Optimale Sortierung und Palettierung in Lager und Vertrieb
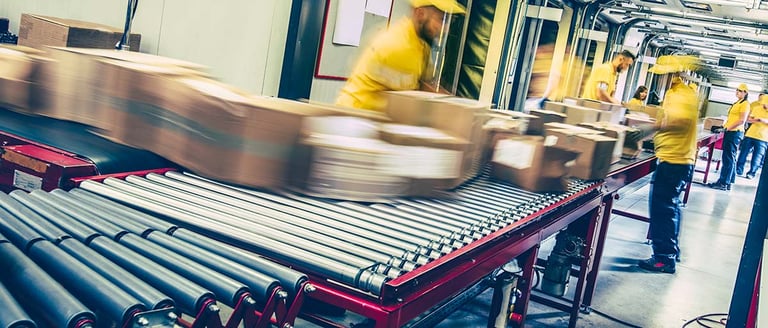
Das zunehmende Arbeitstempo beim Sortieren und Palettieren in den Lagern nach Covid-19 kann zu neuen Risiken für die Gesundheit und Sicherheit sowie zu einer erhöhten Fluktuation der Mitarbeiter aufgrund von Überlastung und Überarbeitung führen. Der Strom der Lastwagen und Container mit den auf Paletten gestapelten Produkten reißt nicht ab. Man muss also schnell und intelligent arbeiten. Aber können die Sortierung und Palettierung im Lager automatisiert werden, und falls ja, in welchem Ausmaß und zu welchen Kosten?
Egal, ob Sie sich in Zeitungen, Technikmagazinen oder auf Logistik-Websites informieren. Häufig werden Sie von produzierenden Unternehmen, Logistik- und Transportunternehmen erfahren, dass trotz der Coronavirus-Pandemie der Umsatz und Gewinn gestiegen ist. Die Nachfrage hat sich verdoppelt, verdreifacht oder sogar verzehnfacht, da die Kunden beim E-Shopping oder im Home-Office von zu Hause aus bestellt haben.
Für Lagerverwalter bedeutet dies, dass dringend Arbeitskräfte benötigt werden, die in der Lage sind sich wiederholende körperliche Arbeit zu verrichten. Kisten, Säcke, Fässer und Pakete jeden Gewichts und jeder Größe müssen beladen, entladen und sortiert werden. Schwerere Güter müssen oft von zwei Personen gehoben werden, während leichtere Pakete mit hoher Geschwindigkeit und Häufigkeit bewegt werden. Die neuen Herausforderungen der Post-Pandemie-Ära werfen die Frage auf: Können wir das anders handhaben? Und wenn ja, wie?
Enormer Zeitdruck, ein hohes Arbeitsaufkommen und bedrohliche Personalknappheit sind keine idealen Voraussetzungen, um Arbeitsprozesse und -abläufe zu verändern oder herum zu experimentieren. Aber es gibt intelligentere Lösungen, die mit minimalen Unterbrechungen in den Arbeitsprozessen und überraschenden Wettbewerbsvorteilen einen großen Unterschied im Betriebsablauf machen.
Lagersortierung und Palettieren ist eine gefährliche Arbeit
Die Lastwagen und Container mit den palettierten Produkten rollen unaufhörlich an. Du musst also schnell und einfallsreich arbeiten. Für das Entladen eines Containers hat man in der Regel drei oder vier Stunden Zeit, also klettern mehrere Leute hinein und bewegen einen Käfig, eine Palette oder ein Förderband dorthin. Sobald die Waren aus dem Container herausgeholt worden sind, müssen die Arbeiter sie sortieren und auf noch mehr Paletten verteilen, damit sie systematisch eingelagert und später für den Versand an den Endkunden abgerufen werden können.
Diese grundlegenden Prozesse in der Warenannahme werden noch weitgehend manuell gehandhabt, teilweise weil sie komplexe Bewegungsabläufe erfordern. Paletten müssen bewegt werden, eine Vielzahl von unterschiedlich verpackten Produkten angehoben werden sowie platziert, sortiert und gescannt werden. Anschließend werden diese Produkte in Regale ein- und ausgelagert, in ein endgültiges Lagerhaltungssystem gebracht und in die abgehenden Lastwagen verladen werden. Ein einziger Artikel kann dabei mehrmals angehoben oder bewegt werden.
