Automate your inbound logistics material handling – AND get ahead of the competition
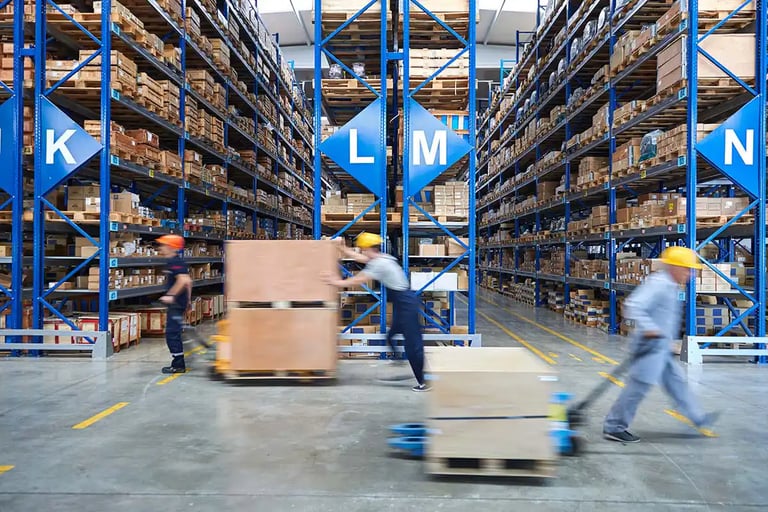
As the growth in e-comerce continues globally, the efficiency of inbound logistics could make or break your business.
Introduction to inbound logistics
Across the world, companies are gearing up to cope with the boom in e-commerce fueled by the Covid pandemic. Like never before, the supply chain is flooded by containers and stillages piled high with packages big and small, carrying everything from tires, gym equipment, white goods and electronics to clothing, wellies or wine.
Around one million companies are now using Fulfillment by Amazon, Amazon’s third-party logistics service, to receive, store, pick and ship out their packaged goods. FBA increased its revenue by almost 50 per cent in 2020 alone. The logistics business of parcel carrier UPS saw its revenue climb nearly 20 per cent in the same period, according to SJ Consulting.
This all adds up to tens of thousands of companies struggling to get inventory unloaded, sorted, stored, picked and shipped as quickly, safely and efficiently as possible. In short, a lot of big stuff needs lifting.
Companies are struggling to get products out the door and cannot find enough staff. Aviation freight is running constantly at levels that previously would have been seen only around Christmas.
With the post-Covid shock to the supply chain, many businesses are looking for novel solutions to their inbound logistics. Innovations in materials handling are helping cut costs and boost efficiency, according to Inbound Logistics magazine.
Facing the challenges of inbound material handling
In this blog, we will look in depth at the challenges facing inbound logistics material handling, with a focus on packages, and outline some ways in which automation can be part of the solution. After a brief look at the state of the industry today, the discussion is organized according to productivity and return on investment, safety, flexibility, and lifting solutions. There is also a short Q&A to finish.
Inbound logistics: The state of our industry
Everyone within inbound logistics is under pressure to speed up our order fulfillment and optimize operations. We want to do more and do it faster in the critical areas that we could potentially optimize, whether it's a standard warehousing arrangement or a 3PL distribution center.
There is nothing as versatile as the human being when it comes to throwing boxes around. So inbound logistics tend to rely on people to do the job.
But e-commerce continues to move more towards heavier, non-traditional purchases, posing a growing challenge to the industry. More and more goods are “noncon” – non conveyable – in other words, they are bigger than you would like them to be, generally heavier than 33lb.
“Logistics is a low margin, high volume, high speed business. But with e-commerce now moving into the heavier area, there is a tension within the industry, which is faced with bulky garden furniture or rowing machines that weigh 220lb. It is a very different world to that which logistics is accustomed to.” says Daniel Banks, former Global Key Account Manager at TAWI.
