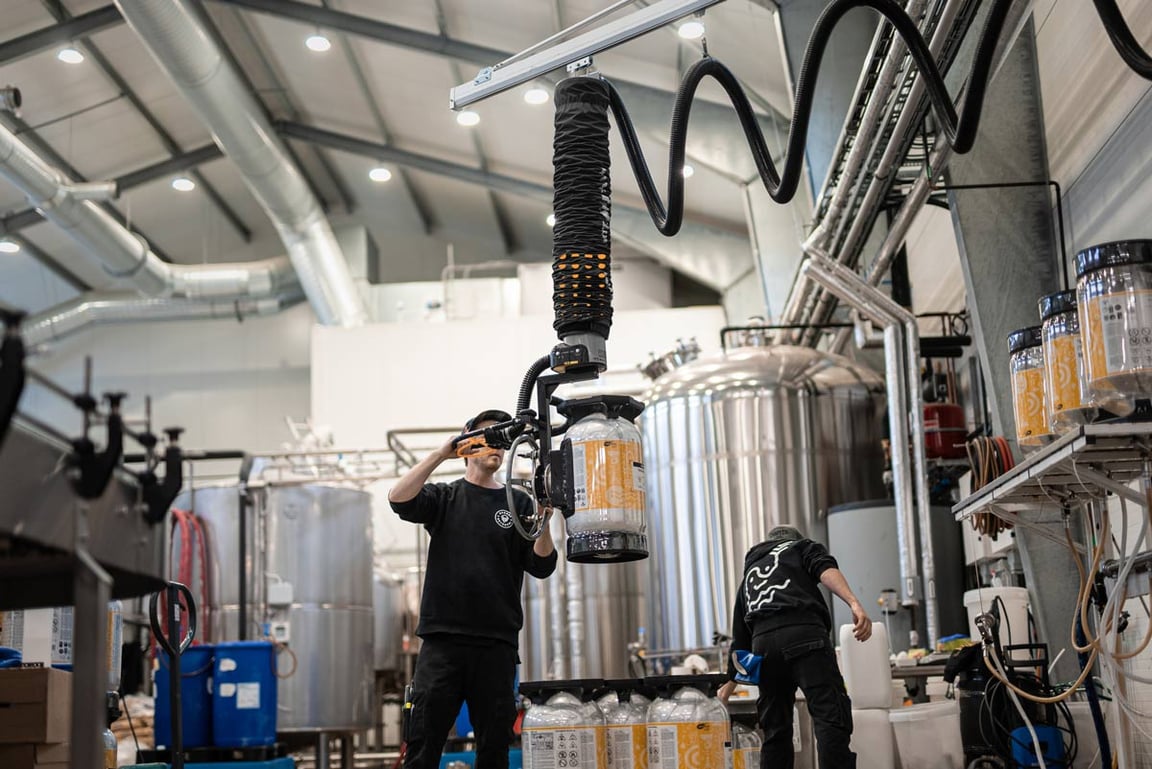
Why material handling in F&B is so important
Material handling is an essential aspect of the food and beverage (F&B) industry, encompassing the movement, storage, protection, and control of products throughout the manufacturing process. Effective material handling ensures that food products are safely and efficiently transported from production to packaging, storage, and distribution.
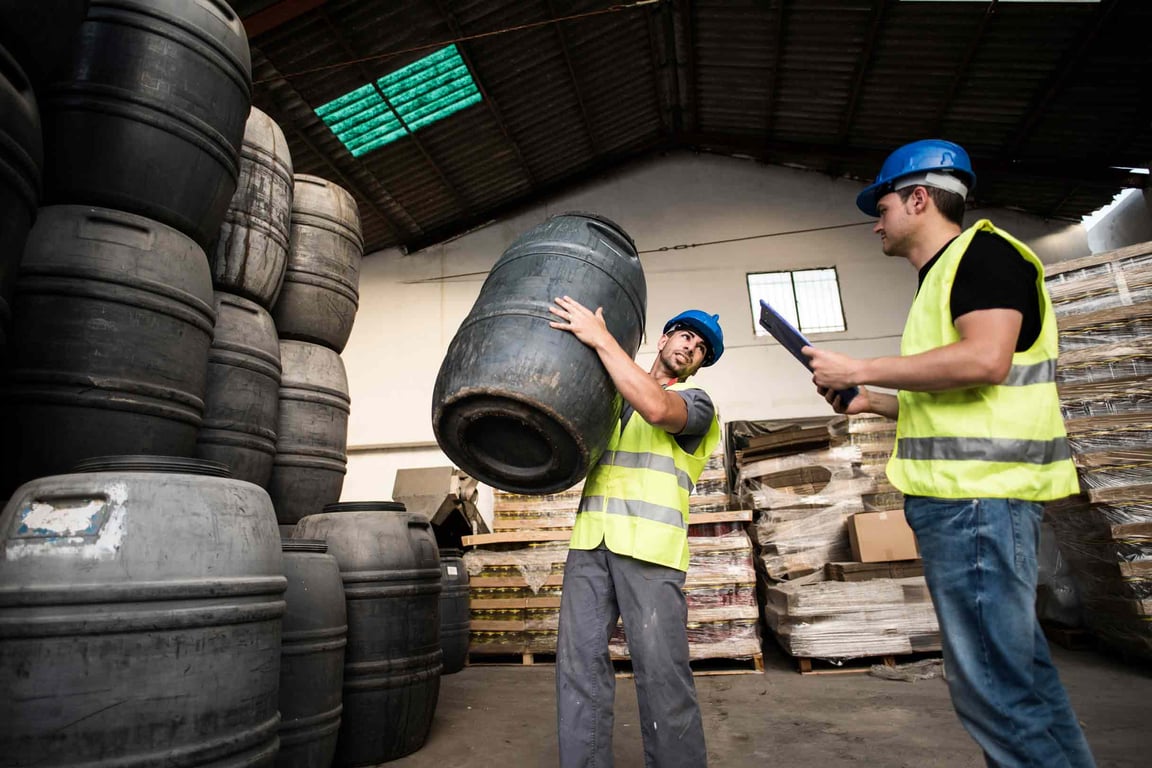
Hazardous manual handling: Risk assessment and preventions
Work-related musculoskeletal disorders (MSDs) resulting from manual handling are a leading cause of lost work time and work restrictions. By conducting a risk assessment in your workplace, you can proactively implement preventive measures to mitigate MSDs.
