Managing risks when unpacking shipping containers
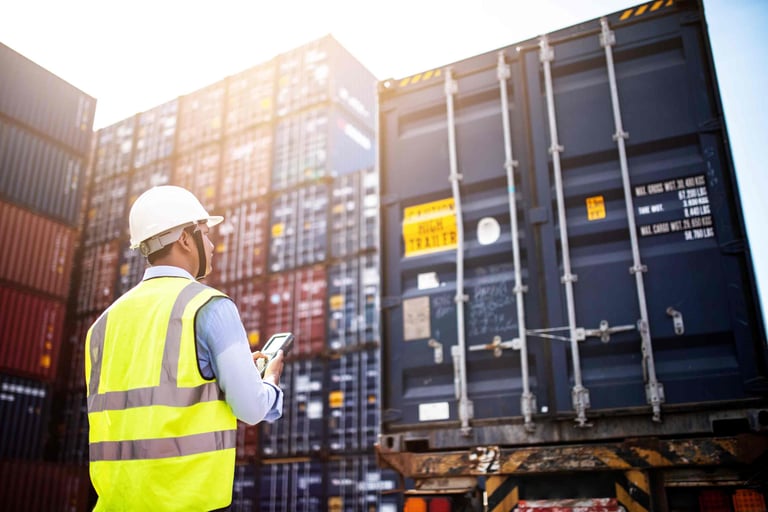
An estimated 21 million shipping containers are currently moving goods from one point to another, with over 500 million loose loaded container shipments every year. This poses challenges to container unpacking health & safety as the large majority of loose loaded containers are loaded and unloaded manually.
What we need is an efficient, economical way to manage health and safety risks when packing and unpacking containers.
With the rapid rise of online and international commerce has come another dramatic increase -. the use of intermodal, or shipping, containers. These large, metal structures are designed and built to move freight across different modes of transport – enabling the containers to go from ship to rail to truck without unloading and reloading the cargo they contain. Shipping containers enable companies to store and transport materials and products efficiently and securely, and are an integral part of modern commerce. There are an estimated 21 million shipping containers currently moving goods from on point to another, with over 500 million loose loaded container shipments shipped every year, transporting 95% of the world’s cargo. A modern logistical miracle. This solution poses challenges to container loading and unloading health & safety, however.
One size fits all (except when it doesn't)
Modern 40-foot shipping containers are built to withstand the stress of intermodal shipping and provide a means to bundle a mix of cargo and packages of different weight, size and shape into loads that will pack tightly in a ship. Most companies do not own their own containers, but rent them, meaning that they have little ability to modify the actual containers. This naturally helps standardization, but does not come without a price. While the containers themselves come in a few standard configurations, the freight they carry is not always as uniform. Loads containing packages of varying size and shape place high demands on flexibility. In addition, palletizing goods inside a container makes it impossible to utilize the full space of the container, as the width of the container can only fit 2 ½ pallets, and entails that the large majority of loose loaded containers are loaded and unloaded manually.
By necessity, containers are often placed on sloping or uneven ground, and the environments in which they are located are often inadequately lighted, which makes safe packing or unpacking of the container contents difficult. In addition, items in the containers might come loose during transport or have perhaps not been packed for easy unpacking. Workers are at risk of being hit by unrestrained items or falling loads. Contents that can come loose during transport can easily shift or fall, forcing the doors open or falling on workers when the door is first opened. The list goes on. In addition, there is usually a very tight time window during which unloading must be completed, adding haste to the list of possibly hazardous factors. All of these factors pose specific challenges to the loading and unloading process – challenges that can dramatically impact your business.
The Most Common Hazards when Packing/Unpacking Shipping Containers:
- Injuries from hazardous manual tasks
- Repetitive strain injuries
- Injuries from slips, trips and falls
- Employees being hit by falling objects
- Injuries from use of incorrect or unsuitable equipment
- Injuries from contact with hazardous materials
- Falls from height
- Physical fatigue
- Musculoskeletal disorders
- Sustainable unpacking of containers
We are used to thinking of “sustainability” in terms of our impact on the global environment. And while that aspect of sustainability is no doubt a crucial one, there is another sustainability issue that affects your container operations. The poor working conditions currently in place at most container sites lead to low employee retention, difficulty in hiring, and the need to hire cheaper, less skilled labor – often from less developed countries. In the long run, none of these is a sustainable business model and presents barriers to both growth and profitability.
While companies dealing with container loading and unloading – from shipping and freight firms to warehouses and harbors – have struggled with reducing risks and injuries, the systems employed to pack or unpack shipping containers are often unsafe or flawed. The very nature of handling packages of varying size and shape demands flexibility and makes it difficult or expensive to introduce automatic solutions. Even the smallest of shortcomings, from selecting unsuitable straps, chains or restraints or using them incorrectly, to using forklifts or other lifters with improper designs, has a negative impact on the time it takes to unload, the safety of personnel, and your operations margins.