„Das wirkt sich mit der Zeit auf den Körper aus“, sagt Anders Knapasjö, Vice President Nordic, Baltic & Germany für Piab Lifting Automation Division und ein Experte für Hochfrequenzheben. „Kurzfristig merken Sie es vielleicht nicht. Aber man merkt es, wenn man nach Hause kommt, sich zum Essen hinsetzt und plötzlich spürt man es. Stellen Sie sich vor, was Menschen erleben, die das seit 10 oder 20 Jahren machen.“
Kein Wunder, sagt Anders, dass die Zahl der Arbeitsunfälle in der Logistikbranche so hoch ist. „Das liegt daran, dass die Menschen hunderte, wenn nicht tausende Male am Tag Gegenstände heben und sich dabei in der Regel in einer ungesunden Körperhaltung bücken und drehen. Selbst wenn es sich um leichtere Gegenstände handelt, erfordert dies unweigerlich einen Tribut vom Körper.“
Neue Herausforderungen für den Lagerbetrieb
Das zunehmende Arbeitstempo in Lagerhäusern nach dem Covid-Lockdowns kann zu neuen Gesundheits- und Sicherheitsrisiken sowie zu einer erhöhten Mitarbeiterfluktuation aufgrund von Überlastung und Burnout führen. Derzeit erleiden Lagerarbeiter in den USA beispielsweise eine doppelt so hohe Rate von berufsbedingten Verletzung wie andere Arbeitnehmer in der Privatwirtschaft – diese ist derzeit höher als im Baugewerbe, im Kohlebergbau und in den meisten verarbeitenden Industrien. Muskel-Skelett-Erkrankungen, wie sie beim manuellen Palettieren auftreten, sind verantwortlich fürmehr als ein Drittel aller Krankheitstage bei geschätzten Kosten von 20 Milliarden Dollar pro Jahr für Schadensersatzzahlungen an die Arbeitnehmer – eine erstaunliche Summe. Schwangeren Arbeitnehmerinnen in einem Lagerhaus in Memphis, das von 3PL XPO verwaltet wird, wurden Anträge für das Heben von leichten Lasten verweigert und in der Folge erlitten diese Fehlgeburten. Außerdem arbeiten Lagerarbeiter häufig in nicht klimatisierten Räumen, was das Verletzungsrisiko aufgrund des hohen Arbeitstempos erhöht.
Die Kosten von Arbeitsunfällen im Lager:
- Lagerarbeiter in den USA erleiden doppelt so viele arbeitsbedingte Verletzungen wie der Durchschnitt
- Dies ist eine höhere Verletzungsrate als im Bergbau und im Baugewerbe
- Verletzungen durch das manuelle Stappen von Paletten verursachen 34 % aller verlorenen Arbeitstage
- Die geschätzten Kosten an Entschädigungszahlungen belaufen sich auf 20 Milliarden Dollar pro Jahr.
Mensch oder Maschine für die Lagersortierung und Palettierung?
Es ist offensichtlich, dass diese Knochenarbeit teilweise oder ganz von einer Maschine erledigt wird. Aber können Sortierung und Palettierung automatisiert werden, und wenn ja, in welchem Umfang und zu welchen Kosten? Die Einführung von Robotertechnik ist ein komplexer Prozess, und die meisten Unternehmen – selbst die großen – sind nicht in der Lage, diese fortschrittlichen Systeme zu implementieren und eine erfolgreiche Integration ist selten. Grundlegende neue Technologien erfordern meist kostspielige Investitionen in die Umstrukturierung von Geschäftsprozessen, die Weiterqualifizierung von Mitarbeitern und die organisatorische Transformation. Irgendwann werden sich die Investitionen letztendlich lohnen, aber die Produktivität und Leistung wird zumindest kurzfristig darunter leiden.
Aus diesem Grund sind gute Arbeitskräfte für positive Unternehmensergebnisse nach wie vor unverzichtbar. Es sind Menschen, die schnell Probleme lösen, mit Ausnahmefällen umgehen und Verbesserungsmaßnahmen ergreifen. Die Kombination von Mensch und Maschine können die Gewinne meist deutlich steigern. Manager, die sich auf die Kombination von Menschen und neue Technologien fokussieren sind schneller in der Lage, einen reibungslosen Betriebsablauf zu garantieren und die Vorteile der Automatisierung zu nutzen. Manager für die Lagerhaltung suchen daher nach „Plug and Play“-Lösungen: Maschinen, die nicht zu groß oder schwerfällig sind, die sich in der Praxis bewährt haben, die benutzerfreundlich und ergonomisch für die Bediener sind, die leicht einzurichten sind und die sich bei veränderten Aufgaben leicht umkonfigurieren lassen.
