Optimal sortering og palletering på lager og distribution
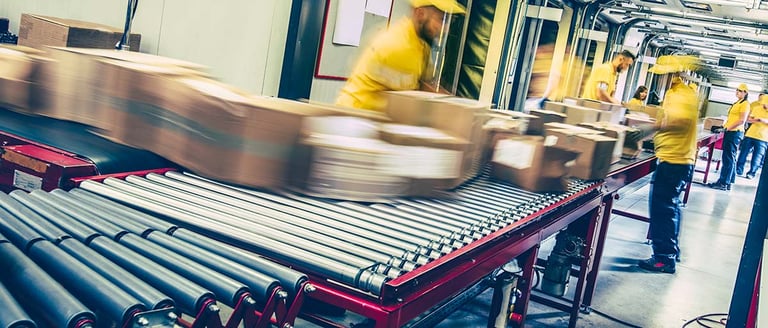
Efter Covid-perioden er betydningen af lagersortering og palletering vokset eksponentielt på grund af stigningen i online shopping og den efterfølgende øgede efterspørgsel på godstransport. Den hurtige arbejdsrytme kan dog udgøre risici for medarbejdernes sundhed og sikkerhed, hvilket kan føre til udbrændthed og høj personaleomsætning.
For at imødekomme disse udfordringer er det afgørende at udforske automatiserede løsninger, der forbedrer effektiviteten og aflaster presset på medarbejderne.
Covid-pandemiens indvirkning på lagerdrift
Uanset om du søger viden i aviser, magasiner om teknik eller på websteder om logistik, vil du sandsynligvis finde ud af, at coronapandemien har været god for virksomheder, der beskæftiger sig med at levere varer til kunder. Disse virksomheder har oplevet, at efterspørgslen er steget til det dobbelte, tredobbelte eller endda til det tidobbelte af deres tidligere efterspørgsel, eftersom de leverer til mennesker, som handler online hjemmefra.
For driftschefer på lagre har dette skabt et presserende behov for medarbejdere, som er villige til at udføre repetitivt, fysisk arbejde såsom læsning, losning og sortering af kasser, sække, tønder og pakker i alle mulige vægt- og størrelsesklasser. Det kræver ofte to personer at løfte tungt gods, mens lettere pakker skal flyttes hurtigt og ofte. Med de nye udfordringer efter pandemien må vi stille os spørgsmålet: Kan vi gøre det anderledes? Hvis vi kan, hvordan skal vi så gøre det?
Sortering og palletering på lagre er farligt arbejde
Lastbiler og containere bliver bare ved med at komme trillende ind med produkter, der er stablet højt på paller. Så du er nødt til at arbejde hurtigt på en smart måde. Du har typisk tre eller fire timer til at losse en container, så flere lagermedarbejdere klatrer ind i den, og du ruller en rullecontainer, en palle eller en båndtransportør hen til den. Når godset er ude af containeren, skal disse medarbejdere sortere og fordele det på adskillige paller, så de kan indlagres og senere plukkes til afsendelse til slutkunden.
Disse grundlæggende ordregennemførelsesprocesser er stadig i stor udstrækning manuelle. Til dels fordi de kræver en kompleks kombination af bevægelser. Du skal manøvrere pallerne og løfte, placere, sortere og scanne en lang række produkter, som er pakket forskelligt. Derefter skal du placere disse produkter på reoler og plukke dem igen, sætte dem endeligt på plads og flytte dem til afsendelse med lastbiler. Et enkelt emne løftes ofte flere gange.
Anders Knapasjö, Vice President for Norden, Baltikum og Tyskland hos Piab Lifting Automation Division og ekspert inden for højfrekvente løft, understreger den langsigtede påvirkning af fysisk anstrengelse på arbejdstagere. Uanset vægten af varerne, så påvirker de gentagne bevægelser, der er forbundet med lagerarbejde kroppen og udsætter logistikmedarbejdere for en øget risiko for arbejdsulykker.
“Dette vil påvirke din krop over tid. På kort sigt bemærker du det måske ikke. Men du lægger mærke til det, når du kommer hjem, sætter dig ned til middag, så mærker du trætheden. Forestil dig, hvad folk, der har gjort dette i 10 eller 20 år, oplever."
Det er ikke så mærkeligt, siger Anders, at arbejdsulykker i logistiksektoren er så høje. "Dette skyldes, at folk løfter objekter hundrede, hvis ikke tusindvis af gange om dagen, typisk bøjer sig og drejer sig, mens de gør det, ofte i ubehagelige positioner. Selv hvis det er lettere objekter, påvirker det uundgåeligt kroppen."
Nye udfordringer for lagerdriften
Det stigende arbejdstempo på lagre efter corona medfører eventuelt nye sundheds- og sikkerhedsfarer samt øget personaleomsætning grundet overarbejde og udbrændthed. I øjeblikket oplever lagermedarbejdere i USA f.eks., at antallet af arbejdsskader ligger på et niveau, der er dobbelt så højt som hos andre medarbejdere i den private sektor. Muskel- og knoglelidelser forårsaget af manuel palletering udgør mere end en tredjedel af alle mistede arbejdsdage, hvilket beløber sig til en anslået omkostning på 20 milliarder dollars pr. år i arbejdsskadeforsikring – et forbløffende beløb. Gravide medarbejdere på et lager i Memphis administreret af 3PL XPO fik afvist deres anmodninger om at udføre lettere arbejde aborterede efterfølgende spontant. Lagermedarbejdere arbejder ofte hårdt i lagerfaciliteter uden aircondition, hvilket øger faren forbundet med at arbejde i et højere arbejdstempo.