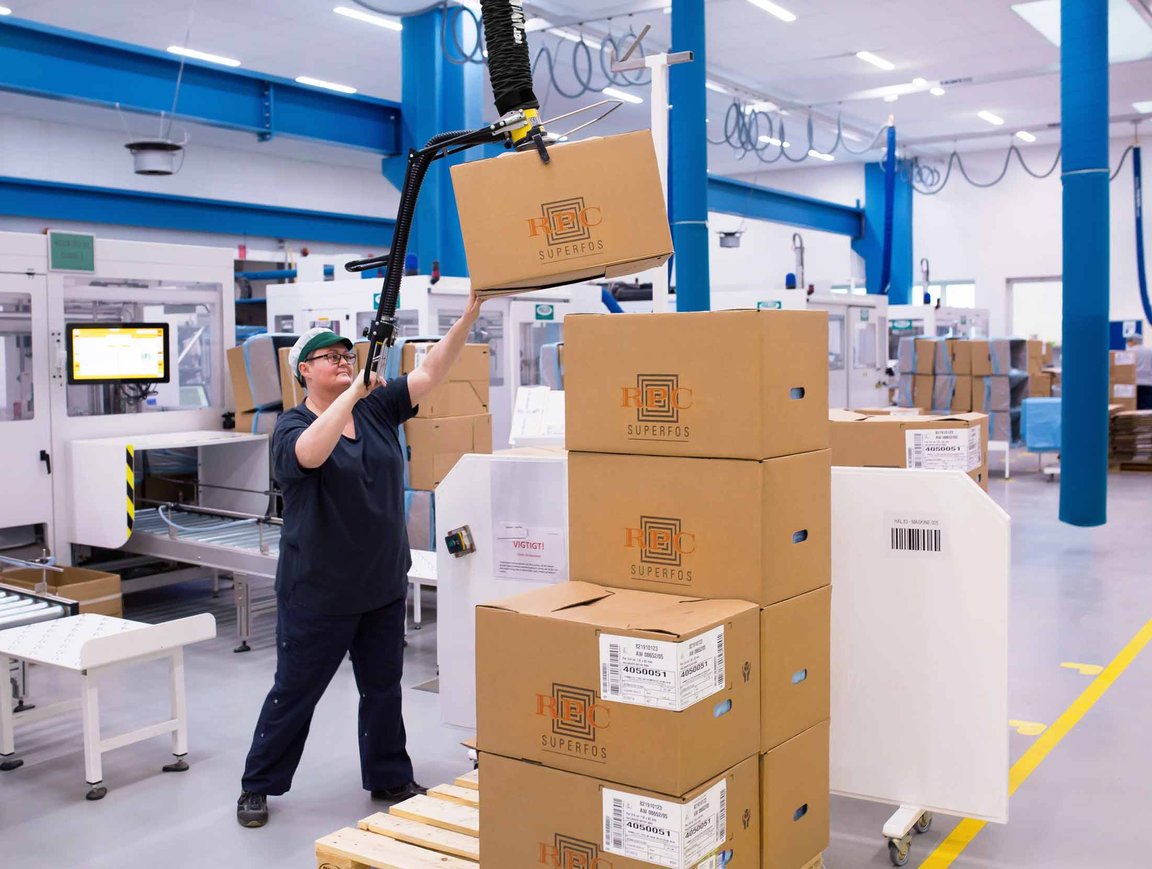
The types of lifting equipment that simplify material handling
As you explore ways to streamline and optimize operations in your warehouse or production plant — it’s time to consider lifting equipment. There are a variety of lifters and accessories to choose from beyond traditional forklifts.
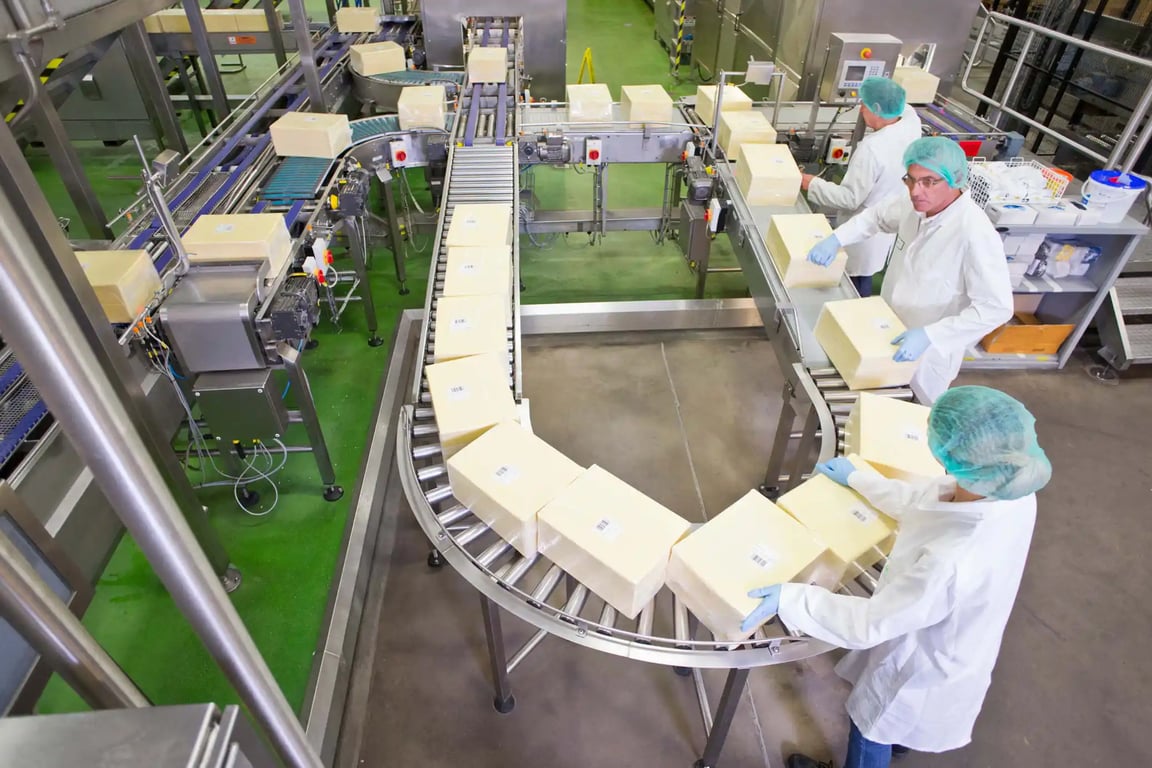
Sustainability and Savings in Food & Beverage
When considering TAWI vacuum lifters, lifting trolleys, and mobile lifting solutions, the initial draw lies in their efficiency and safety benefits. These tools streamline lifting tasks, reduce physical strain on workers, and transform two-person jobs into seamless solo operations.
