An Introduction to Vacuum Technology
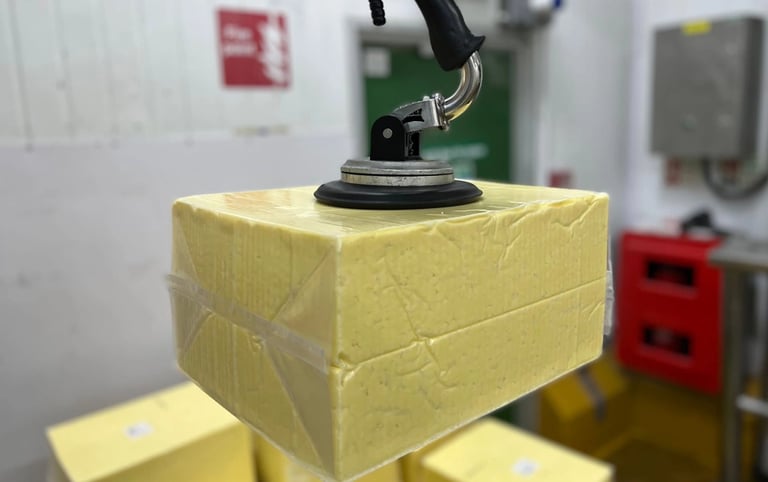
Vacuum technology is an irreplaceable part of a wide range of scientific and industrial applications. You will find vacuum systems in areas as diverse as packaging, freeze-drying, numerous forms of manufacturing, and even particle accelerators. This article is a brief overview of vacuum technology in general and, more specifically, how it is applied in vacuum lifting.
What is a Vacuum?
The word vacuum is derived from Latin for “empty space”, but in the real world there is no such thing. Even the vacuum of space contains small amounts of matter and a perfect vacuum exists only in theory. For all practical purposes, a vacuum is the state of a volume of space with significant negative pressure compared to the atmosphere. An artificial vacuum is created by removing matter, normally air molecules, from a limited space.
What is a Low, Medium or High Vacuum?
In a vacuum system, less is more. Since a vacuum is created by minimizing the amount of air molecules in a closed environment, fewer molecules means a higher degree of vacuum. As air is removed, you will achieve an amount of negative pressure relative to the proportion of molecules removed. Depending on the requirements of a specific application, the methods used to create a vacuum vary a lot.
As measured in mbar pressure, different types of vacuum levels are divided into the following ranges:
- Rough (or low) vacuum – Atmospheric pressure to 1 mbar. Used in numerous applications including industrial handling technology. In this range, the level of vacuum is often referred to as a percentage, e.g. 80% vacuum.
- Medium (or fine) vacuum – 1 to 10-3 (0.001) mbar. Used in e.g. freeze-drying of foodstuffs, steel degassing, light bulb production.
- High vacuum (HV) – 10-3 to 10-8 mbar. Used in e.g. electron tube manufacturing, smelting of metals.
- Ultra-high vacuum (UHV) – 10-8 to 10-11 mbar. Used in e.g. metal coating, electron beam melting.
In order to reach higher pressure ranges, the complexity and energy cost increases exponentially. While many of the most common applications are in the rough range, quite a few manufacturing processes and scientific uses necessitate the higher ranges. All ranges beyond the rough range become increasingly difficult to measure.
How to Create a Vacuum
The level of vacuum required in different industrial applications varies a great deal, and the same is true for the equipment used to generate it. However, a variety of pumps – in some cases working in multiple stages – are always involved in creating and maintaining a vacuum system. A few examples of different types of vacuum pumps:
- Cryopumps: Industries that work in the ultra-high vacuum range, such as optical film or semiconductor manufacturing, use cryogenic pumps that “trap” molecules on an extremely cold surface. Cryopumps are also frequently used in scientific research areas like particle accelerators and space simulation chambers.
- Roots pumps: In metal purification and different types of coating applications, multi-stage roots pumps may be employed. These pumps compress gas between counter-rotating lobes to reach into the medium or high vacuum ranges.
- Screw pumps: When freeze-drying foodstuffs, screw pumps that use asymmetrically rotating screws are commonly used to speed up sublimation during the drying process.
- Rotary vane pumps: Last but not least, rotary vane pumps, which use rotors to continuously compress and exhaust air, are the most common vacuum pumps. Rotary vane pumps are employed universally in the low and medium vacuum ranges for, among numerous other applications, vacuum lifting technology.
The Mechanics of Vacuum Lifting
Vacuum lifting technology operates in the rough vacuum range, which can be measured using mechanical gauges in millimeters or inches of mercury (mmHg or inHg), and/or kilopascal (kPa). These units are always negative and denoted with a minus (-) on the gauge.
Kilopascal is particularly useful as an approximation of the percentage of vacuum. 50% vacuum is about -50kPa relative to atmospheric pressure. Several additional units and scales are also used in vacuum measurements, but the percentage scale is the most useful in the rough range as it is universally understandable.
Vacuum System Components
Vacuum Suction Cups and Tubes
A common misconception about suction cups/feet is that the inside of the cup is gripping the load and pulling it upwards due to the vacuum. In reality, it is the higher atmospheric pressure outside the cup that is exerting pressure downwards, towards the object, that produces the clamping effect.
