How to create a healthy & safe workplace in the food and beverage industry
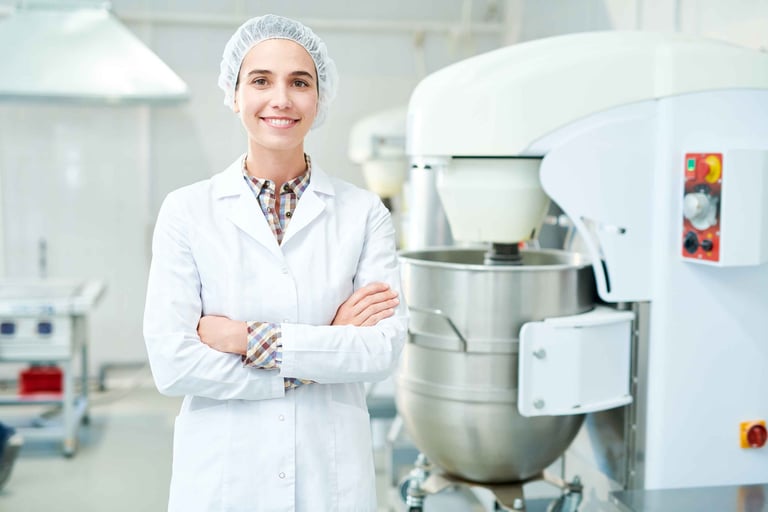
Safe lifting and handling is an integral part of the food and beverage industry. Unfortunately, this tends to be a key source of injuries in the workplace. Implementing a healthy and safe procedure in your facility goes far past meeting government standards and laws, as it has a major impact on your business. TAWI has years of experience with helping companies in the food and beverage industry make their procedures as ergonomic, safe, and sanitary as possible, as well as improving the health of both the employees and the operations in the process.
Susceptible to hazardous lifting
It can be assumed that most manual handling injuries occur in the high-risk sectors such as the construction or heavy manufacturing industries. However, injuries occur regularly in every industry.
For example, about a fourth of all accidents that occur in the manufacturing sector occur in the food and beverage industry. Manual handling in the food and beverage industry can consist of handling and packaging raw materials, or moving containers on and off conveyors, as well as inspecting, packing and loading the final product. Many of these tasks involves repetitive and potentially hazardous steps, such as:
Heavy lifting and awkward lifting
Repetitive movement
Sustained posture
Unstable and unbalanced loads
Such tasks within the food industry include lifting and moving of heavy bags of ingredients, large drums, shrink-wrap rolls, and kegs. In addition, workers are repeatedly lifting and handling bottles, cans, unwrapped food products, liquid ingredients, and even smaller, more delicate objects. This array of heavy lifting makes the food and beverage industry susceptible to hazardous lifting.
Safer lifting solutions
Like most occupations, the food manufacturing industry can be hazardous to its workers. The wide range of ingredients and packaging in the food and beverage industry all have one thing in common – the need to move them from where they are, to where they need to be. This can be risky to both the employees and the products they are handling. Handling products within the food industry is constantly a sanitary challenge.
The injuries most frequently arising from manual handling are musculoskeletal disorders, or MSDs. This term is used to describe the various forms of damage caused by heavy, repetitive, or incorrect handling and lifting to the body’s joints, ligaments, and the back muscles. MSDs also cover injuries to joints, ligaments, tendons and nerves in the wrists, arms, shoulders, neck, abdomen and leg. These types of injuries are also known as ‘sprains and strains’, repetitive strain injuries, or occupational overuse syndrome. No matter what you call them, MSDs can have serious and permanent affects to your employee’s ability to carry out their work – and be extremely debilitating to both your workforce and your productivity.
Work-related upper limb disorders (WRULDs)
What in the world is a WRULD? Workers carrying out lighter repetitive tasks can suffer from chronic injuries, known as “work-related upper limb disorders” or WRULDs. These injuries account for almost a quarter of occupational ill health. The risk of damage to muscles and joints is not limited to particular sectors of the food and drink industry or to specific roles. And while around one-half of injuries in the food and drink industry are caused by handling and lifting heavy objects, the other half are not.
The overexertion that results from repetitive motions such as bending, twisting, and turning are common causes of shoulder and back injuries. Strains and sprains from lifting loads improperly or from carrying loads that are either too large or too heavy to be safely managed, are everyday hazards. In fact, studies have shown that over a third of all missed workdays are the result of shoulder and back injuries, most frequently affecting the spinal region and ranging from minor strains to long-term disc problems. While the injuries resulting from the lifting and handling of heavy and/or awkward objects and repetitive, non-ergonomic lifting are often minor, over long periods of time they can have a major impact to your body.
Case in point – back pain is the most common MSD caused by the manual handling of loads in a workplace. About one fourth of workers suffer from back pain, which tops the list of all reported work-related disorders. Prevention is vital when it comes to work-related MSDs due to manual handling. The more workers are exposed (for longer periods or higher percentage of their work time) the more likely they are to report an MSD complaint.
The top four causes of WRULDs in the food and drink industry:
Stacking/unstacking containers
Pushing racks and trolleys
Packing products (such as cheese, confectionery and biscuits)
Handling drinks containers (drums, kegs, etc.)