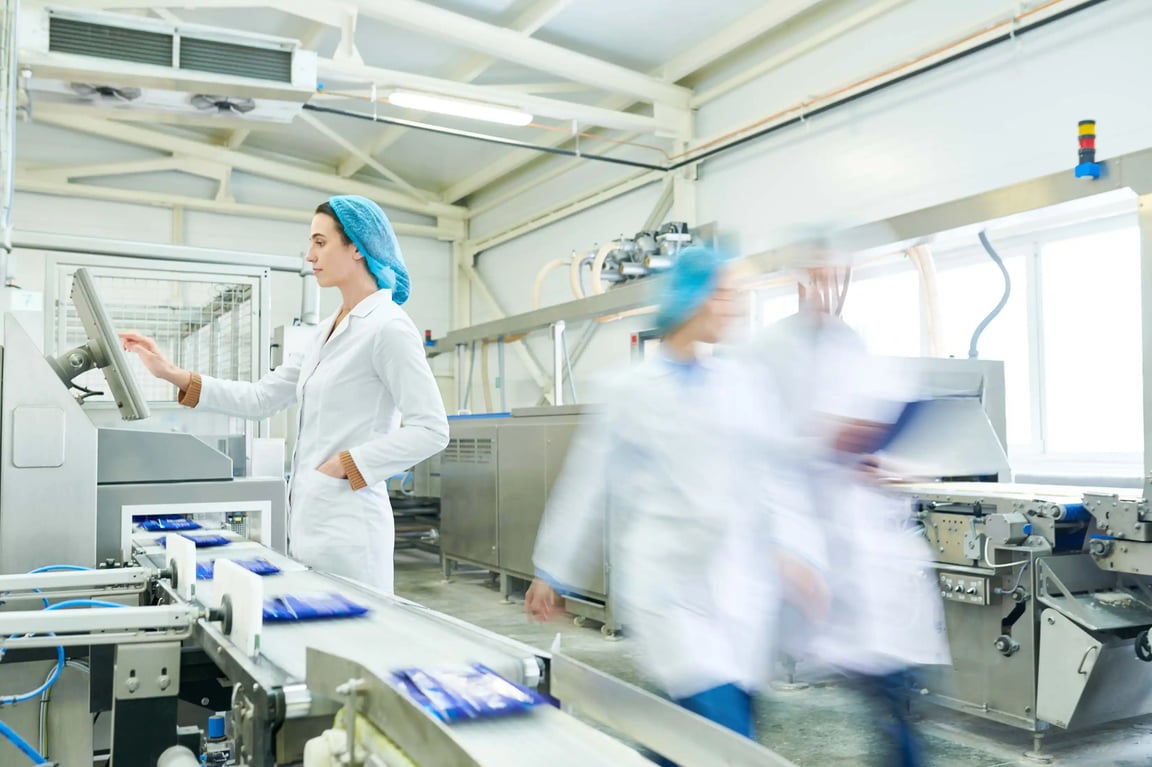
The (Re)evolution of the food packaging process
Goods and products must be protected and preserved if they are to get from where they are produced to where they are used without being damaged. And while modern packaging does a remarkable job at safeguarding contents, smart companies are now understanding that how you handle the food packaging process is just as important.
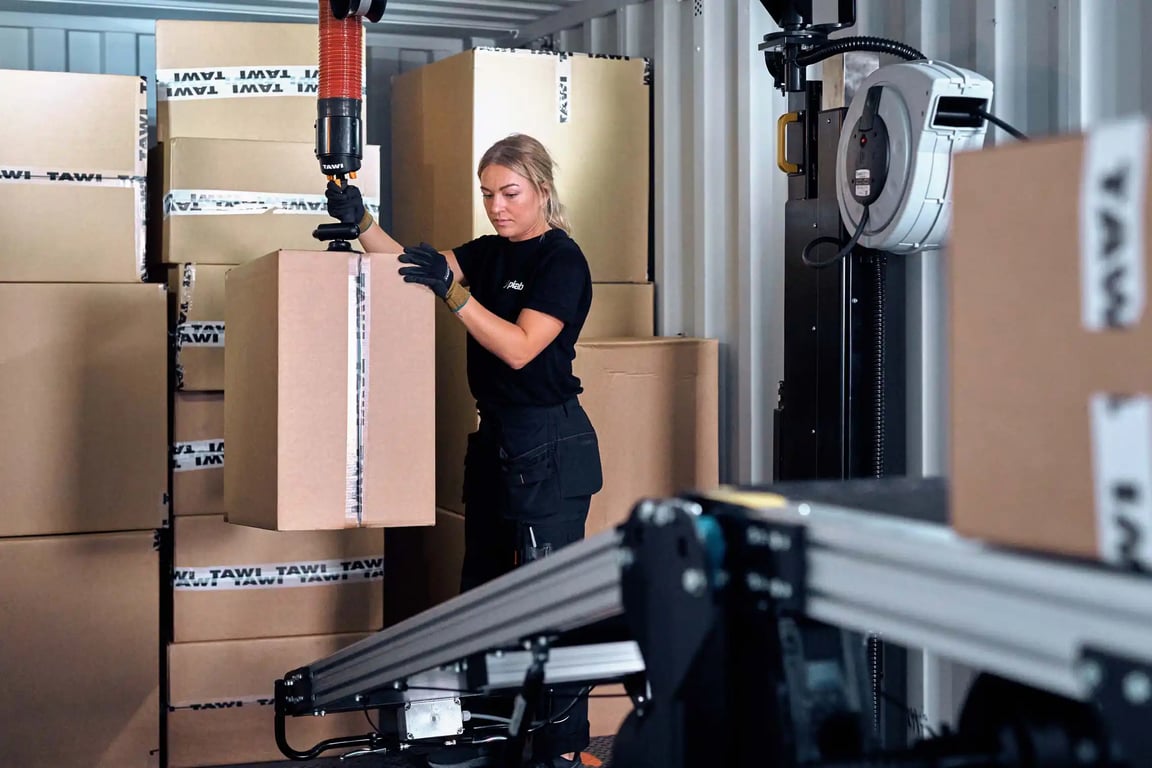
Container Unloading Equipment in 2024: A Comparative Analysis of The Best Technical Solutions
In 2022, global parcel shipping volume amounted to over 161 billion parcels. This volume is expected to skyrocket to 256 billion parcels by 2027, growing at a compound annual growth rate of 59%. Whilst the prospect of industry growth may be appealing, the reality for individual companies is often quite different.