Does this mean hiring beefy men, and more of them? If we look at the big players in logistics, such as FBA, we see a very different picture. A quick video tour of an Amazon fulfilment centre reveals a small, mixed workforce and a great deal of automation.
What the tour doesn’t show, however, is the inbound material handling – getting the boxes out of the truck or container. Manual unloading is a potential bottleneck. Speed is essential, which means reducing any downtime while making sure no goods are damaged.
At Amazon, this process is semi-automated, with the use of vacuum lifters to unload the packages and feed them onto a conveyor. This is particular efficient when dealing with a loose load, when packages of all shapes and sizes are piled on top of each other.
“A good example of the challenges faced by the industry is bags of pet food weighing 33-55lb. With Covid, people were forced to buy pet food online. Then they discovered this was much easier than buying it at a store themselves, so there was a surge in demand. These bags are heavy and not a comfortable lift because they aren’t rigid.” Daniel says.
Inbound logistics: Productivity and ROI
It is no exaggeration to say that most people in this business aspire to Amazon’s level of innovation, energy and growth. Fulfillment by Amazon has set the bar high in terms of their response to the challenges of post-Covid logistics.
What works for a huge multination, however, might not be right for other 3PL operators or the logistics departments of package handlers across industry and the globe. The most expensive or sophisticated machinery is not always the best solution.
Instead, detailed planning is essential to get the best return on investment from equipment that has the potential to improve your inbound logistics material handling.
“You need to start from the concrete conditions that we know differ between each company and site, such as the number of full-time employees, the shift, the percentage use of automation as well as labor costs,” says Michael Wooster, UK general manager for TAWI.
“From this starting point, you decide on the volume or number of solutions needed, then you can begin to calculate the yearly savings that derive from factors such as increased flexibility and efficiency, to give you the return on your investment,” Michael continues.
If you can move from a two-person pick to a one-person pick, it might seem to be a no brainer – you have doubled your productivity at a stroke. Unfortunately, however, there is no one-size-fits-all answer to every warehouse or distribution center.
Finding the right solution for your business
There is a broad range of lifting solutions out there that can ease the logistics flow, inefficient processes and outdated technology and that hinder growth cannot be replaced overnight. Each inbound logistics material handling case is unique, depending on factors such as:
- Weight, size and shape of packages
- Variety of loads
- Palletized versus loose load
- Cost and availability of labor
- Size of the workforce
- Shift patterns
- Warehouse layout
- Availability of charge points
- Method of transport
In terms of a site manager looking at this process, you need to get the container emptied quickly and refilled with something else. You’ve got loose loaded containers jam packed with boxes up to the ceiling, so you cannot use a forklift and the conveyor has to come right up to the container.
Space is tight. Unloading is often a bottleneck that slows down the palleting operation on the end of the conveyor if it's not done efficiently enough to keep up with the speed of picking from the conveyor to pallet.
These pain points within inbound logistics can actually be minimized with different lifting machines that make the process more efficient. The result is significantly more efficient workflows that do not leave employees exhausted, while you are also be able to reduce the number of employees needed.
The ROI is different for each site according to its unique conditions, and must be modelled in detail to allow accurate forecasts. But return on investment in lifting equipment is often measured in months rather than years.
Michael Wooster says: “Targeted investment that is tailored to your business will result in measurable productivity and staff health improvements in both the short and long term.”
Inbound logistics: Health & Safety
Whatever changes you want to make to your inbound material handling, they have to make business sense. Return on Investment is essential in a business with tight margins.
However, automation can also present operations managers with an opportunity to make an efficiency case for better health and safety in the inbound logistics process.
“We know that when investing in new solutions or systems it is critical to understand the return on that investment,” says Peter Wood, specialist in airports and logistics for TAWI in Europe.
“But the benefit you get from automated lifting solutions is also healthier and happier employees, lower sick leave and lower corresponding costs. Machines should never slow you down, they don’t get tired – and they massively reduce the risk of injury.”
