Warehouse sorting and palletizing for efficient operations
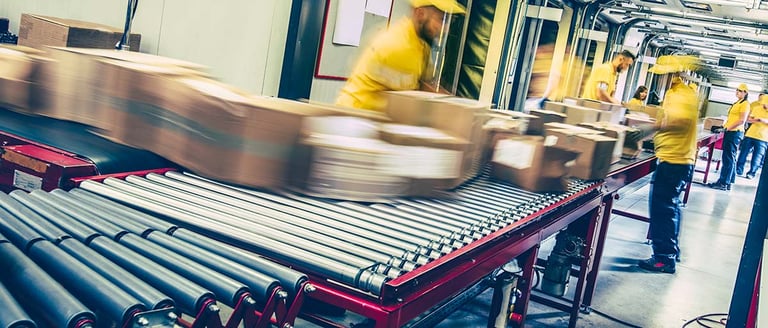
In the era of post-Covid, the significance of warehouse sorting and palletizing has grown exponentially due to the surge in online shopping and subsequent increase in demand for goods transportation. However, the fast-paced nature of this work can pose risks to the health and safety of employees, leading to burnout and high turnover rates.
To address these challenges, exploring automated solutions that enhance efficiency and alleviate the strain on workers is crucial.
The Impact of the Covid Pandemic on Warehouse Operations
In recent times, numerous sources, such as newspapers, tech magazines, and logistics websites, have highlighted the positive impact of the Covid pandemic on companies involved in transporting goods to customers. The rise in e-commerce reliance has resulted in a significant demand spike, sometimes even tenfold.
This increase in demand has created an urgent need for warehouse managers to find workers who are willing to engage in repetitive physical tasks such as loading, unloading, and sorting various items of different sizes and weights. Handling heavier goods often requires two-person lifting, while lighter packages need to be swiftly and frequently handled. Given the unique challenges posed by the post-pandemic era, it becomes imperative to explore alternative approaches to warehouse sorting and palletizing.
Addressing the Hazards of Warehouse Sorting and Palletizing
Warehouse sorting and palletizing inherently involve hazardous work conditions. The continuous arrival of trucks and containers loaded with palletized products necessitates swift and intelligent handling. Workers employ various tools such as cages, pallets, or conveyors to unload containers within a limited timeframe of three to four hours. Once the goods are removed from the container, workers can start the sorting process and distribute them onto additional pallets for storage and subsequent shipping to end customers.
Due to their complexity, these fundamental fulfilment processes continue to rely on manual labor. Workers are required to maneuver pallets, lift, place, sort, and scan diverse products that are packaged differently. Additionally, the products must be stored, retrieved from racks, configured for shipment, and loaded onto outbound trucks, often resulting in multiple lifts for each item.
Anders Knapasjö, Vice President Nordic, Baltic & Germany for Piab Lifting Automation Division and an expert on high-frequency lifting, emphasises the long-term impact of such physical exertion on workers. Regardless of the weight of the objects, the repetitive actions involved in warehouse work gradually take a toll on the body, exposing logistics workers to an elevated risk of workplace injuries.
“This will affect your body over time. In the short term, you may not notice it. But you notice when you come home, you sit down to dinner, and suddenly you feel it. Imagine what people who have been doing this for 10 or 20 years, what they experience.”
Little wonder, Anders says, that workplace injuries in the logistics sector are so high. “This is because people are lifting objects hundreds if not thousands of times a day, typically bending and turning as they do so, often in awkward positions. Even if these are lighter objects, this takes an inevitable toll on the body.”
Challenges in the Post-Covid Warehouse Operations
The increasing pace of work in warehouses post-Covid may introduce new health and safety hazards and increased employee turnover due to overwork and burnout. For example, warehouse workers in the USA experience work-related injuries at a rate nearly twice that of other private industry workers. Musculoskeletal disorders caused by manual palletizing account for over one-third of all lost work days, resulting in an estimated cost of $20 billion per year in workers' compensation. It is evident that warehouse employees face significant risks in their daily operations.
