How to Measure Vacuum: Methods, Units and Scales
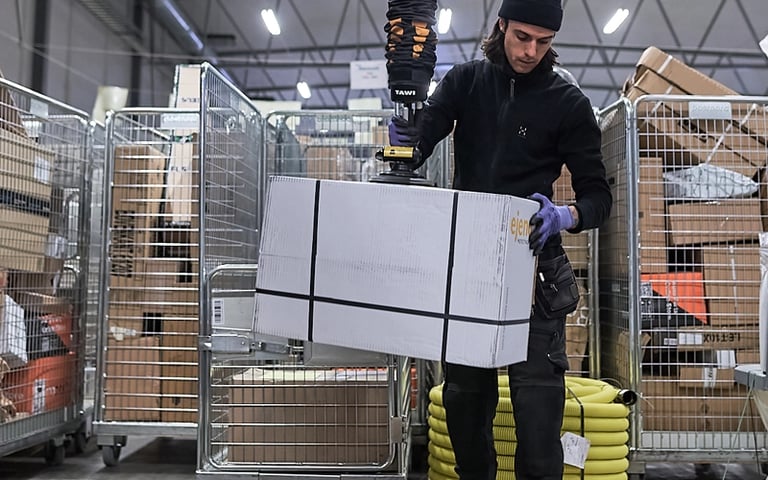
Measuring a vacuum essentially means putting a number on the absence of something. More precisely, what is measured is the amount of negative pressure in a volume of space caused by an absence of air relative to the atmosphere. Unfortunately, there is no universal vacuum unit of measurement. Depending on the level of vacuum needed in a specific application, it is often necessary to use different scales, units and gauges.
A Brief History of Vacuum Measurement
A key event in the history of vacuum technology was an experiment performed by Italian physicist Andrea Torricelli in 1643. Torricelli filled a glass tube about 1 m in length with mercury. He then plugged one end of the tube and inverted it, placing the open end in a basin of mercury.
When removing the plug, the mercury would eventually come to rest at about 760 mm (30 inches) above the surface of the basin – regardless of the height the mercury in the basin or angle of the tube.
This device measures the atmospheric pressure and can be used as a barometer (which Torricelli is credited with inventing). The experiment also demonstrated that the space left above the mercury in the inverted tube was a vacuum.
A few hundred years later, the same technology would come to use in the invention of the vacuum lifter.
Common Vacuum Units and Scales
Millimeters or inches of mercury are still used for measuring pressure in vacuum systems. Millimeters of mercury or mmHg (Hg being mercury in the periodic table of elements) is also a basis for the Torr (after Torricelli) unit of vacuum measurement. 1 Torr equals 1 mmHg and 760 Torr/mmHg equals atmospheric pressure (1 atm). Unlike in the 17th century, however, we can now create vacuums that can be measured in very small fractions of a Torr.
Additional units are used in different parts of the world to measure vacuum pressure. The most common are:
atm – standardized atmospheric pressure, 760 mmHg
PSI – pounds per square inch, absolute (PSIA) or gauge pressure (PSIG)
inHg – inches of mercury
mmHg – millimeters of mercury
Torr – almost but not exactly equal to millimeters of mercury
micron (mTorr) – a millitorr is 1000th of a Torr
kPa – kilopascals, newton-force per square meter
mbar – millibars, bar (kPa x 100) x 1000
In North America, it’s common to use inHg in the rough vacuum range, Torr in higher vacuum ranges, and microns (thousands of a Torr) for pressures reached by backing pumps.
Outside of North America, the more common units are negative millibar and/or kPa (often both are used on gauges). Pascal (as in kilopascal/kPa) is the metric standard unit for pressure and is normally the unit used in scientific and technical papers.
In the so-called rough vacuum range, from atmospheric pressure down to 25 Torr, it is also common (and more practical) to define vacuum as a percentage of a full vacuum. For example, a vacuum lifting system may operate at around 60% of a total vacuum.
Is a Perfect Vacuum Possible?
No. A perfect vacuum, which can also be referred to as full vacuum or absolute vacuum, would be a volume that contains no matter whatsoever. Outer space comes close with just a few hydrogen atoms per cubic meter, but it never reaches zero and the same is true even in the most technically advanced vacuum systems on Earth.
Although a small volume may contain no particles for a very brief moment, there would still be quantum phenomena such as photons. A perfect vacuum is nevertheless an inevitable theoretical reference point that we, for example, use when determining and comparing percentages of vacuum. A perfect vacuum (100%) as measured in all units including PSI, mmHg, Torr, mbar or inHg, is 0.
What is Considered a High Vacuum?