Covid has posed specific health and safety problems, such as the need to eradicate “team lift”. Any operation that requires two or more bodies in close collaboration became a Covid social distancing challenge – you couldn’t have two people in a trailer or stood next to each other on a conveyor.
“These times call for social distancing, which can be solved instantly with lifting equipment as there is no longer a need for two people in the crowded space of the container,” Peter says.
Sorting goods onto pallets is challenging, as the height difference can be tough for the manual handlers – lift, bend and twist movements are hard on the back and spine, especially when you are trying to keep pace with a conveyor belt. Loose boxes of varied sizes stacked in narrow places can be hard to reach and awkward to handle, and we are all familiar with the problems caused when boxes have not been stacked correctly on pallets.
Ergonomic lifters increase productivity in the workplace by making lifting easy, and when lifting is easy you can lift more for longer and with less effort, and you can move from team-lifting to one-person lifting.
“By eliminating the heavy manual lifting from your workflow, companies help to keep employees alert and efficient all day every day, while ensuring they are not exposed to risks of life-changing injury,” Peter says.
Inbound logistics: Flexibility for Profitability
Logistics operations in fast-paced global markets need to constantly adapt to changing economic conditions and customer needs. A flexible and adaptable workforce is a central aspect of long-term business success.
In logistics, the varied nature of the physical strains involved in manual lifting is an important challenge to employee flexibility and job rotation. Quite apart from dealing with heavy objects, tasks that require frequent repetitive movements, such as sorting packages from a conveyor onto a pallet, are also demanding, especially when they have to be done at a high pace over an entire shift.
It is difficult to rotate jobs to help with these problems when only a few can perform certain types of work. This also makes the business vulnerable to lack of resources or sick leave.
Making your business less vulnerable and more flexible is therefore one of the biggest benefits of automation in inbound logistics material handling, because it helps most employees to perform the most demanding tasks.
Benefits of flexibility include:
- Employees can perform a wide range of different tasks
- They can be moved around to where they are most needed at any particular moment
- They can move between workstations to avoid unnecessary downtime
- A wider range of tasks and functions can be managed with existing resources
- It is easier to hire part-time or agency staff at busy periods
- You have more freedom to hire the right person for your company rather than the best person to perform a particular task
When employees can perform a larger variety of work steps, their productivity can be optimized by being able to move around to any task, depending on where the need arises. In this way, a flexible workforce brings a variety of cost efficiencies while offering more opportunities to employees.
“Lifting machines don’t discriminate, you don’t just need bulky men to do material handling on site,” Peter Wood says.
“When you are ringing a recruitment agency, you don’t need to specify that you need people who can handle big weights. For agency workers, there is plenty of demand for their services, they can choose which job to take. Faced with a choice between manual lifting and automated solutions, which job are they going to choose?"
“Obviously, smart lifting technologies enable women to do the job. They open up jobs to different people. You can get the best person for your company rather than a best person for a job,” Peter says.
Giving varied tasks to staff not only means higher productivity and efficiency – it also creates a more dynamic working environment. This leads to a greater commitment and motivation.
Creating flexibility in the workforce comes with many additional benefits, such as increased productivity, minimized downtime and improved health and safety of employees, all of which contribute to increased results.
In addition, smart lifters give everyone the power to lift heavy goods no matter their strength or size. A flexible workforce means employees can move between workstations to avoid unnecessary downtime and ensure continuous productivity. Businesses have much greater flexibility in terms of recruitment and employee rotation.
Inbound logistics material handling: Smart lifting solutions
At their production site in Belgium, Rockwool, makers of insulation materials, faced an untenable situation. Each worker was lifting nearly three hundred 55lb boxes each day, weighing a total of more than 7 tons.
Rockwool invested in ergonomic vacuum lifters. Productivity increased, as workers were now able to maintain their work speed throughout the day without getting tired.
