Container Unloading Equipment in 2024: A Comparative Analysis of The Best Technical Solutions
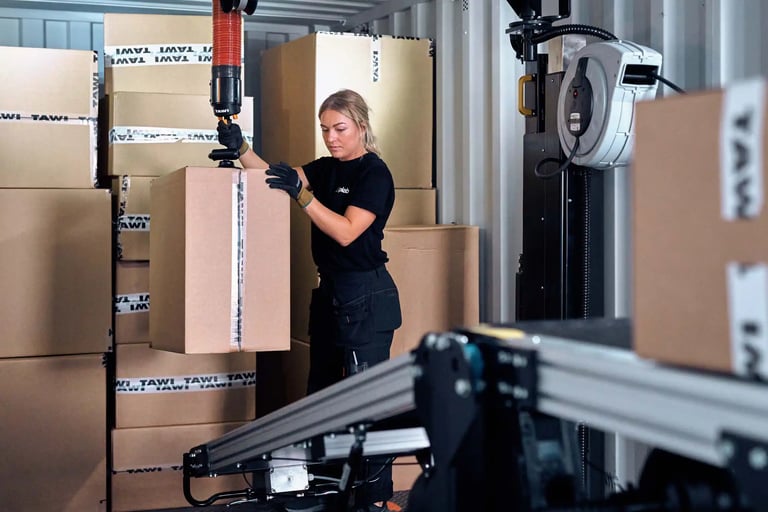
In 2022, global parcel shipping volume amounted to over 161 billion parcels. This volume is expected to skyrocket to 256 billion parcels by 2027, growing at a compound annual growth rate of 59%. Whilst the prospect of industry growth may be appealing, the reality for individual companies is often quite different.
Increasing pressures and expectations from buyers, coupled with labor shortages, make the forecasted growth in conjunction with the existing pain points within the industry problematic. If not managed properly, this growth could be hampered by bottlenecks in the industry like loading and unloading containers. In this article, we've compared the best container unloading equipment available in 2024.
Some have already turned to technology, but it's necessary for all logistics companies to avoid being overwhelmed and eventually outrun by competitors.
The Changing Landscape of Client Expectations
Next-day and even same-day delivery options have fundamentally changed the way people shop. They blend the convenience of online retail with the immediacy of brick-and-mortar stores. Some of the biggest logistics providers, such as DHL, DPD, FedEx and UPS, are operating new same-day delivery models. Given the compelling proposition of next-day delivery for consumers, demand is expected to increase significantly. Shipping and logistics are fundamental aspects of eCommerce and have a decisive impact on consumer purchasing behavior.
In Statista’s 2023 Top Shop survey asking US consumers about their eCommerce shipping preferences, it was clear that the B2C express market (same-day and next-day delivery) in France and the UK is expected to reach 1.2 billion parcels in 2023 and 1.9 billion parcels in 2027. Similar demands are expected from B2B. Same-day delivery is expected to grow from 70 million parcels in 2022 to between 260-521 million parcels by 2027.
Container Unloading Equipment: Solutions on the Market in 2024
The team at TAWI have surveyed two of the leading options in the container unloading sector to see what’s available and whether they can compete with our own container unloading equipment.
Boston Dynamics
Boston Dynamics’ product, Stretch, is a mobile robot designed to automate case handling and other warehouse tasks. Here are its strengths and weaknesses:
Strengths:
- Continuous operation: Stretch can work continuously through single or multiple shifts at any time of day or night.
- Versatility: Stretch can handle a wide range of package types and sizes, from standard brown to highly graphical.
- Autonomous operation: Stretch’s advanced vision system allows it to detect and automatically retrieve any boxes that shift and fall whilst unloading, so it can keep going without operator intervention.
Weaknesses:
- Cost: Whilst the exact cost is not mentioned, high-tech solutions like Stretch often come with a significant price tag, which might be a barrier for some businesses.