Berechnung des ROI für Sortierung und Palettierung in Lagerhäusern
Jedes kompliziertere Automatisierungsprojekt, welches mehr Zeit, mehr Platz, mehr Fachwissen und mehr Bauteile erfordert, wird strikt abgelehnt, da es die steigenden Nachfrage bremsen würde. Für jede Handlungskategorie, sei es das Bewegen, Sortieren, Ausrichten, Verstauen oder Auslagern von Gütern, bieten betriebsbereite Systeme eine weitaus höhere Rentabilität als groß angelegte, kundenspezifische Installationen.
Die gängige Meinung ist heutzutage, dass die Automatisierung Großunternehmen begünstigt, die im Geld schwimmen. Die Erfahrung zeigt jedoch, dass dies nicht der Fall ist. Die Anlagenrendite (ROI) für Maschinen, die den Sortier- und Palettiervorgang unterstützen, lässt sich einigermaßen genau berechnen.
Optimieren Sie Ihre Sortierung und Palettierung im Lager durch Vakuumhebern mit hoher Arbeitsfrequenz
Vakuumheber mit hoher Förderleistung sind so konzipiert, dass sie die manuelle Arbeit eines Menschen nachahmen. Ein Standard-Vakuumheber muss mit beiden Händen bis zur Palette gezogen werden, und man muss warten, bis das Vakuum abgebaut ist, was ein oder zwei Sekunden dauert. Das Hochleistungs-Hebegerät verfügt über eine Taste zur schnellen Freigabe, die es dem Bediener ermöglicht, ein Paket fallen zu lassen, noch bevor es die Palette erreicht. Wenn Sie so mit einer statt zwei Personen sortieren und palettieren können, sind die Kosteneinsparungen offensichtlich. Und wenn Sie eine große Vielfalt an Arbeitnehmern für diese Aufgabe einstellen können, anstatt nur sportliche junge Leute, verschwinden Ihre Personalprobleme über Nacht.
“ Mit Hilfe dieser modernen Technologie können Sie bis zu Ihrem 83. Lebensjahr heben und Ihr Rücken bleibt gesund,” sagt Anders.
Mit dem Hochgeschwindigkeits-Heber können Sie zum Beispiel mit nur einer Hand schnell und einfach greifen und anheben, während der Saugfuß die meisten Arten von verpackten Waren halten kann. Diese Technologie bietet:
- Das Handling von Paketen mit hohen Geschwindigkeiten
- Das Heben von Fässern, Gepäck, Lebensmitteln und mehr
- Greifen Sie von oben oder von der Seite
- Einhändiges Heben mit benutzerfreundlichem Joystick-Griff
- Zeitsparende Schnellauslösung
- Maßgeschneiderte Saugfüße für unterschiedliche Verpackungen
- Pakete um 360° drehen
Eine Plug and Play-Lösung für die Sortierung und Palettierung im Lager
Jollyroom ist das größte E-Commerce-Unternehmen für Kinder- und Babyartikel in Nordeuropa. Wie bei vielen E-Commerce-Unternehmen haben sich in den letzten Jahren neue Herausforderungen für die Logistik des Unternehmens ergeben, z. B. Lieferverzögerungen, schwer planbare Auftragsbestände und erhöhte Kundenwünsche. Daher beschloss Jollyroom, sich nach Lösungen für die Handhabung von schweren und sperrigen Gütern umzusehen. Die Priorität war, krankheitsbedingte Fehlzeiten zu minimieren und bessere ergonomische Arbeitsbedingungen für die Mitarbeiter zu schaffen. Die Vakuum-Hebelösungen von TAWI erfüllten die Anforderungen und wurden besonders wegen ihrer einfachen Bedienung geschätzt.
“ Die gleiche Arbeit erfordert beim Einsatz von TAWI-Hebegeräten weniger Personal. Anstatt dass zwei Personen einen schweren Gegenstand heben müssen, kann eine Person mit dem Vakuumheber dies selbst erledigen,“ sagt Niklas Blomberg, der Projektleiter Logistik des Unternehmens in Göteborg.
Dadurch wird der Sortiervorgang zeit- und kosteneffizienter, vor allem aber wird das Heben von Gütern bis zu 70 kg fast mühelos, was den Mitarbeitern langfristig ein ergonomisches Arbeitsumfeld sichert.