“The investment in lifting equipment pays off quickly due to the obvious health benefits for the employees,” says Danny Flass, Production Site Supervisor.
Vacuum lifting equipment is a semi-automatic solution to the efficiency, safety and flexibility challenges facing inbounds logistics material handling that we have outlined above. The technology is versatile and can be customized to suit specific business needs. And it is user-friendly, requiring minimal training and a short period to grow accustomed to the new way of working.
TAWI is a world leader in this technology
With headquarters in Sweden, TAWI solutions are provided through a worldwide network of distributors and technicians. A global team of experienced engineers design lifting solutions customized for your needs.
TAWI is there for businesses who want to improve the working conditions for their employees, and at the same time increase productivity and workforce flexibility.
When you invest in TAWI lifting solutions, our service and support team will ensure that the equipment never fails you. These are robust, reliable tools that lift anything up to 600lb safely and swiftly.
Choosing TAWI means that you get Swedish quality and reliability, in product, service and support. We offer a complete range of smart lifting solutions used in everything from very specific manufacturing processes to the high-speed parcel handling at busy distribution centers.
TAWI lifting equipment handles everything from boxes and sacks, to blocks of meat and cheese. We can turn, tilt and rotate heavy barrels, large panels and much more. TAWI lifting solutions include vacuum lifters for various types of loads, unique mobile vacuum lifting solutions, lifting trolleys, different types of hoists, and a wide range of crane systems. This means that TAWI equipment cover all your lifting needs.
Q&A
How long will it take to get a return on my investment?
The ROI is different for each site according to its unique conditions, and must be modeled in detail to allow accurate forecasts. But return on investment in lifting equipment is often measured in months rather than years.
Will lifting equipment slow down our processes?
If you have any doubt about how fast vacuum lifting equipment can work, watch this short video here: https://bit.ly/3C7hf9t
What if I have different items that I need to lift in the same area?
With TAWI, you can quickly change the suction foot to ensure quick, efficient, and safe handling of a wide variety of packages.
How much training is necessary to use the equipment?
There is a level of skill involved, such as learning to control the up and down motion of the lift tube. But training takes no longer than an hour.
What is the difference between vacuum lifting equipment and robotics?
A vacuum lifting machine is not a robot, it is an aid to a human. Incidentally, this keeps the cost down because humans can sense subtle but vital factors and respond accordingly – something that machines find it very hard to replicate. Robots are controlled remotely by digital software.
What happens if there is a power cut?
In the case of critical problems such as power failure, protection valves ensure that the load is not immediately dropped to harm bystanders or the load itself. Vacuum lifting also lowers the risk of damage to materials such as scratches or deformation, and the risk of dropping goods is minimized.
Isn’t a person more flexible, fast and efficient than a lifting machine?
Yes and no. First, it depends on each person and their physical characteristics. Secondly, it is rare for a person to be able to lift repeatedly at high speed for a whole shift, day after day, without becoming exhausted or injuring themselves.
Can lifting equipment be trialed?
Yes. TAWI, for example, has demonstration units that we can take out to customers. Our representative sets the units up and then we leave the units with you normally for a week so they can get truly trialed without us overseeing the operators, so that get used to them. We also have demonstration areas at our outlets in several countries, so companies can bring us the products that they need to lift and we can trial the vacuum units and discuss different possibilities.
Humans can move anywhere, surely machines are less flexible?
Vacuum lifters are suspended from gantries, which generally allows them to be custom built to fit the shape and size of any specific area. Many warehouses have tight, narrow workspaces with low headroom, but here too solutions exist, depending on the goods you are handling. Certain equipment enables one-handed operations, as well as challenging operations such as stacking.
Flexible lifting aids ensure the operator can move around and reach all the floor space needed for optimum efficiency. The latest vacuum lifting tools from TAWI are battery powered, so that order pickers, for example, are highly mobile.