Any negative pressure significantly below standard atmospheric pressure (760 Torr/mmHg, 29.9 inHg or 14.7 PSI) is considered a vacuum. Vacuum quality is subsequently divided into ranges that are somewhat arbitrary but primarily based on the equipment needed to achieve or measure it.
The vacuum range that can be measured in units of mercury (Hg) is called the rough vacuum range. This is where vacuum lifting equipment and numerous other industrial applications operate.
These are the vacuum pressure ranges as measured in Torr (or fractions of 1 Torr).
Atmospheric pressure: 760 Torr
Rough vacuum: 760 to 25 Torr
Medium vacuum: 25 to 1×10-3 Torr
High vacuum: 1×10-3 to 1×10-9 Torr
Ultra-high vacuum: 1×10-9 to 1×10-12 torr
Extremely high vacuum: Less than 1×10-12 Torr
What defines a high vacuum is then that it is normally placed in the range between 1×10-3 to 1×10-9 Torr, equaling one thousandth (0.001) of a Torr (or 1 micron) down to one billionth (0.000000001) of a Torr. Another delimiting factor is that it usually requires multi-stage pumping and is measured using an ionization gauge.
Vacuum Measuring Gauges
In vacuum handling technology and other applications that operate in the rough vacuum range, the vacuum level is typically measured using direct-reading gauges. Direct-reading gauges can provide an accurate measurement from atmospheric pressure down to about 1 Torr and in some cases lower. Such technologies include u-tube manometers, capacitance manometers and Bourdon tubes.
U-tube manometers: One of the most basic devices for measuring pressure and vacuum is the u-tube manometer. It is shaped as a U and when a vacuum is applied to one leg, the liquid in the tube rises in that leg and falls in the other.
Capacitance manometers: A capacitance manometer gauge is a considerably more complex and accurate form of manometer. It uses a tensioned diaphragm with one side being exposed to the volume that is to be measured. The other side contains an electrode assembly with a reference electrode and a pressure-sensing electrode. As the diaphragm deflects relative to the pressure it causes a capacitance change, which is sensed and ultimately converted to an exact measurement.
Bourdon-tube vacuum gauges: The most common pressure gauge by far is the Bourdon-tube gauge. This relatively simple but precise mechanical instrument has been in use since the 19th century and is still extensively used. It is highly useful in a wide variety of applications, including installation and troubleshooting of industrial vacuum systems.
The Bourdon tube itself is a tube bent into an arc connected to the vacuum system. It will bend more or less from the pressure relative to the atmosphere, which actuates the attached dial via a set of gears and springs.
Measuring a Vacuum Lifting System
A vacuum lifting system works in the rough vacuum range, making it comparatively easy to measure the vacuum level using conventional gauges. Depending on the measurement’s purpose – such as installing, adjusting or detecting leaks – the starting point is to attach a manometer to the applicable part of the system. In the case of TAWI vacuum systems, we know the exact capacity of our vacuum pumps and measuring the vacuum level is only needed in specific circumstances.
Vacuum System Troubleshooting
Issues with poor lifting capacity are normally caused by leaks in the system, which can be located by measuring the vacuum level in different parts of the system. The initial measuring method is to place a manometer attached to a test plate over the suction feet area. This will simulate a load and that should be able to reach the vacuum pump’s capacity.
A vacuum lifting system is never 100% sealed, but if the vacuum level does not reach 55–60% (of theoretical absolute vacuum), this indicates a leak. It is then possible to measure at several positions along the route between suction feet and pump to identify the leak’s location.
Adjusting for Porous Loads
When reaching the pump’s capacity at the suction feet, it is also possible that the leak is the load itself, which causes a loss of negative pressure. A solution is to increase the pump capacity – not in terms of what vacuum level the pump can reach, but in terms of the flow that the pump is capable of evacuating.
Porous loads require higher-capacity pumps to evacuate air compared to flat, non-porous loads. This is why it’s possible to use a small vacuum pump with a flow of 4m3/h (141 ft³/h) hanging from a chain hoist to lift steel plates weighing as much as 1.5 tons (3,300 lbs.).
At the other end of the scale, you may need a 3kW pump providing a flow of 230 m3/h (8,133 ft3/h) when lifting a 25kg (55 lbs.) bag of flour or a porous plywood sheet.
In other words, many considerations go into selecting the right type of vacuum system for a specific application. To ensure the safety of the system, the required lifting capacity is also multiplied by a factor of two.
Learn more
Here’s a great introduction to vacuum technology
This article will guide you to safe lifting using vacuum technology.
Here you can learn more about working efficiently with vacuum lift systems.
Have you read enough? Get in touch to talk to a TAWI representative.