Omkostninger forbundet med personskader på lagre:
- Lagermedarbejdere i USA pådrager sig dobbelt så mange arbejdsrelaterede skader som gennemsnittet
- Det er en højere personskadefrekvens end inden for minedrift og bygge og anlæg
- Skader forårsaget af manuel palletering er skyld i 34 % af alle mistede arbejdsdage
- Den estimerede omkostning er 20 milliarder dollars om året i arbejdsskadeforsikri
Menneske eller maskine til sortering og palletering på lagre?
Automation fremstår som en gennemførlig løsning for at afbøde de udfordringer, der påvirker lagerdrift. Selvom introduktion af robotteknologi kan virke kompleks og kræve betydelige investeringer i omstrukturering af forretningsprocesser, opkvalificering af medarbejdere og organisatorisk transformation, vejer de langsigtede fordele tungt i forhold til de oprindelige tilbageslag i produktivitet og præstation.
Det er vigtigt at erkende, at mennesker fortsat er uundværlige for at opnå optimale forretningsresultater. at mennesker fortsat er uundværlige for at opnå optimale forretningsresultater. En kombination af maskiner og menneskelig ekspertise fører til betydelige gevinster i effektivitet og problemløsningsevner. Lagerdriftsledere søger "plug and play"-løsninger – maskiner, der er kompakte, brugervenlige og nemt kan tilpasses skiftende opgaver og arbejdsprocesser.
Beregning af investeringsafkastet fra sorterings- og palleteringsteknik på lagre
Ethvert automatiseringsprojekt som er mere end almindeligt kompliceret – som tager mere tid, kræver mere plads og ekspertise, flere dele – afvises på stedet, fordi det ville stække bestræbelserne på at imødekomme den hurtigt voksende efterspørgsel. Plug and play-systemer tilbyder for hver aktivitetskategori, uanset om det er flytning, sortering, vending, placering eller plukning af gods, et langt større investeringsafkast end store, specialkonstruerede installationer.
Højfrekvent løfteteknologi, såsom vakuumløft, har vist sit potentiale i at reducere skader og øge produktiviteten. For eksempel implementerede TNT (nu FedEx) i Sverige med succes vakuumløfteteknologi for at reducere skader blandt medarbejdere og opretholde eller øge produktiviteten under sorterings- og palleteringsprocessen. Implementeringen af vakuumløfteteknologi førte til en reduktion af skader med mere end 40%, mens produktiviteten forblev uændret.
Vigtigheden af hastighed og ergonomi
For pakker, der flyttes fra et transportbånd og over på paller eller ind i rullecontainere, gælder det generelt, at manuel håndtering vil være hurtigere end med mekanisk hjælp i cirka den første time. Men når man når til den tredje time, vil hastigheden for begge metoder være den samme. Efter tre til fire timer vil maskinen hver gang være hurtigere end mennesket, fordi den ikke finder det anstrengende at løfte og aldrig bliver træt.
Høkfrekvente vakuumløftere, såsom dem, der tilbydes af TAWI, giver en betydelig fordel i optimering af lager sortering og palleteringsoperationer. Disse løftere er designet til at efterligne den måde, en person arbejder manuelt på, og tilbyder højhastigheds håndtering af pakker, én-hånds løft med et brugervenligt joystick-håndtag, hurtig frigivelse for tidsbesparelse og evnen til at rotere pakker 360°. Ved at integrere moderne teknologi som højfrekvente vakuumløftere kan lagre markant forbedre effektiviteten og give medarbejderne langvarige ergonomiske arbejdsvilkår.
“Vi har et avanceret værktøj til beregning af investeringsafkastet for vores kunder, hvor vi indregner alle fakta om de udfordringer, de står overfor, deres medarbejdere, deres pakkerater osv., så vi kan sammenregne omkostningerne og holde dem op mod investeringen,” siger Anders. “Men sædvanligvis ses afkastet på investeringen efter seks til syv måneder. Det er her, det bliver interessant for dem.”
Konklusion
Optimering af lager sortering og palleteringsoperationer er afgørende for effektiv ordreafvikling, at minimere skader og forbedre medarbejdernes trivsel. Ved at tage automatiseringsløsninger i brug, såsom højfrekvente vakuumløftere, kan lagre reducere fysisk belastning, øge produktiviteten og opnå en hurtigere returnering på investeringen. Det er tydeligt, at en kombination af avanceret teknologi og menneskelig ekspertise er nøglen til succes i det udviklende landskab af post-Covid lagerdrift.
En plug-and-play-løsning til lager sortering og palletering
Jollyroom er den største e-handelsvirksomhed for børne- og babyprodukter i Norden. Ligesom mange e-handelsvirksomheder har de seneste år medført nye logistiske udfordringer for virksomheden, herunder forsendelsesforsinkelser, vanskeligheder med at planlægge lagerbeholdning og øgede kundekrav. Derfor besluttede Jollyroom, at de måtte se på mulige løfteløsninger til håndtering af de tunge og voluminøse varer. Prioriteten var at minimere sygefravær og skabe bedre ergonomiske forhold for deres medarbejdere. Vakuumløfteløsninger fra TAWI opfyldte kravene og er blevet særligt værdsat på grund af, hvor lette de er at betjene.
"Det samme arbejde kræver færre personer, når man bruger TAWI-løftere. I stedet for at have to personer til at løfte en tung genstand, kan én person bruge vakuumløfteren og klare det selv," siger Niklas Blomberg, virksomhedens projektleder for logistik i Göteborg.
Dette gør sorteringsprocessen mere tids- og omkostningseffektiv, men vigtigst af alt gør det løft af varer op til 70 kg uden besværs, hvilket sikrer, at medarbejderne får langvarige ergonomiske arbejdsvilkår. Læs hele casen her.