Cost of warehouse injuries:
- US warehouse workers suffer twice the average rate of work-related injuries
- This is a higher injury rate than mining and construction
- Injuries caused by manual palletizing cause 34% of all work days lost
- The estimated cost is $20 billion per year in compensation
- The Role of Automation in Warehouse Sorting and Palletizing
The Role of Automation in Warehouse Sorting and Palletizing
Automation emerges as a viable solution to mitigate the challenges faced by warehouse operations. While introducing robotics may seem complex and require significant investments in business process redesign, worker reskilling, and organizational transformation, the long-term benefits outweigh the initial productivity and performance setbacks.
It is essential to recognize that people remain indispensable to achieving optimal business results. A combination of machines and human expertise leads to significant gains in efficiency and problem-solving capabilities. Warehouse operations managers are seeking "plug and play" solutions—machines that are compact, user-friendly, and easily adaptable to changing tasks and workflows.
Calculating ROI on warehouse sorting and palletizing technology
Efficient automation projects focus on plug-and-play systems that offer a higher return on investment than large-scale custom installations. While large-scale automation may slow down efforts to meet surging demand, targeted automation solutions prove to be cost-effective and yield a faster ROI.
High-frequency lifting technology, such as vacuum lifting, has demonstrated its potential in reducing injuries and increasing productivity. For example, TNT (now FedEx) in Sweden successfully implemented vacuum lifting technology to reduce injuries to workers and maintain or increase productivity during the sorting and palletizing process. The implementation of vacuum lifting technology led to a reduction of injuries by more than 40%, while productivity remained unaffected.
The Importance of Speed and Ergonomics
In general, manual handling may be faster than mechanical assistance for the first hour or so when packages are coming off a conveyor belt into different pallets or cages. However, as the hours progress, machines consistently outperform humans due to their ability to handle the strain of lifting without fatigue.
High-frequency vacuum lifters, such as those offered by TAWI, provide a significant advantage in optimizing warehouse sorting and palletizing operations. These lifters are designed to mimic the way a person works manually and offer high-speed package handling, one-handed lifting with a user-friendly joystick handle, quick release for time-saving, and the ability to rotate packages 360°. By incorporating modern technology like high-frequency vacuum lifters, warehouses can significantly improve efficiency and provide employees with long-term ergonomic working conditions.
“We have a sophisticated tool to calculate ROI for our customers where we incorporate all the facts about the challenges they face, their employees, their parcel rates and so on, so we can add up the costs and put them against the investment,” Anders says. “But typically the ROI is as soon as 6 or 7 months. This where it becomes interesting for them.”
Conclusion
Optimizing warehouse sorting and palletizing operations is crucial for efficient order fulfilment, minimizing injuries, and enhancing worker well-being. By embracing automation solutions, such as high-frequency vacuum lifters, warehouses can reduce physical strain, increase productivity, and achieve a faster return on investment. It is evident that a combination of advanced technology and human expertise is the key to success in the evolving landscape of post-Covid warehouse operations.
A plug-and-play solution for warehouse sorting and palletizing
Jollyroom is the largest e-commerce business for child and baby products in the Nordics. Like many ecommerce businesses, recent years have thrown up new logistic challenges for the company, including shipment delays, hard-to-plan order stocking and increased customer demands. So Jollyroom decided that they needed to look at possible lifting solutions for handling the heavy and bulky goods. The priority was to minimize sick leave and provide better ergonomic conditions for their employees. Vacuum lifting solutions from TAWI met the requirements and have been especially appreciated due to how easy they are to operate.
"The same work requires less personnel when using TAWI lifters. Instead of having two people lift a heavy article, one person using the vacuum lifter can manage this by themselves," says Niklas Blomberg, the company’s Project Leader Logistics in Gothenburg.
This makes the sorting process more time and cost-efficient, but most of all it makes lifting goods up to 155lbs almost effortless, ensuring that employees have long-term ergonomic working conditions. Read the full case study.