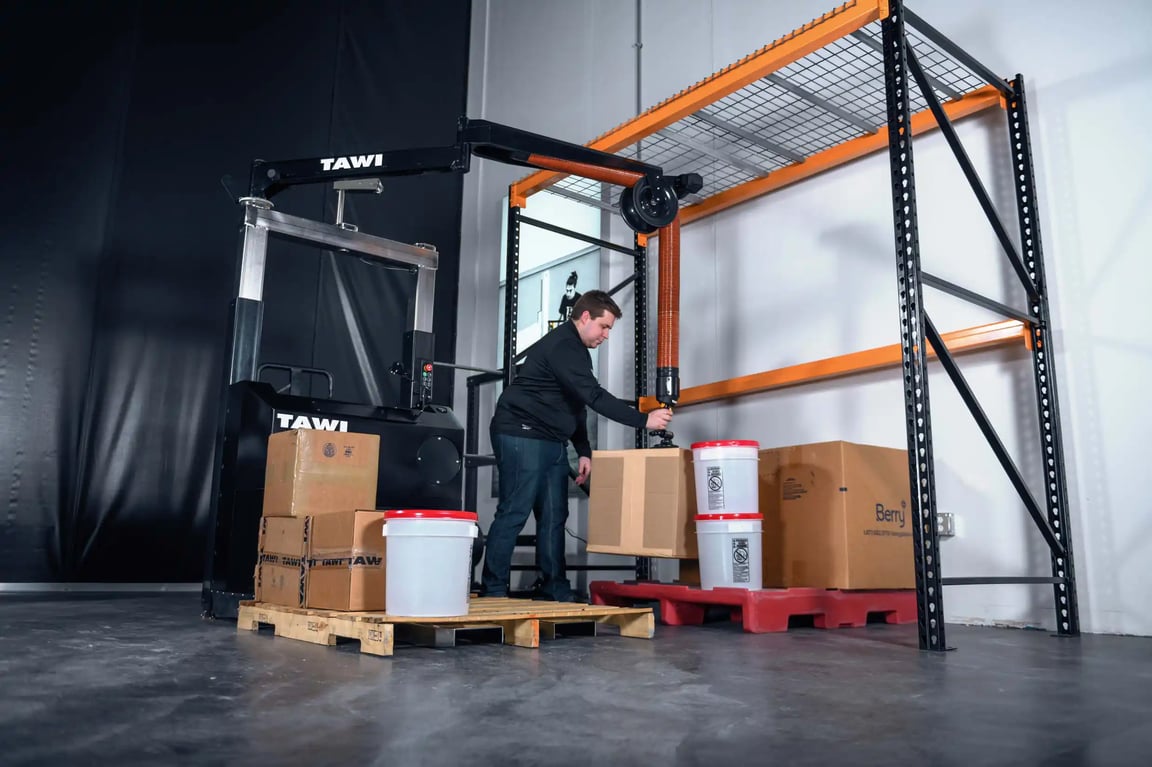
Comparing the best order picker & LLOP products on the market
In the logistics sector, selecting the correct order picker and Low Level Order Picker is essential to achieve maximum efficiency and productivity. The global market offers a range of order pickers to suit different operational needs.
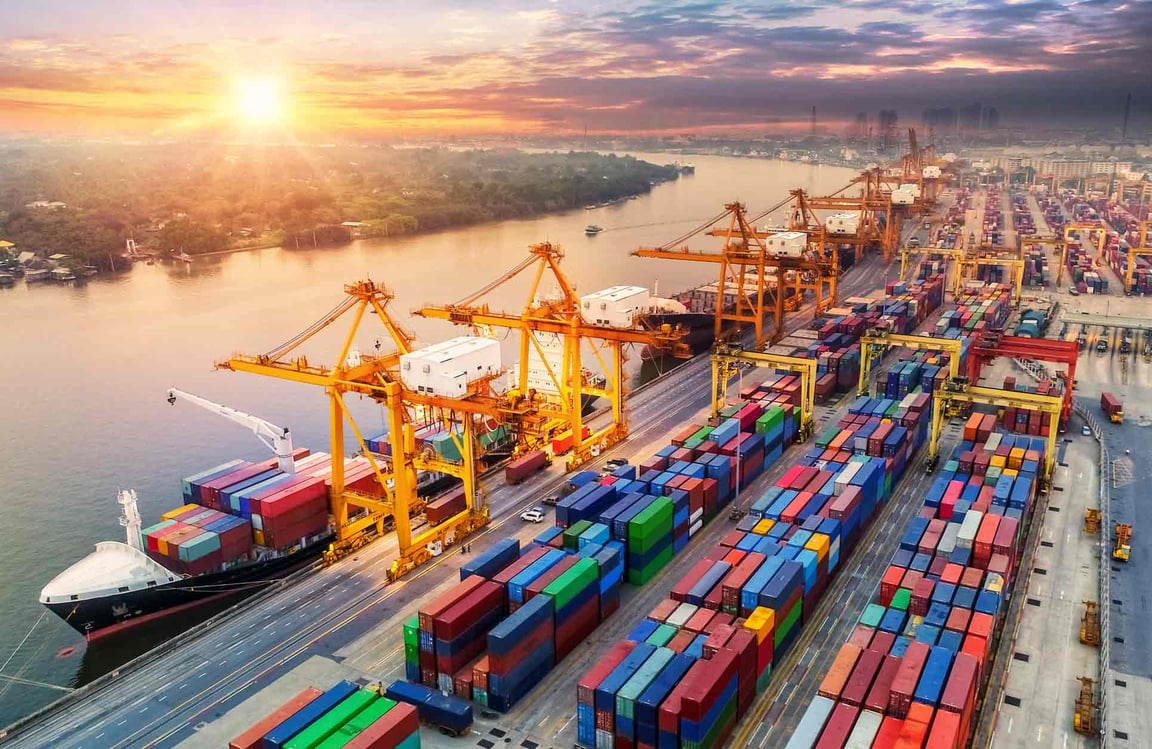
Top logistics trends in 2024
The logistics industry is constantly changing and adapting to the rapid growth of technology and the need to conserve the environment. For any business to stay ahead of the curve and remain competitive in these times, it must be flexible enough to accommodate the latest technological advancements, new processes, and strategies to succeed. Logistics technology will continue to expand and grow, making the logistics industry more agile and reliable. Here are some top trends to watch in 2024 that will shape the future of the logistics industry.