- Dependence on technology: As with any technology-dependent solution, there may be potential issues related to software glitches, hardware malfunctions, or other technical problems. This is worsened as their solution is fully automated, meaning total disruption of work.
- Capacity: Unlike other solutions on the market, Stretch only lifts up to 22.7kg, a relatively small weight which could be limiting.
- Deployment: Stretch requires a few days of installation which could have an impact on your facility's operations.
Slip Robotics
Slip Robotics offers licensed robots-as-a-service that empower people to auto-load and unload any truck in 5 minutes.
Strengths:
- Speed and Efficiency: Slip Robotics’ automated loading robots (ALRs) can load and unload any truck in just 5 minutes, driving 10x speed, throughput and safety across the supply chain.
- Safety: The use of SlipBots eliminates the need for people or forklifts inside trailers, increasing safety.
- Savings: SlipBots can cut idle time, freight damage, trailers and docks, leading to cost savings.
- Ease of Use: SlipBots work upon arrival at any dock, with zero Wi-Fi or IT integration required. They can be controlled with a simple click of a button.
Weaknesses:
- Dependence on Technology: Just as with Boston Dynamics, a complete reliance on automated solutions raises the risk of an inoperable warehouse if issues related to software glitches, hardware malfunctions or other technical problems occur. Further to this, the replacement of people with robots might frame your business in a negative light as it would mean job loss for many. Whilst an employee will operate the slip controller that commands robots, it doesn’t require skilled labourers, further exacerbating the shortage of skilled workers in the future.
- Training and Adaptation: Whilst SlipBots are designed to be user-friendly, there may still be a learning curve for operators to adapt to the new technology, requiring a whole different set of skills from what current employees have.
- Limited capabilities: The SlipBot only takes palletised stock out of lorries.
- Limited use cases: The SlipBot solution has to travel with your cargo in the shipping container which means it only really remains a valid solution if the containers remain in a closed system at all times.
- Critically, it doesn’t address concerns about lifting and human wear. Ultimately, the SlipBot still needs to be loaded and unloaded itself.
Although Boston Dynamics’ Stretch and Slip Robotics’ SlipBots offer innovative solutions, TAWI’s container unloading equipment provides a much more versatile and adaptable solution. TAWI’s solutions are designed to handle a wide range of goods, improving efficiency and safety in various operations such as unloading containers and sortation.
TAWI: The Best All-Round Container Unloading Equipment
Our range of solutions comprehensively addresses the pain points within the logistics sector and goes beyond the first step of unloading and loading containers. We understand the challenges and are helping prepare companies for anticipated pressures and setting them up to thrive in the face of industry growth.
Whilst we have a range of solutions to help address wider logistics and warehousing concerns, let’s focus on our like-for-like solution.
TAWI Container Unloader:
This product is designed to improve efficiency and safety whilst unloading containers and during sortation.
We’ve designed the Container Unloader to handle the tight spaces of trucks and shipping containers and can unload items to the conveyor belt or a pallet.
It is capable of picking up over twice the weight that Boston Dynamics’ Stretch can at 110 lbs. Whilst Slip Robotics can support heavier loads, its capabilities are limited, only being able to shift pallet stock out of the container to another location, without unloading it off the actual pallet, essentially acting as a glorified, and extremely expensive forklift.
Admittedly, our solution isn’t completely autonomous, and neither would we want it to be. For some, this will be a weakness, but for TAWI, we view it as a strength. A human workforce is still vital to these facilities' smooth and safe operation. We aim to ergonomically support and enhance the capabilities of people who have already highly optimized this sector.
Conclusion
Whilst the logistics industry is set to grow exponentially, companies must turn to technology to keep up with increasing pressures and expectations. It’s this ergonomic approach to lifting which supports a workforce to work quicker and more efficiently. It’s tried and tested and our clients can attest to it.
If you are interested in levelling up container unloading flexibility, productivity and employee health, get in touch with our team.