For this reason, the height of a vacuum cup has no effect whatsoever on the level of vacuum or its lifting capability. However, the amount of surface area that comes in contact with the load does matter. This is why you need to adjust the cup’s surface to match the intended loads. Although it may be possible to lift heavy objects with a comparatively small cup, you also have to account for shear forces when objects are moved and add a safety margin.
Estimating Suction Cup Holding Force
To estimate the suction area needed to hold a flat, non-porous load using a hoist-mounted vacuum yoke such as TAWI’s Panel Gripper, this is one way to calculate:
The holding or lifting force is an approximate 1 kg per 1cm2 at 100% vacuum (2.2 lbs. per 0.155in2). As we have already established, there is no such thing as a 100% vacuum, but it’s a useful reference point.
In actual use, you might operate a lift at 60% vacuum. 60% of 1 kg is 0.6 kg, meaning that we can lift 0.6 kg per 1cm2 of suction cup area (1.32 lbs. per 0.155in2). Then divide the result by a safety factor of 2, which is typically used.
Example: A suction cup with a 300 mm (11.8″) diameter (706cm2 or 109.4in2) has a holding force of 212 kg (467 lbs.) at 60% vacuum and a safety factor of 2.
Estimating Lift Tube Capacity
With lifters that use a separate hoist for lifting and yoke-mounted suction feet that attach to the load, a simplified approximation of the suction feet contact area is useful. The situation is different when both gripping and lifting are performed using vacuum technology, such as with the TAWI Multifunctional Lifter.
In a tube-assisted vacuum lifting system, the tube itself operates at a negative pressure of anywhere between 0–60% due to the flexibility of the tube. To compensate for this, the holding force must always be greater than the area of the lifting tube. Therefore, we always ensure that the suction cup area is at least 2.5 times larger than the area of the tube.
The result is that you are guaranteed to never drop the load before it is lowered to the ground, and you are able to hold 2.5 times as much as you are able to lift. In other words, the suction cup area, while still important, is secondary to the lifting tube area in this case.
Customizing a Vacuum System
Aside from standalone systems such as the TAWI Mobile Order Picker, vacuum lifting systems are often customized to a great extent to meet the requirements of each individual use case. Some of the factors that determine the choice of components are:
Weight, shape and surface of the workpieces.
Travel distance for handling.
Rotation or tilting requirements.
Desired speed or cycle time.
A wide variety of suction feet/cups, yokes, cranes and rails may be selected and combined for a specific application to ensure optimal deployment and utilization.
For example, solid boxes may be lifted using a tube-assisted lift like our Multifunctional Lifter, with an appropriately sized handle and suction cup. If the loads have a porous or uneven surface, as is common with bags, a rubber skirt might be added around the suction cups to maximize the contact area while also compensating for air leakage with a higher flow from the vacuum pump.
Sheets may require custom yokes, rotating capabilities and possibly vertical rail transportation, all of which are a good fit for our Sheet Gripper.
Although any of these systems perform the same basic function of lifting and handling, the configuration and component selection will be quite different in each use case.
Hoses, Connectors and Filters
To complete the vacuum system, you have to attach hoses adapted for vacuum using hose clamps, sealing rings and screw unions. Making sure that all of these parts are perfectly fitted and sealed is essential to ensure safe operation of any pressurized system. These components must be adapted to the individual system, with special care taken in terms of tolerances and durability.
One or more filters are also used in order to protect the vacuum pump from dust and other contaminants that could shorten its life span or introduce operational faults.
Vacuum Pumps
Vacuum pumps used in vacuum lifting systems are normally gas displacement pumps, also known as gas transfer pumps. The basic principle of a displacement pump is to pull air into an expanding volume via an intake valve, compress it into a smaller volume and then eject the compressed air back into the atmosphere.
The operating principle of all displacements pumps is the same, but the type used in vacuum lifting systems is typically dry-running (oil-free) rotary vane pumps. As the name implies, these pumps use an internal rotor with multiple vanes that take in, compress and exhaust the air continuously.
There are several advantages to this pump type. It is compact in size, requires limited maintenance compared to other varieties, and it can operate at a constant suction rate.
Advantages of Vacuum Lifting Systems
Many aspects make vacuum lifting stand out compared to the alternatives. Some of the more important benefits are:
- Increased productivity – The operator’s physical stature is never a concern. Anyone can be trained to use a vacuum lifter or gripper safely and lift heavy loads without losing energy. The result is significantly more efficient workflows that do not leave employees exhausted.
- Ergonomic health – Because very little effort is required in the lifting and handling, physical strain is significantly reduced along with the risk of workplace-related injuries. Other than keeping the staff healthier and happier, this should also lead to fewer sick days that may otherwise put a dent in productivity.
- Workforce flexibility – Since anyone can lift, businesses have much greater flexibility in terms of recruitment and employee rotation. The efficient workflows are also less labor-intensive, allowing for a smaller workforce.
- Prevents damage – Compared to various types of mechanical lifting, vacuum lifting typically lowers the risk of damage to materials, such as scratches or deformation.
- Safety – Vacuum lifting systems are inherently safe for several reasons. One is that lifting cannot be initiated at all should the vacuum system malfunction. And in the case of critical problems such as a power outage, fail-safe valves will ensure that the load is not immediately dropped.
If you have additional questions about how our vacuum lift systems work and in what ways they can be tailored to your specific needs and workflows, do not hesitate to contact us for a free consultation.