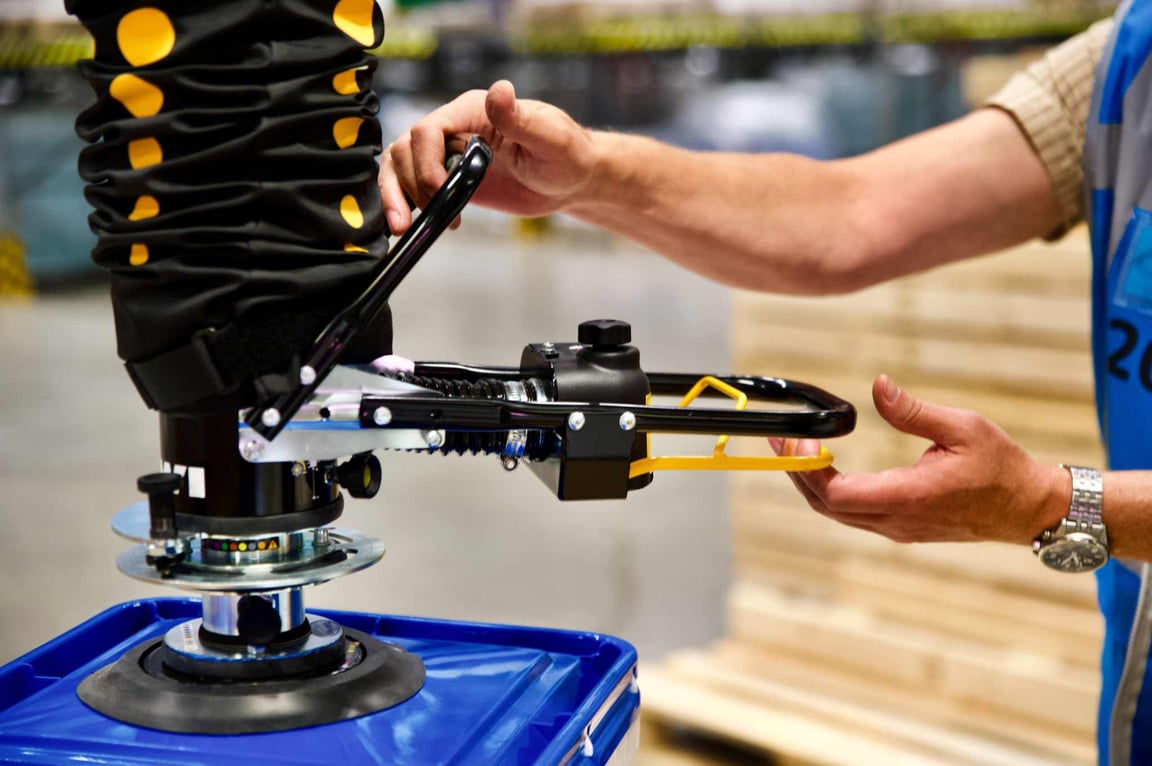
What to consider when choosing lifting tools for your vacuum lifter
The vacuum lifter is an excellent lifting aid that makes material handling safe, efficient and easy. But to get maximum functionality out of your vacuum lifter, it must be equipped with the right lifting tool. This not only enables you to lift your goods in the best possible way, but if you also have several different tools, you also make it possible to handle even more types of goods in your business. But how do you know which lifting tool is right for your goods?
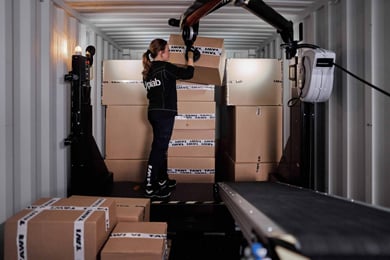
Efficient Loading and Unloading
Well-organized loading and unloading are key to an efficient logistic process. Taking a step towards automation in your manual handling processes is an essential strategy to make your logistic workforce more efficient.
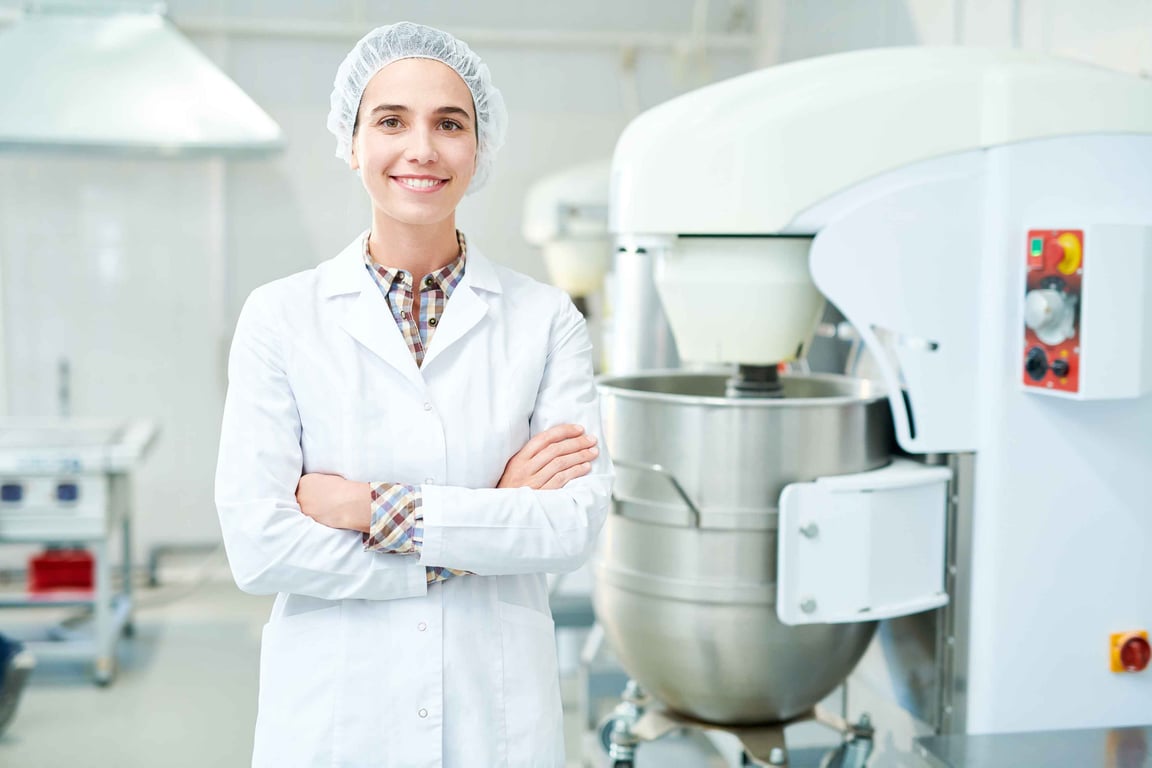
Creating optimal health & safety in the food and beverage industry
Safe lifting and handling is an integral part of the food and beverage industry. Unfortunately, this tends to be a key source of injuries in the workplace. Implementing a healthy and safe procedure in your facility goes far past meeting government standards and laws, as it has a major impact on your business. TAWI has years of experience with helping companies in the food and beverage industry make their procedures as ergonomic, safe, and sanitary as possible, as well as improving the health of both the employees and the operations in the process.
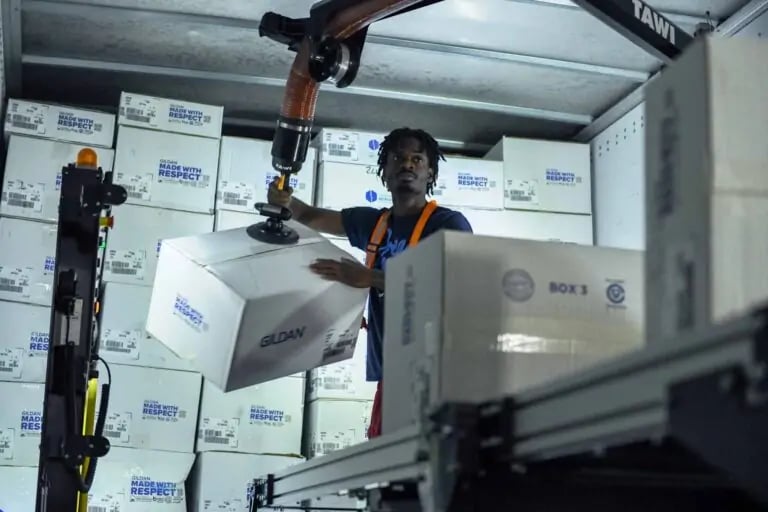
5 Steps to improve operational efficiency in logistics
At TAWI, we offer expert guidance rooted in our industry insights and our vacuum lifters. These lifters, capable of handling a wide variety of goods without causing any damage, have consistently demonstrated greater performance compared to manual handling.