Studies have shown, however, that three-quarters of these injuries can be prevented.
Vacuum technology can provide a solution
Vacuum lifting technology is increasingly being used as a way to lift, move, and sort products and packages safely, quickly, and efficiently. It removes the risk of careless accidents or workplace injuries caused by the often heavy and repetitive lifting required in the food and beverage industry. Any operator, regardless of size or strength, can have precise and weightless control of even the heaviest, most cumbersome bags. And with no limitation on who can lift what, it is far easier to achieve workplace flexibility and diversity.
A quick checklist:
Are your employees lifting manually without a lift assist?
Does your business have a high rate of workers’ injury?
Is manually lifting products slowing down your workflow?
Do you have trouble recruiting or maintaining workplace diversity?
If you answered “YES” to any of the above, it’s time you considered implementing a vacuum assisted lifter into your workflow.
TAWI has a wide range of lifting solutions that have been developed specifically for the food and beverage industry, and our solutions can streamline your entire workflow, from the receiving of incoming goods, to processing, packaging and palletizing. Our stainless-steel vacuum lifters allow operators to lift food with minimal effort and absolute precision, while our lifting trolleys provide additional mobility. From start to finish, a safer and more productive workplace can be resolved with a TAWI lifter.
Many Health and Safety Managers purchase TAWI systems to reduce workplace injuries, but quickly discover a range of additional benefits, such as increased lifting ability, improved production workflow, and reduced employee turnover, giving them an even greater return on their investment. The added value from a vacuum lifting solution comes from both ends of the balance sheet – reduced costs as well as higher efficiencies, productivity and profit, benefitting the entire economic well-being of a business, and improving its level of trust and reputation.
The hidden costs of an unsafe workplace
Most are aware that creating a safer workplace, with lower risk of injury or death, is a no-brainer. While difficult to measure sometimes, the benefits of a healthy workforce are reflected in increased productivity, lower absenteeism, improvements in talent acquisition and retention, and other areas.
Beyond the physical impact lies another crucial factor – the economic impact of ignoring employee safety. Work habits or procedures, whether unidentified or unresolved, cost companies huge amounts of money, and these costs can add up. They include absence due to sickness or injury, high staff turnover, expenses from retraining new employees, and the loss of production. Not to mention, to productivity weakens causing a strain on the workflow.
When it comes to the stock market, companies with strong health and wellness programs out-perform those who don’t. And the same goes for the factory floor, as companies with strong safety procedures out-perform their competitors with weak procedures.
These hidden costs of an unsafe workplace include:
Equipment or process damage
Downtime/loss of production
Absence due to injury or illness
Retaining costs or overtime
Damage to company reputation
Employee health can impact your business as much as employee safety. The long-term negative impact of improper work habits is not always immediately apparent. Poor health and safety in the workplace can become chronic concerns and create many problems in the future. all of these factors affect your business. TAWI can help make your workplace safe and efficient which makes for good business.
TAWI safety can be your niche
The key to preventing manual handling injuries in the food and beverage industry is to think and act, both smart and safe. More often than not, companies are finding that an integral part of such an approach is the use of vacuum lifting tools and solutions in order to make manual handling tasks more efficient and dramatically reduce risks and injuries. And more and more, companies are turning to TAWI to help them make their workflows safer and more effective.
TAWI has been supplying material handling equipment for the food industry for many years, and we have a thorough understanding of the special demands of this industry. Our flexible vacuum lifting solutions enable you to lift almost any type of surface or dimension quickly, safely, and in a sanitary fashion. TAWI stainless-steel vacuum lifters meet the highest clinical standards and have been carefully designed to reflect the requirements of operations where sanitation and product integrity is of the utmost importance.
A TAWI ergonomic vacuum lift system:
Grips and lifts all types of materials safely and effortlessly
Turns a 2-person lift, into a 1-person lift
Improves workforce flexibility
Meets strict sanitary requirements
Reduces worker injuries and saves your business money
Implementing a TAWI system reduces the risk of accidents and the consequent injuries to your workforce and your balance sheet. Our vacuum lifting solutions can help you create a workplace where employees are less likely to suffer from back sprains, muscle pulls, wrist, elbow, and spinal injuries, and less prone to injuries from accidents caused by heavy or improper lifting. In addition, a TAWI lifting solution enables a single employee to safely and securely lift and move loads that previously required multiple employees, from the most delicate items to heavy or awkward loads which are difficult to grasp or hold.
With a TAWI lifter, you can reduce employee stress and fatigue, lower damage to products, and increase worker motivation and satisfaction. All of which leads to increased productivity and lower costs.
A brand you can trust
Handling food and beverages requires trust. The trust that employees have that you will not endanger their health and well-being. The trust that food companies have in that sub-suppliers will ensure that no harmful substances make their way into the food products. The trust consumers have that the things they purchase are safe to eat. Achieving this level of trust places major demands on health and safety, as well as on sanitation and quality.
TAWI’s long history of supplying lifting solutions to the food industry has earned us the trust of our customers. Our ergonomic solutions can be customized for almost any need and have helped a wide range of companies achieve and maintain a productive workflow, a safer workplace, and a more efficient and profitable operation. We look forward to earning your trust as well – and helping you build a better business while doing so. Contact us here to schedule a consultation.