What this means to you
The items packed in containers vary significantly, ranging from small to large, heavy to light, easily handled to awkward and bulky. The loading and unloading of this very un-standardized cargo, requires conducting repetitive, manual tasks that involve lifting heavy or bulky items in situations and environments that require workers to lift in dangerous or awkward postures. The risks involved with container loading and unloading vary from one container to another.
As with any loading, unloading, or movement of goods, the manual lifting and shifting involved can – even when properly done – involve risk to your employees. Unpacking goods by hand can lead to musculoskeletal injuries caused by repetitive actions or by working with goods above shoulder height or below knee level. In addition, workers unpacking containers may be struck by falling goods—particularly if goods have shifted during transport or goods spill from the container when first opened. Common injuries associated with packing and unpacking shipping containers include minor sprains, strains, abrasions, fractures, and other lifting related injuries. In the best-case scenario, these injuries can cause severe organizational or economic damage, in the worst case, incapacity or even death.
How much does a sprained shoulder cost?
The simple truth is that workers are at risk when they are unpacking heavy, awkward and unsecured items. The systems used to unpack containers often include the manual handling of goods and involve heavy lifting, awkward postures, and repetitive motions.
Whether damage to the cargo itself or the workers handling it, manual lifting can result in an economic blow to your operations. Products not fit for delivery, absence of your work force due to injury, stress, or illness, the inability to properly plan your resources – all can impact your bottom line. Repetitive stress injuries are responsible for a large percentage of worker absence, and the rigorous physical demands of container work make finding skilled employees difficult.
Add to these obstacles the numerous legal restrictions/responsibilities in place, the challenge of planning and scheduling personnel when not knowing what a specific container contains, and all the while maintaining the pace and productivity of the loading or unloading process, and the challenge is clear. And any disturbance to the loading or unloading process can mean that you are late in delivering, or even have nothing to deliver at all. Which leads to dissatisfied customer and reduced revenue. Late or missed deliveries, employee injury or absence, damaged goods, increased workforce turnover – all affect your ROI, all pose threats to your business.
A glimpse of a silver lining in unpacking of shipping containers
The number and use of shipping containers is not likely to decrease – demands on safer loading and unloading procedures, however, are increasing all the time. On the positive side, improved working conditions lead to higher employee motivation, which means lower levels of sick leave or absence due to injury, more contented employees, and increased employee retention.
Combined, these improvements maintain or even improve productivity and make it easier to plan resources and to adjust your processes to accommodate changes in incoming goods and daily work situation. In addition, when you create a safer workplace, you are also making it safer for the goods and cargo you are handling. Less breakage, fewer missed deadlines, happier customers. Knowing all that, what should one do?
We need a way of safely loading and unloading containers that:
- Removes or reduces repetitive manual labor
- Creates workflow safety and efficiency
- Limits damage to container cargo
- Keeps costs down and productivity up
- Improves planning
- Improves employee retention
- Meets safety regulations
- Increases workforce flexibility and quality
- The problem is clear - how about the solution for unpacking containers?
There are currently very few lifting aids available, and the physically stressful conditions (involving lifting, bending, and twisting) involved with container loading and unloading lead to injuries and increased sick leave. What is needed is an efficient, economical way to manage health and safety risks when packing and unpacking containers – whether transported by land or sea and from packing to opening of the container doors and removing and transporting items to their final destination.
The search for a more ergonomic method of container unloading is on. Companies have become aware of the fact that in order to guarantee a safe and profitable operation, every possible hazard must be eliminated or minimized in order to safeguard workers’ health and safety. The irregularities and challenges of container cargo loads, however, have made these efforts difficult.
A few common-sense remedies have been applied, ranging from taking extra care when moving or shifting container contents, to attaching securing devices to reduce the number of items that fall or to protect those items that do. The chaotic nature of container yards, however, and the time pressure usually in place complicates the situation. What is needed is a way of lifting and moving container cargo safely that eliminates the risk of musculoskeletal injuries, that can deal with a wide range of weights, sizes, and dimensions, and that can remove some of the physical stress and danger from this rapidly growing sector. What is needed is a better, safer way of loading and unloading containers.
What TAWI is doing
A safe and healthy workplace does not happen by chance or guesswork. It requires analysis and planning. It requires that one understand not only the risks, but the circumstances that give rise to them. And this is what we at TAWI specialize in. At TAWI, we are always working on new methods and products with which to control and minimize risks. We work closely with our customers to find the best solutions to their problems, consulting stakeholders, engineers, and other experts, as well as workers themselves, to create the best products possible.
TAWI has lengthy experience in helping companies of all sizes and types find safer, more productive, and more efficient ways to handle and move their products. We are experts at developing solutions that are easy and economical to implement, require little maintenance, provide fast ROI, and that help our customers stay competitive in increasingly tough markets. We are known for our flexible and innovative solutions in a wide array or industries. Our container unloader and mobile high-frequnecy lifter offers efficient loading and unloading in confined spaces.