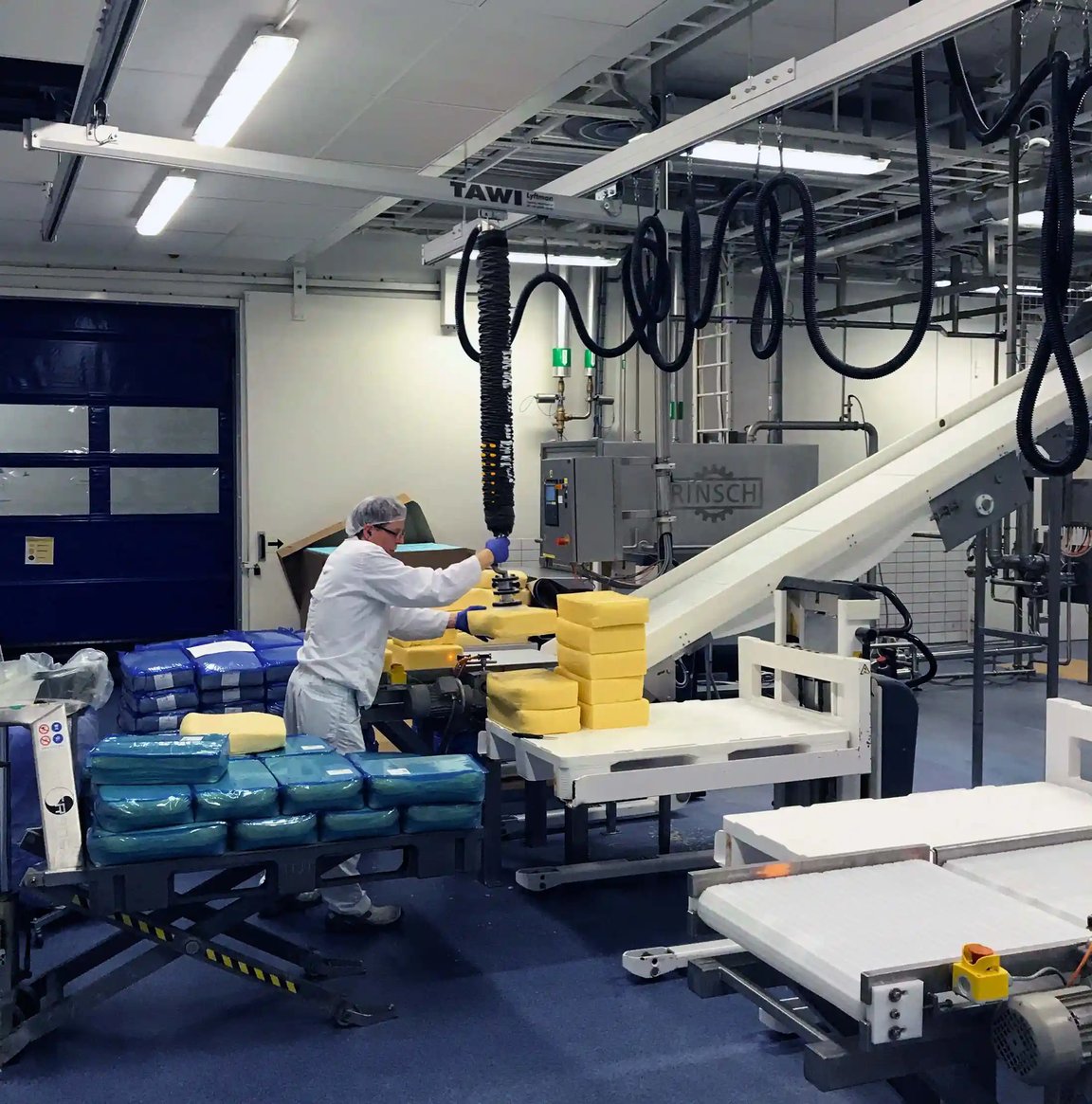
Helping food manufacturers keep up with demands
Food and Beverage plant operators know better than most the importance of marginal gains and precise optimizations. While most businesses downsized during the COVID19 crisis, the food and beverage industry continued to operate at full-scale production.
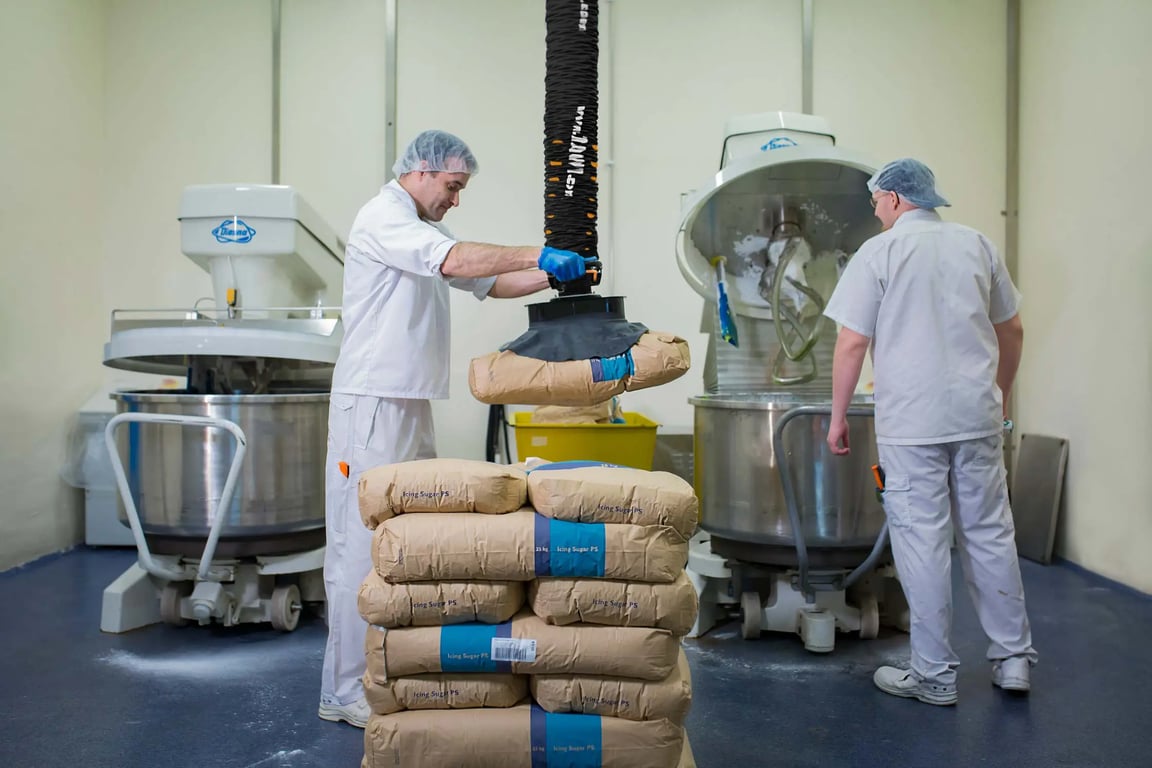
Is vacuum lifting even right for my food & beverage business?
“As an industry, companies are in deep need of modernizing, but they tend to be woefully underinvested in technology [...] unlike B2C, these B2B organizations are battling legacy architecture, a mishmash of processes that hamper attempts to drive profitable growth” - Howard Doberman, Global Operations Transformation Leader, Deloitte.
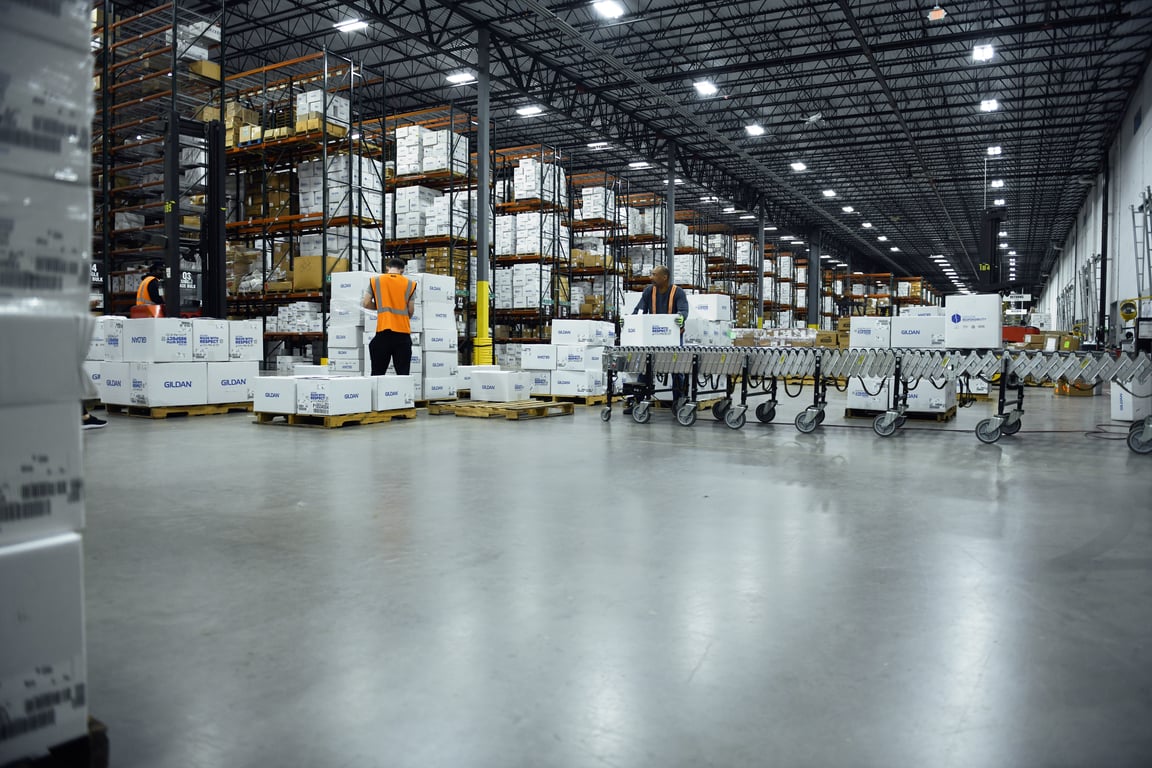
The Biggest Logistical Issues in 2025
The logistics sector is becoming increasingly intertwined with the economics, politics and environmental state of the world. These challenges faced by this industry are not merely logistical but are reflective of broader societal trends and shifts.
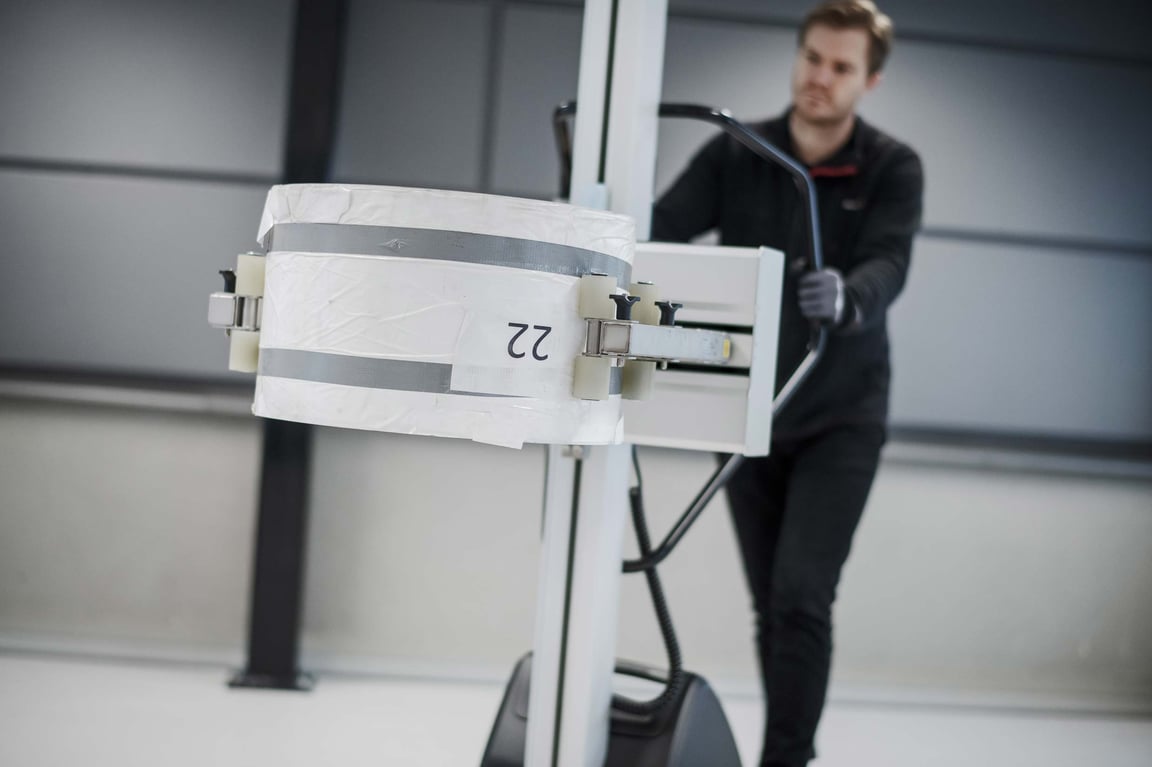
Pick and move reels from pallets with smart reel lifting equipment
Depending on how reels need to be picked up from pallets and then placed for further use, a various amount of lifting solutions can be used. Investing in reel lifting equipment optimized for your workflow significantly reduces work-related injuries and boosts efficiency and workforce flexibility.
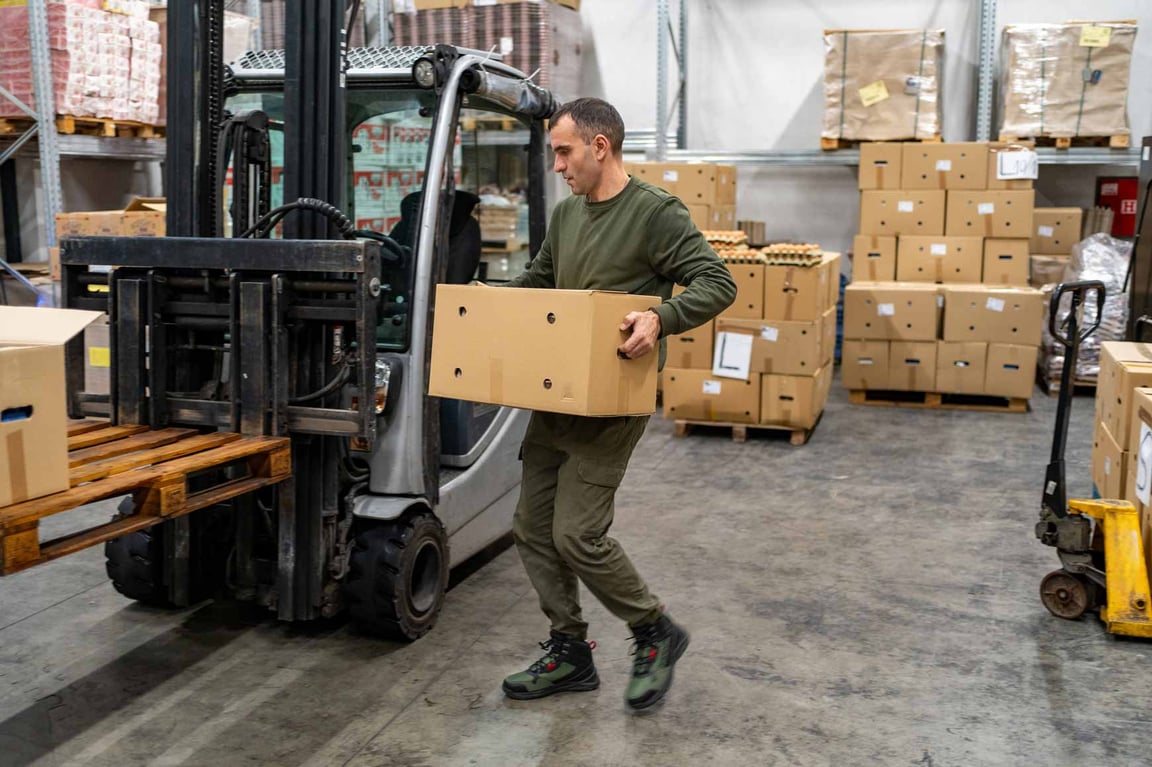
Is warehouse safety at odds with productivity & efficiency?
Contrary to popular belief, safety, productivity, and efficiency are not mutually exclusive in warehouse operations. In fact, they can coexist and mutually enhance each other. But how is this achieved?
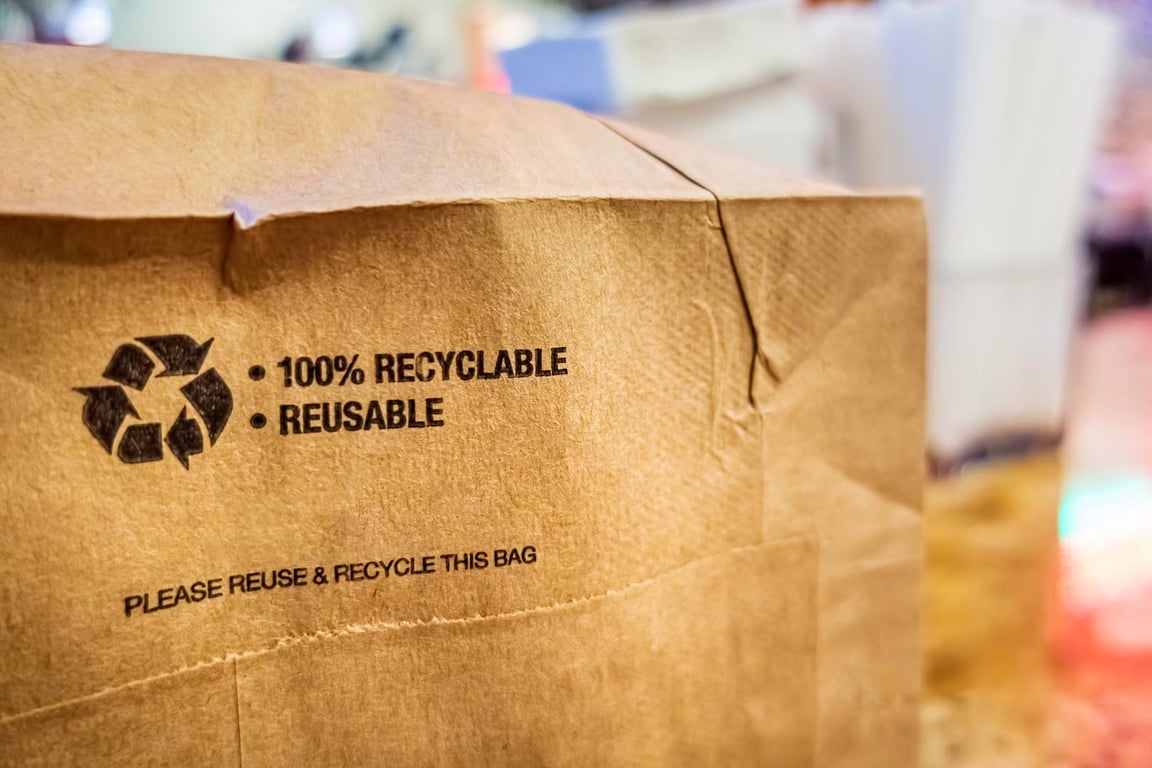
Trends in packaging materials - Will it lift?
Packaging materials are a vital component of modern logistics, not only protecting products during transportation and storage but also reflecting the brand image of businesses. This has led to a significant evolution in packaging materials, driven by technological advancements, changing consumer preferences and sustainability concerns.